Das Rennen um die Feststoffbatterie
Eine neue Generation von Batterien könnte die Karten im Markt der E-Mobilität neu verteilen. Doch ob die Feststoffbatterie der erhoffte Game Changer wird, hängt vom Erfolg der Entwickler ab. Porsche Consulting hat die Chancen der neuen Technologie analysiert.
07/2023
6 HERAUSFORDERUNGEN
bei der Industrialisierung der Feststoffbatterie
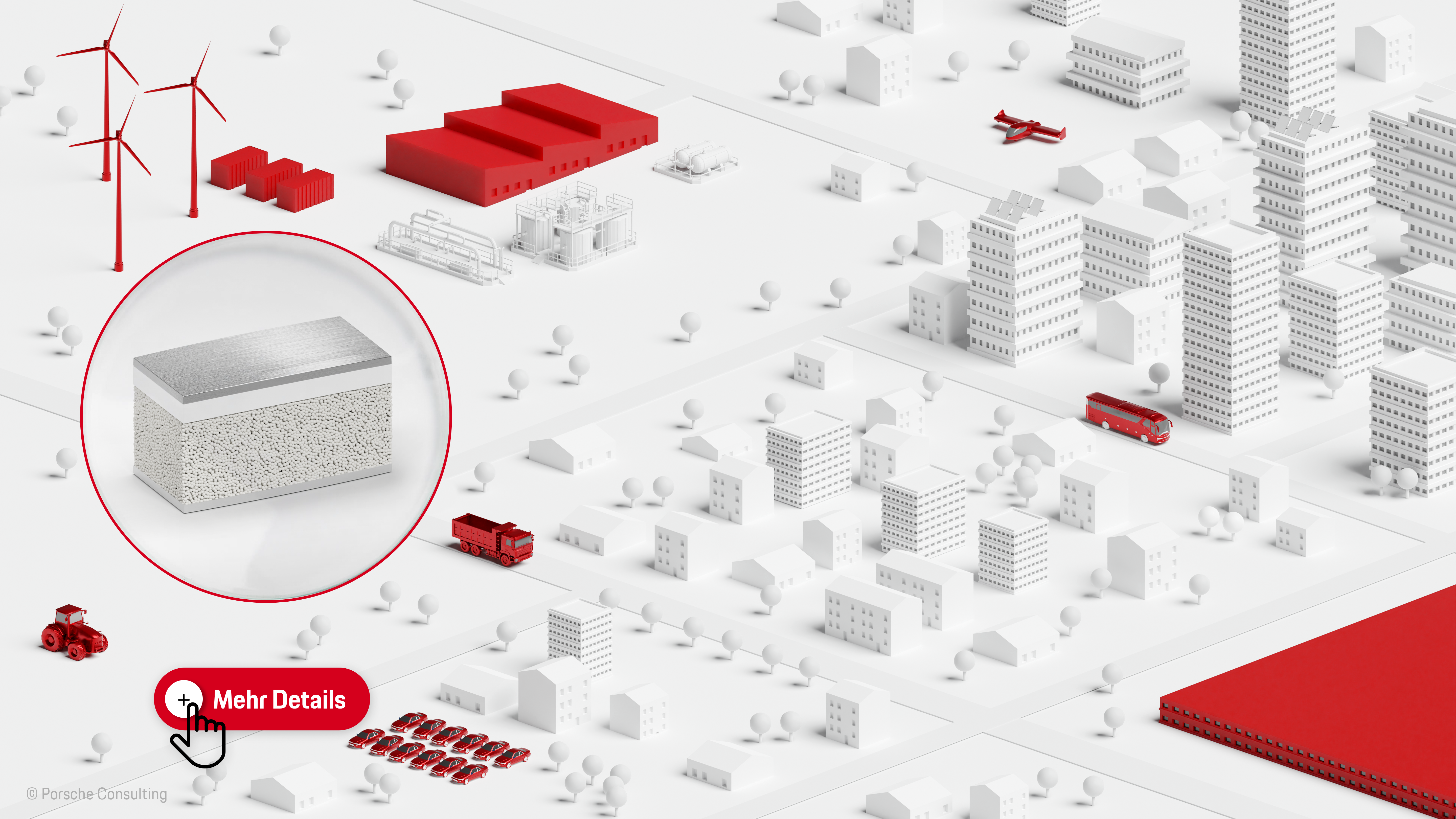
Die Batterie gilt als Herzkammer moderner Autos mit Elektroantrieb. Dennoch haben sich viele Hersteller bei dem wichtigsten und wertvollsten Bauteil ihrer Fahrzeuge lange auf die Zulieferindustrie verlassen. Doch damit scheint inzwischen Schluss zu sein: Um Kernkompetenzen im Bereich der Batterietechnik aufzubauen und ihre Marken mit innovativer Technologie stärker vom Wettbewerb abzugrenzen, investieren die Automobilhersteller verstärkt in den Bau eigener Gigafactorys. So hat allein Volkswagen in den nächsten Jahren sechs Gigafabriken in Europa geplant – mit einem Gesamtproduktionsvolumen von über 240 Gigawattstunden.
