The Race for Solid-State Batteries
Solid-state batteries could reshuffle the deck on the market for electric vehicles. Whether this new generation of batteries can become a real game changer, however, depends on the success of its researchers and developers. Porsche Consulting analyzed the opportunities offered by the new technology.
07/2023
SIX CHALLENGES
for solid-state batteries
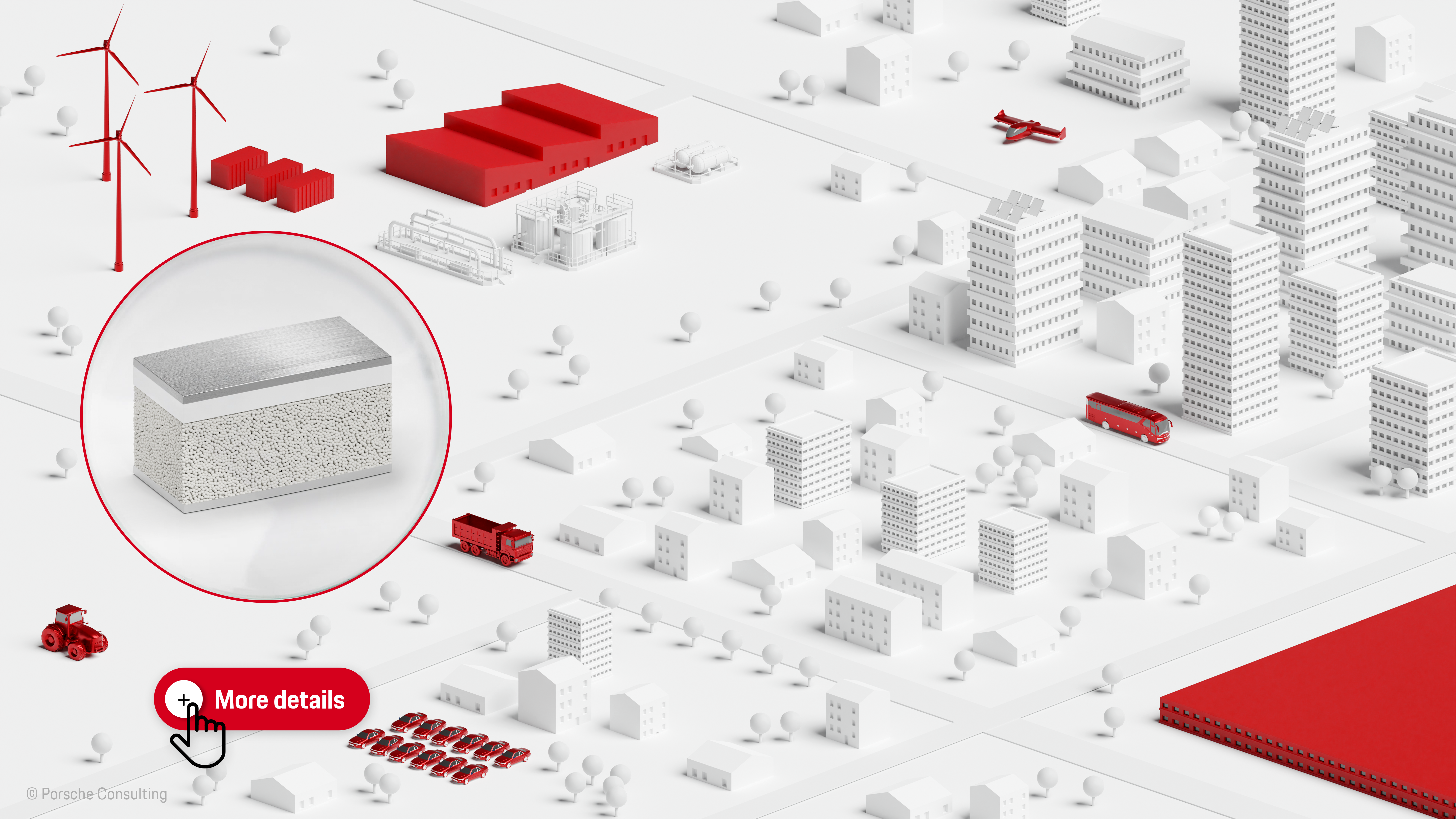
The battery is considered the heart of modern electric vehicles. Many carmakers have long relied on the supplier industry for this most important and valuable component in their products. Yet that appears to be changing. To develop their own core expertise in battery systems and to elevate their brands above the competition with innovative technology, car manufacturers are investing to an ever greater degree in building their own gigafactories. Volkswagen alone plans to open six gigafactories in Europe in the near future—with an overall production volume of more than 240 gigawatt hours.
