Die Medizintechnik-Fabrik der Zukunft
Mit einer hochmodernen Fabrik setzt Siemens Healthineers neue Maßstäbe in der Medizintechnik. Und ein „digitaler Zwilling“ sorgt mit einer sehr hohen Transparenz für größte Effizienz.
09/2024
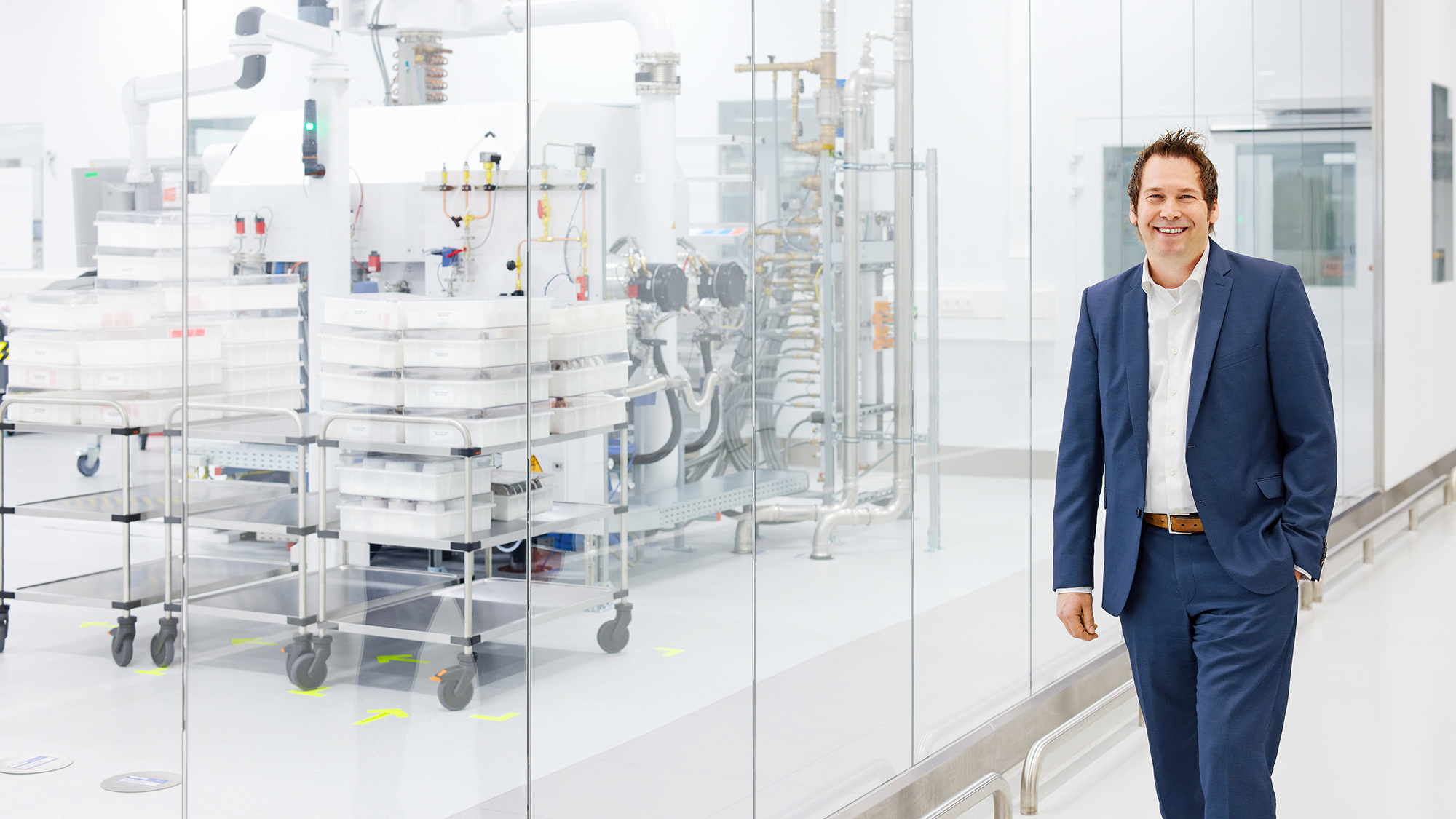
Jeder von uns könnte in diese Situation kommen: Die Medizinische Notaufnahme eines Großstadt-Krankenhauses. Ein Rettungswagen trifft ein. Auf einer gelben Fahrtrage schieben Sanitäter eine Patientin ins Gebäude. Die Mittvierzigerin konnte plötzlich ihren rechten Arm und ihr rechtes Bein nicht mehr fühlen. In der hell erleuchteten Ambulanz ist eine Ärztin schnell zur Stelle, befragt die Patientin. Ihre erste Diagnose: „Minderdurchblutung im Gehirn“. Die Therapie muss sofort beginnen.