Porsche Consulting schätzt den globalen Batteriemarkt auf über 5.500 Gigawattstunden im Jahr 2030 ein. Zwei Drittel davon entfallen auf den Bereich Personenwagen. Laut den Berechnungen verzehnfacht sich der Gesamtmarkt damit in dieser Dekade. Doch das ist erst der Anfang, denn parallel zu den Milliarden, die in eigene Fabriken fließen, investieren die Autokonzerne massiv in eine ganz neue Generation von Batterien. Sie könnten die Karten im Geschäft mit der E-Mobilität ganz neu verteilen.
Die Innovation braucht Rückenwind
Von einem echten „Game Changer“ spricht Dr. Fabian Duffner, Partner Advanced Technologies bei Porsche Consulting, wenn es um die Feststoffbatterie geht. Sie kann aus seiner Sicht nicht nur die Automobilwelt revolutionieren, sondern auch beispielsweise Flugzeugen die Elektrifizierung ermöglichen. Ihre zentralen Vorteile: längere Reichweiten, schnellere Ladezeiten, höhere Sicherheit. Und vor allem: Sie gibt den Automobilherstellern die Chance, sich noch schneller aus der Abhängigkeit von asiatischen Zellherstellern zu lösen. Denn anders als bei der herkömmlichen Lithium-Ionen-Batterie handelt es sich bei den Technologieführern der Feststoff-Batterie in erster Linie um Start-ups aus den USA.
Dennoch drückt Duffner ein wenig auf die Euphoriebremse: „Die Feststoffbatterie wird kein Selbstläufer. Es gibt zahlreiche Herausforderungen, die technisch und ökonomisch erst noch gelöst werden müssen, bevor die industrielle Fertigung beginnen kann.“ Sechs Themen sind aus seiner Sicht zentral: die Verbesserung der Produkt- und Materialeigenschaften, die Transformation der Produktion in den Großserienmaßstab, die Integration der Batterien in die Fahrzeugsysteme, der Aufbau robuster Lieferketten für neue Materialien und Maschinen, die Reduktion der Produktionskosten sowie die Finanzierung der Serienentwicklungs- und Skalierungsphase.
Die Feststoffbatterie kann ein echter Game Changer für die Elektrifizierung sein. Die Herausforderungen bis zur serienreifen Industrialisierung sind allerdings gewaltig.
Um an der Spitze zu sein, haben sich die meisten Automobilhersteller bei Feststoff-Start-ups eingekauft – trotz vieler Hürden, die bei dieser Technologie noch bestehen. Dass sich diese Investitionen lohnen könnten, zeigen Zahlen von Porsche Consulting: Werden die Herausforderungen gelöst und tritt die Marktreife somit wie prognostiziert ein, schätzen die Berater das mögliche Marktvolumen rund um die industrielle Fertigung der Feststoffbatterien kumulativ bis 2035 auf über 400 Milliarden Euro ein.
Wird die neue Technik also tatsächlich der „Game Changer“ in der Automobilindustrie und darüber hinaus? Welche Weichen müssen gestellt werden, um die industrielle Basis dafür zu schaffen? Wie ist der Stand der Technologie und welche Herausforderungen gilt es noch zu lösen, damit aus den Prognosen Realität werden kann? Welche Chancen und Risiken ergeben sich schließlich für Europas Unternehmen? Das Porsche Consulting Magazin dokumentiert den aktuellen Wissensstand zu diesen und weiteren zentralen Fragen rund um die Feststoffbatterie.
