Neue Schule
in 12 Wochen
Wenn es nach Kleusberg geht, können viele Schülerinnen und Schüler schon bald auf moderne Unterrichtsräume hoffen. In seinen Werken fertigt der deutsche Mittelständler hochwertige, komplett ausgestattete Module, die auf der Baustelle nur noch per Mobilkran eingeschwenkt und miteinander verbunden werden müssen. Individuell planen können Bauherren am Konfigurator. Der Clou: Statt Masse gibt es Klasse.
05/2024
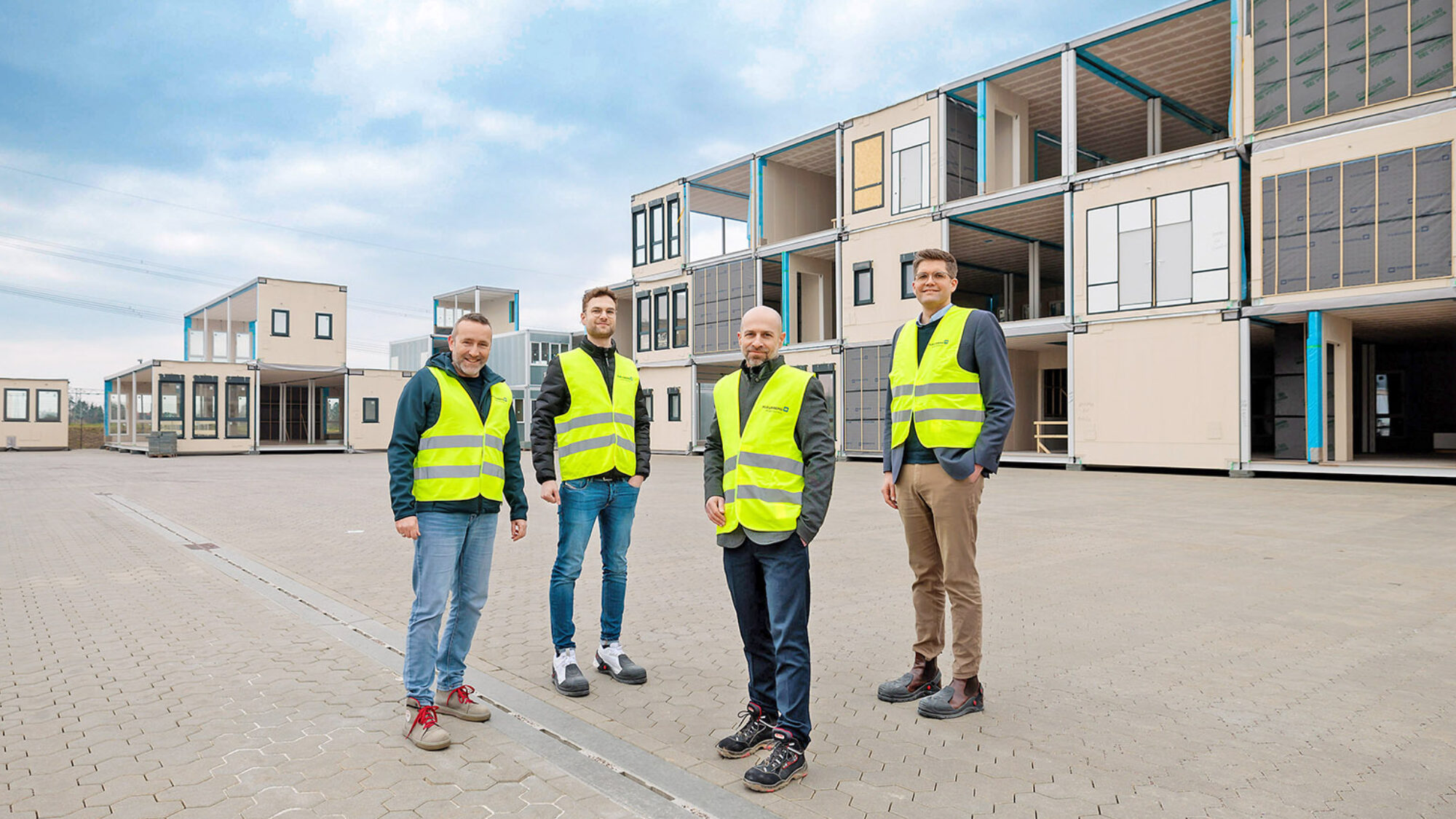
Die Zukunft des Schulbaus steht neben dem Parkplatz von Werk 2 des Modulbau-Unternehmens Kleusberg im ostdeutschen Kabelsketal, nahe der Stadt Halle/Saale. Das Mustergebäude ist ein riegelförmiger, eingeschossiger Quader mit Flachdach und Holzfassade. Er stammt aus dem Schulbaukasten des Unternehmens, der dank vordefinierter Module kürzere Bauzeiten bei gleichzeitig hoher architektonischer Flexibilität ermöglicht. Die Einheit besteht aus modernem Klassenzimmer, Nebenräumen und Sanitärbereich. Neben der verkürzten Bauzeit punkten die neuen Schulen auch im Bereich Nachhaltigkeit: Sie lassen sich bei Bedarf an einem anderen Ort neu errichten und am Ende ihrer Lebensdauer zu fast 100 Prozent recyceln. Kleusberg und die Managementberatung Porsche Consulting zeigen hier ein gemeinsam entwickeltes bedarfsgerechtes und nachhaltiges Konzept. Klassische Probleme am Bau scheinen damit lösbar.
