Two Women
Get Rid of Plastic
Plastic wraps, coatings, and single-use containers — the synthetic content in all these products could be replaced by a bio-based granulate called “Traceless.” It is a fully compostable natural substance with similar properties to plastic.
09/2022
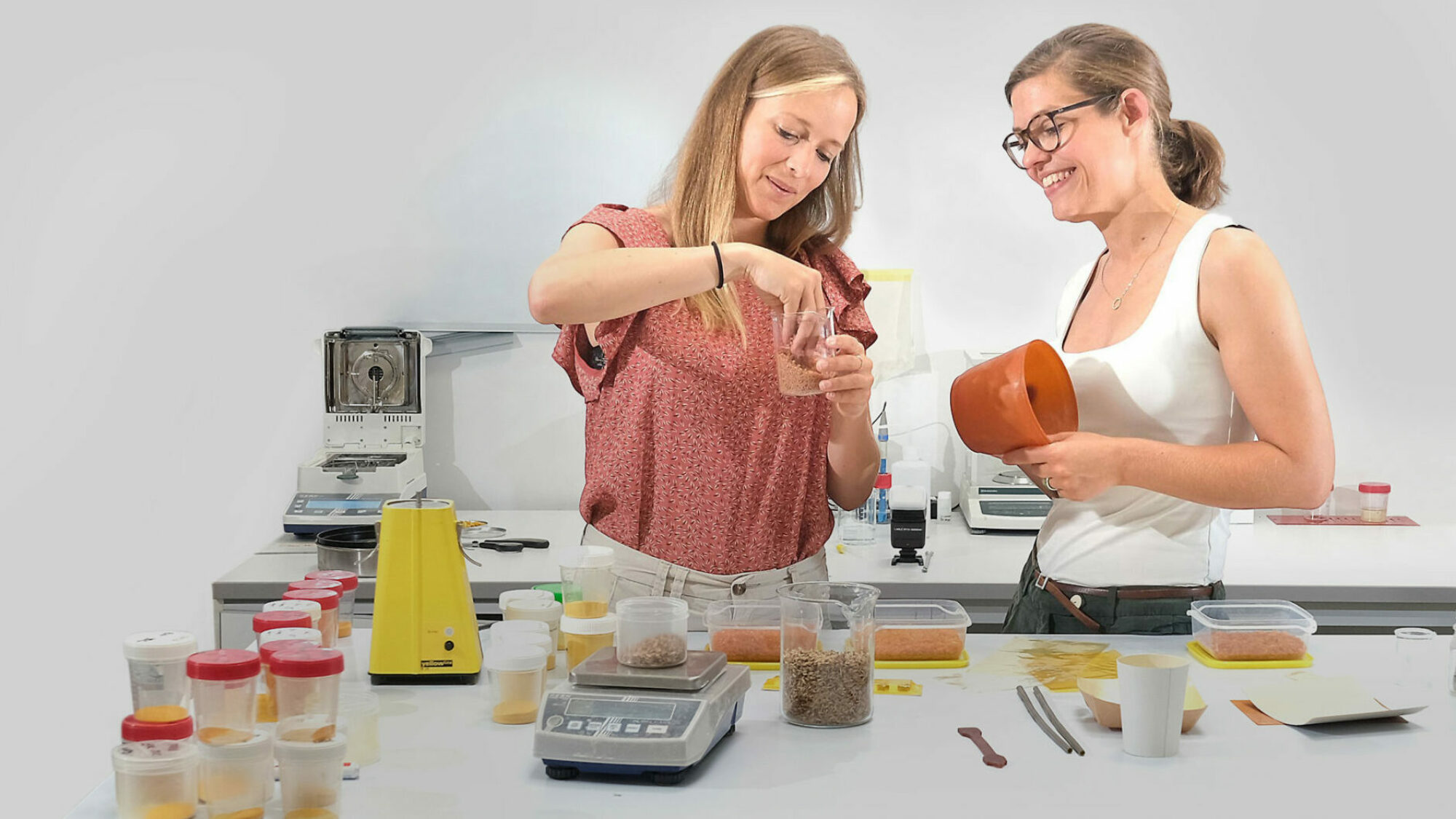
A grey rolling door rises at the press of a button to reveal an unprepossessing warehouse space. Here in Buchholz, a small town in northern Germany, one of the most important goals of the future—a world without plastic—is being actively pursued. Traceless Materials GmbH, a German start-up, has developed an innovative solution. Hidden away inside small sample vessels on a laboratory table as well as in large black boxes on the right side of the depot: a light orange crystalline substance that is capable of replacing plastic. With this substance, the two founders of Traceless, CEO Dr. Anne Lamp and COO Johanna Baare, seek to revolutionize the plastics industry—and to wage war on plastic pollution. The two women and their team—winners of a 2022 German Entrepreneur Award in the category “StartUp”—are keenly dedicated to achieving their goal.
