Wie Gigafactories ein Giga-Geschäft werden
Beim Elektroauto kommt es auf die Batterie an – eines der wichtigsten und teuersten Bauteile: Nur der Hersteller, der ihre Technik beherrscht und zu konkurrenzfähigen Preisen produzieren kann, überlebt. Die Batterieexperten von Porsche Consulting kennen die Wege, wie sich die begehrten Stromspeicher in großen Mengen herstellen lassen – zum halben Preis.
06/2021
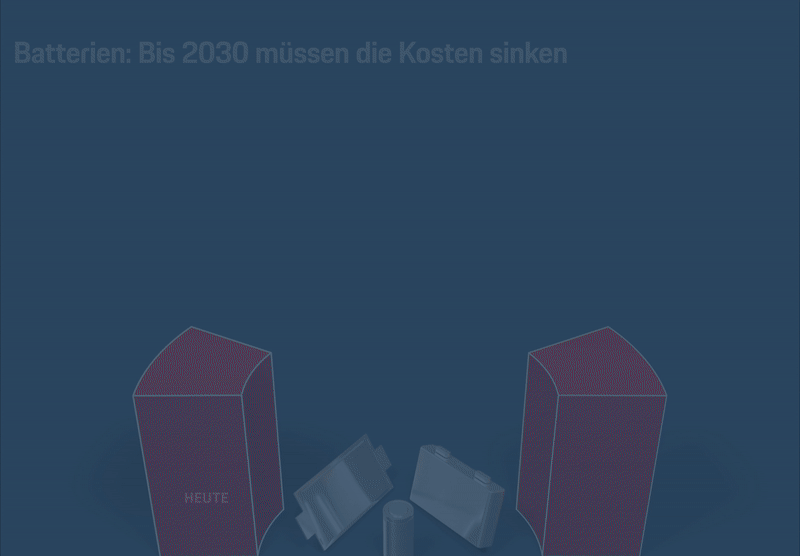
Die Zahl der Menschen, die sich für Elektrofahrzeuge entscheiden, steigt kontinuierlich, auch dank zusätzlicher Anreize für Neuwagenkunden. Nun muss die Industrie handeln und schnell Fabriken für die Akkumulatoren bauen, auch in Europa. Diese sogenannten Gigafactories erfordern gigantische Investitionen. Doch wie und wo wird daraus ein rentables Geschäft? In einer umfassenden Analyse hat ein Expertenteam von Porsche Consulting Chancen und Risiken gegenübergestellt. Im Fokus: moderne Batterietechnologien, effiziente Produktionsprozesse, der passende Standort und die richtige Skalierung für eine nachhaltige Produktion in Europa.
EU-Länder setzen auf Elektromobilität
Was im konventionellen Fahrzeug der Motor ist, ist im Elektroauto die Batterie. Sie hat großen Einfluss auf Reichweite und Schnellladeverhalten. Beim Gesamtpreis des Fahrzeugs schlagen die Batteriekosten im Jahr 2021 mit bis zu 40 Prozent zu Buche. Das macht die Elektromobilität bislang vergleichsweise teurer. Außerdem sind die Batteriegröße und damit die Reichweite des Fahrzeugs wichtige Kaufkriterien für die Kunden. Dennoch: Im Vorjahr 2020 stieg die Zahl der in der Europäischen Union (EU) neu zugelassenen Elektrofahrzeuge auf ein Rekordhoch von mehr als einer Million, ermittelte der europäische Branchenverband ACEA. Noch locken Kaufprämien die Kunden. Der Grund: Insbesondere die EU-Länder setzen auf Elektromobilität, um die Ende 2019 im „Green Deal“ gesteckten Klimaziele zu erfüllen.
Üblicherweise haben reine Elektrofahrzeuge Batteriegrößen von 50 bis 100 Kilowattstunden. Umgerechnet heißt das: Bis 2030 ist eine Produktionskapazität von mehr als 1.000 Gigawattstunden notwendig, um die europäischen Automobilhersteller zu versorgen. Die Industrie steht daher vor der Herausforderung, Kosten zu senken und gleichzeitig große Batteriefabriken in Europa aufzubauen. Diese Gigafactories müssen wirtschaftlich und nachhaltig betrieben werden. Nur so können in jedem Preissegment Elektrofahrzeuge in ausreichender Menge angeboten werden.