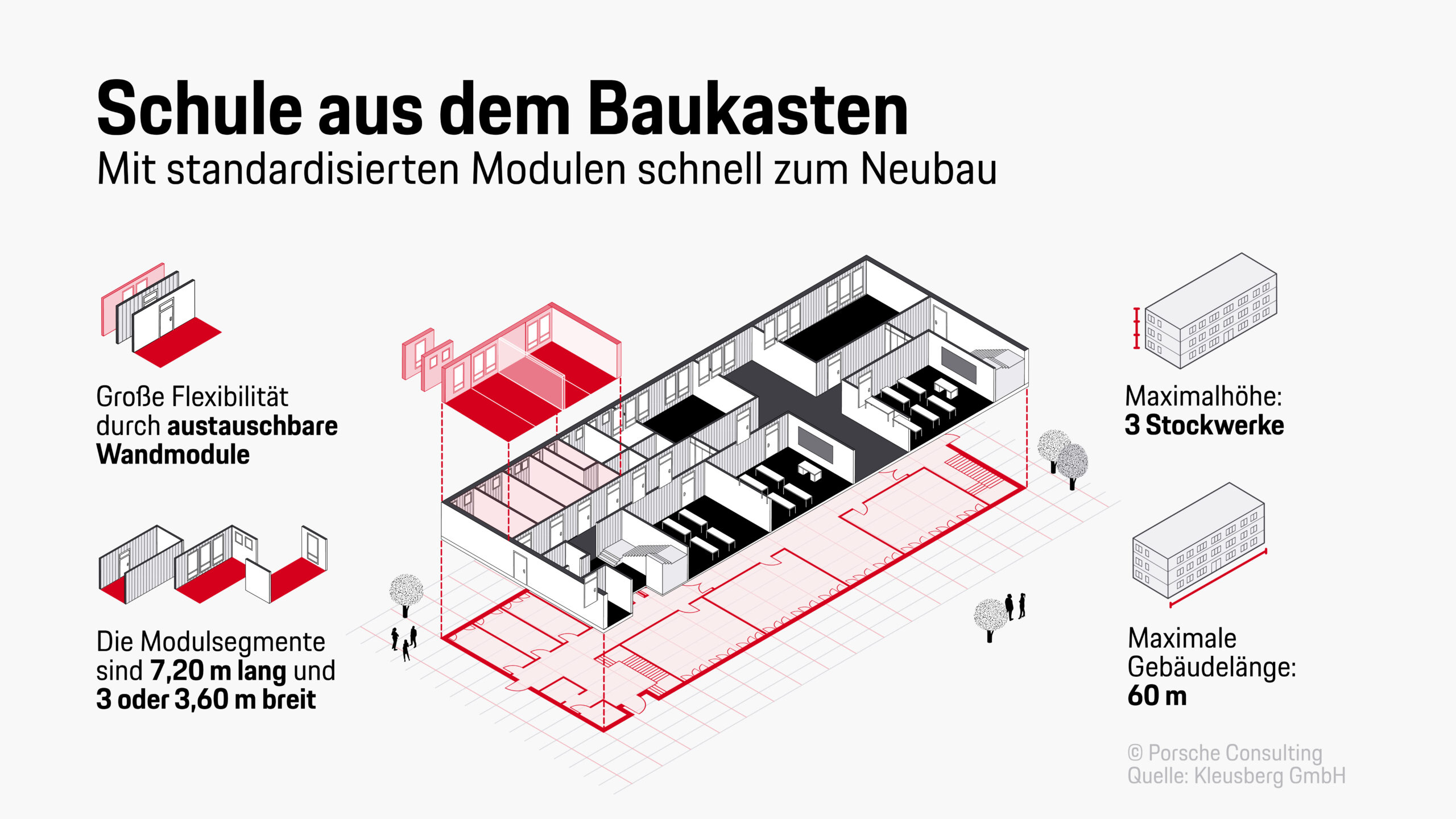
Die Idee dahinter: Schulen sollen in Zukunft – technisch gesehen – nicht mehr als Unikate geplant und gebaut werden, sondern sich einfach aus standardisierten Modulsegmenten konfigurieren lassen. Damit geht Kleusberg einen entscheidenden Schritt über den bereits seit Jahrzehnten etablierten Modulbau hinaus: Aus dem Projekt- wird künftig ein Produktgeschäft. Bauträger können sich neue Schulen dank des Baukastenprinzips aus einem Online-Konfigurator aussuchen und in Auftrag geben – und das, ohne Abstriche bei den Gestaltungsmöglichkeiten machen zu müssen.
Alle Anforderungen an die verschiedenen Funktionen einer Schule wurden von Kleusberg während der Produktentwicklung berücksichtigt. Kurz gesagt: Was Schüler und Lehrer nicht sehen, ist standardisiert. Alles andere rund um die Layoutkonfiguration und Ausstattung lässt sich in weiten Grenzen individualisieren.
„Dieser Produktgedanke ist für die Baubranche neu, denn Bauen verlangt eigentlich nach Individualität – unter anderem wegen der jeweiligen Grundstückszuschnitte und der unterschiedlichen Vorgaben in den örtlichen Bebauungsplänen“, erklärt Kleusberg-Geschäftsführer und Architekt Oliver Hartmann (Jahrgang 1970). „Wir arbeiten stattdessen mit 44 vordefinierten Modulsegmenten, mit denen wir fast jede denkbare Konfiguration realisieren können. Das macht es uns möglich, jede Schule trotz Standardisierung exakt an die Wünsche unserer Auftraggeber anzupassen. Wir zielen mit dem Baukasten zunächst auf Schulerweiterungen oder bis zu vierzügige Grundschulneubauten.“
Kleusberg GmbH: Den Anfang macht eine Schreinerei
Möglich sind riegel-, L- oder Z-förmige Schulgebäude mit vier bis 16 Räumen und maximal drei Stockwerken. Auf rund 500 bis 2.500 Quadratmetern können zwischen 100 und 420 Schülerinnen und Schüler unterrichtet werden – und zwar mit ganz unterschiedlichen pädagogischen Konzepten: Die Modulsegmente des Schulbaukastens lassen sich auf verschiedene Weise kombinieren, sodass klassische Flurschulen mit gleich großen Räumen ebenso realisiert werden können wie Schulen mit unterschiedlich geschnittenen Klassenzimmern oder einer zentralen Mitte, um die sich einzelne Räume gruppieren. So realisiert Kleusberg zeitgemäße Bildungslandschaften – beispielsweise mit Räumen für individualisiertes Lernen oder die Inklusion von Kindern mit Beeinträchtigungen.