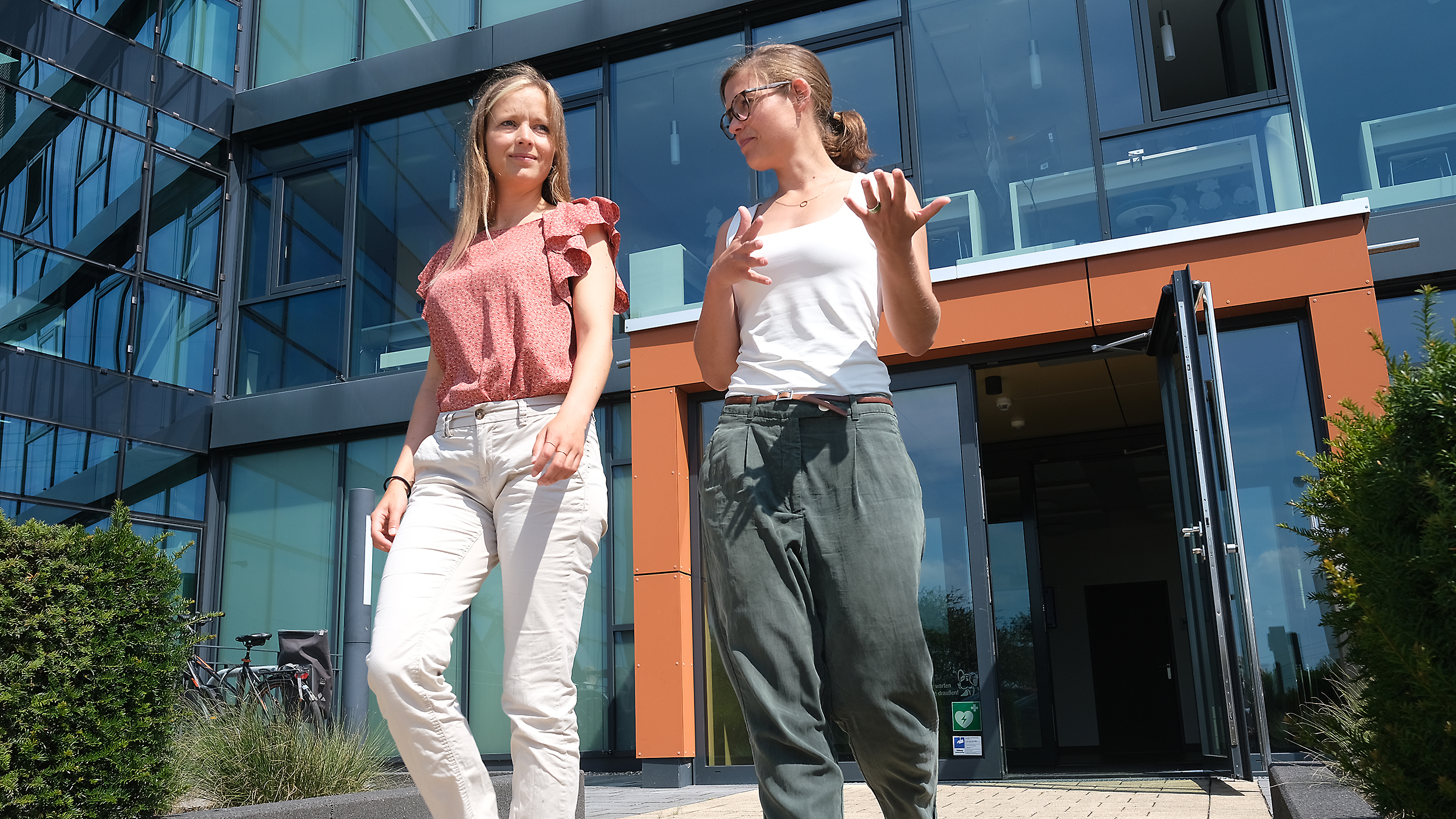
Sheeting made of grain residues—compost in nine weeks
A truckload every minute. Or expressed in numbers, around ten million tons a year. According to the NABU conservation organization, that is the rate at which plastic waste lands in the world’s oceans. That figure will more than double by 2040, predicts a study by the Pew Charitable Trusts non-profit and the Systemiq system designer. One of the main causes is the enormous increase in single-use plastics. And the consequences are dire. Marine animals and birds are dying. Habitats such as coral reefs are suffering from a build-up of waste. And biodiversity is profoundly at risk. To avert the impending demise of the oceans, there is a great need for pioneers—companies like Traceless.