Porsche Consulting expects the global battery market to surpass 5,500 gigawatt hours by 2030. Two-thirds of this capacity will be used for passenger cars. According to its calculations, the overall market will increase tenfold this decade. But that is only the beginning, because in addition to pumping billions of euros into their factories, automotive corporations are investing enormous sums in an entirely new generation of batteries. Those could completely reshuffle the deck in the field of electromobility.
Innovation needs momentum
Dr. Fabian Duffner, Partner in Advanced Technologies at Porsche Consulting, refers to solid-state batteries as game changers. As he sees it, they can not only revolutionize the automotive world but also enable electrification of aircraft, for example. Their main advantages include longer ranges, faster charging times, and greater safety. Above all, they give carmakers a chance to free themselves sooner from dependence on Asian cell producers. In contrast to the major producers of conventional lithium-ion batteries, most of the leaders in solid-state battery technology are start-ups from the USA.
Duffner cautions against euphoria, however. “Solid-state batteries are not a sure thing,” he states. “Numerous challenges, both technical and economic, need to be mastered before industrial production can begin.” He lists six key areas of activity: improving product and material properties; transforming production to large-scale standards; integrating the batteries into vehicle systems; establishing robust supply chains for new materials and machinery; lowering production costs; and funding the series development and scale-up stage.
Solid-state batteries can be a real game changer for electrification. But huge challenges need to be overcome before industrial production is possible.
Despite the many tasks ahead, nearly all the major carmakers have bought into residue start-ups with the aim of leading the field. Porsche Consulting’s calculations suggest that their investments could pay off. If the challenges are met and the technology can go onto the market as predicted, the consultants see a potential cumulative market for industrial production of solid-state batteries of more than 400 billion euros by 2035.
Will the new technology fulfill its promise and become the next “game changer” in the automotive and other industries? What steps have to be taken to lay the industrial foundations? What is the current state of the technology and what challenges still need to be overcome for the forecasts to be fulfilled? What opportunities and risks do European companies ultimately face? Porsche Consulting The Magazine documents the current state of knowledge about these and other critical questions pertaining to solid-state batteries.