Ein Anästhesist versetzt die Erkrankte in Narkose. Die Betäubung setzt ein. Über die Leiste schiebt die Ärztin einen Katheter – eine Art Draht – bis in die Hirngefäße vor. An einem großen Bildschirm sieht sie, wo ihr Instrument gerade ist und wie die Gefäße verlaufen. Sie entdeckt, dass eine Arterie im Gehirn durch einen Thrombus, ein Blutgerinnsel, blockiert ist. Es gelingt der Medizinerin, den Thrombus mithilfe des Katheters abzusaugen. Das Gefäß ist wieder frei. Eine Stunde später kann die Patientin ihre rechte Seite wieder fühlen. Großes Glück. Denn wenig später hätte ein folgenschwerer Schlaganfall eintreten können. Dank der präzisen Diagnose und passenden raschen Behandlung verlässt die Patientin nach wenigen Tagen gesund die Klinik.
Navigationssystem für Ärzte
Szenen wie diese spielen sich in Deutschland mittlerweile viele Tausend Mal jährlich an den entsprechend ausgestatteten Kliniken ab. Und nicht nur dort. „Diese Eingriffe gibt es auch in Japan oder Nepal, in Südafrika oder den USA. Dank neuer, bildgestützter Verfahren hat sich die Prognose von Schlaganfallpatienten enorm verbessert“, sagt Horst Schmidt, Leiter des Geschäftsbereichs Power & Vacuum bei Siemens Healthineers, einem führenden Unternehmen für Medizintechnik.
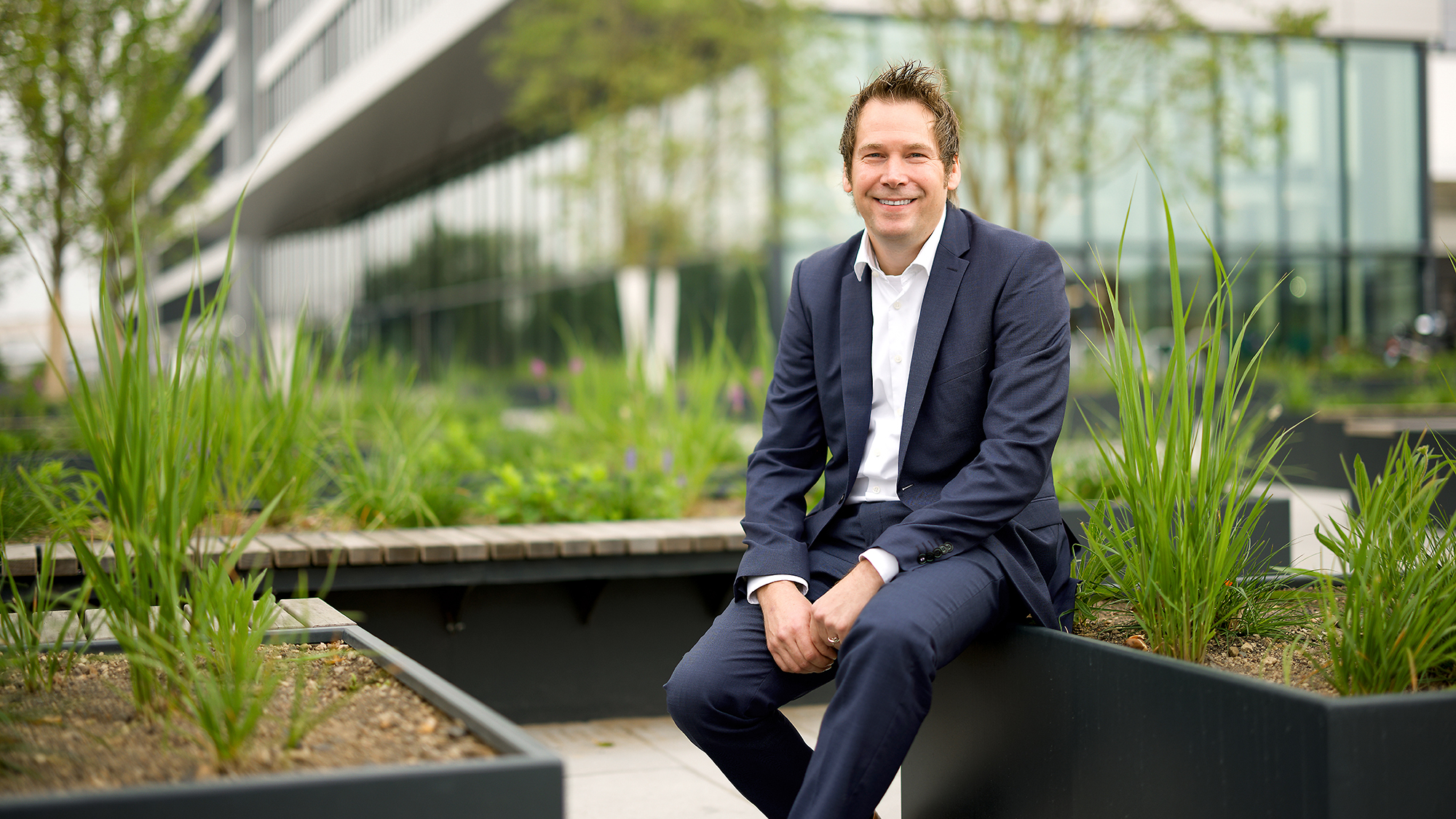
Man sagt in der Neurologie bei der Behandlung auch: Time is Brain. Voraussetzung für eine sogenannte endovaskuläre Schlaganfalltherapie ist neben dem Können des Behandlers, dass er am Bildschirm überhaupt sieht, wo genau er sich im Körper befindet. Ermöglicht wird das durch mehrere Aufnahmen in kurzer Folge. Und die werden zu einer Art Videofilm zusammengesetzt. Diese Bildgebung liefert Siemens Healthineers. „Unsere Geräte sind im Grunde das Navigationssystem des Arztes“, sagt Schmidt. Und für die Herstellung des Herzstücks genau dieser Navigationssysteme ist er zusammen mit seinem Team verantwortlich.