Reichweite rauf, Preis runter:
Entwicklung von Automobilbatterien in 130 Jahren
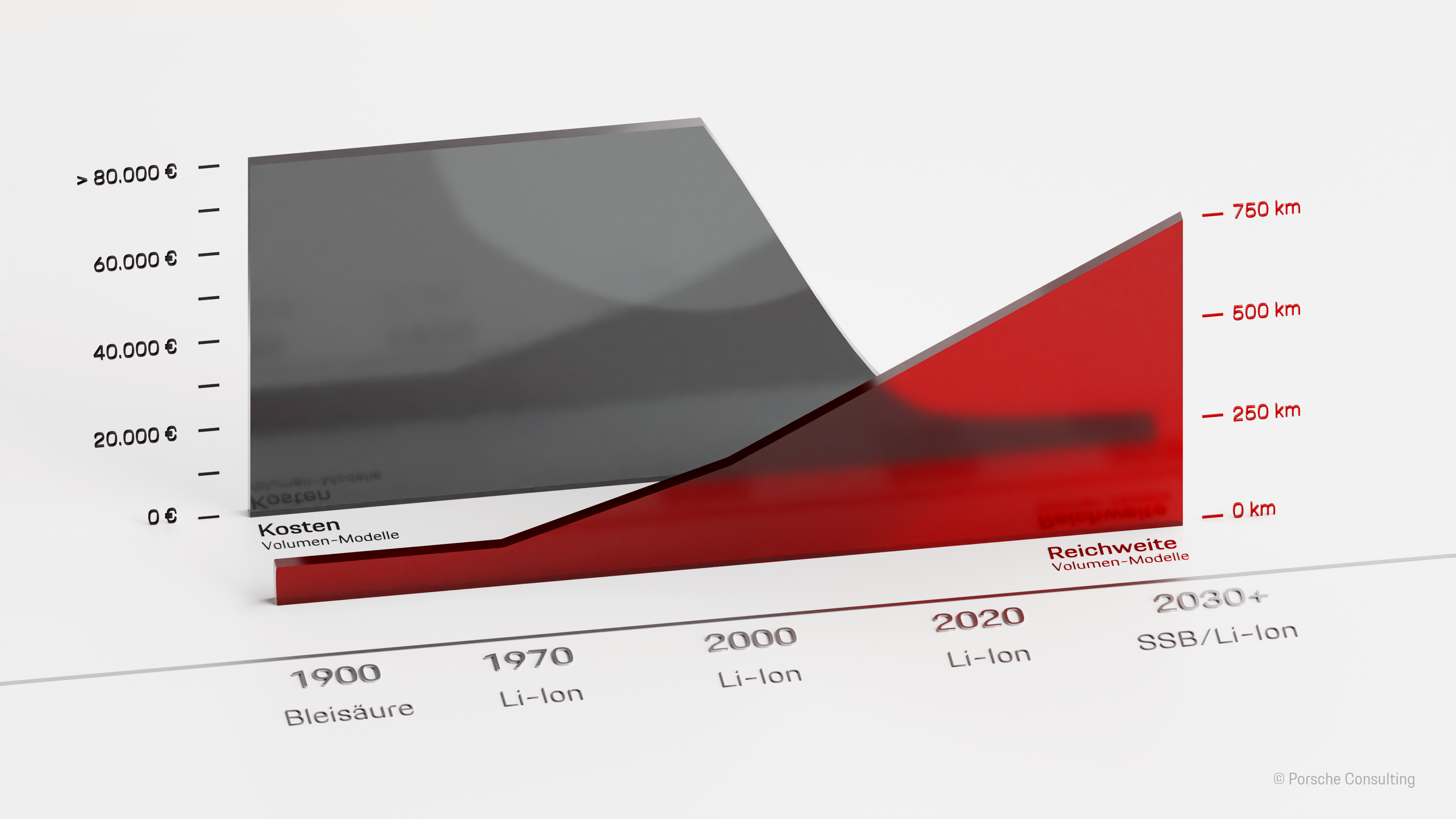
Was sind die zentralen Vorteile der Feststoffbatterie im Vergleich zur Lithium-Ionen-Batterie?
Umfragen der Marktforscher zeigen immer wieder, dass es Käufern von E-Autos im Wesentlichen auf drei Kriterien ankommt: eine möglichst hohe Reichweite, eine kurze Ladezeit der Batterien und Anschaffungskosten, die mit Verbrennern vergleichbar sind. Antriebsleistung, Sicherheit und Lebensdauer gehören zu den weiteren Anforderungen an die Batterie. Wenn es tatsächlich gelingt, Fahrzeuge mit Feststoffbatterien in Serie zu produzieren, dürften moderne E-Autos alle diese Kriterien erfüllen. Möglich macht das der Festelektrolyt, der als Separator zwischen Anode und Kathode fungiert. Durch diesen chemisch stabilen Festelektrolyten können als Energiespeichermaterialien Alternativen zum heute verwendeten Grafit zum Einsatz kommen, beispielsweise Lithium-Metall. Der Vorteil: Im Verhältnis zum Gewicht liegt die Speicherkapazität von Lithium-Metall zehnmal höher als die von Grafit. Die höhere Energiedichte, die auf diese Weise erzeugt wird, erhöht den Energieinhalt bei gleichem Batterievolumen und lässt schon bis 2030 Reichweiten von über 750 Kilometern realistisch erscheinen.
Endlich größere Reichweite, kürzere Ladezeiten, mehr Sicherheit und geringere Kosten
Gleichzeitig können Ionen durch den festen Elektrolyten schneller transportiert werden, was dafür sorgt, dass auch die zeitintensiven Ladezeiten der Vergangenheit angehören werden. Länger als zehn Minuten wird das „Auftanken“ einer E-Auto-Batterie dann nicht mehr dauern, schätzen Fachleute. Das Laden einer Autobatterie wird dann kaum mehr Zeit in Anspruch nehmen, als einen Tank mit Benzin oder Diesel zu füllen. Auch die Sicherheit im Fahrzeug wird durch die neue Technik optimiert, denn der flüssige Elektrolyt einer herkömmlichen Lithium-Ionen-Batterie ist brennbar. Zwar fangen Lithium-Ionen-Akkus nur äußerst selten Feuer – bei der Feststoffbatterie kann diese Gefahr aber nahezu ausgeschlossen werden.
„Unter dem Strich zeigt sich, dass die Vorteile der Feststoffbatterie im Vergleich zur Lithium-Ionen-Batterie gewaltig sind. Allerdings ließe sich Ähnliches von den technischen Problemen behaupten, die noch gelöst werden müssen, um sie in die Serienreife zu überführen“, sagt Duffner.
Ich glaube, Lithium-Metall-Feststoffbatterien werden im Vergleich zu herkömmlichen Lithium-Ionen-Batterien eine deutliche Leistungssteigerung mit sich bringen. Wenn Elektroautos mit Batterien ausgerüstet werden, die eine höhere Energiedichte, kürzere Ladezeiten und mehr Sicherheit bieten, wird das zu einem Quantensprung in Bezug auf ihre Akzeptanz und ihren Einsatz führen. So etwas wollen wir auf den Markt bringen.