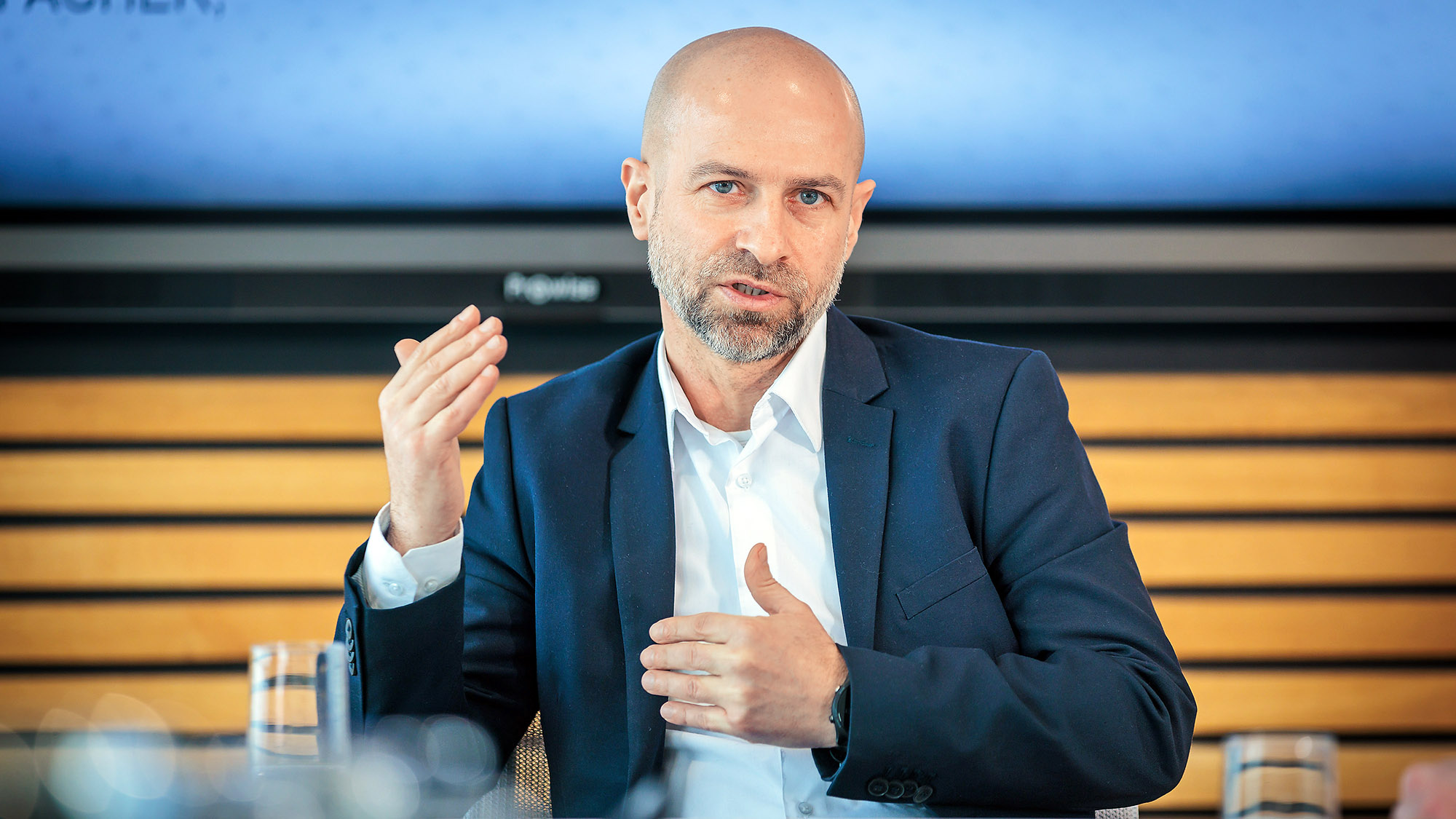
Per Konfigurator zum Unikat
Um seinen Kunden die Auswahl zu erleichtern, bietet Kleusberg die vier Ausstattungspakete „Basis“, „Best Seller“, „Design“ und „Natur“ an. Sie unterscheiden sich unter anderem durch die Gestaltung der Beleuchtungselemente, das Material der Fensterrahmen, die eingesetzte Heiztechnik und die Energieeffizienz der Gebäude. Wer sich durch den von Kleusberg verfolgten Paketgedanken und den Schulkonfigurator an die Automobilindustrie erinnert fühlt, ist auf der richtigen Spur. „Wir hatten bei der Produktentwicklung die Autohersteller im Hinterkopf, die aus einer vorgegebenen Palette von Konfigurationsmöglichkeiten höchst individuelle Lösungen erzeugen, ihren Kunden zur Orientierung ebenfalls Ausstattungspakete anbieten und ihre Produkte seriell auf einer Fertigungsstraße produzieren“, sagt Hartmann.
