Projekt „P“:
Tabula rasa bei Audi
Audi hat seine Produktion in eine neue Organisationsform überführt. Eines der größten Umstrukturierungsprojekte der deutschen Automobilindustrie wurde in nur einem Jahr realisiert – und zahlt sich bereits aus.
09/2020
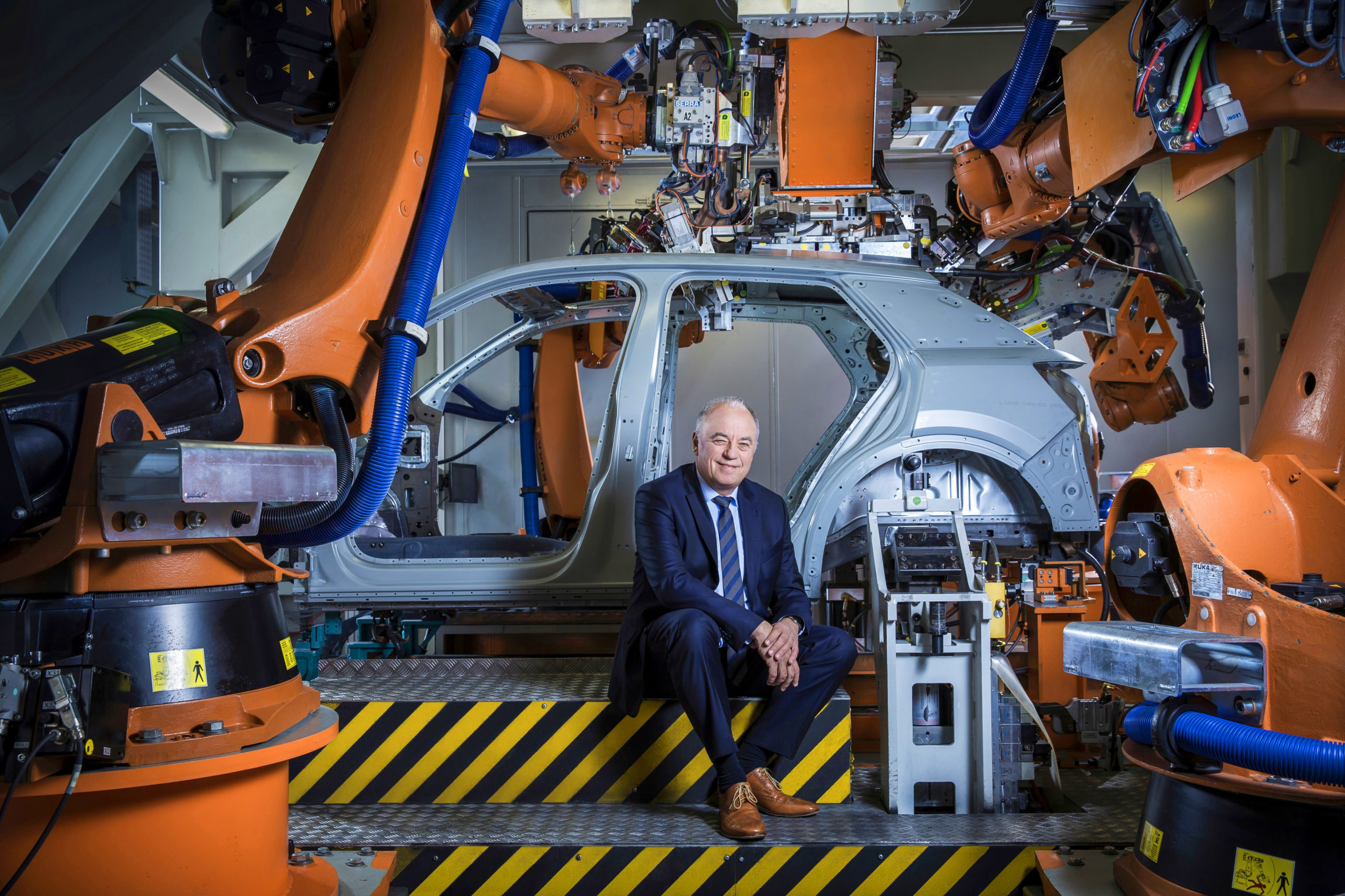
Der 2. Dezember 2019 ist für den Geschäftsbereich Produktion und Logistik bei Audi ein besonderer Tag. Er markiert den Beginn einer neuen Zeitrechnung für die Produktion. Sie ist das Herzstück eines jeden Automobilherstellers und wurde bei Audi in eine neue Organisationsform überführt. Das mag nach einer spröden Verwaltungsreform klingen. Doch das wäre so, als würde man den Wechsel vom Verbrennungsmotor zum Elektroantrieb mit einem simplen Modell-Facelift vergleichen. An jenem ersten Montag im Dezember 2019 ist „das größte Transformationsprojekt in der Geschichte von Audi“ geschafft, so Produktionsvorstand Peter Kössler. „Wir haben unsere komplette Organisation pulverisiert.“ Man könnte auch sagen: eine der größten internen Reorganisationen bewältigt, die die deutsche Automobilindustrie je erlebt hat.