Kaffee verbindet
Schmidts Arbeitsplatz ist das neu errichtete HEP-Center („High-Energy Photonics Center“) von Siemens Healthineers im süddeutschen Forchheim, einer kleinen Stadt (34.000 Einwohner), nahe Nürnberg. Der neue Produktionsstandort, direkt am Main-Donau-Kanal, löst auch zwei ältere Fabriken ab, die an ihrer Kapazitätsgrenze angelangt waren. Hier im HEP werden jetzt die Herzstücke für viele der bildgebenden Geräte von Siemens Healthineers produziert: Die Röntgenröhren mit den Hochspannungsgeneratoren. Wer Höchstleistungen erwartet, braucht eine gute Atmosphäre. Arbeitgeberattraktivität, gutes Zusammenspiel, hohe Motivation. Das neue Gebäude verbindet Produktion und Verwaltung, hautnah. In allen Etagen des Neubaus gibt es lässige Kaffeebars. Hier treffen sich Menschen aus Fabrik und Büros. Der tägliche Kontakt sorgt auch für kurze Wege und schnelle Lösungen bei der interdisziplinären Zusammenarbeit. Aber das ist nur ein kleiner – wenngleich wichtiger – Teil warum das HEP ein Leuchtturmprojekt ist, nicht nur für die Medizintechnikindustrie, sondern für die Produktionsumgebungen der Zukunft insgesamt.
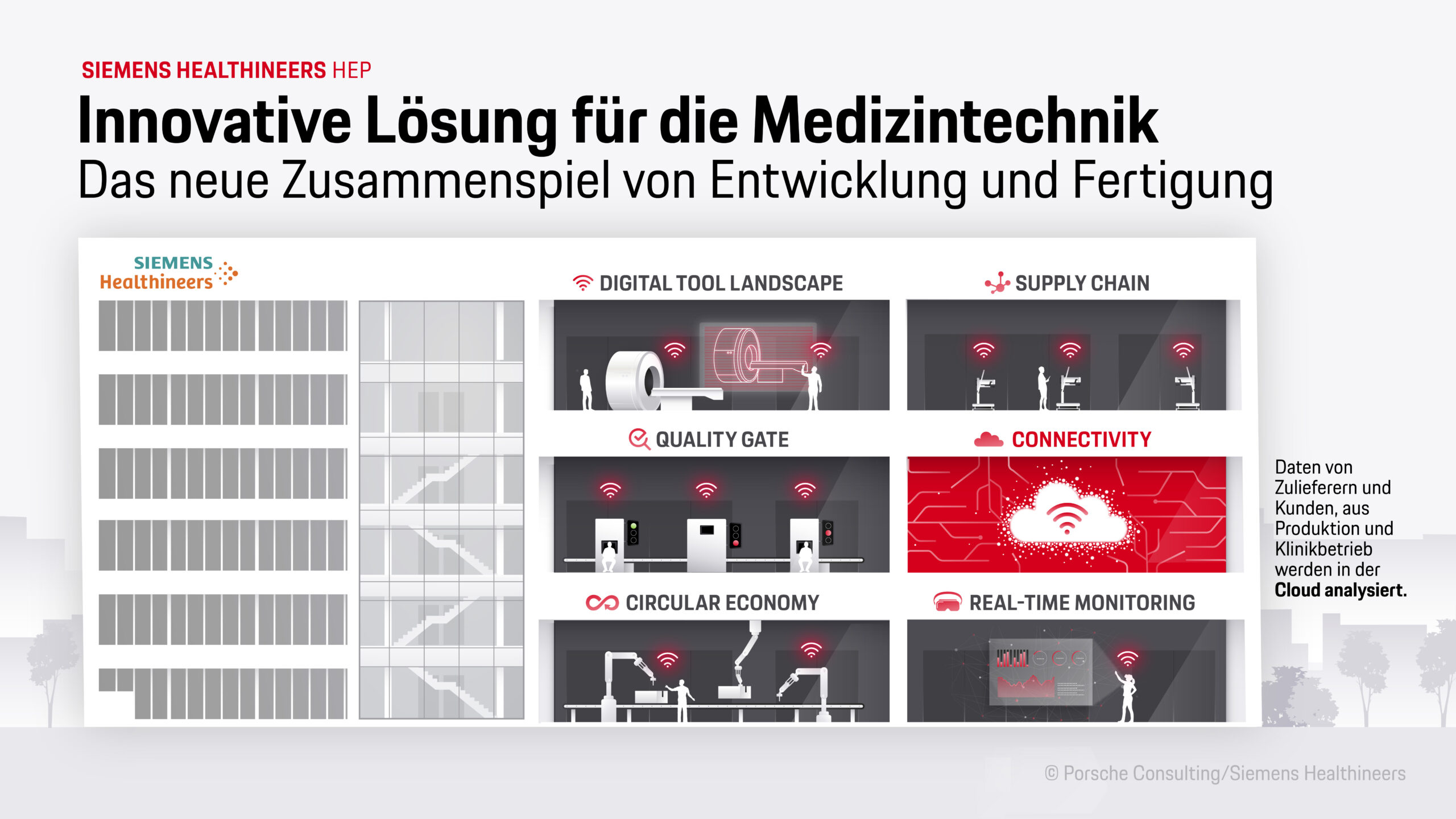
In der transparenten Fabrik ist alles digital miteinander verbunden – von den Produktionsanlagen über die Ausrüstung bis hin zu logistischen Prozessen, einschließlich des digitalen Zwillings des Gebäudes. Die digitale Transformation im HEP Center zielt darauf ab, die Arbeitsleistung zu steigern, Risiken zu minimieren und Wissenstransparenz zu gewährleisten. Beispiele dafür sind:
- Digitaler Shopfloor und Visualisierung: Digitale Tools wie Digital Shopfloor Applications (DSA) und Manufacturing Execution Systems (MES) werden genutzt, um Key Performance Indicators (KPIs) zu visualisieren und Entscheidungsprozesse zu verbessern.