Greater ranges, lower costs:
Car battery development over 130 years
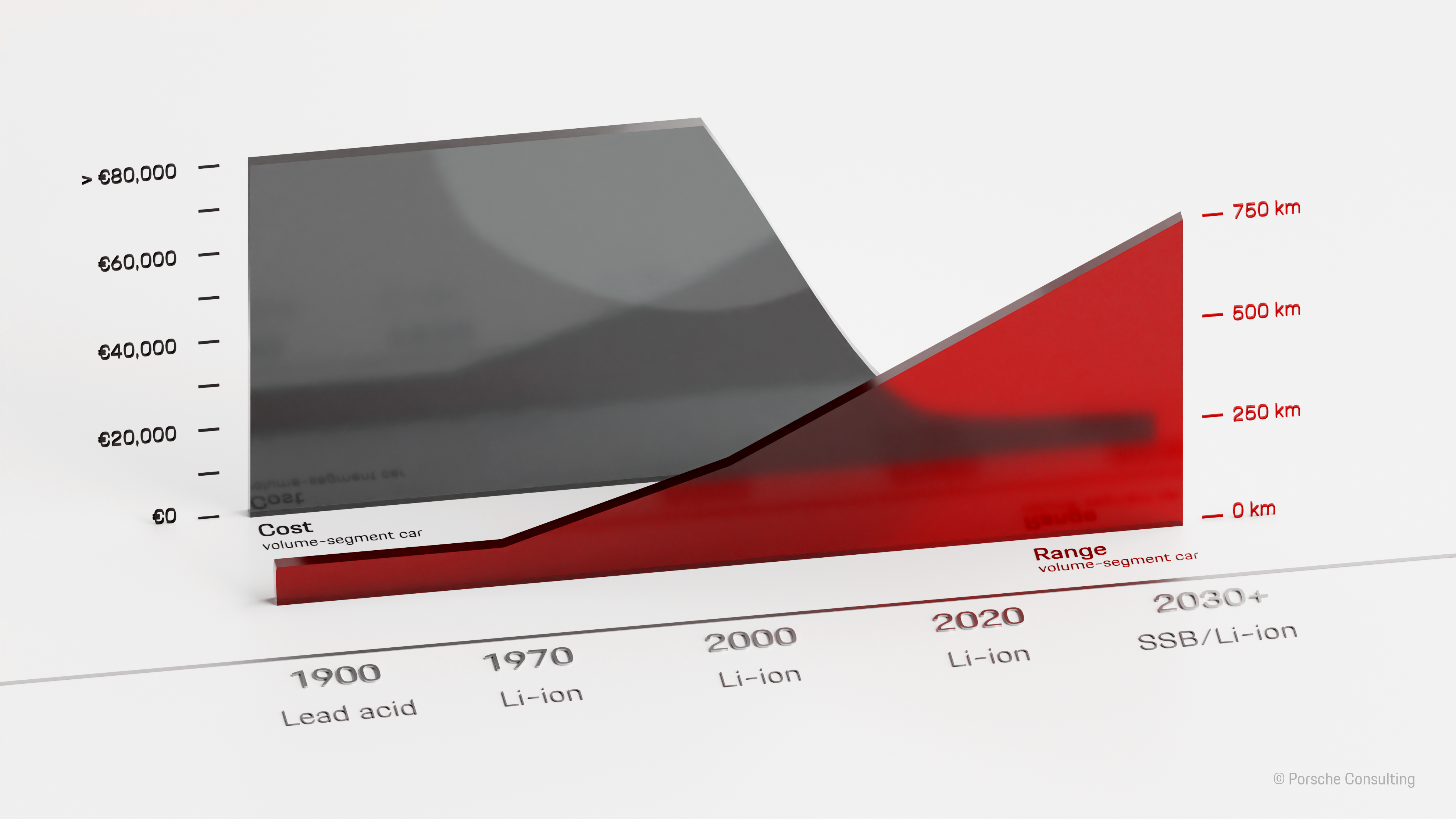
What are the main advantages of solid-state over lithium-ion batteries?
Surveys by market researchers consistently show that customers want electric cars to meet the following three main criteria: long ranges, short charging times, and overall price tags comparable to those for combustion cars. Additional demands on the batteries have to do with their drive power, safety, and longevity. If electric cars can in fact be mass-produced with solid-state batteries, they would meet all these criteria. This would be possible thanks to solid electrolytes, which function as separators between the anodes and cathodes. With chemically stable solid electrolytes, the graphite currently used to store energy could be replaced by other materials such as lithium metal—whose storage capacity is ten times that of graphite by weight. The higher energy density would considerably increase battery volume for the same energy content, which in turn would enable ranges to realistically exceed 750 kilometers as early as 2030.
Finally—Longer range, faster charging, greater safety, and lower costs
Moreover, ions can be transported faster through solid electrolytes, which would put an end to today’s lengthy charging times. Experts estimate that it will take no more than ten minutes to “fuel” an electric car’s battery. This would be hardly any different than filling a tank with gasoline or diesel. The new technology will also enhance safety, because the liquid electrolytes in conventional lithium-ion batteries are flammable. Although it is extremely rare for lithium-ion batteries to catch fire, the risk can be virtually excluded for solid-state batteries.
“In sum, the advantages of solid-state over lithium-ion batteries are enormous. However, the technical issues that have to be solved before the batteries are ready for series production are of a roughly similar magnitude,” observes Duffner.
I believe solid-state lithium-metal batteries will deliver a step-change improvement in performance compared to today’s lithium-ion batteries. Adoption will skyrocket when electric vehicles are equipped with batteries that deliver higher energy density, faster charging times and enhanced safety. That’s what we’re trying to bring to market.