Um den Batteriebedarf lokal zu decken, sind allein in Europa 20 Gigafactories bis 2030 notwendig.
„Der weltweite Bedarf an Antriebsbatterien wird sich bis zum Jahr 2030 voraussichtlich mehr als verzehnfachen“, hat Frank Seuster, Partner für Produkt und Technologie bei Porsche Consulting, mit seinem Expertenteam hochgerechnet. „Um den Batteriebedarf lokal zu decken, sind allein in Europa 20 Gigafactories bis 2030 notwendig“, sagt Seuster. Für den Geschäftserfolg von Unternehmen und Investoren wird entscheidend sein, welche Batterietechnologien sie mit welchen Produktionsprozessen an welchem Standort herstellen. Denn allein für die Batteriezellfertigung seien europaweit bis 2030 Investitionen von über 50 Milliarden Euro erforderlich, so der Berater.
Welche Batterietechnologie ist die Richtige?
Aus Kundensicht müssen sich Elektrofahrzeuge an konventionellen Modellen mit Verbrennungsmotor messen lassen. Vorteile bieten viele Elektroautos beispielsweise bei Beschleunigung und Fahrkomfort. Allerdings wünschen sich die meisten Kunden derzeit vor allem, seltener Ladestationen ansteuern zu müssen, um Zwangspausen auf Langstrecken zu vermeiden. Ein Weg dahin sind leistungsfähigere Batterien mit höherer Energiedichte. Bei gleichbleibenden Dimensionen kann der Akku dem Fahrzeug also mehr Reichweite ermöglichen. Mehr Energie, aber nicht mehr Platzbedarf für die Batterie, lautet das engagierte Entwicklungsziel. Obendrein muss der Preis sinken. Beides kann durch technologischen Fortschritt gelingen.
Hersteller und Zulieferer arbeiten daher intensiv daran, die aktuelle Lithium-Ionen-Technologie zu verbessern. In den vergangenen zwei Jahrzehnten konnten die Batteriekosten um rund 80 Prozent gesenkt werden. Einen großen Anteil daran hat der schrittweise Ersatz von teurem Kobalt durch Nickel. Beide Metalle binden das Lithium in die Schichtstruktur der Kathode ein. Der höhere Nickelgehalt hat auch dazu beigetragen, die Energiedichte – verantwortlich für Größe und Gewicht der Batterie – im gleichen Zeitraum zu verdreifachen. Um die Reichweiten weiter zu erhöhen, forschen eine Reihe von Herstellern daran, die Chemie nickelreicher Zellen weiter zu verbessern. Dabei wird besonderes Augenmerk auf Sicherheit und Langlebigkeit gelegt.
Beim Kurzstreckenverkehr können Lithium-Eisenphosphat-Zellen die Wende zur Elektromobilität beschleunigen.
„Energiedichten lassen sich durch einen höheren Silizium-Anteil in der Anode weiter steigern. Die Technologieforschung konzentriert sich hier darauf, eine ausreichende Lebensdauer der Batterien sicherzustellen“, sagt Experte Lukas Mauler, Manager bei Porsche Consulting. Sein Spezialgebiet sind die Batterietechnologien und der Markt für die gefragten Energiespeicher. Mauler betont, dass je nach Fahrzeugsegment auch der Einsatz anderer chemischer Zusammensetzungen von Lithium-Ionen-Zellen sinnvoll sein kann: „Beim Kurzstreckenverkehr können Lithium-Eisenphosphat-Zellen die Wende zur Elektromobilität beschleunigen. Denn der Kostenvorteil dieser Technologie überzeugt Autokäufer, die stark auf den Preis achten.“ Die Langlebigkeit sei außerdem auch für Nutzfahrzeuge und den gewerblichen Einsatz attraktiv. Wer eine Gigafactory baut, sollte deshalb die Wahl der geeigneten, zukunftsfähigen Technologie abhängig machen von dem Fahrzeugsegment, das bedient werden soll. Unerlässlich, so Mauler, sei eine flexibel ausgerichtete Angebotspalette, mit der auf dynamische Marktentwicklungen reagiert werden kann. Dies betrifft auch zukünftige, sogenannte Post-Lithium-Ionen-Technologien wie die Feststoffbatterie. Deren industrielle Herstellung wird noch in diesem Jahrzehnt erwartet.