- Digitalisierung von Daten: Das HEP Center konzentriert sich auf die Transformation, Generierung, Verarbeitung und Vernetzung digitaler Daten, um die Wertschöpfung von Produktions- und Geschäftsprozessen zu steigern.
- Automatisierung: Durch den Einsatz neuer Hardware wird mindestens ein manueller Schritt in jedem Prozess automatisiert.
Natürlich geht es bei einer neuen Produktionsanlage heute um Effizienz, Automatisierung und Digitalisierung. Das gesamte Gebäude ist digitalisiert und vernetzt, jedes Bauteil lässt sich digital verfolgen. Trotzdem fallen keine Arbeitsplätze weg. „Das HEP wurde errichtet, um durch einen erhöhten Output mehr Wachstum zu schaffen“, sagt Schmidt. Und dann nennt er noch zwei andere wesentliche Dinge, die das HEP ermöglichen soll: Qualität und Präzision. Die Röntgenstrahler, die im HEP entstehen, werden in die Röntgengeräte, in die Mammographiegeräte für die Brustkrebsvorsorge, in die Computertomographen, und in die Geräte der interventionellen Radiographie von Siemens Healthineers eingebaut, die etwa das Arbeiten mit Kathetern im Gehirn oder in den Herzkranzgefäßen ermöglichen. „Das ist ein High-End-Bereich“, so Schmidt. „Unsere Kunden sind Mediziner auf der ganzen Welt, die ihre Patientinnen und Patienten bestmöglich versorgen wollen, zunehmend auch mit mobilen Geräten. Sie streben ständig nach einer noch besseren Qualität, einer noch höheren Auflösung, um noch früher und präziser Diagnosen stellen und Eingriffe vornehmen zu können.“
Roboter übernehmen die Nachtschicht
Ein wesentlicher Schlüssel dafür sind Automatisierung und Digitalisierung der Produktion. 2019 entwickelte Siemens Healthineers gemeinsam mit einem Team der Managementberatung Porsche Consulting das Zielbild einer Smart Factory. „Damals, am Anfang, hatten wir einen recht weiten Weg vor uns. Aber wir haben ihn erstaunlich schnell beschritten“, sagt Dr. Jens Fürst, Principal Key Expert Digitalization & Automation. Nicht einmal fünf Jahre hat die Errichtung des rund 350 Millionen Euro teuren Gebäudes gedauert. Eine sehr gute Zeit für ein derart komplexes Projekt, das auf drei übereinander liegenden, breiten Produktionsebenen und daneben sechs schmaleren Büroebenen eine Fläche von acht Fußballfeldern umfasst.