The cell “breathes”
Lithium-ion versus anodeless batteries
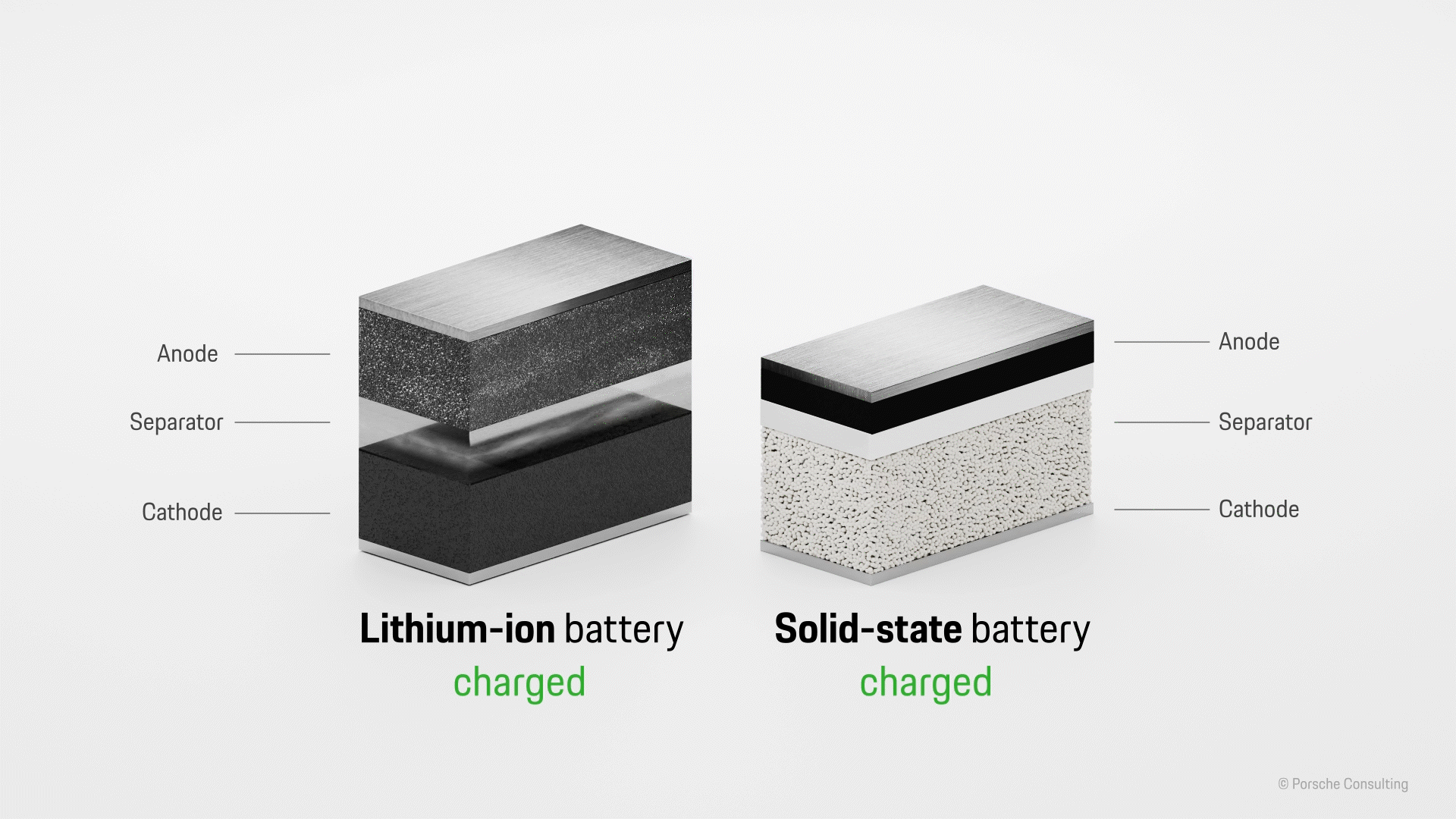
Which markets are relevant for solid-state batteries?