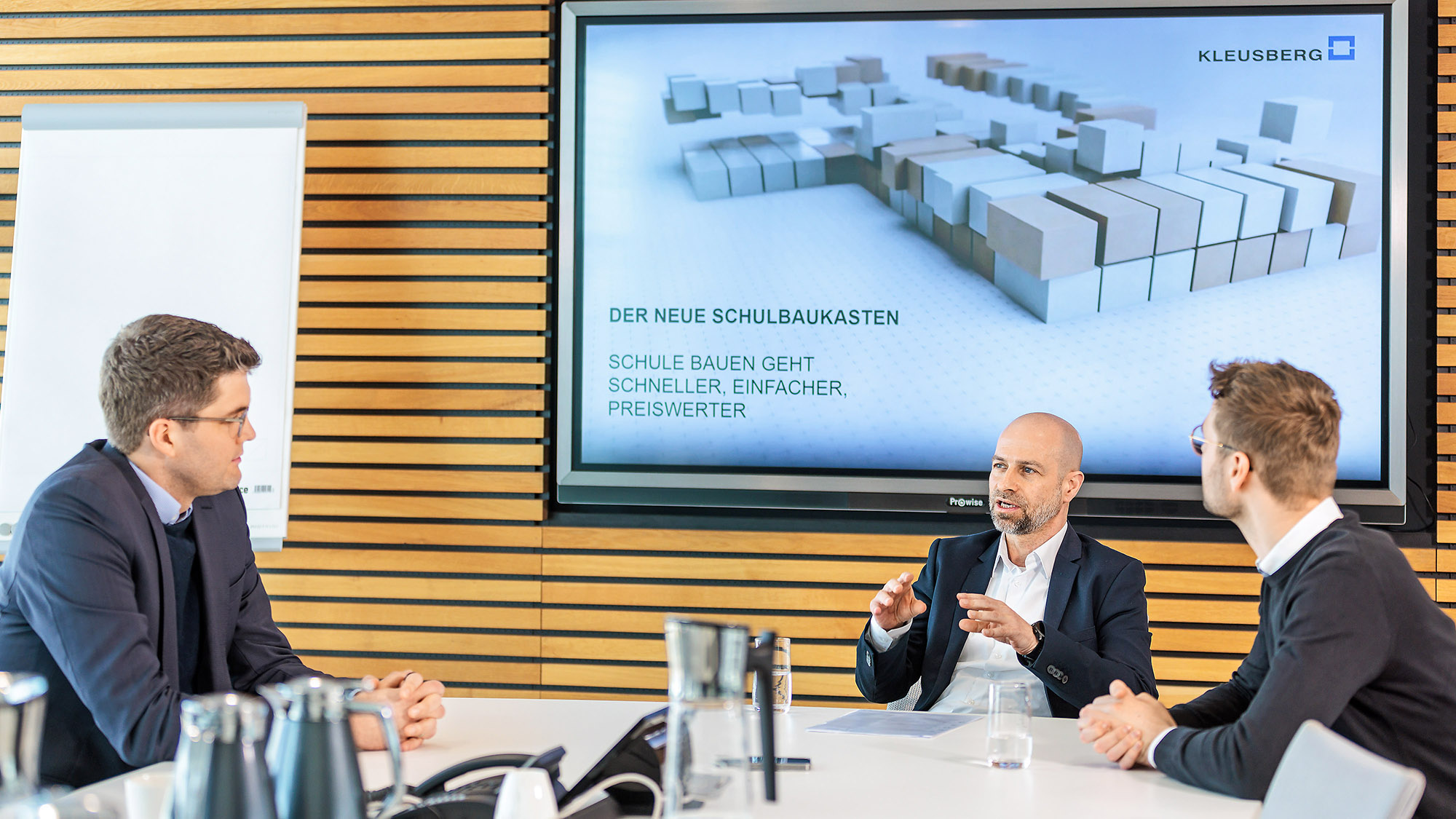
Einen großen Unterschied zur Autoindustrie gibt es aber auch: Es gelten nicht in jedem Bundesland andere Vorschriften für die Zulassung von Fahrzeugen – wohl aber deutschlandweit 16 unterschiedliche Schulbauordnungen. Und so war es eine der größten Herausforderungen bei der Produktentwicklung, allen behördlichen Vorgaben gleichzeitig gerecht zu werden. „Wir wollten einen Schulbaukasten entwickeln, der in allen Regionen funktioniert“, berichtet Jonas Beuth (Jahrgang 1993), der bei Kleusberg die Produktentwicklung leitet. „Darum mussten wir den kleinsten gemeinsamen Nenner aus allen Vorschriften finden.“ Keine leichte Aufgabe, schließlich ist die Zahl der Bauvorschriften in Deutschland allein zwischen 2005 und heute von 5.000 auf 20.000 gestiegen.
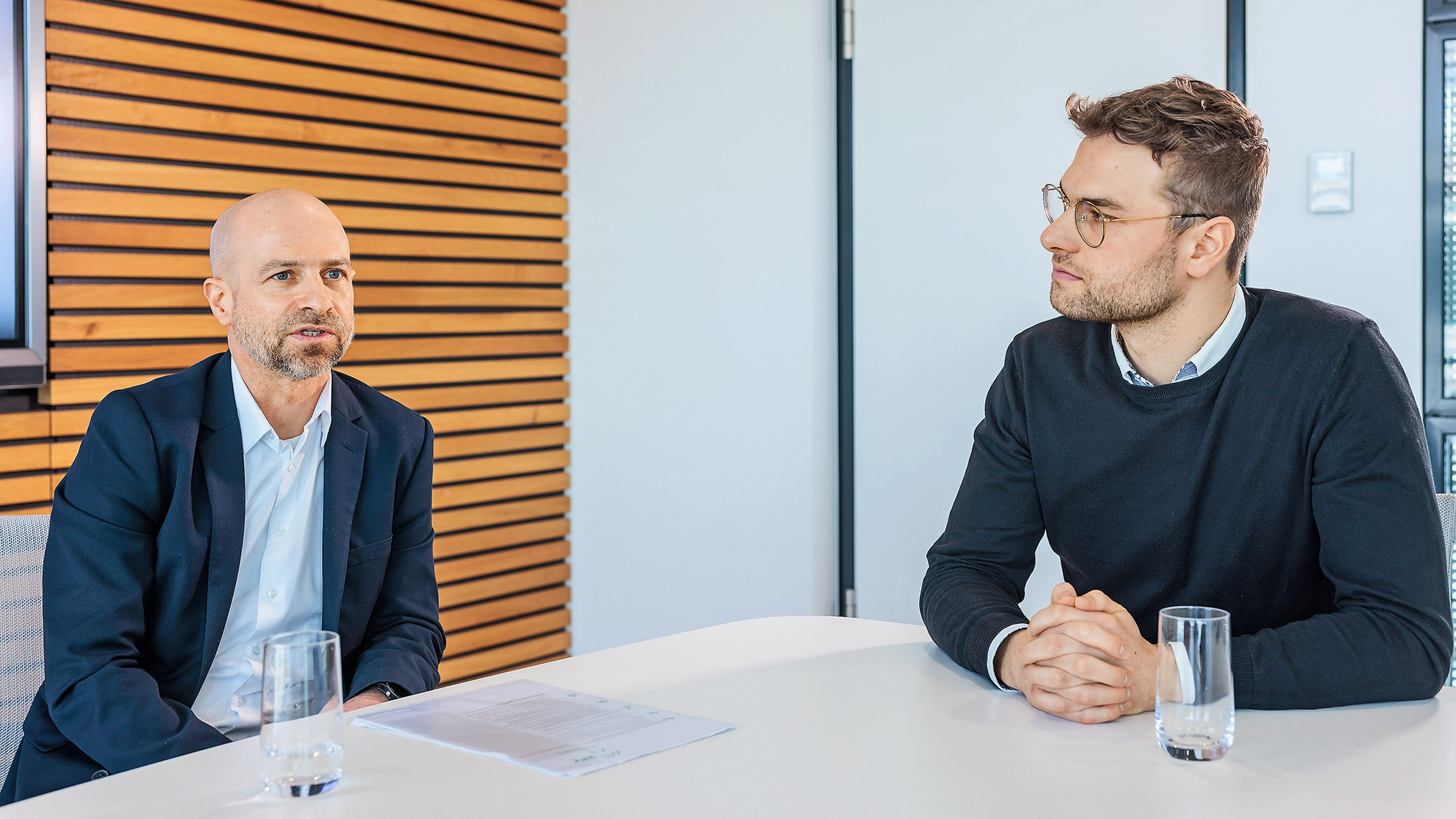
Immerhin musste Kleusberg nicht bei null anfangen. Nach über 160 im Projektgeschäft errichteten Schulen in Modulbauweise wusste man dort sehr genau, was sich die öffentlichen und privaten Bauträger wünschen. Außerdem holte sich das Unternehmen Rat bei Architekten, Lehrern und Hausmeistern. „Ein erfolgreicher Übergang zum Produktgeschäft setzt ein tiefes Verständnis des Marktes und der Kunden voraus – insbesondere, wenn der Produktgedanke wie in diesem Fall noch völlig neu ist“, sagt Tobias Michels (Jahrgang 1989), Senior Manager im Bereich Construction & Real Estate bei Porsche Consulting. Mit