Founded in 2020 in the town of Buchholz in der Nordheide south of Hamburg, Traceless has developed a completely new product: a bio-based granulate that can be further processed into a sustainable alternative to plastic. The founders have even ensured that the plastics industry doesn’t have to convert its injection molding machinery in order to further process the product. The granulate is made of residues from processing grain, which are also used in animal feed. Of crucial importance here is that the material is completely biodegradable under natural composting conditions—within a record time of nine to twelve weeks, the founders promise. As the name “Traceless” indicates, this is a solution that vanishes without a trace.
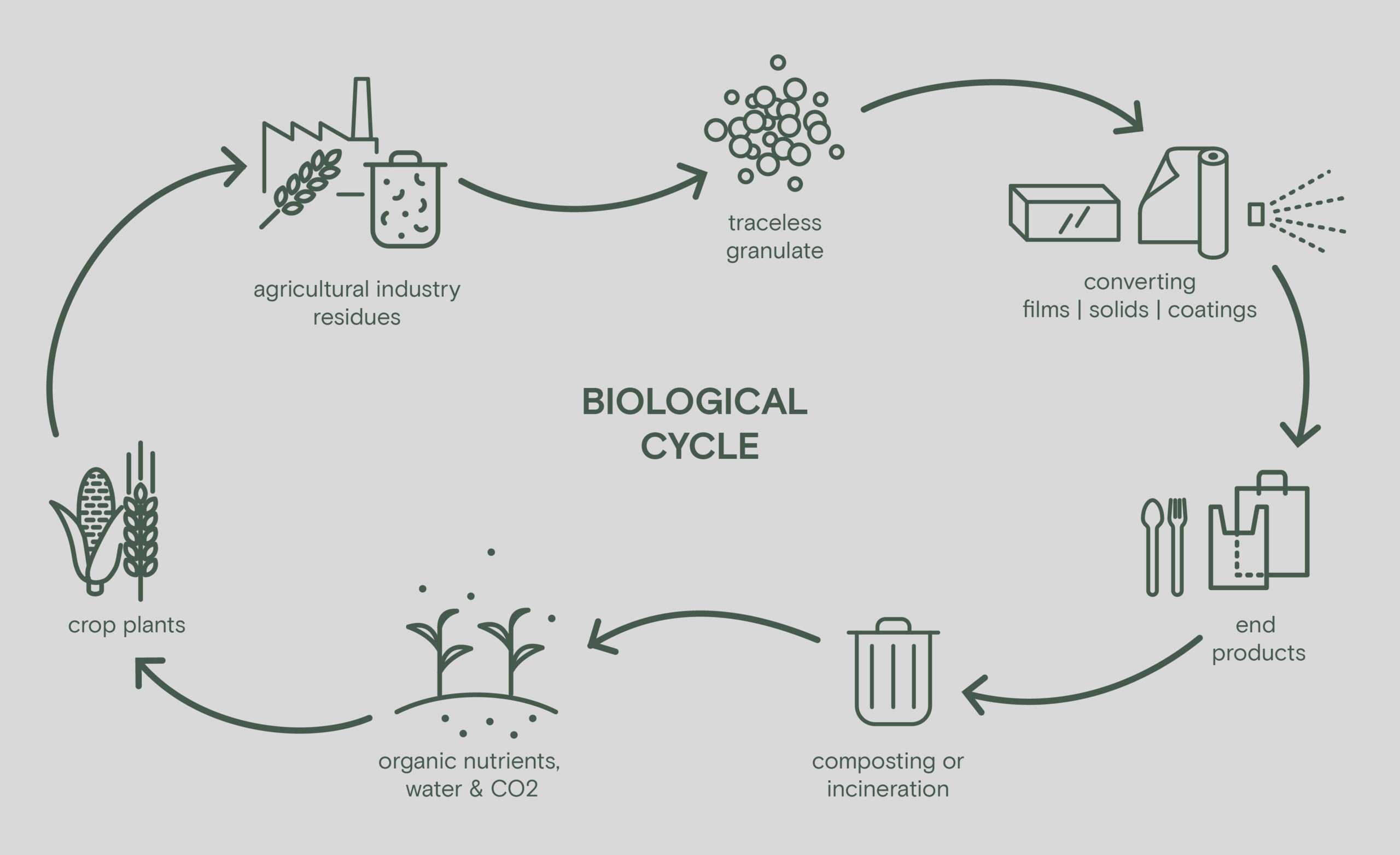
First major client: the Otto Group