If the associated challenges can be mastered, solid-state batteries will most likely replace lithium-ion models in many areas by 2035. There will probably be a transitional stage in which they will initially only be seen in high-end market segments due to lower production volumes and higher costs. Predictions from Porsche Consulting indicate that premium car brands will be the first to hit the roads with solid-state batteries on board. At the same time, solid-state drive systems might also see initial use in aircraft. These will not be large passenger and cargo planes but rather electric vertical takeoff and landing craft (eVTOLs)—small flying machines with two to six seats that could soon shift taxi services into the skies. The advantages of solid-state batteries here include their lower weight, their higher performance of special relevance for takeoff and landing, and not least of all their positive safety features. Over the medium term, they will be able to power flights of up to 1,000 kilometers.
One battery, many applications
In terms of cost, solid-state batteries will only be able gain an edge over lithium-ion systems after 2030, when industrial production of the new technology picks up speed and further advances in material efficiency are made. At that point they will almost certainly have lifespans equal to or greater than their predecessor models. The use of solid-state batteries will then by no means be limited to electric cars. “On the contrary,” says Dr. Xiaohan Wu, Senior Expert at Porsche Consulting. “The overall improvement in battery KPIs will enable other sectors to be electrified, which is currently inconceivable with today’s technology.”
Even if numerous technical hurdles still stand in the way of series production, lab results already show not only the viability of the solid-state principle but also its outstanding potential.
When will the first solid-state batteries be ready for series production?
Although these batteries have plenty of potential and what looks like an enormous range of applications, research in the field still seems like betting on the future. Although developers have already designed cells that work at room temperature, it could take a few years before large-scale series production is possible. Nor is that a sure thing, because the most promising concepts have thus far only been demonstrated with lab prototypes or are still in pilot phases. At any rate, the industry is still quite far from the highly automated production systems currently used for lithium-ion batteries.
Pilot projects starting in 2024
In addition to the start-ups based primarily in the USA, competency clusters have been formed worldwide, all seeking to industrialize solid-state cells. In Japan, vehicle manufacturers are driving the development of solid-state batteries as part of the NEDO industrial consortium, together with cell manufacturers and material suppliers along the entire value chain. If experts’ expectations are met, pilot projects could be launched in 2024 and large-scale series production might then follow around 2027. It would initially be limited to the premium vehicle segment, which is less sensitive to cost pressures. “We anticipate full industrialization as of 2030, with correspondingly higher performance and lower production costs,” says Dr. Wu. The disruptive quality of the new technology would be evident by then at the latest, and could affect the entire automotive industry. Porsche Consulting accordingly expects cars with solid-state batteries to make up 5 to 15 percent of the market by 2035, which could mean as many as 35 million vehicles out on the roads.
A Nobel Prize was awarded for the invention of the lithium-ion battery. Industrialization of lithium-metal solid-state batteries, which are superior in every way, would qualify for another!
Can gigafactories currently making lithium-ion batteries be converted to solid-state production?
Although late to the game, German carmakers are now fully focused on electromobility and have announced investments worth billions of euros in new gigafactories. These factories, however, are designed to make the power systems currently dominating the market for electric cars, namely lithium-ion batteries. What will happen if the technical issues surrounding solid-state batteries can be resolved by 2027 or so? Can current production processes be easily adapted to the new and better technology? “We estimate that around 40 percent of the machinery in today’s gigafactories is also suitable for making solid-state batteries,” says Professor Jens Leker from the University of Münster (WWU).
But it’s not just a matter of machinery. Processes and manufacturing methods also need to be completely revamped. That is important to ensure cell production efficiency. While some standard processes can be retained, for instance in powder composition, coating, and calendaring, others would need to be added, for example in lamination as well as sintering and pressing. Given the material properties of solid-state electrolytes, a larger number of process steps would also have to be done in a controlled atmosphere.
Converting today’s lithium-ion factories to solid-state battery production will require considerable resources, because around 60 percent of the machines and systems will have to be replaced and the different production areas re-dimensioned.
More streamlined and economical
These and other specific properties of solid-state batteries would lead to higher production costs than for today’s lithium-ion batteries. On the other hand, some properties of solid-state batteries could yield significant savings. Solid-state products can admit of more stable material combinations, for example. This in turn could considerably streamline formation and aging processes—production steps that take up around a third of the space in today’s gigafactories. Moreover, the filling process for liquid electrolytes would no longer be relevant, including the time needed for the liquid to infuse the porous active materials.