seinem Team unterstützte er Kleusberg dabei, den Schulbaukasten für den Alltag in den Gebäuden maßzuschneidern. Michels: „Dabei kommt es manchmal auf vermeintliche Kleinigkeiten an: Je nach Platzierung des Lehrerpults im Klassenzimmer kann es zum Beispiel nur zwei oder bis zu zehn Minuten dauern, bis sich die Schüler am Unterrichtsbeginn beruhigen.“
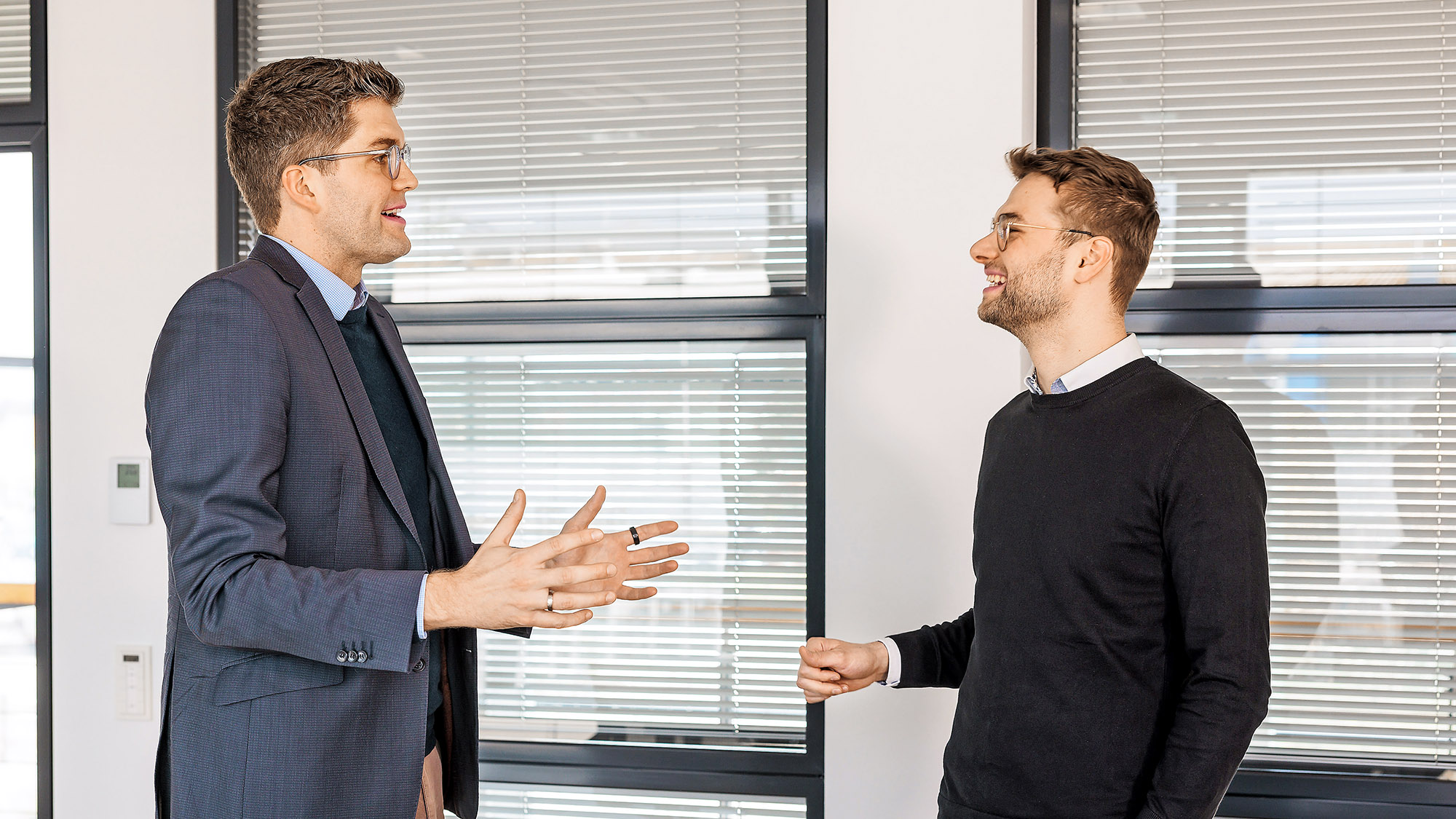
In drei Monaten zur neuen Schule
Eine Zeitersparnis ganz anderer Art ermöglicht die Produktionsweise der Schulbaumodule: Nur drei Monate sollen in Zukunft zwischen Produktionsstart und Schlüsselübergabe vergehen – im konventionellen Schulbau können hingegen schon einmal mehrere Jahre bis zum Einzug vergehen. Möglich macht das die serielle Fertigung der Gebäudebestandteile, die in einer 500 Meter langen Halle auf dem Werksgelände in Kabelsketal-Dölbau stattfindet. Das heißt: Am einen Ende des Gebäudes kommen maßgeschneiderte Stahlprofile für das Tragwerk an, am anderen Ende verlassen pro Woche bis zu 80 komplette Module – bestehend aus den geforderten Segmenten – die Produktionshalle. Dazwischen entstehen an Vorfertigungslinien Komponenten wie Böden, Decken und Wände, die schrittweise an der Grundkonstruktion befestigt werden. Von oben betrachtet erinnert das Layout der Fertigung an eine Fischgräte, weshalb Experten auch vom „Fischgräten-Ansatz“ sprechen – eine weitere Inspiration aus den Fabriken der Automobilindustrie.