Batteriekosten halbieren – das ist möglich
Zellkosten lassen sich durch Optimierung der eingesetzten Materialien verringern. Eine vielversprechende Strategie stellt die schrittweise Reduktion von kostspieligem Kobalt dar. Im Gegenzug werden vermehrt Nickel und Mangan eingesetzt. Das ermöglicht eine günstigere chemische Zusammensetzung der Zellen. Ein höherer Silizium-Anteil steigert den Energieinhalt der Zellen und führt so zu einer effizienteren Nutzung sonstiger Batteriematerialien. In beiden Fällen arbeiten Forscher heute noch intensiv an einer ausreichenden Langlebigkeit der Batterie. Weiterhin können Verbesserungen an Zell- und Elektrodendesign die Batteriekosten zusätzlich verringern. Innovationen im Herstellungsprozess tragen zu einer weiteren Reduktion der Zellkosten bei. Neuartige Verfahren zur Trockenbeschichtung der Elektroden verzichten auf umweltschädliche Lösemittel. Damit können teure und energieintensive Trocknungsstrecken entfallen, die einen Großteil der Energiekosten einer Batteriefabrik ausmachen. Um den kostspieligen Ausschuss von Batterien zu verringern, helfen innovative Smart-Factory-Ansätze, Ursachen zu erkennen und zu beseitigen, bevor Fehler entstehen. Beschleunigte Prozessgeschwindigkeiten in zahlreichen Fertigungsschritten helfen zusätzlich bei der besseren Nutzung teurer Maschinen und Anlagen.
Batteriekosten können außerdem durch die Nutzung standortbezogener Kostenvorteile gesenkt werden. Standorte mit niedrigen Energie-, Lohn- und Baukosten bieten hier Potenzial. Das muss jedoch unternehmensspezifisch abgewogen werden hinsichtlich weiterer Kriterien wie nachhaltiger Energieversorgung und Verfügbarkeit von Fachkräften. Die steigende Batterienachfrage gibt Herstellern weiterhin Spielraum, Batteriefabriken intelligent zu skalieren, und hilft, „Economies of Scale“ zu erzielen. Eine höhere Produktionskapazität ermöglicht es, unterschiedliche Anlagen besser aufeinander abzustimmen und so die hohen erforderlichen Investitionen effizienter zu nutzen.
Produktionsprozesse effizient und flexibel gestalten
Auf den Produktionsflächen einer Gigafactory, wo in zahlreichen Schritten Elektroden hergestellt, in Zellenform montiert und für die spätere Nutzung aktiviert werden, vollzieht sich stets eine dynamische Entwicklung. Für den Aufbau einer Gigafactory ist daher viel Kapital notwendig. Je nachdem, wie viele Fahrzeugbatterien im Jahr hergestellt werden sollen, liegt die Größenordnung zwischen zwei und vier Milliarden Euro. Die höchsten Einzelinvestitionen entfallen auf Maschinen und Anlagen und machen rund 10 Prozent der Batteriekosten aus, wie Porsche Consulting in seinem technologiebasierten Batteriekostenmodell vorrechnet.
Bereits in der Vergangenheit senkten höhere Prozessgeschwindigkeiten die Produktionskosten. So konnten die Gigafactories wirtschaftlicher genutzt werden. In naher Zukunft sind weitere Effekte zu erwarten. Neuartige Prozesstechnologien wie die Trockenbeschichtung der Elektroden versprechen weitere Kostensenkungen. „Durch den Wegfall umweltschädlicher Lösemittel können teure Trocknungsstrecken, die viel Energie benötigen, eingespart werden. Das senkt die Kosten und verbessert gleichzeitig die Ökobilanz von Elektrofahrzeugen. Ein wertvoller Doppeleffekt“, sagt Dr. Fabian Duffner, Senior Manager bei Porsche Consulting. Er ist der Produktions- und Kostenspezialist im Expertenteam.