The idea for Traceless came from Hamburg native Dr. Anne Lamp, born in 1991, around three years ago when she was working on her PhD in process engineering at the Hamburg University of Technology. Alongside her doctoral research, she turned her attention to another process: namely, how a material with similar properties to plastic could be produced from agricultural industry byproducts. Initial samples were generated, and the first large company became interested. This was the family-run Otto Group, a long-standing international e-commerce business. “Otto was excited right away, even though it took some imagination to envision real packaging materials from those early samples,” says Lamp. “But that was when I started to realize this could really attract people’s attention.”
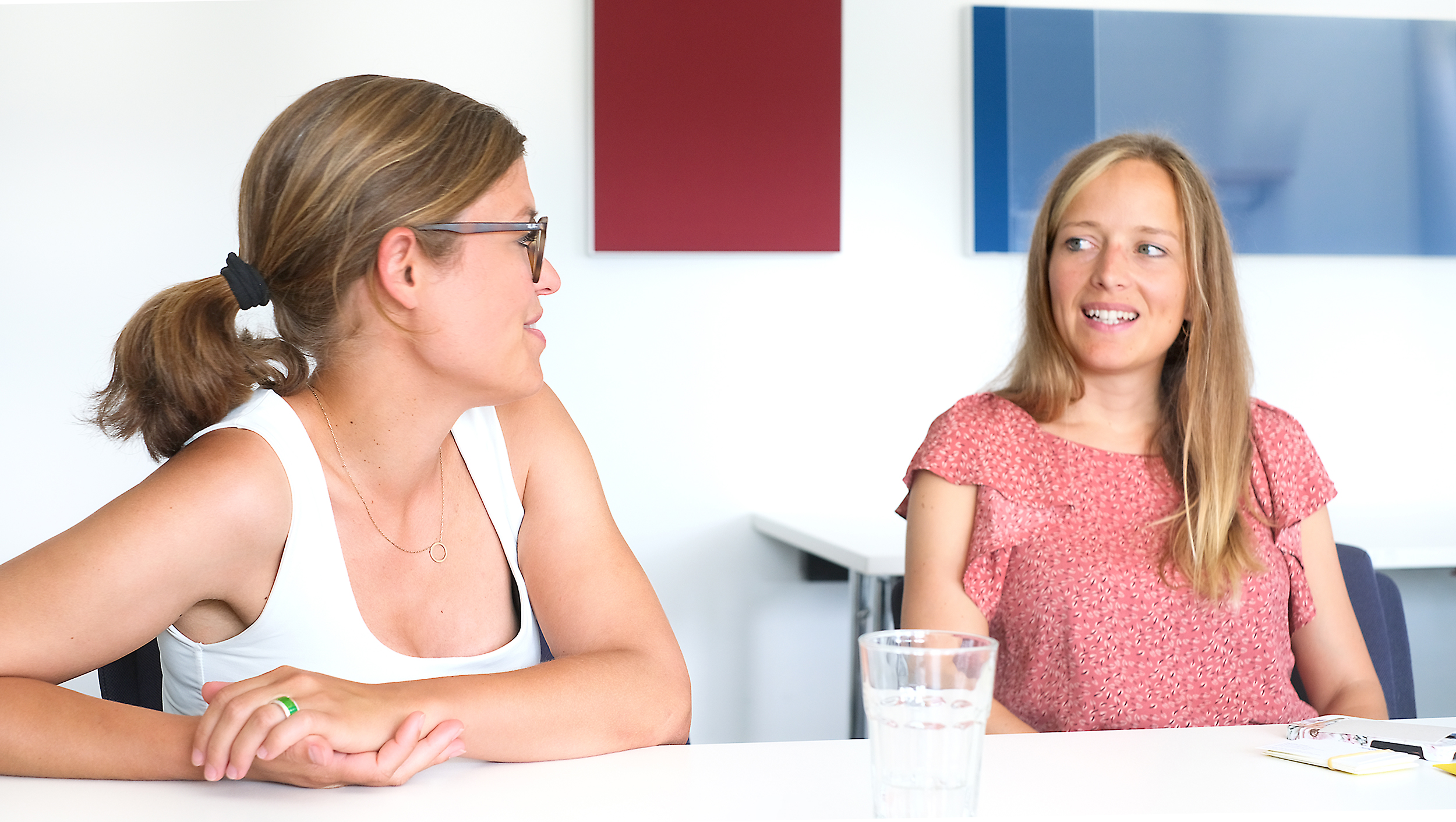
While still a doctoral candidate, she promptly entered her idea and first project samples in the “ActOnPlastic” challenge from Project Together, a Berlin-based incubator. There she met her co-founder Johanna Baare. “The challenge was to bring together 100 ideas to solve the global plastic problem,” says Lamp. “Mine was one of them. Everyone with an idea was assigned a mentor from business, and I was matched with Johanna.” The two women held virtual meetings for half a year on Zoom, refining the idea into an actual business model. Two and a half years later, when Lamp took the plunge to launch a business, she was clear about one thing: “I can’t do this alone, I need Johanna at my side.” While Lamp brings the technical expertise, Baare is responsible for business matters. “What makes us such a strong founder team is that we complement each other so well in our respective areas of expertise,” says Baare, who was born in 1988 and earned degrees in psychology and business administration.