Nach ihrer Fertigstellung gelangen die Module des Schulbaukastens per Schwertransport vom ostdeutschen Bundesland Sachsen-Anhalt zu ihren Bestimmungsorten, wo sie von Kleusberg zum Schulgebäude zusammengesetzt werden – im Wesentlichen per „Plug-and-Play“, weil Rohre und elektrische Leitungen schon verlegt sind und nur noch miteinander verbunden werden müssen. Selbst die Toiletten und Waschbecken für WC-Räume sind bereits installiert, wenn die Module an der Baustelle ankommen. „Wegen des hohen Vorfertigungsgrades fällt vor Ort viel weniger Arbeit an“, erklärt Beuth. „Dort kümmern wir uns vor allem um die Flurbereiche, die Modulstöße in den Klassenzimmern, die Fassade und das Dach.“
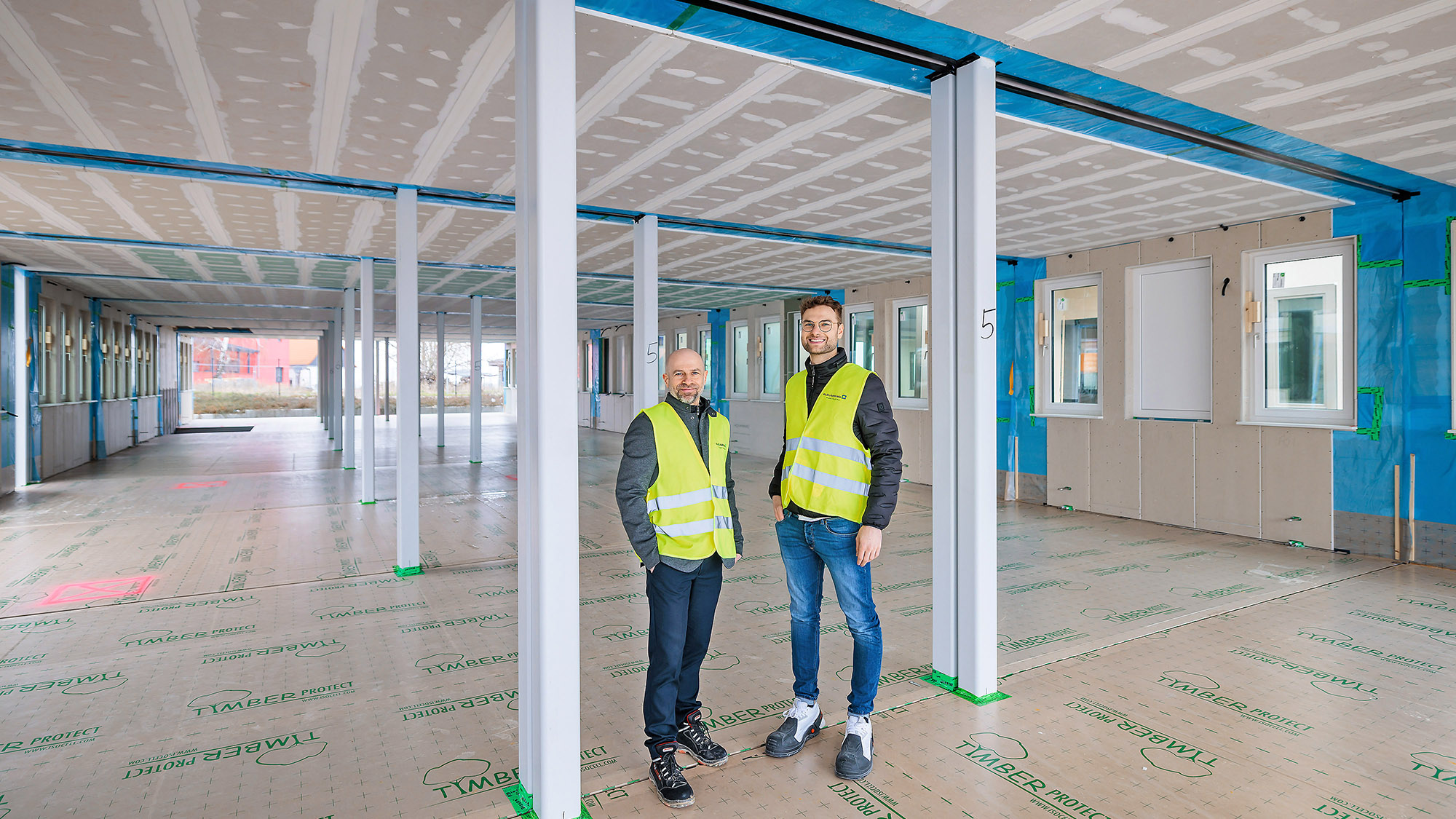
Keine Verzögerungen, keine Mehrkosten
Die serielle Fertigung spart aber nicht nur Zeit: Wegen der größeren Stückzahlen kann Kleusberg bei seinen Zulieferern, zum Beispiel den Sanitärherstellern, auch günstiger einkaufen und mit Nachunternehmern bessere Konditionen aushandeln, weshalb die Baukosten im Vergleich zum herkömmlichen Projektgeschäft-Modulbau um rund 15 Prozent sinken sollen. Hinzu kommt, dass Kostenexplosionen und Verzögerungen dank des Produktansatzes künftig nahezu ausgeschlossen sein dürften, ebenso wie Qualitätsprobleme: Da die Fertigung unter kontrollierten Bedingungen im Werk abläuft, nach jedem Fertigungsschritt eine Qualitätskontrolle stattfindet und alle Produktexpertinnen und -experten bei Fragen schnell greifbar sind, sollten die