Die atmende Zelle
Lithium-Ionen- versus anodenfreie Feststoffbatterie
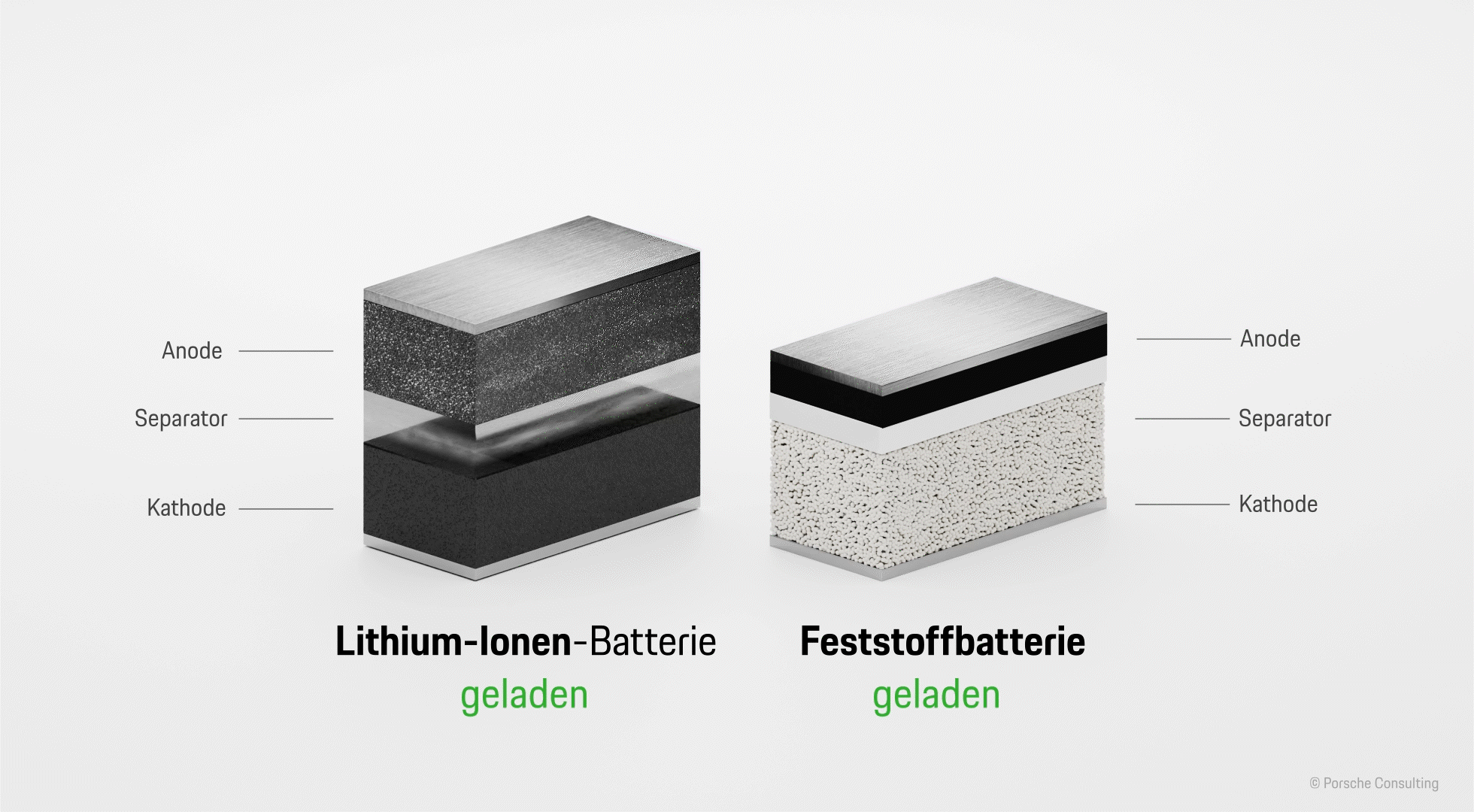
In welchen Märkten könnten Feststoffbatterien zum Einsatz kommen?
Gelingt es, die Herausforderungen der Feststoffbatterie zu lösen, wird diese die Lithium-Ionen-Batterie aller Voraussicht nach in vielen Bereichen bis 2035 ersetzen. Wahrscheinlich wird es zuvor eine Übergangsphase geben, in der die Feststoffbatterie aufgrund noch geringer Stückzahlen und hoher Kosten zunächst hochpreisigen Marktsegmenten vorbehalten bleibt. So lassen die Prognosen von Porsche Consulting erkennen, dass zunächst Pkw-Marken im Premium-Segment mit Feststoffbatterien unterwegs sein werden. Parallel dürfte die Antriebstechnik auch in erste Flugzeuge verbaut werden. Allerdings nicht in die großen Passagier- und Frachtmaschinen, sondern in sogenannte Electric Vertical Take-Off and Landing Aircrafts (eVTOLs) – kleine elektrische Zwei- bis Sechssitzer, die schon bald den Taxibetrieb in die Luft verlagern könnten. Die Vorteile der Feststoffbatterie sind dabei das reduzierte Gewicht, ihr hohes Leistungsvermögen, das speziell für Start- und Landung wichtig ist, und nicht zuletzt ihr gutes Sicherheitsprofil. Mittelfristig ist durch die Feststoffbatterie elektrisches Fliegen auf Kurzstrecken von bis zu 1.000 Kilometern denkbar.