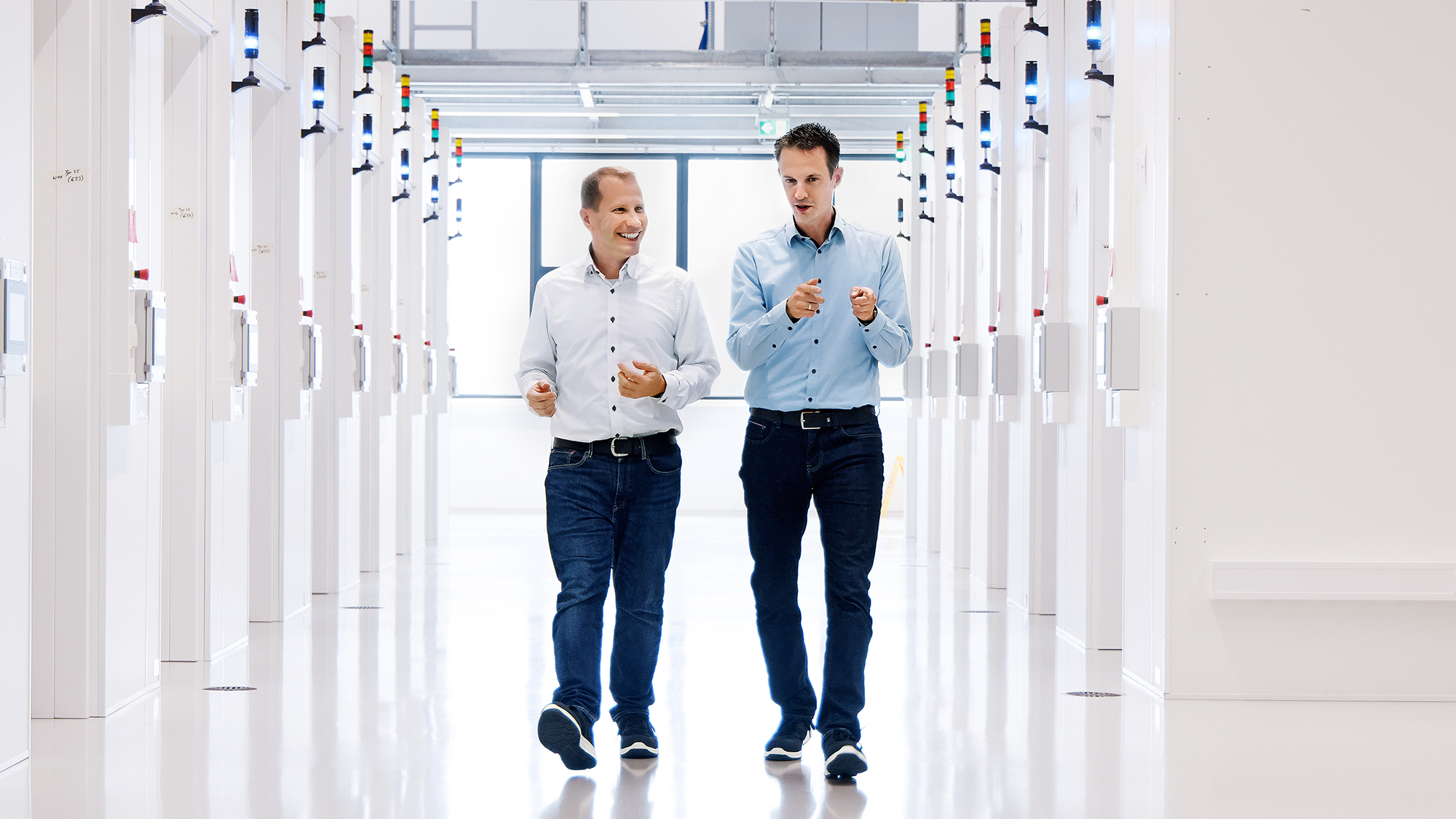
Gäste führt Jens Fürst gern auf den innenliegenden „Balkon“. Das ist eine schmale Galerie im dritten Stock der Produktionshalle, mit imposantem Panoramablick auf die Montagelinien. Aus der Vogelperspektive lassen sich die verschiedenen Schritte der Produktion der Röntgenröhren einschließlich der Generatoren gut überblicken. Grob zusammengefasst geht das so: Zuerst die Fertigstellung der Röntgenröhren im klinisch sauberen Reinraum. Dann werden die Röhren nachts von Robotern automatisch „konditioniert“. Das heißt: Unter Hochspannung erreichen sie einen noch höheren Reinheitsgrad. Am nächsten Tag, wenn die Mitarbeitenden die Frühschicht beginnen, werden die Röntgenröhren in abgeschirmten Kabinen noch einmal von Menschenhand auf ihre Funktionalität und Präzision getestet, bevor sie dann in einem anderen Werk in die Endgeräte eingebaut werden.
Gemeinsam zur Digitalisierungsstrategie
Jens Fürst arbeitet eng mit Dr. Markus Kaupper zusammen. Der blickt zurück auf den Anfang der neuen Fabrik: „Ich war vor fünf Jahren technik- und digitalisierungsbegeistert, konnte aber aus heutiger Perspektive betrachtet nicht wirklich einschätzen, was möglich war.“ Heute ist Kaupper Head of Digitalization des HEP.