Module weitgehend gleichbleibende Eigenschaften haben. „Autos kommen ja auch aus einer Fabrik und werden nicht einzeln vor Ort in der Garage des Kunden gebaut – was mit Sicherheit zu sinkender Qualität führen würde“, zieht Architekt Hartmann den nächsten Vergleich mit den Autoherstellern. „Und falls wir in der seriellen Fertigung auf ein Problem stoßen sollten, können wir es schnell erkennen und zuverlässig abstellen.“ Selbst dem zunehmenden Fachkräftemangel auf dem Bau könnte das Konzept entgegenwirken: Immer weniger Menschen wollen bei Wind und Wetter Mauern errichten oder die Außendämmung anbringen. Bei Kleusberg findet die Produktion hingegen hauptsächlich in einer Fabrikhalle statt, was die Attraktivität der Bauberufe deutlich erhöhen könnte.
Die Schule folgt den Schülern
Eine weitere Eigenschaft der Schulen aus dem Baukasten ist den Kleusberg-Entwicklern besonders wichtig: ihre Nachhaltigkeit. Da Außen- und Innenwände sowie Böden und Decken zum größten Teil aus Holz bestehen, weisen die Module eine positive CO₂-Bilanz auf. Sie binden also mehr Kohlendioxid, als bei ihrer Produktion entsteht. Hinzu kommt: Die Module lassen sich auch nach vielen Jahren noch problemlos voneinander lösen und wiederverwenden. „Wenn es in einer Gegend zu wenige Schüler gibt, können wir eine bestehende Schule demontieren und an einer anderen Stelle mit größerem Bedarf neu aufbauen“, so Hartmann. „Nachhaltiger geht es wirklich nicht.“