Eine Batterie für viele Fälle
Erst wenn ab 2030 die industrielle Produktion der neuen Batterietechnologie an Fahrt gewinnt und weitere Fortschritte beim Thema Materialeffizienz erreicht werden, wird sie den Lithium-Ionen-Batterien auch in puncto Kosten überlegen sein. Zu diesem Zeitpunkt wird sie aller Voraussicht nach eine ebenso lange, wenn nicht sogar längere Lebensdauer aufweisen als ihr Vorgängermodell. Der Einsatz der Feststoffbatterie wird dabei keinesfalls auf das E-Auto beschränkt bleiben. „Das Gegenteil ist der Fall“, bestätigt Dr. Xiaohan Wu, Senior Experte bei Porsche Consulting: „Die ganzheitliche Verbesserung der Batterie-KPIs erlaubt die Elektrifizierung weiterer Branchen, die mit der heutigen Technik noch nicht vorstellbar ist.“
Auch wenn es noch zahlreiche technische Hürden gibt, die wir bis zur Serienfertigung der Feststoffbatterie überwinden müssen – die Laborergebnisse zeigen schon heute, dass nicht nur ihr Prinzip funktioniert, sie unterstreichen auch das herausragende Potenzial der Feststoffbatterie.
Wann wird es erste serienreife Feststoffbatterien geben?
Auch wenn das Potenzial der Feststoffbatterie groß ist, ihr Einsatzspektrum gewaltig erscheint – noch ist die Forschung daran eine Wette auf die Zukunft. Zwar haben Entwickler bereits erste Zellen entwickelt, die bei Raumtemperatur funktionieren, doch bis zur Großserie könnte es noch einige Jahre dauern. Und auch das ist keinesfalls sicher, denn die vielversprechendsten Konzepte wurden bisher entweder nur mit Prototypen im Labor demonstriert oder sie befinden sich in einer Pilotphase. In jedem Fall ist die Industrie noch ein ganzes Stück weit entfernt von einer hochautomatisierten Produktion, wie man sie von der Lithium-Ionen-Batterie kennt.
Piloten starten 2024
Neben den vorwiegend amerikanischen Zell-Start-ups haben sich weltweit Kompetenzcluster gebildet, die an der Industrialisierung der Feststoffzelle arbeiten. Ein Beispiel: In Japan sind es die Automobilhersteller, welche die Entwicklung der Feststoffbatterie im Rahmen des Industriekonsortiums NEDO gemeinsam mit Zellherstellern und Materiallieferanten über die gesamte Wertschöpfungskette vorantreiben. Wenn sich die Erwartungen der Experten erfüllen, könnten Pilotanwendungen ab 2024 und ein großserieller Markteintritt etwa im Jahr 2027 erfolgen. Dieser wäre zunächst auf die weniger kostensensitiven Premium-Segmente beschränkt. „Ab 2030 rechnen wir mit einer vollständigen Industrialisierung und mit einer einhergehenden Performance-Steigerung bei sinkenden Produktionskosten“, sagt Dr. Wu. Spätestens dann zeige sich auch die „disruptive Qualität“ der neuen Technik. Die könnte die komplette Automobilindustrie erfassen. Entsprechend geht Porsche Consulting bis 2035 von Marktanteilen für feststoffbatteriebetriebene Fahrzeuge von 5 bis 15 Prozent aus. Das dürfte bis zu 35 Millionen Fahrzeugen entsprechen, die dann auf den Straßen unterwegs sein werden.
Die Erfindung der Lithium-Ionen-Batterie wurde mit einem Nobelpreis geehrt. Die Industrialisierung einer ganzheitlich überlegenen Lithium-Metall-Feststoffbatterie wäre einen weiteren wert!
Können die bisher auf Lithium-Ionen-Batterien ausgerichteten Gigafactorys auf die Produktion von Feststoffbatterien umgerüstet werden?
Auch wenn sie spät dran sind: Die deutschen Automobilhersteller setzen mittlerweile voll auf die Elektromobilität – und haben Milliardeninvestitionen in neue Gigafabriken angekündigt. Die Gigafactorys sind allerdings auf eine Antriebstechnik ausgelegt, die aktuell den Takt bei E-Autos vorgibt: Lithium-Ionen-Batterien. Doch was geschieht, wenn die technischen Probleme mit der Feststoffbatterie selbst ab etwa 2027 gelöst sind? Lassen sich die Produktionsabläufe einfach auf die neue, überlegene Technik adaptieren? „Wir schätzen, dass sich rund 40 Prozent der Maschinen in den heutigen Gigafactorys auch für die Herstellung von Feststoffbatterien eignen werden“, sagt Prof. Dr. Jens Leker von der Westfälischen Wilhelms-Universität Münster.