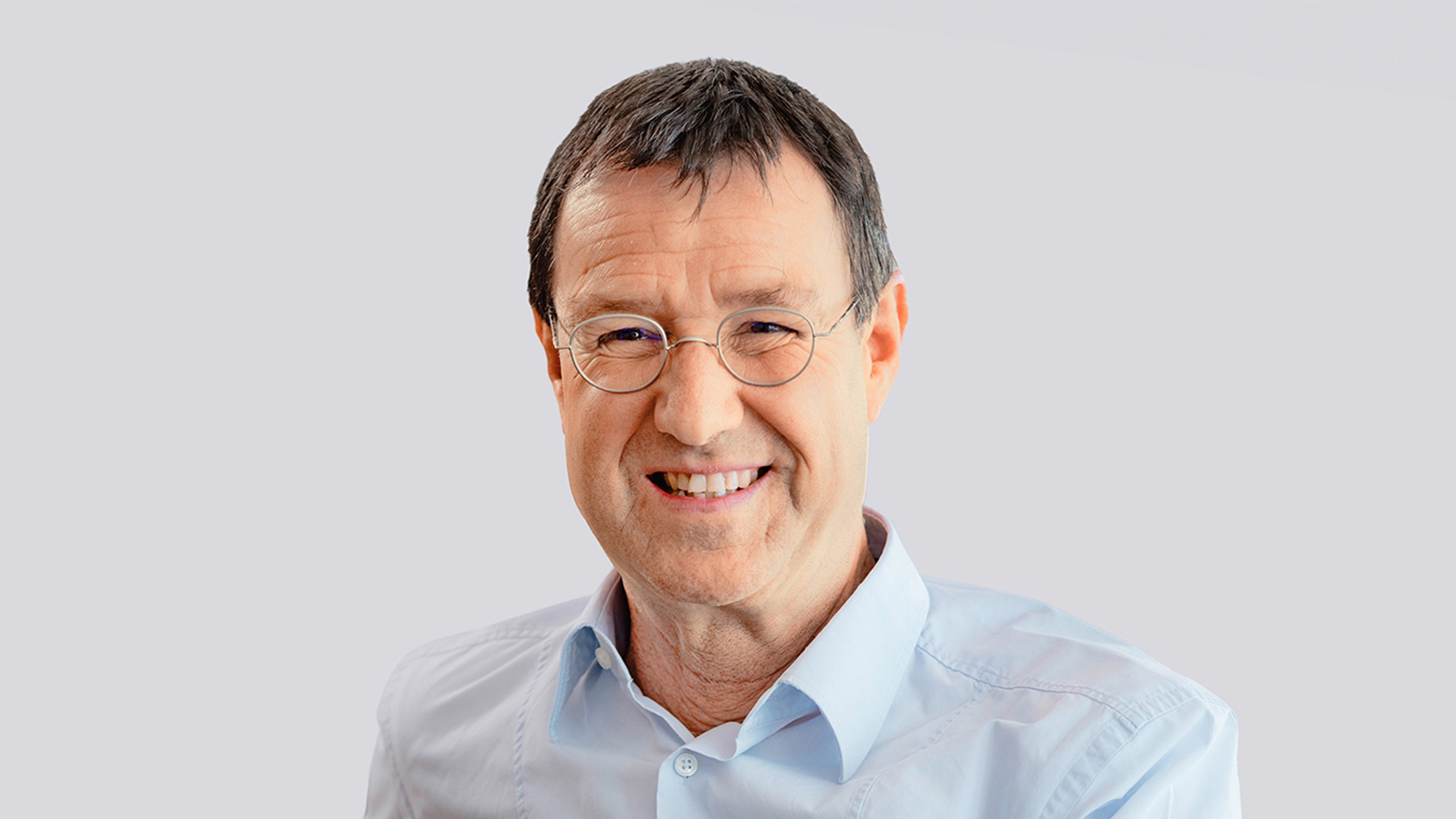
Fast jeder Teil der Fabrik, jeder Prozess, jedes Bauteil, was durchgeschleust und verarbeitet wird – alles ist digital erfasst: seine Maße, sein physikalisches Verhalten, seine Performance-Daten. Ein digitaler Zwilling der Fabrik. „Das HEP repräsentiert unsere erste vollständig digitalisierte Fabrik und ist ein zentrales Element unseres Smart-Factory-Netzwerks“, erklärt Dr. Peter Schardt, Chief Technology Officer von Siemens Healthineers. Und er fügt hinzu: „Ein zuverlässiges und vernetztes Fertigungsumfeld ist im medizinischen Sektor von grundlegender Bedeutung“.
Der Service „ahnt“ den Einsatz
Wenn etwa ein Produkt am Ende der Produktion die Qualitätskontrolle nicht optimal besteht, suchen die Fachleute zunächst im digitalen Zwilling nach Fehlerquellen. Sie finden beispielsweise heraus, dass an einer Stelle die sogenannten Greiferflächen nicht optimal zum Produkt passen. Das kann für Ungenauigkeit sorgen. Und bevor eine neue Produktionslinie in Betrieb genommen wird, geschieht dies zunächst so lange virtuell, bis alle Probleme behoben sind. „Wenn wir es dann in der Realität umsetzen, läuft es meist direkt ziemlich glatt“, sagt Kaupper. Gerade für kleine Produktionslinien, wie es sie hier meist gibt, ist das ein enormer Effizienzvorteil.
Weil der digitale Zwilling ständig mit realen Daten gefüttert wird und diese mit künstlicher Intelligenz verarbeitet werden, kann Siemens Healthineers auch zunehmend präzise Prognosen stellen. Zum Beispiel in Bezug auf den Verschleiß von Bauteilen. So gewähren manche Ärzte als Kunden im Rahmen des Programms „TubeGuard“ Siemens Healthineers Zugriff auf die Sensoren der Geräte in Betrieb. Anhand der Daten lässt sich mittlerweile sehr genau vorhersagen, wann der Röntgenstrahler ausfällt. „Ein Servicemitarbeiter steht dann schon mit dem Ersatz bereit, bevor der Kunde sich meldet“, sagt Horst Schmidt. Noch ein Effizienzgewinn – für Siemens Healthineers ebenso wie für die Kliniken und Mediziner, die damit die vergleichsweise kurze Ausfallzeit für einen nötigen Austausch so punktgenau planen können.