Neue Matrix für neue Herausforderungen
„Kompetenzorientierte Matrixorganisation“ heißt der Schlüssel zur Zukunft von „P“, dem Produktionsressort von Audi. Mit dieser neuen Organisationsform soll der Hersteller den Herausforderungen der Branche deutlich effektiver und kosteneffizienter begegnen können, denn die Automobilindustrie muss den größten Wandel ihrer Geschichte bewältigen. Sie wird von innovativen technologischen Trends und einer grundsätzlichen Neuorientierung der mobilen Gesellschaft in ihren Grundfesten erschüttert. Digitalisierung, autonomes Fahren, alternative Antriebe, intelligente Assistenzsysteme, Big Data – wer heute ein Auto konzipiert, benötigt mehr Know-how als die NASA-Ingenieure für den Bau der ersten Mondrakete. Das Rad der Innovationen dreht sich immer schneller, wer nicht mithält, kann schnell abgehängt werden. Innovative Geschäftsmodelle und Produkte sind gefordert. Und dafür braucht es eine Produktion, die mit der immer rasanteren Taktung neuer technologischer Entwicklungen und sich wandelnden Erwartungshaltungen der Kunden Schritt halten kann. Dafür wurde die Produktion von Audi nun in nur gut einem Jahr von der ersten Idee bis zur „Liveschaltung“ in eine sogenannte kompetenzorientierte Matrixorganisation überführt.
Das bedeutet: Ein völlig neues Zusammenarbeitsmodell. Neue Verantwortlichkeiten. Neue Kommunikationswege. Neue Schnittstellen zu anderen Unternehmensbereichen sowie der Wegfall einer kompletten Hierarchieebene. Und dafür – das ist essenziell – erfolgte eine umfängliche Konzentration von Kompetenzen. Aufgaben können effektiver gebündelt und standardisiert werden. Zeit- und kostenintensive Doppelarbeiten und nicht zuletzt ein überladener Produktionsprozess sollen künftig vermieden werden. Das große Ziel der Transformation: die Werke maximal von unnötigen Lasten befreien, damit sie sich auf ihre Kernaufgabe fokussieren können – die Fertigung von Automobilen. Als Bindeglied zwischen den Bereichen steht nun eine neue Organisationseinheit mit dem Namen „Strategic Planning“. Sie bestimmt die zentralen Leitlinien und Zielvorgaben für alle Aktivitäten rund um die Produktionswerke von Audi sowie in den Zentralbereichen von der Logistik bis zum Presswerksverbund.