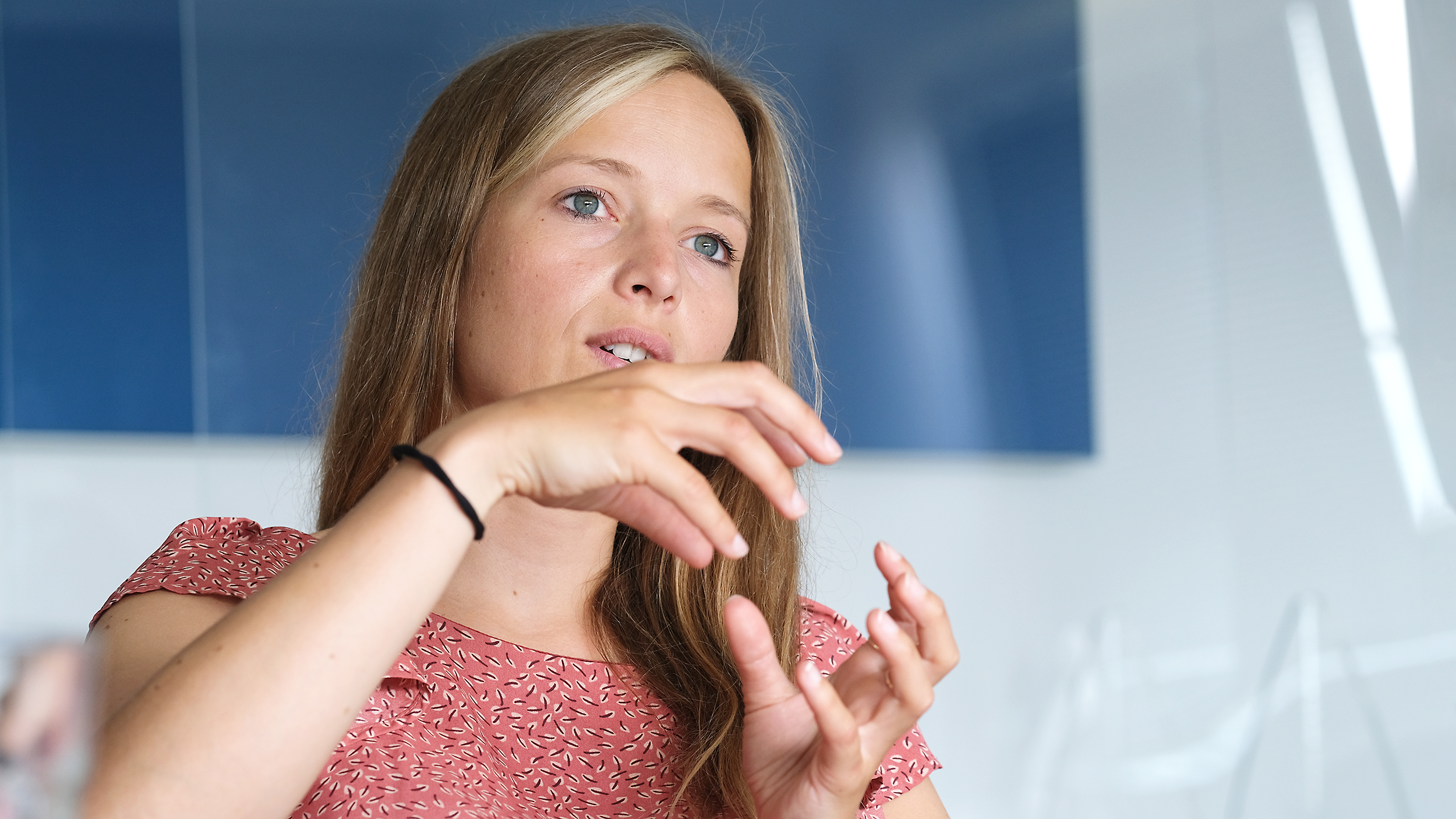
What truly unites the two young entrepreneurs is the goal on which they resolutely base all their business decisions. “Our mission is for our product to make a real impact,” says Lamp. “We want Traceless to replace as many plastic products as possible, especially those that could end up in the environment or for which we don’t have the right recycling techniques.” Traceless has a wide range of potential applications. The granulate can be used to make wraps and coatings as well as alternatives to hard plastics. Packaging and single-use products are high on the agenda as well. Products like straws, ice cream spoons, fruit and vegetable containers, and e-commerce packaging materials could all be replaced by Traceless in the future. In order to clearly distinguish these end products from their conventional plastic counterparts, each will be stamped with the Traceless logo.