Lust auf eigene Programme
Das Arbeiten im HEP ist auch für die Mitarbeitenden eine grundlegende Umstellung. „Diesen Grad an Automatisierung und Digitalisierung kann man den Menschen nicht mal so eben überstülpen“, sagt Verena Gollisch, Transformation Managerin beim HEP. „Viele einstige Tätigkeiten fallen weg, viele Mitarbeiterinnen und Mitarbeiter mussten sich neu orientieren. Das kann die oder der Einzelne als Chance sehen, oder als Bedrohung. Es war und ist uns wichtig, unsere Mitarbeitenden frühzeitig einzubinden und Raum für Mitgestaltung zu schaffen, um direktes Feedback zu erhalten und die Chancen des HEP für alle anfassbar zu machen.”
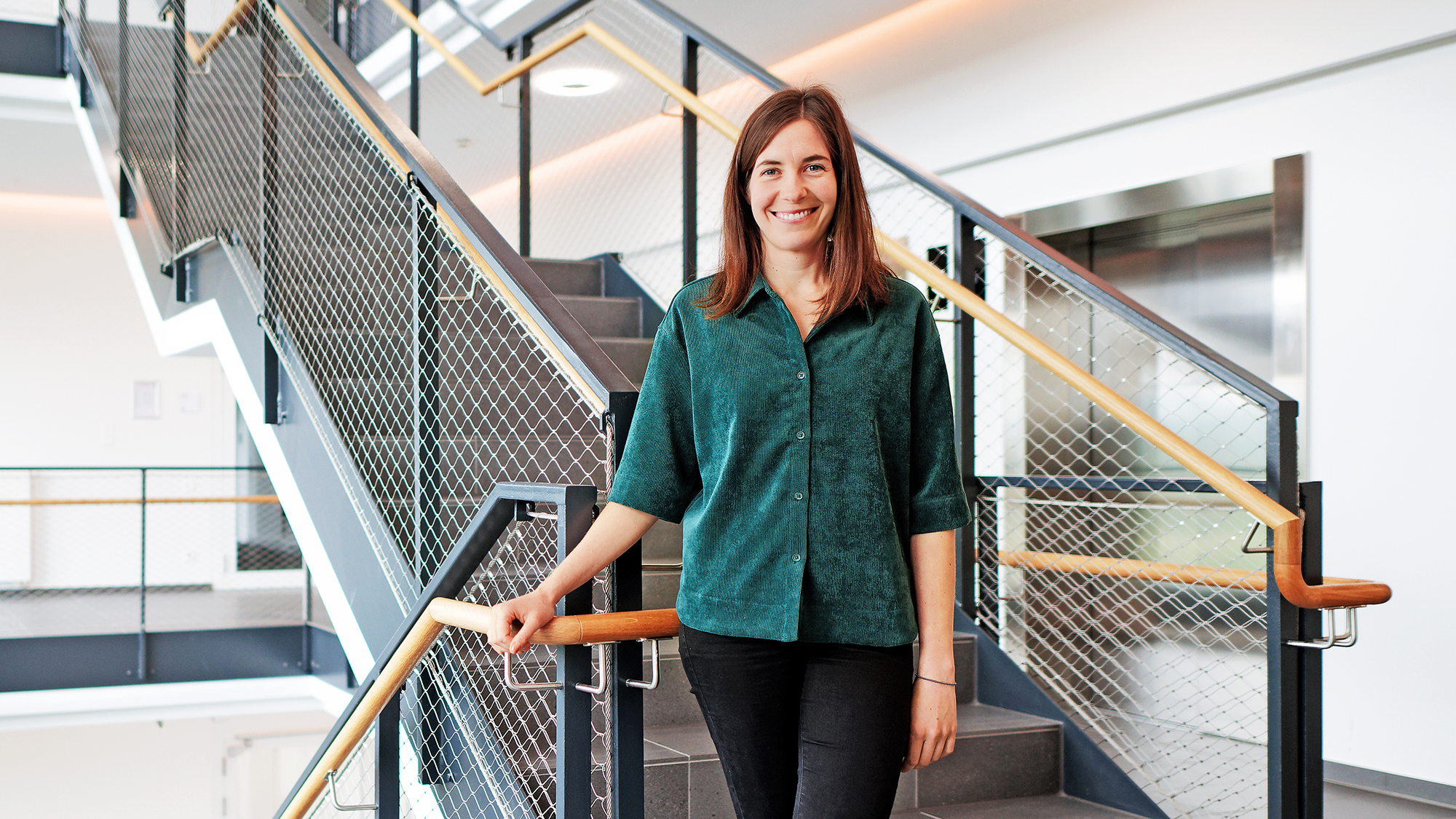
In zahllosen Veranstaltungen wurden die Mitarbeiter beim Aufbau des HEP eingebunden; in „Hackathons“ konnten sie Software-Programme schreiben, um die Abläufe zu verbessern, in geschützten Räumen ließen sich neue Einsatzgebiete ausprobieren. Heute, das Werk ist fast vollständig hochgefahren, betont Kaupper, dass die Umstellung auch auf Seiten der Mitarbeiter geglückt ist. „Wir haben viele Talente in unserem Team entdeckt. Da ist zum Beispiel die Logistikfachkraft, die in ihrer Freizeit gerne programmiert und eine App entwickelt hat, um das Smartphone als Scanner zu benutzen“, sagt Kaupper.