Fotos von Faxgeräten
Um die Bedeutung dieser Umstrukturierung zu verstehen, muss man in die Vergangenheit schauen. Dabei reicht zunächst ein Blick in den Herbst 2018. Damals fand das erste große Treffen zwischen Produktionsvorstand Peter Kössler, allen Managern des Geschäftsbereichs und den für die anstehende Transformation beauftragten Beratern von Porsche Consulting und Audi Consulting statt. Zu diesem Auftaktmeeting zeigte Kössler einige Fotos aus seiner Anfangszeit bei Audi. Der gebürtige Ingolstädter ist bereits seit Mitte der Achtzigerjahre, als er seine ersten Tage als Trainee bei Audi erlebte, in der Welt der Vier Ringe zu Hause. Kössler also präsentierte beim Treffen Fotos von alten Wählscheibentelefonen, von großen Computern mit wenig Speicherplatz und von Faxgeräten. „Das war Audi, als ich vor mehr als 30 Jahren hier anfing“, erklärte der Manager. Die Geräte wurden seitdem durch immer modernere Technik ausgetauscht. Doch die Organisationsstruktur, das Rückgrat für eine erfolgreiche Automobilproduktion, die wurde in 30 Jahren kaum verändert.
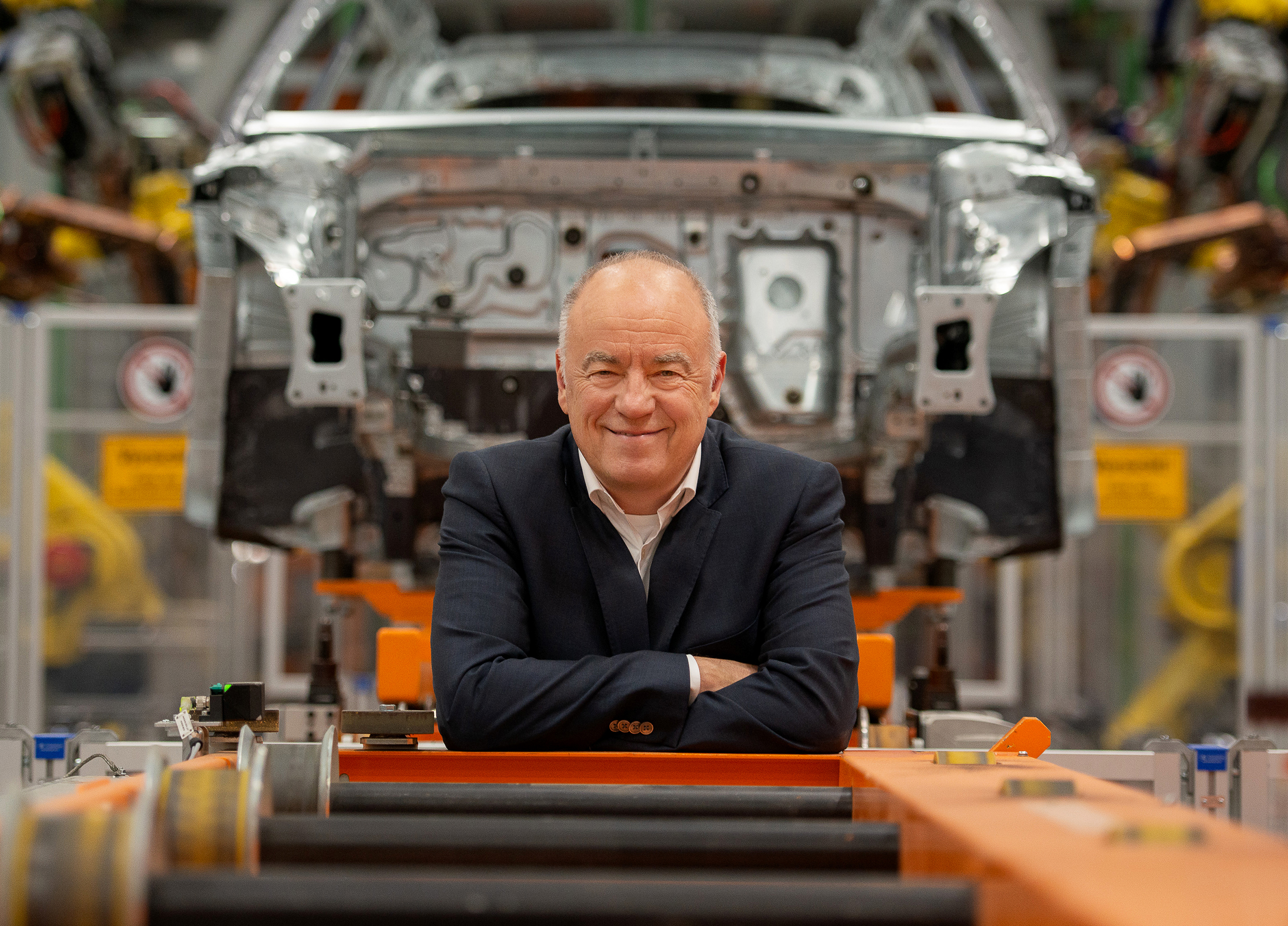
„Die Produktion von Audi orientierte sich jahrzehntelang an Funktionen“, erklärt Boris Kainz, Associate Partner bei Porsche Consulting, der das Reorganisationsprojekt bei Audi begleitete. Das war kein Problem, als es mit Ingolstadt und Neckarsulm nur zwei Standorte gab. Da hat man sich auf dem kurzen Dienstweg abgestimmt. In der heutigen globalisierten Welt mit fünf Werken, dazu Joint-Venture-Kooperationen in China, kürzeren Produktzyklen und einer steigenden Produkt- und Variantenvielfalt, war das Prinzip nicht zukunftsfähig. Die Audi-Produktion glich einem föderalen System, in dem jedes Werk und jeder Zentralbereich eine eigene Einheit verkörperte, mit eigenen Zielen, Standards, Problemen und Lösungsansätzen. „Eine zentrale Koordination und Steuerung, die vor allem das Optimum der Gesamtmarke im Fokus hatte, war zäh, zeitintensiv und manchmal schlicht unmöglich“, so Kainz. Die Botschaft hinter der Fotos-von-früher-Schau von Vorstand Kössler also war klar: Es musste sich etwas verändern. Und „etwas“ bedeutete: eigentlich alles.
„Think Big – klein wird’s von allein“