When it comes to potential savings, however, the anode is the key component. Producing the anodes for lithium-ion batteries is extremely time-intensive, and also associated with high costs. Around 15 to 20 percent of the floor space in today’s plants is devoted to anode production alone. If anodes are not needed, manufacturers would not need the relevant materials or machinery, either. Nor would the skilled production personnel be needed, or they could be transferred to other areas. The most innovative start-ups in the solid-state field—Quantumscape, for instance—are therefore pursuing cell concepts without any active materials on the anodes at all. Successful development of anode-free solid-state cells will be crucial for the new generation of batteries, according to Duffner. “Solid-state batteries will only trigger the expected transformation in the automotive and other industries if anode-free concepts can be established and the corresponding cost benefits achieved.”
Nine steps to a solid-state battery
How factories can be restructured

What other challenges are associated with solid-state batteries?
In addition to their production, solutions also need to be found for integrating the batteries into vehicles. The main problem here is that solid-state batteries can be said to “breathe.” The expansion and contraction process for lithium-metal anodes can take up more than ten centimeters of space in a vehicle. Engineers therefore have to find ways of integrating volume fluctuations of this magnitude into an otherwise rigid vehicle structure. In addition, today’s prototype cells require substantially larger formats to be relevant for the automotive industry and other applications.
The materials are yet another field with a considerable list of tasks to be tackled before industrialization is possible. The material properties of the three main components of solid-state batteries—solid electrolytes, cathodes, and anodes—need to be improved. The cathode material and solid electrolyte have to be chemically compatible, for example via a suitable coating on the cathode material. Undesirable auxiliary reactions can otherwise significantly reduce the solid-state battery’s lifespan. The solid electrolytes themselves also need considerable enhancement. Above all, researchers need to work on their chemical stability. In addition, ion transport has to be further accelerated if solid-state batteries are to one day form the heart of sports cars.
In order for solid-state batteries to achieve the envisioned energy density, it is important to reduce the thickness of the coating on the solid electrolyte separator to fewer than 20 micrometers. That is roughly three times thinner than a human hair. It poses a huge challenge for large-lot production, because the separators have to be not only thin but also “pinhole free,” i.e., without the tiniest irregularities on their surfaces. Moreover, these dense separators are needed on a very large scale: if a production capacity of 20 gigawatt hours is to be achieved, separators are needed that, laid side by side, would cover an area of 150 million square meters—equivalent to around 20,000 soccer fields. To keep costs under control here, failure rates for these valuable solid electrolyte separators need to be minimized.
Securing new supply chains
It will take a few years for researchers and developers to improve the properties of solid-state batteries to the point that industrial production can begin. But even that will not mean all the problems are solved. The industry’s next step will consist of setting up supply chains for the new materials. In doing so, the existing chains for lithium-ion batteries will be of only limited use. The requisite set of chemicals is simply too different. Supplies of high-demand raw materials like lithium, in particular, will need to stabilized with respect to both their availability and price. Solid-state electrolytes contain up to 50 times more lithium per unit of volume than conventional liquid electrolytes.
Given these considerations, Porsche Consulting’s battery experts predict it could take up to two years before the supplier industry builds its first plants for the necessary materials. Construction and start-up of the actual battery plants could take even longer, with experts estimating at least two and a half years here. “To save time and costs, the players should start preparing early on and coordinate their processes,” says Senior Expert Wu.
Industrialization of solid-state batteries is also associated with major financial risks. Constructing a pilot plant in the megawatt range already costs 500 million to one billion euros. If planners envision building their own gigafactory with a capacity of up to 20 gigawatt hours, this will require an additional investment of around two billion euros. Machines, systems, and buildings will cost 1 to 1.5 billion. And another 0.5 to 1 billion are projected during the start-up phase for high failure rates and for factory personnel. It is therefore hardly surprising that start-ups like Solid Power and Solid Energy System began looking for partners early on—whether in connection with contract production or as joint ventures with carmakers.