Durch den Wegfall umweltschädlicher Lösemittel können teure Trocknungsstrecken, die viel Energie benötigen, eingespart werden.
Noch effizienter und nachhaltiger wird jede Herstellung, wenn unnötiger Ausschuss in der Fertigung vermieden wird. Das gilt auch für die Mängelquote in Batteriefabriken. Die Lösung: Früherkennungssysteme. Sie verhindern, dass Fehler überhaupt entstehen. Dafür eignen sich Smart-Factory-Ansätze. Der Vorteil: Die digitale Vernetzung aller Maschinen und Anlagen ermöglicht zuverlässige Prognosen. Wenn Hersteller beim Bau einer Gigafactory solche Prozessverbesserungen von Anfang an mit einplanen und mit Innovationen kombinieren, leisten sie einen Beitrag für erschwingliche und umweltfreundliche Elektromobilität, reduzieren die Investitionskosten und bleiben langfristig wettbewerbsfähig. So hat Porsche Consulting den südkoreanischen Batteriehersteller LG Chem, einer der globalen Marktführer, beim Neuanlauf seiner Batteriefabrik in Polen beraten: „Mit dem Instandhaltungskonzept von Porsche Consulting können wir die Produktion um 14 Prozent steigern“, so Kyong Deuk Jeong, Präsident von LG Chem Wrocław Energy.
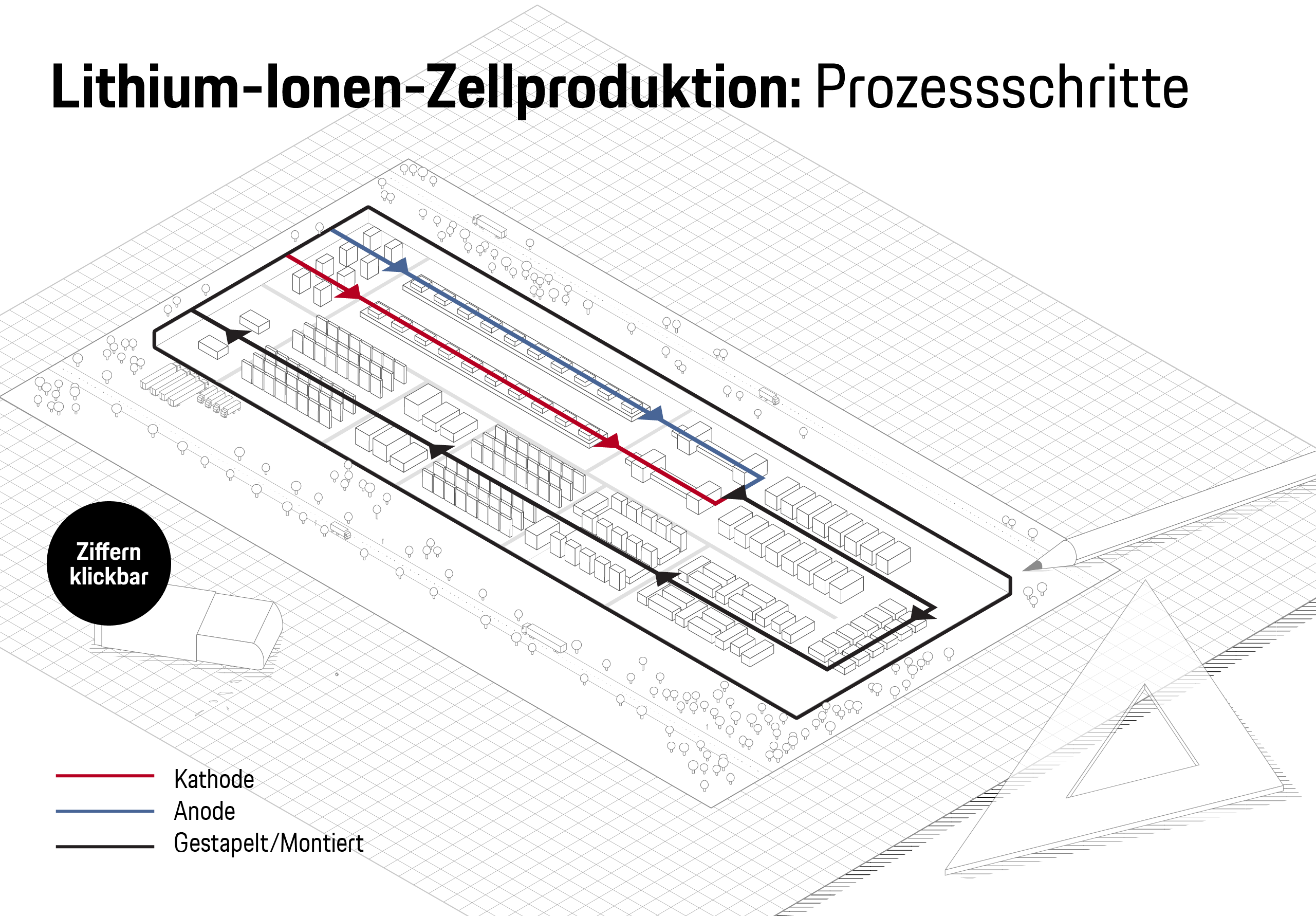
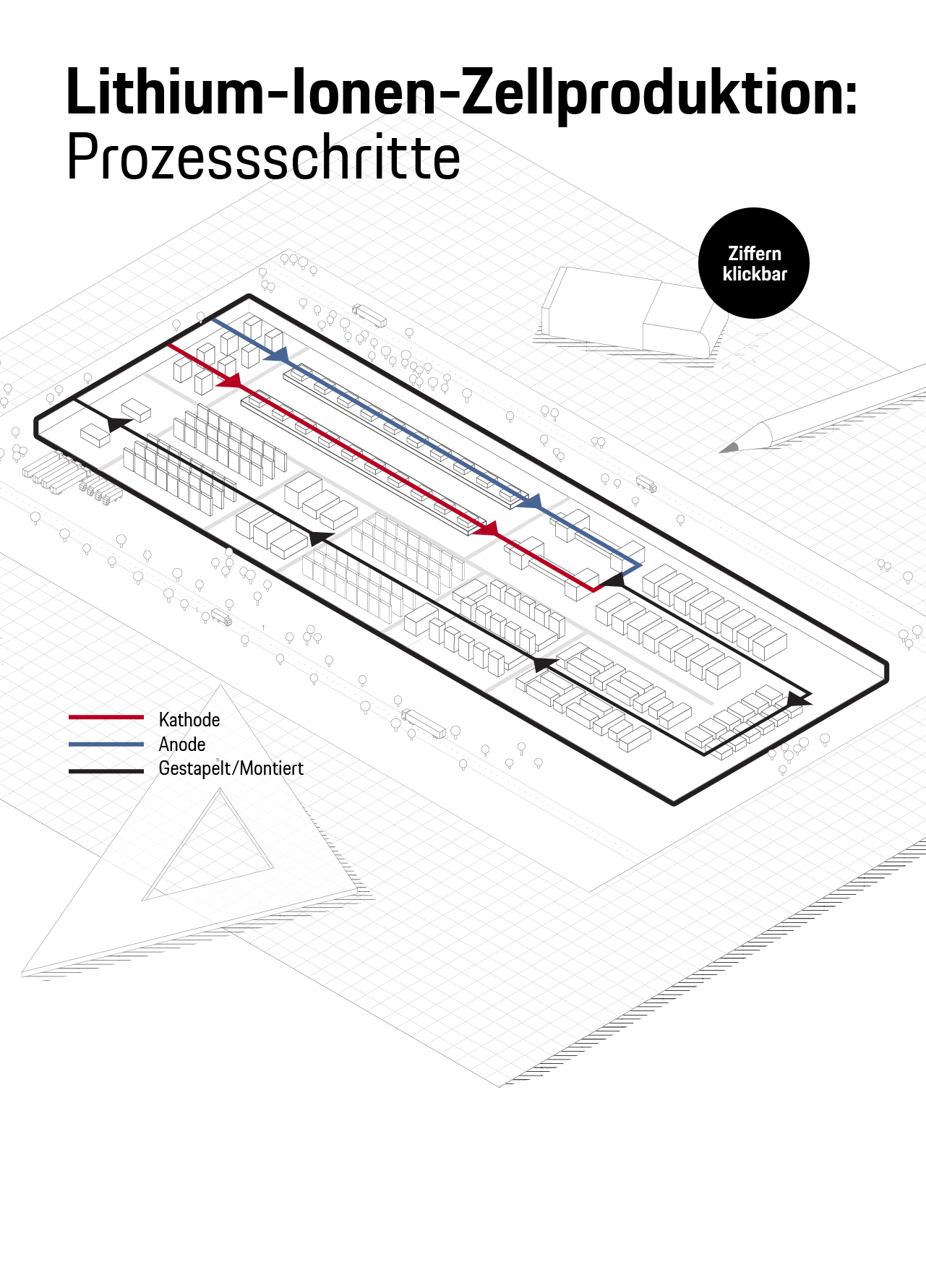
Welcher Standort hat welche Vor- und Nachteile?