Doch es geht nicht um die Maschinen allein, auch Prozesse und Herstellungsmethoden müssen ganz neu aufgestellt werden. Das ist wichtig, um die Zellproduktion effizient zu gewährleisten. Während einige klassische Verfahren etwa bei der Pulvermischung, Beschichtung und beim Kalandrieren beibehalten werden können, kommen andere in der Zellproduktion hinzu, beispielsweise bei der Laminierung, aber auch beim Sintern und Pressen. Aufgrund der Materialeigenschaften des Festelektrolyten wird zudem eine größere Anzahl von Prozessschritten unter Schutzatmosphäre stattfinden müssen.
Die Umrüstung heutiger Lithium-Ionen- zu Feststoffbatterie-Fabriken ist mit erheblichem Aufwand verbunden, da circa 60 Prozent der Maschinen und Anlagen ersetzt werden müssen und sich die Dimensionierung der Produktionsbereiche komplett unterscheidet.
Schlanker und sparsamer
Diese und weitere spezifische Eigenschaften der Feststoffbatterie werden zu Mehrkosten im Vergleich mit der Produktion heutiger Lithium-Ionen-Batterien führen. Dem stehen aber auch einige Eigenschaften der Feststoffbatterie gegenüber, die signifikante Einsparungen mit sich bringen werden. So können bei Feststoffbatterien stabilere Materialkombinationen eingesetzt werden. Hierdurch können die Formierung und das Aging – das sind Produktionsschritte, die in heutigen Gigafabriken rund ein Drittel der Fläche einnehmen – maßgeblich verschlankt werden. Zusätzlich entfällt das Befüllen des flüssigen Elektrolyten inklusive der Einziehzeit der Flüssigkeit in die porösen Aktivmaterialien.
Vor allem aber ist die Anode zentral, wenn es um Einsparpotenziale bei der Feststoffbatterie geht. So ist die Anodenproduktion bei Lithium-Ionen-Batterien nicht nur äußerst zeitintensiv, sie ist auch mit hohen Kosten verbunden. Rund 15 bis 20 Prozent der Fläche heutiger Industrieanlagen entfallen allein auf die Anodenproduktion. Kann auf die Anode verzichtet werden, sparen die Hersteller nicht nur das notwendige Material und die entsprechenden Maschinen ein – auch die für die Produktion nötigen Experten können an anderer Stelle eingesetzt werden. Die innovativsten Start-ups im Segment der Feststoffbatterien, wie zum Beispiel Quantumscape, verfolgen daher Zellkonzepte, die komplett ohne Aktivmaterial an der Anode auskommen. Ob ihnen die Entwicklung der anodenfreien Feststoffbatterie gelingt, ist aus Sicht von Fabian Duffner entscheidend für die neue Batteriegeneration: „Nur wenn es gelingt, anodenfreie Konzepte zu etablieren und hierdurch die damit verbundenen Kostenvorteile zu realisieren, wird es der Feststoffbatterie gelingen, den prognostizierten Wandel in der Automobilwirtschaft und darüber hinaus auszulösen.“
9 Schritte zur Feststoffbatterie
Wie Fabriken umstrukturiert werden können

Welche weiteren Herausforderungen gibt es beim Blick auf die Feststoffbatterie?
Neben der Herstellung der Batterie selbst müssen Lösungen für ihre Integration ins Fahrzeug gefunden werden. Das Hauptproblem: Die Feststoffbatterie „atmet“ quasi. Dieser Prozess der Ausdehnung und anschließenden Schrumpfung kann bei der Lithium-Metall-Anode mehr als zehn Zentimeter im Gesamtfahrzeug betragen. Ingenieure müssen also eine Möglichkeit finden, wie sich eine solche Volumenänderung in einen ansonsten starren Fahrzeugrahmen integrieren lässt. Daneben muss das Zellformat der heutigen Prototypenzellen deutlich vergrößert werden, um für den Einsatz in der Automobilindustrie und weitere Anwendungen relevant zu werden.
Auch beim Thema Material haben die Forscher aktuell noch eine volle To-do-Liste, die sie bis zu einer echten Industrialisierung abarbeiten müssen. Verbessert werden müssen die Materialeigenschaften aller drei maßgeblichen Komponenten der Feststoffbatterie – Festelektrolyt, Kathode und Anode. Das Kathodenmaterial und der Feststoffelektrolyt müssen chemisch aufeinander abgestimmt werden, zum Beispiel durch geeignete Oberflächenbeschichtung des Kathodenmaterials. Ansonsten drohen unerwünschte Nebenreaktionen, die die Lebensdauer der Feststoffbatterie verringern. Auch die Festelektrolyte selbst haben noch deutlichen Optimierungsbedarf. Die Forscher müssen vor allem an ihrer chemischen Beständigkeit arbeiten. Auch der Ionentransport muss weiter beschleunigt werden, wenn die Feststoffbatterie als Ganzes als Herzkammer eines Sportwagens bestehen will.