Was dann innerhalb von nur etwas mehr als einem Jahr geschaffen wurde, ist beeindruckend. Audi hatte ein Change-Team, bestehend aus Managern aller Bereiche mit den „Heavy-Project-Managern“ Dr. Siegfried Schmidtner und Michael Breme, ins Leben gerufen, bei Porsche Consulting war es ähnlich. „P“-Chef Peter Kössler gab die Maxime aus: „Think Big – klein wird’s von allein.“ Das wiederum bedeutete: Ohne Verbote und losgelöst von den eigenen Bereichen denken. Ob und wie eine Idee umsetzbar sein würde, das sollte erst später entschieden werden. Dazu wurde ein eigenes, transparentes Kommunikationskonzept aufgesetzt, um alle immer auf demselben Informationsstand zu halten. Alle Beteiligten, von den Mitarbeitern über den Betriebsrat bis zum Management und Vorstand, sollten jederzeit gut informiert sein. Über hundert Manager von Audi wurden direkt in die Transformation eingebunden, insgesamt würden mehr als 50.000 Mitarbeiter in der Produktion von der Umstrukturierung betroffen sein.
Eine weitere Maxime des Wandels: Struktur folgt Prozess. Mehr als tausend einzelne Prozesse wurden identifiziert und jeder wanderte auf den Prüfstand: Gibt es Überschneidungen? Können mehrere dezentral verankerte Prozesse an einer zentralen Stelle zusammengelegt werden? Eine Schlüsselszene im großen, einjährigen Transformationsprojekt beschreibt, wie es dabei zuging: Mitte März 2019, also nach rund vier Monaten, organisierten die Berater von Porsche Consulting einen Workshop in einem Tagungsort außerhalb von Ingolstadt. Der Blick auf Wiesen und Wälder in einem Seminarraum im ersten Stock war bald schon versperrt. 1.100 weiße Papierstreifen, jeder mit einem konkreten Prozess aus der Produktion von Audi beschriftet, wurden auf die Wände, Fenster und sogar den Fußboden geklebt. Dann begann das Ringen. Jeder Arbeitsschritt, jeder Teilprozess, jeder „Schnipsel“ wurde hinterfragt. 25 Mitglieder des Change-Teams von Audi liefen mit „büschelweise Papierstreifen“ in den Händen durch den Raum, erzählt Boris Kainz. „Da wurde abgerissen, zerknüllt, zusammengefasst, neu geklebt und sortiert. Alle haben mitgemacht und die Ärmel hochgekrempelt. Wir haben das ganz bewusst mit Papier, Stift und Klebeband gemacht. Das ist eine ganz andere, ganz physische Erfahrung.“ Und das Ergebnis konnte sich sehen lassen: Die Zahl der Hauptprozesse wurde um die Hälfte, die der Teilprozesse um ein Drittel reduziert.