Hier bleiben Menschen unersetzlich
Viele Arbeitsplätze haben jetzt einen großen Bildschirm, auf dem der Computer dem Personal anhand von Bildern zeigt, was sie mit welchem Werkzeug als nächsten Arbeitsschritt umsetzen sollen. Man kann das als Bevormundung sehen – oder als Hilfestellung, als unmittelbare Qualitätskontrolle, die der Computer den Menschen abnimmt. „Zum Glück herrscht inzwischen in den Köpfen der Mitarbeitenden die Vorstellung vor: Die Computer nehmen den Menschen die Arbeit nicht weg, sie nehmen ihnen Arbeit ab“, sagt Gollisch. Und so ist es ja auch bei den allermeisten Arbeitsplätzen: Der Mensch wird durch Maschinen und Programme ergänzt, indem jeder seine Stärken einbringt. Aber der Mensch bleibt der Chef. Und in manchen Bereichen ist er ohnehin nicht zu ersetzen. Für die Herstellung der Röntgenröhren etwa beschäftigt Siemens Healthineers Glasbläser, ein klassischer Handwerksberuf, der unentbehrlich ist für die High-End-Produkte, die hier im HEP hergestellt werden.
Vielleicht ist das auch etwas, was man sich von diesem Leuchtturmprojekt abgucken kann: Setze auf Automatisierung und Digitalisierung und zähle dabei zugleich auf deine Mitarbeiter: Erst wenn das alles ineinandergreift, handelt es sich wirklich um eine Fabrik der Zukunft.
Vom Ziel zur Zukunft
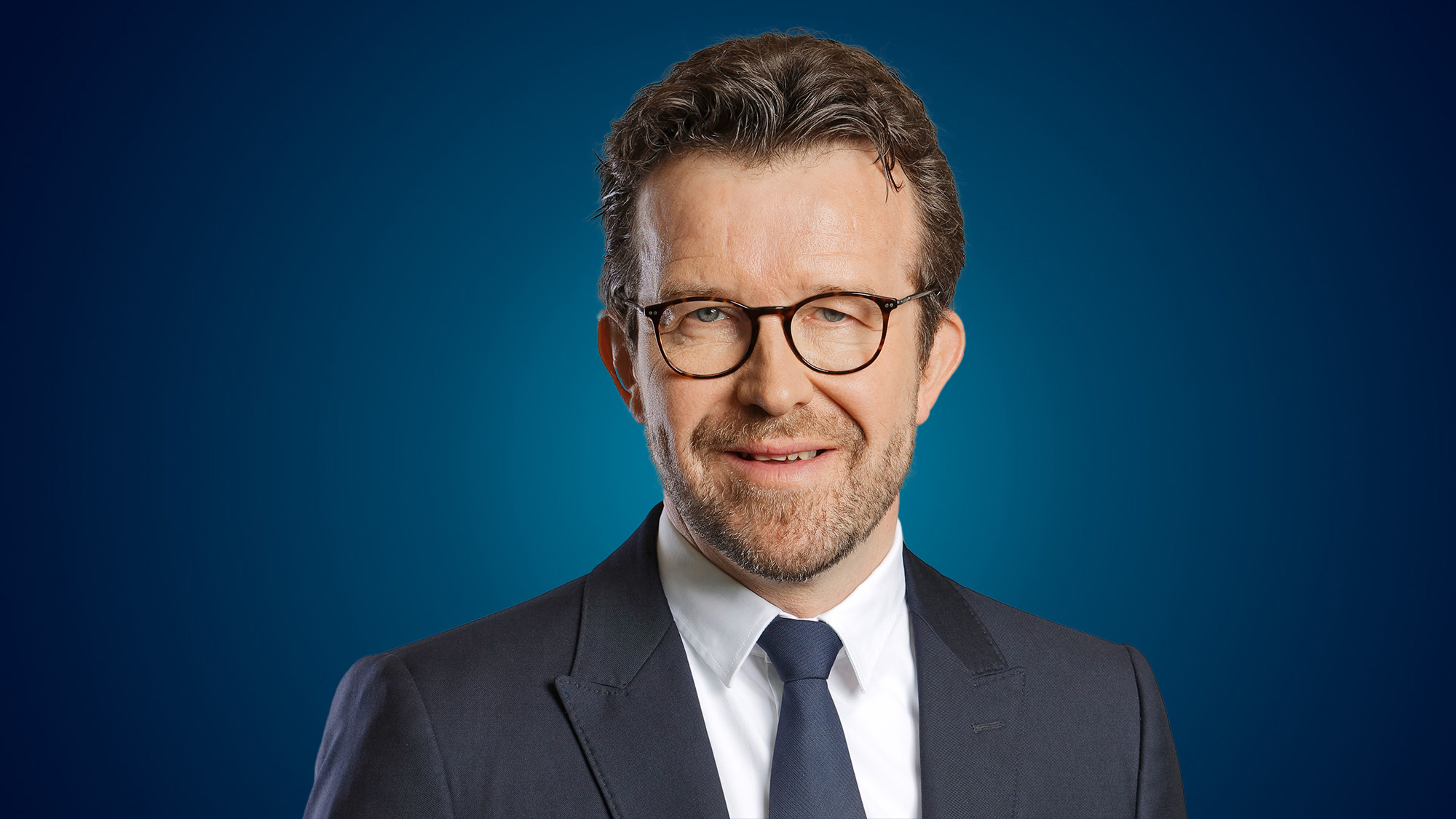