Traceless—Holistically Sustainable
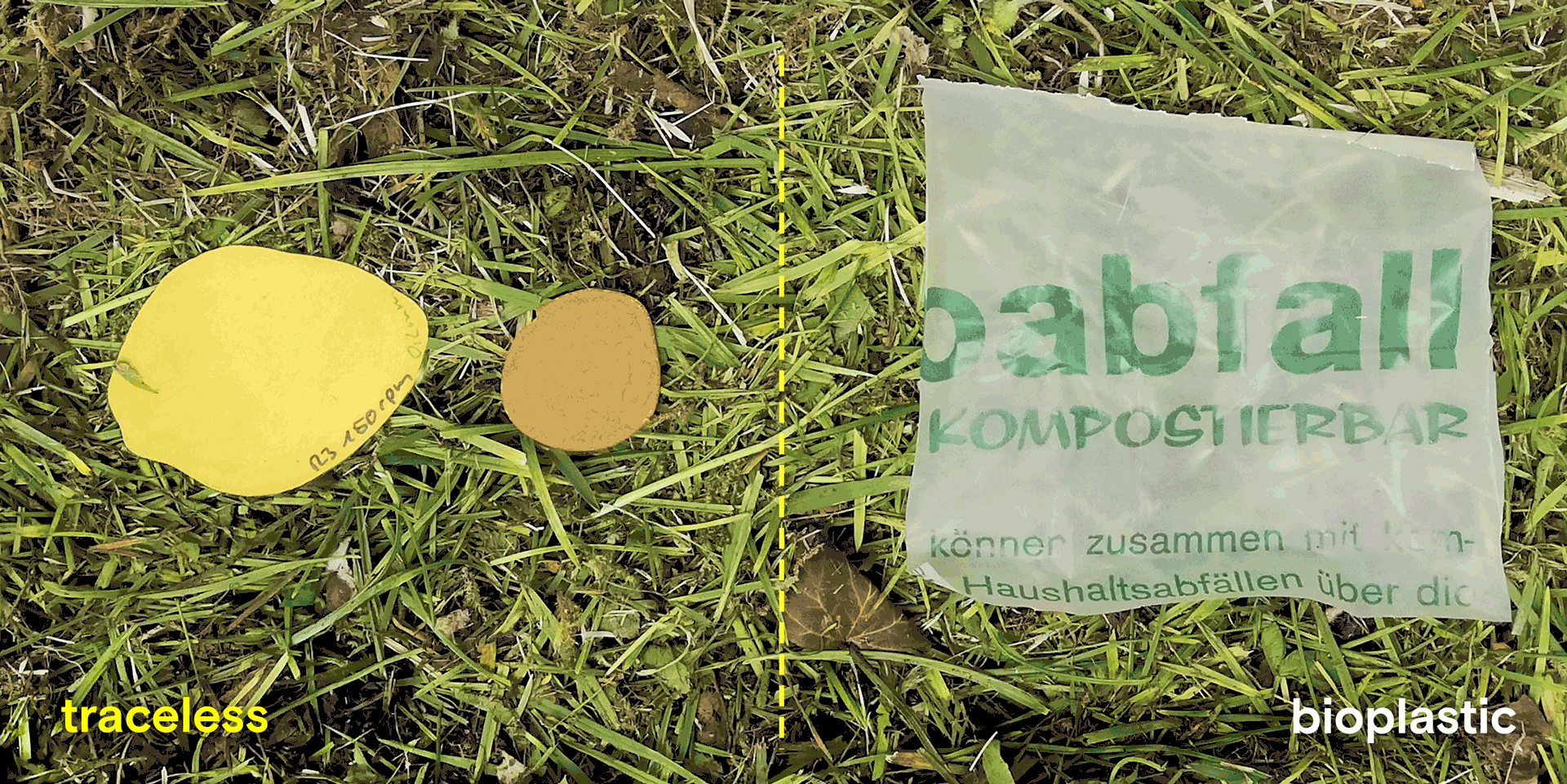
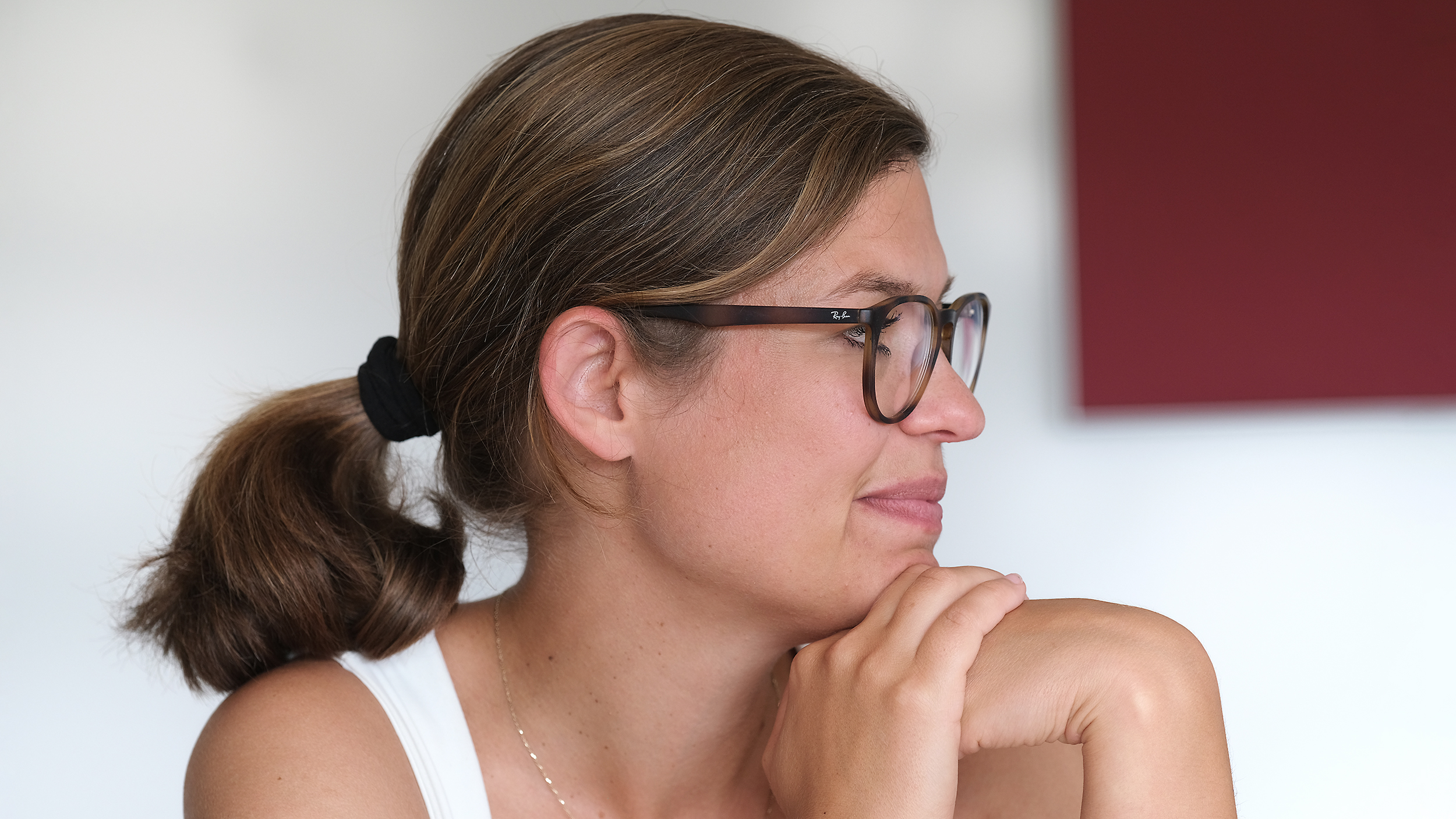
From pilot phase to takeoff
In conjunction with several partners, including the Otto Group and Lufthansa AG, a 22-member team is working intensively on the first pilot products. Plans call for Otto to already start testing Traceless shipping materials in 2022. And Lufthansa, Germany’s largest airlines, is ready to use the first prototypes for its onboard packaging. Further steps are needed, however, before production can begin on an industrial scale. The granulate is currently being made in small batch sizes at the first pilot plant in Buchholz. “Compared to the volumes we used to make at the lab, that’s already quite a lot for us,” says Baare. “But it’s essentially nothing for the plastics industry so we really have to scale it up. That’s our greatest challenge, but it’s also a major incentive to ramp up our material production as fast as possible because there’s clearly a high level of demand.” The team is preparing to start up a larger plant in 2024, in order to produce on a mass scale and be capable of replacing entire product lines with natural materials in the near future.