Klare Verantwortlichkeiten – Experten für jede Herausforderung
Wie sehr die Entschlackung der Audi-Produktion guttut, ist heute am Beispiel Logistik zu sehen. Früher gab es in jedem der fünf Werke einen Logistikmanager, der vor allem das Wohl und Wehe der eigenen Produktionsstätte vor Augen hatte und einzig seinem Werkleiter berichtete. Das bedeutete, dass etwa bei Lieferengpässen in der Supply Chain das stärkste Werk beziehungsweise der am besten vernetzte Logistikleiter die Nase vorn hatte. Andere Werke, die vielleicht auf die gleichen verspäteten Fensterheber warteten, hatten mitunter das Nachsehen. Heute ist es anders. Die einzelnen Logistikleiter der fünf Werke berichten dem Zentralbereich Logistik. Von dort wird die Verteilung, etwa der Fensterheber, gemeinsam mit den Standorten so gesteuert, dass im Sinne der Gesamtmarke eine optimale Lösung erreicht wird.
Auch für den Produktionsanlauf eines neuen Modells ist kein Werk mehr allein verantwortlich. Im Gegensatz zu früher: So musste der Standort Brüssel im Jahr 2017, an dem bis dato nur ein Modell – der A1 – produziert worden war, den Anlauf des neuen, technisch besonders anspruchsvollen und ersten Elektromodells der Marke Audi – des e-tron – stemmen. „Das war eine Riesenherausforderung für einen Standort, der bis dahin nur alle sieben Jahre einen Modellwechsel hatte“, sagt Vorstand Peter Kössler. Damals sei deutlich geworden, dass man ein solches Werk mit der Aufgabe nicht allein lassen dürfe. „Das Werk musste über sich hinauswachsen und viel improvisieren.“ Mit der neuen kompetenzorientierten Matrixorganisation sei kein Standort mehr auf sich allein gestellt. Ein Anlauf-Team, bestehend aus den relevanten Zentralbereichen, in dem Experten für exakt diese Aufgabenstellung arbeiten, würde den Produktionsanlauf koordinieren und für Audi – wie für das Werk – zum Erfolg führen.
Erste große Belastungsprobe: Corona
Die erste Belastungsprobe für die neue Organisation kam schnell und heftig. Dabei hatten alle Verantwortlichen auch noch großes Glück im Unglück: Die Auswirkungen der Corona-Pandemie schlugen erst zu, als die neue Produktionsorganisation eingespielt war und auf Hochtouren lief. Peter Kössler sagt dazu: „Im Lichte der derzeitigen Situation und der vergangenen Monate mit Lieferengpässen, Kurzarbeit und stillstehenden Produktionsbändern muss ich ganz klar sagen: Ohne die neue Organisation hätten wir besonders die schwierigen Wochen in diesem Frühjahr nie in der Form bewältigen können. Wir haben alle Werke, insbesondere bei der Logistik, aus einer Hand gesteuert und sind den täglich neuen Herausforderungen mit einer schlüssigen Strategie begegnet.“
Und so hat sich das Neue bei „P“ ganz schnell etabliert. Das Ungewöhnlichste an dem riesigen Wandel aber ist dies: Wer im Herbst 2018 zum letzten Mal ein Werk von Audi betreten hat und das nun wieder tut, wird keinen Unterschied merken. Die größte Transformation in der Geschichte von Audi hat auf dem Shopfloor kaum sichtbare Spuren hinterlassen – und doch ist jetzt alles anders.