Continued funding for technological advances will be a critical factor in the success of these start-ups. It costs around a billion euros just to scale up from lab to pilot production. Another two billion are needed to put a gigafactory into operation.
Which companies are the leaders in solid-state battery development?
While Asian manufacturers like CATL and LG dominate lithium-ion technology, most of the leaders in solid-state battery technology are start-ups in the USA. The established Asian players are not leaving the field without a fight, however. For example, leading cell manufacturers in Korea are forming close partnerships with their suppliers to drive the technology forward. The big carmakers appear to have learned their lesson from lithium-ion batteries. In order to prevent further dependence on Asian suppliers, they have been investing heavily in tech start-ups.
Volkswagen alone has invested more than 300 million dollars in Quantumscape, a California-based start-up that specializes in anodeless solid-state batteries with solid ceramic separators. In April 2021, Ford and BMW announced they were investing a total of 130 million dollars in Solid Power, a battery developer in Colorado. Solid Power plans to start by bringing solid-state batteries with silicon anodes to the market, and then take the second step of furnishing them with lithium-metal anodes. In any case, these investments appear to have paid off. Both Quantumscape and Solid Power are listed on the stock market and have attained unicorn status with market capitalization of more than a billion dollars.
Use of 3D printers
Mercedes has also made major investments as part of its “Electric only” strategy. In January 2022 the corporation expanded its collaboration with the Taiwanese provider Prologium by several tens of millions of euros. It also bought into Factorial Energy, a Massachusetts-based company whose backers include Stellantis (Fiat,Peugeot, Chrysler). In Europe, Ilika and Blue Solutions (Bolloré Group) are especially prominent in solid-state battery development. While Ilika’s strong showing with small-format prototypes has attracted investors like Jaguar, Land Rover, and Honda, Blue Solutions’ solid-state polymer batteries have already seen commercial use in electric buses (eCitaro) from Mercedes. The technology is not well suited for use in passenger cars, because the temperature behavior requires a long preheating period before start-up.
While material innovations are driving the development of solid-state batteries, new production methods could boost the industrialization process. Sakuu, a California start-up, has developed a new 3D printing process for solid-state batteries. Sakuu wants the technique to accelerate production of the new battery generation, lower costs, and reduce space requirements.
The introduction of cost-competitive solid-state batteries can only occur once large-scale manufacturability is achieved. New techniques such as 3D printing could provide a start-to-finish solution with the necessary material, energy, and capital expenditure savings.
It remains to be seen who will end up winning this race. Chinese producers should not be discounted. The major Asian players have a different starting situation and can therefore develop different strategies of relevance to solid-state batteries. They are seeking in large part to optimize existing lithium-ion batteries. This can be achieved not least of all by successively installing solid electrolytes to produce what are known as “semi-solid-state batteries.” Chinese manufacturers enjoy substantial benefits from their existing gigafactories, which allow engineers to try out many new developments in actual practice.
What opportunities arise for companies?
The disruptive potential of solid-state batteries is opening up entirely new opportunities, according to experts. While Asian manufacturers were instrumental in creating the lithium-ion battery business, German and other European companies can now take the entire value chain for solid-state batteries into their own hands. The financial prospects are promising, according to the experts at Porsche Consulting. The market potential for cell producers alone is estimated at 200 billion euros by 2035. Another 150 billion euros are estimated for the material and supplier industries. And mechanical engineering companies that concentrate on equipping the new gigafactories can expect sales of 70 billion euros.
The shift in technology to solid-state batteries is a chance for mechanical engineering companies to enter all stages of the production process: With high transferability of lithium-ion expertise for established companies, and with lower transferability also for newcomers.
That being said, some obstacles need to be overcome. It remains unclear how the cells can be made on an industrial scale with the requisite quality standards. And the mechanical engineering sector has apparently not read the signs of the time. As of 2022, there were simply no suitable industrial systems for producing solid-state batteries. In other words, there are still some open questions on the road to the solid-state battery. The first players who can provide the right answers will reap the commercial benefits in the future.
Asia leads 2:0 at halftime in the lithium-ion game. We in Europe should take the opportunity right away to move out ahead in production technology and machinery for solid-state batteries.