Potenzielle Kunden reagieren bisher sehr positiv auf die Schulbaukasten-Idee. „Zuerst gibt es oft eine gewisse Skepsis, weil wir den konventionellen Weg verlassen“, berichtet Beuth. „Bisher konnten wir aber alle Bedenken ausräumen und Interessenten vom Schulbaukasten überzeugen. Denn Vorteile wie eine kurze Bauzeit und Kosteneinsparungen überzeugen die Bauträger.“ Und deren Bedarf ist groß: Die KfW-Bankengruppe, eine staatliche Förderbank, hat Schulgebäude als den größten Investitionsbereich der Kommunen in Deutschland identifiziert und schätzt, dass rund 47 Milliarden Euro in den Neubau und in die Modernisierung bestehender Schulen fließen müssen. Hinzu kommt, dass die Zahl der Schülerinnen und Schüler bis 2030 um rund neun Prozent steigen wird – eine Zunahme um rund eine Million.
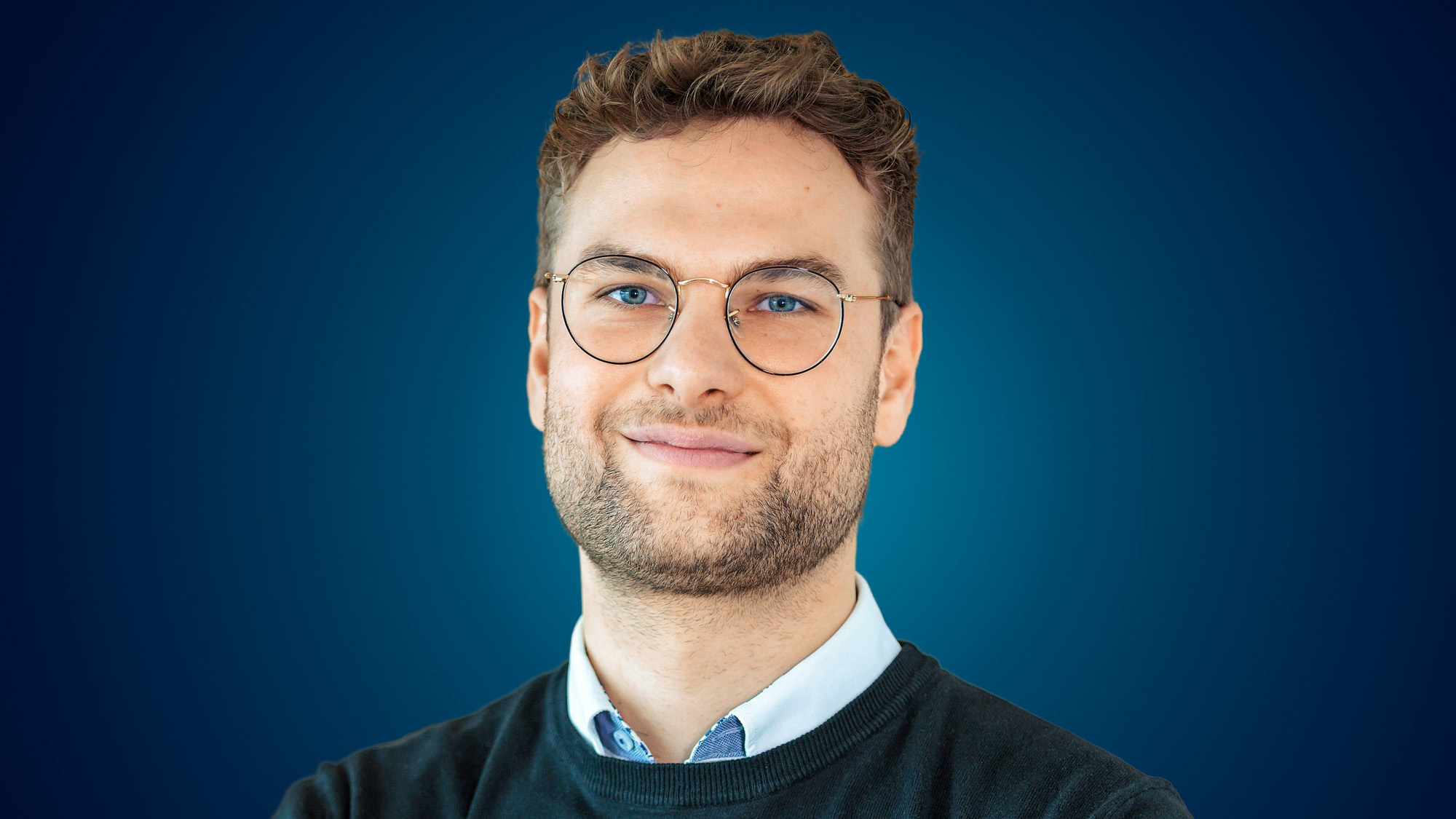
Die Idee ist übertragbar
Kein Wunder also, dass Kleusberg bereits mit ersten Kunden einig geworden ist. Ziel des Unternehmens ist es, in den nächsten Monaten weitere Auftragseingänge für den Schulbaukasten zu verzeichnen. Und natürlich denken die Produktentwickler bereits über diesen ersten Markt hinaus – denn die Idee hinter dem Schulbaukasten lässt sich auch auf den Bau von beispielsweise Bettenhäusern in Kliniken, Studentenwohnheimen oder Unterkünften für Geflüchtete übertragen. Es wäre darum keine Überraschung, wenn auf das serielle Klassenzimmer bald noch viele andere maßgeschneiderte Gebäude aus einem Kleusberg-Konfigurator folgen würden.
Perspektive mit Potenzial
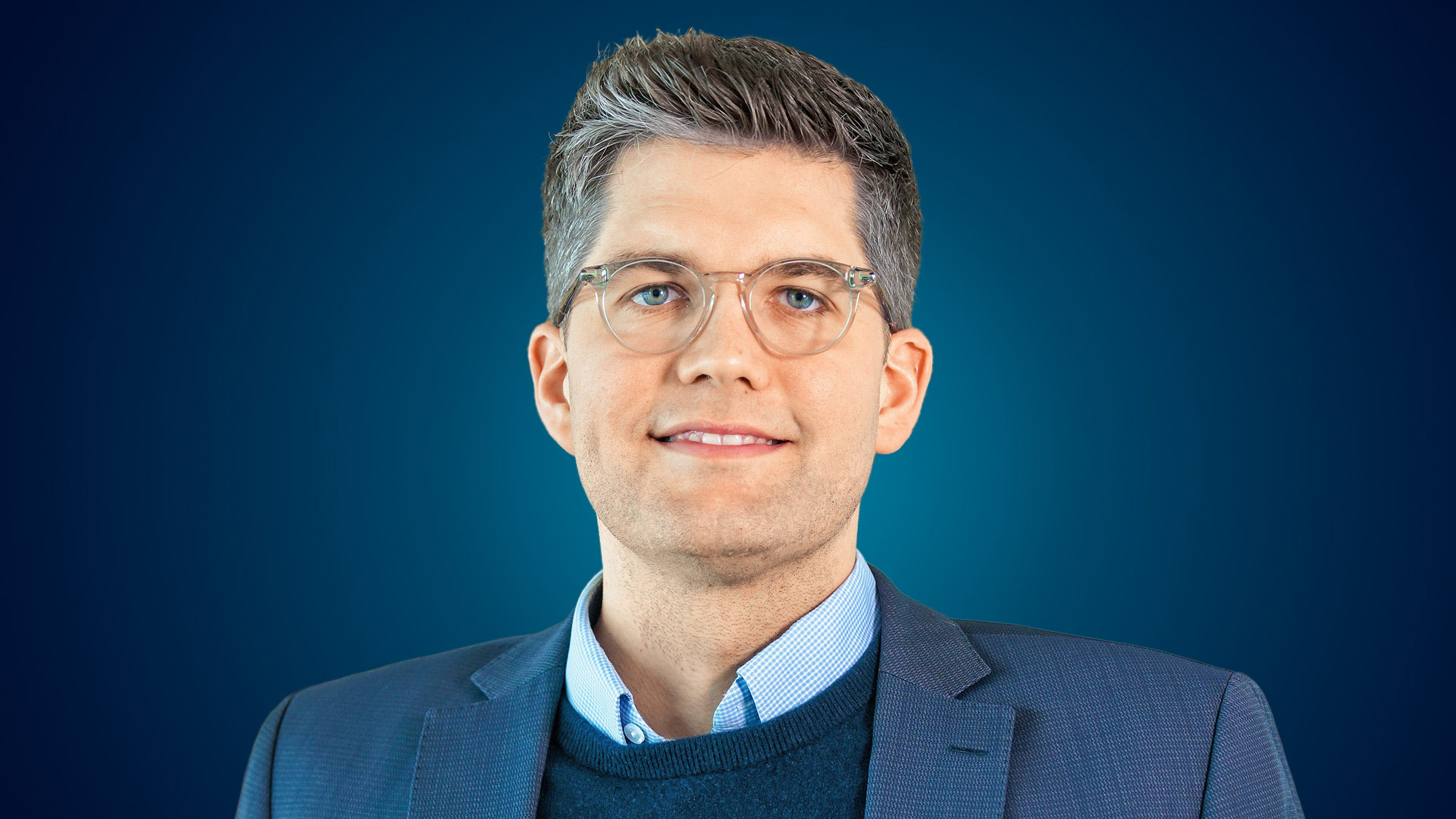