Damit die Feststoffbatterie tatsächlich die versprochene Energiedichte erreicht, ist es wichtig, die Schichtdicke des Festelektrolytseparators auf weniger als 20 Mikrometer zu reduzieren. Das ist in etwa dreimal dünner als ein menschliches Haar. Für die Großserienproduktion stellt das eine gewaltige Herausforderung dar. Denn die Separatoren müssen nicht nur dünn, sondern auch „pinhole free“ sein, also frei von kleinsten Unregelmäßigkeiten auf der Oberfläche. Zudem benötigt man diese dichten Separatoren in einem sehr großen Umfang: Soll eine Produktionskapazität von 20 Gigawattstunden erreicht werden, sind Separatoren notwendig, die nebeneinandergelegt eine Fläche von 150 Millionen Quadratmetern einnehmen würden – das entspricht in etwa 20.000 Fußballfeldern. Um die Kosten im Griff zu behalten, sollte hierbei die Ausschussrate des wertvollen Feststoffelektrolytseparators auf ein Minimum reduziert werden.
Neue Lieferketten absichern
Es wird noch einige Jahre dauern, bis Forscher und Entwickler in den Start-ups die Eigenschaften der Feststoffbatterie so weit optimiert haben, dass mit der industriellen Produktion begonnen werden kann. Doch auch dann werden noch nicht alle Probleme aus der Welt geschafft sein. So ist es wichtig, dass die Industrie in einem nächsten Schritt die notwendigen Lieferketten für die neuen Materialien etabliert. Hierbei kann sie nur beschränkt auf die bereits bestehende Supply Chain von Lithium-Ionen-Batterien zurückgreifen. Das Set der benötigten Chemikalien ist einfach zu unterschiedlich. Vor allem bei stark nachgefragten Rohstoffen wie Lithium ist es geboten, dass sich die Hersteller im Hinblick auf Verfügbarkeit und Preisschwankungen absichern. Feststoffelektrolyte enthalten aufs Volumen bezogen bis zu 50-mal mehr Lithium als konventionelle Flüssigelektrolyte.
Vor diesem Hintergrund rechnen die Batterie-Experten von Porsche Consulting damit, dass es bis zu zwei Jahre dauern wird, bis die Zulieferindustrie erste Anlagen errichtet hat, um die nötigen Materialien bereitzustellen. Der Bau und die Inbetriebnahme der eigentlichen Batterieanlagen dauert sogar noch länger. Mindestens zweieinhalb Jahre veranschlagen die Experten dafür. „Um Zeit und Kosten zu sparen, sollten sich die Akteure also frühzeitig vorbereiten und ihre Prozesse aufeinander abstimmen“, sagt Experte Wu.
Die Industrialisierung der Feststoffbatterie ist zudem mit großem finanziellen Risiko verbunden. Allein für den Aufbau einer Pilotanlage im Megawatt-Bereich muss mit Kosten von 500 Millionen bis 1 Milliarde Euro gerechnet werden. Falls die Planer den eigenständigen Aufbau einer Gigafabrik mit bis zu 20 Gigawattstunden anstreben, müssen sie mit weiteren Investitionen von rund 2 Milliarden Euro kalkulieren: 1 bis 1,5 Milliarden Euro werden Maschinen, Anlagen und Gebäude kosten. Weitere 0,5 bis 1 Milliarden Euro entfallen den Experten zufolge während des Anlaufs auf die hohen Ausschussraten und das benötigte Personal. Daher ist es wenig überraschend, dass Start-ups wie Solid Power und Solid Energy System sich frühzeitig um Produktionspartnerschaften bemüht haben – sei es im Rahmen einer Auftragsfertigung oder als Joint Venture mit Automobilherstellern.
Die Finanzierung des weiteren technologischen Fortschritts ist ein kritischer Erfolgsfaktor für die Technologie-Start-ups. Allein die Kosten der Skalierung vom Labormaßstab in eine Pilotfertigung belaufen sich auf eine Milliarde Euro. Weitere zwei Milliarden Euro kommen hinzu, falls sie eine Gigafabrik hochfahren.
Welche Unternehmen liegen bei der Entwicklung der Feststoffbatterie vorn?
Während bei der Lithium-Ionen-Technologie asiatische Hersteller wie CATL und LG dominieren, handelt es sich bei den Technologieführern der Feststoffbatterien in erster Linie um Start-ups, die vorwiegend in den USA beheimatet sind. Die etablierten asiatischen Player überlassen das Feld aber nicht kampflos. So schließen zum Beispiel die führenden Zellhersteller in Korea enge Partnerschaften mit ihren Lieferanten, um die Technologie voranzutreiben. Die großen Automobilhersteller scheinen aus den Erfahrungen mit den Lithium-Ionen-Batterien gelernt zu haben: Um nicht wieder in eine Abhängigkeit von asiatischen Zulieferern zu geraten, haben sie sich massiv bei Tech-Start-ups eingekauft.
Allein Volkswagen hat über 300 Millionen US-Dollar in das kalifornische Start-up Quantumscape investiert, das sich auf anodenfreie Feststoffbatterien mit keramischen Feststoffelektrolyten spezialisiert hat. Im April 2021 gaben zudem Ford und BMW bekannt, dass sie insgesamt 130 Millionen US-Dollar in den Batterieentwickler Solid Power mit Sitz in Colorado investieren. Solid Power will zunächst Feststoffbatterien mit Silizium-Anoden zur Marktreife bringen und seine Batterien in einem zweiten Schritt mit Lithium-Metall-Anode ausstatten. Die Investitionen der Hersteller dürften sich in jedem Fall gelohnt haben: Sowohl Quantumscape als auch Solid Power sind börsennotiert und haben zwischenzeitlich mit einer Marktkapitalisierung von über einer Milliarde Dollar den „Unicorn-Status“ erreicht.