Die Zellfabriken der Zukunft werden zu den größten Produktionsgebäuden der Welt gehören. Die einzelnen Unternehmen favorisieren für ihre Investments unterschiedliche Standorte: Northvolt hat sich für Schweden, Volkswagen für Deutschland und LG Chem für Polen entschieden. Bei der Standortwahl spielen neben der Nähe zur EU-weit verstreuten Fahrzeugproduktion weitere Faktoren eine Rolle. Wo gibt es genügend Fachkräfte, welche Kosten müssen für Energie und Personal eingeplant werden, wo ist regenerativ erzeugter „grüner“ Strom verfügbar?
Der große Standortvergleich von Porsche Consulting hat ergeben: Während einige EU-Länder bei zwei dieser Kriterien besonders gut abschneiden, erreicht derzeit noch kein Land überall einen Spitzenplatz. Die Hersteller treffen daher eine Abwägung zur Standortwahl anhand ihrer Marktposition und Strategie: „Newcomer bevorzugen Länder mit ausreichend Batterieexperten, um Technologiekompetenz aufzuholen. Etablierte Marktführer setzen teilweise auf Kostenvorteile bei Lohn und Energie“, sagt Dr. Fabian Duffner. Weiterhin nutzen Zellhersteller regenerativ erzeugten Strom für ihre Gigafactories als Differenzierungsmerkmal. Das schafft zusätzliche Wettbewerbsvorteile: „Kunden und die Öffentlichkeit generell erwarten neben dem emissionsfreien Betrieb eine ressourcenschonende Herstellung ihres Fahrzeugs, die maßgeblich von der Batterieproduktion beeinflusst wird“, so Dr. Duffner.
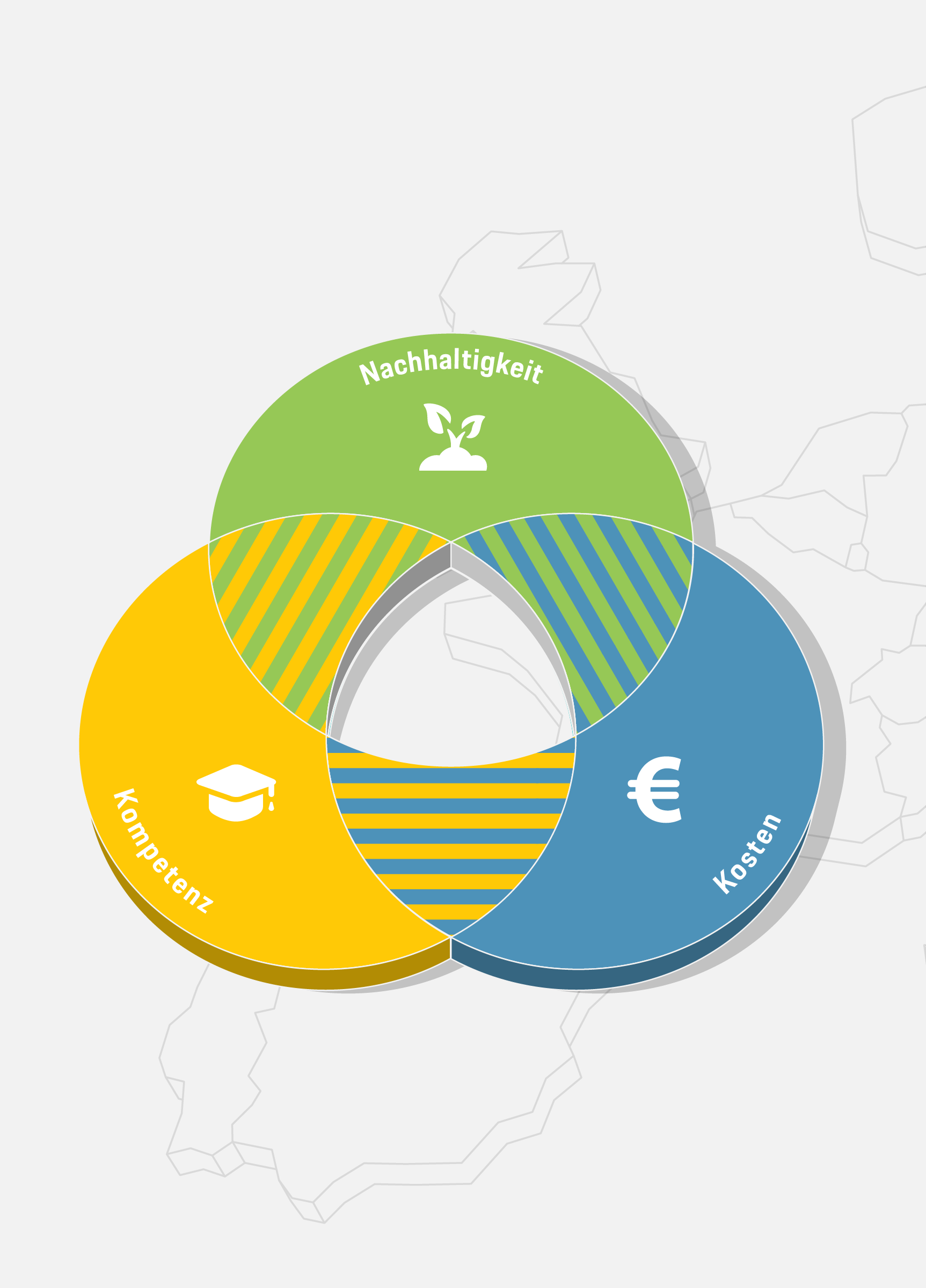
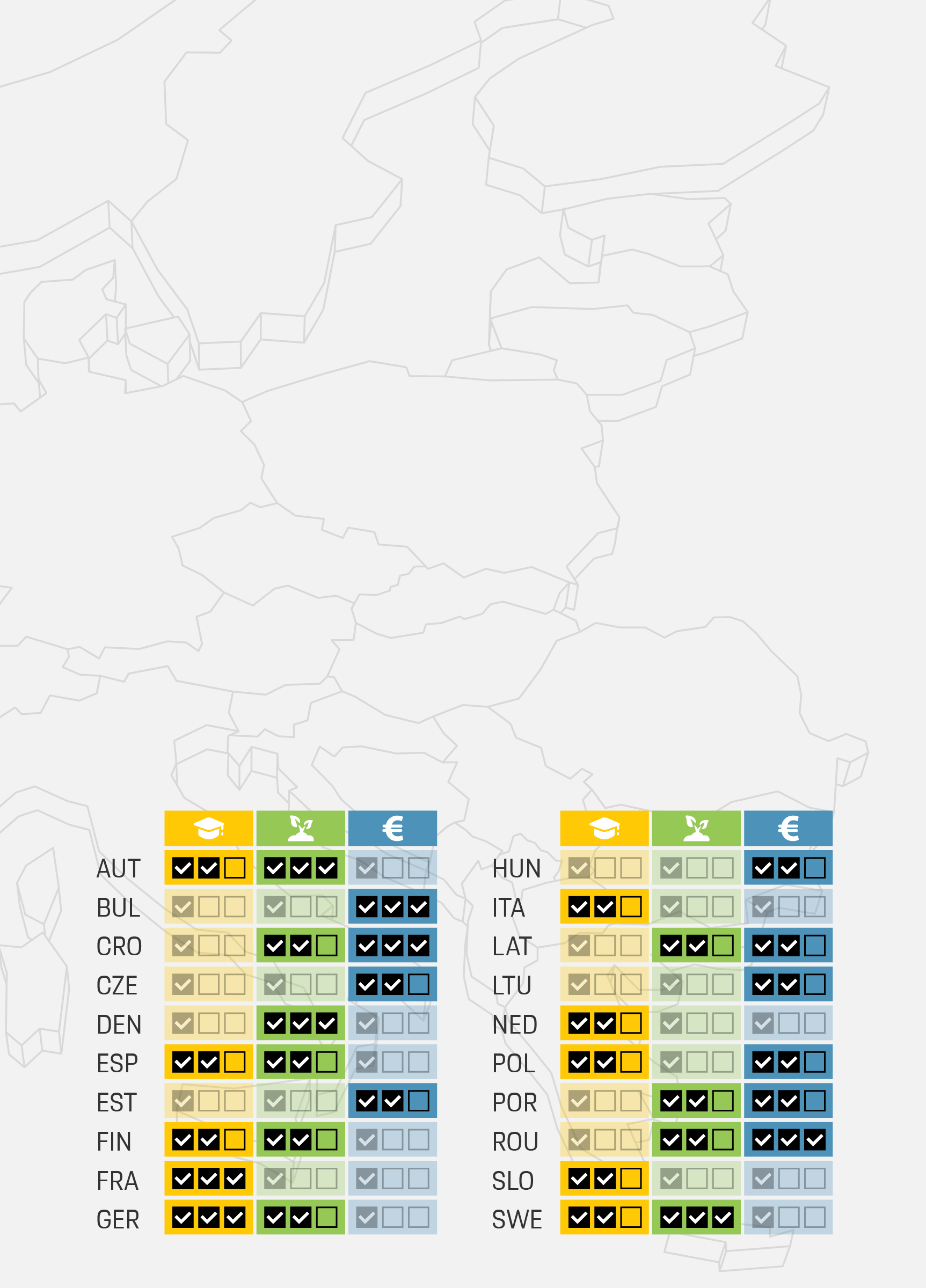
Batterieproduktion:
Wer kann was in Europa?
Porsche Consulting hat die Länder der EU auf ihre Eignung als Standort für eine Batteriefabrik hin untersucht. In den drei Kategorien Nachhaltigkeit, Kompetenz und Kosten fasst die Analyse
verschiedene Indikatoren zusammen: länderspezifische Forschungsaktivitäten, die Verfügbarkeit relevanter Fachkräfte und Investitionen in Bildung, länderabhängige Energie-, Lohn- und Baukosten sowie den Anteil regenerativ erzeugten Stroms am Bruttostromverbrauch. Einige Länder vereinen schon zwei Vorteile, manche einen. Noch kein EU-Land kann bisher in allen drei Kategorien gleichzeitig glänzen.
Prognosemodelle helfen beim Weichenstellen
Können Gigafactories tatsächlich ihrer Schlüsselrolle für klimaneutralen Antrieb nachkommen und so schon bald zu einem Giga-Geschäft werden? Für Investoren und Hersteller, die jetzt vorausschauend und strategisch überlegt handeln, eröffnen sich tatsächlich hervorragende Perspektiven. „Die dynamische Entwicklung der Batterietechnologie schafft branchenübergreifend enorme Marktpotenziale. Davon können außer der Autoindustrie insbesondere auch der Maschinen- und Anlagenbau durch ganz neue Chancen profitieren“, sagt Experte Lukas Mauler. Um Innovationen ganzheitlich einzuschätzen, kooperieren die Porsche-Berater mit einem Netzwerk aus Industrieexperten und Forschern. Gemeinsam bewerten die Fachleute Marktpotenziale anhand selbst entwickelter, zuverlässiger Prognosemodelle. „Wenn die Industrie jetzt die richtigen Weichen für den Aufbau der Batteriefabriken stellt, wird das Elektroauto bis 2025 günstiger sein als der Verbrenner“, erwartet Mauler auf Basis seiner neuesten Berechnungen.