„Die Organisation hat sich in vielen Bereichen neu gefunden“
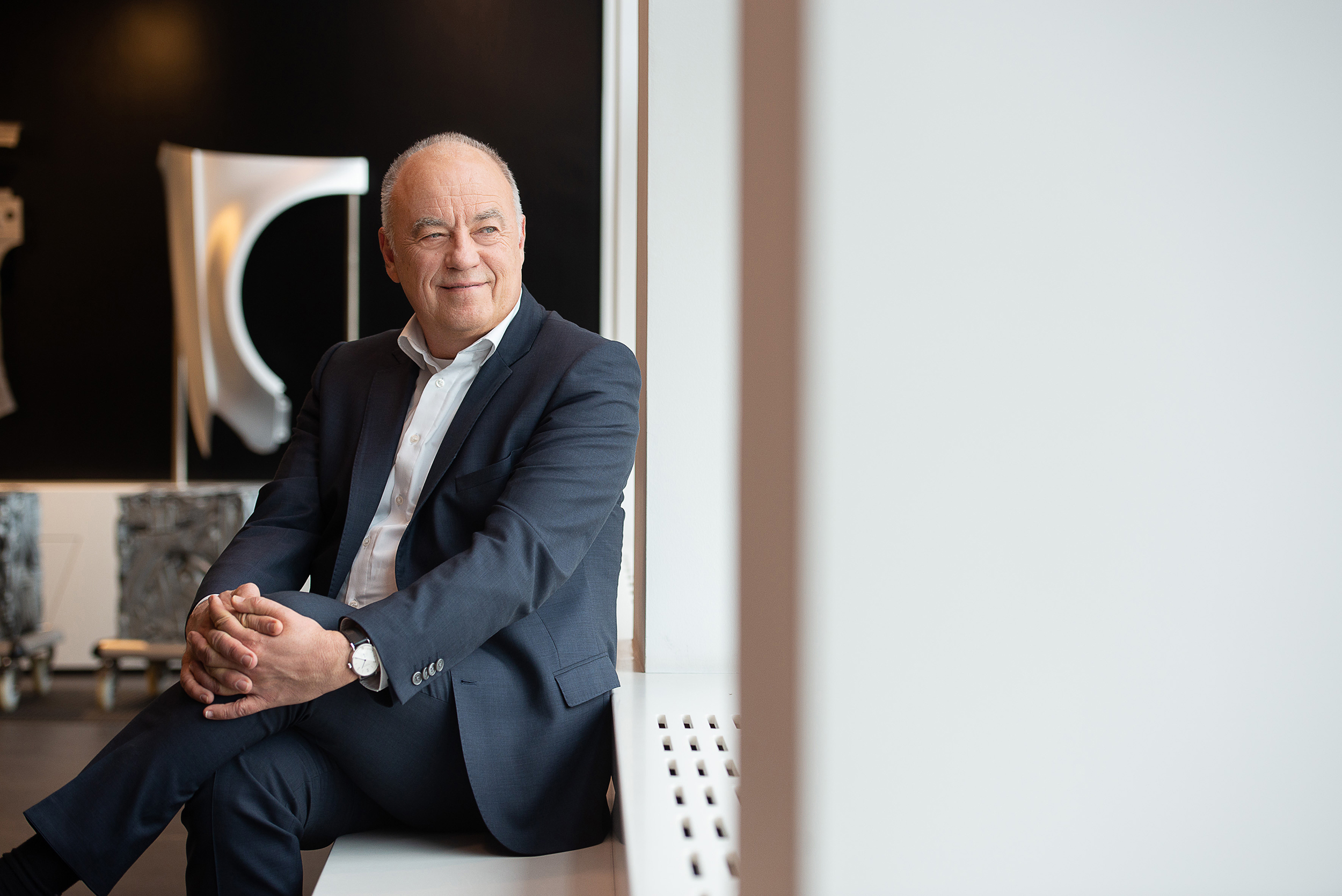