Einsatz für 3-D-Drucker
Auch Mercedes hat im Rahmen seiner „Electric only“-Strategie tief in die Taschen gegriffen: Im Januar 2022 weitete der Konzern mit einem hohen zweistelligen Millionenbetrag seine Kooperation mit dem taiwanesischen Anbieter Prologium aus. Zugleich hat sich Mercedes an Factorial Energy mit Sitz im US-Bundesstaat Massachusetts beteiligt, in das auch Stellantis (Fiat, Peugeot, Chrysler) investiert hat. In Europa haben vor allem die Firmen Ilika und Blue Solutions (Bolloré Gruppe) mit der Entwicklung eigener Feststoffbatterien auf sich aufmerksam gemacht. Während Ilika mit kleinformatigen Prototypen Investoren wie Jaguar, Land Rover und Honda überzeugen konnte, werden die Polymer-Feststoffbatteriezellen von Blue Solutions bereits kommerziell in elektrischen Bussen (eCitaro) von Mercedes eingesetzt. Für den Einsatz im Pkw ist die Technologie kaum geeignet, denn das Temperaturverhalten verlangt ein langes Vorwärmen vor dem Betrieb.
Nicht nur Materialinnovationen treiben die Entwicklung der Feststoffbatterie voran, auch neue Produktionsmethoden könnten der Industrialisierung einen Schub geben. So hat das kalifornische Start-up Sakuu ein neues 3-D-Druckverfahren entwickelt, mit dem sich Feststoffbatterien herstellen lassen. Auf diese Weise will Sakuu die Batterien der nächsten Generation schneller, günstiger und auf kleineren Flächen produzieren.
Kosteneffiziente Feststoffbatterien können erst dann eingeführt werden, wenn die Großserienproduktion realisierbar ist. Neue Verfahren wie der 3D-Druck könnten eine durchgängige Lösung bieten – mit den erforderlichen Einsparungen an Material, Energie und Investitionskosten.
Wer am Ende die Nase vorn hat, bleibt abzuwarten. Dabei sollte man die chinesischen Hersteller im Blick behalten. Die großen asiatischen Player haben eine andere Ausgangslage und entwickeln so mitunter andere Strategien beim Blick auf die Feststoffbatterie. So versucht man dort in erster Linie, die bestehenden Lithium-Ionen-Batterien zu optimieren. Das geschieht nicht zuletzt auch durch den sukzessiven Einbau von Festelektrolyten, sodass die sogenannten „Semi-Feststoffbatterien“ („semi-solid-state batteries“) entstehen. Als großer Vorteil der chinesischen Hersteller gelten die dort bereits bestehenden Gigafabriken, in denen die Ingenieure schlicht vieles in der Praxis ausprobieren können.
Welche Chancen ergeben sich für die Unternehmen?
Das disruptive Potenzial der Feststoffbatterie eröffnet aus Sicht der Experten ganz neue Chancen für die Industrie. Denn während vor allem asiatische Hersteller das Geschäft mit der Lithium-Ionen-Batterie gemacht haben, können deutsche und europäische Unternehmen jetzt die komplette Wertschöpfungskette der Feststoffbatterie in die eigene Hand nehmen. Die finanziellen Aussichten seien vielversprechend, sagen die Berater von Porsche Consulting. So belaufe sich das Marktpotenzial allein der Zellhersteller bis 2035 auf 200 Milliarden Euro. Bei der Material- und Zulieferindustrie seien weitere 150 Milliarden Euro zu erwarten. Und der Maschinenbau, der sich auf die Ausrüstung der neuen Gigafactorys konzentriert, kann mit Umsätzen von 70 Milliarden Euro rechnen.
Der Technologiewechsel auf Feststoffbatterien bietet eine Chance für den Einstieg von Maschinenbauern in allen Schritten des Produktionsprozesses: Bei hoher Übertragbarkeit von Lithium-Ionen-Kompetenzen für bereits etablierte Unternehmen, bei niedriger Übertragbarkeit auch für Neueinsteiger.
Allerdings müssen vorher einige Hemmnisse aus dem Weg geräumt werden. Denn noch sei keinesfalls klar, wie die Zellen mit den entsprechenden Qualitätsanforderungen im industriellen Maßstab hergestellt werden können. Auch hat der Maschinenbau die Zeichen der Zeit offenbar noch nicht erkannt. Auf dem Stand des Jahres 2022 gibt es schlicht keine geeigneten Serienanlagen zur Produktion von Feststoffbatterien. Es bleiben also noch einige Fragen auf dem Weg zur Feststoffbatterie offen. Wer als Erstes die passenden Antworten liefert, wird am Ende das Geschäft in der Zukunft machen.
Im Bereich Lithium-Ionen-Kompetenzen führt Asien nach der ersten Halbzeit mit 2:0. Bei den Fertigungstechnologien und den Maschinen für Feststoffbatterien sollten wir in Europa die Chance nutzen, gleich in Führung zu gehen.