Anders kann besser sein
Bei der Goldbeck GmbH gibt es alles aus einer Hand: Das Bau- und Dienstleistungsunternehmen aus Bielefeld plant, errichtet und betreut Gewerbeimmobilien wie Hallen, Büros und Parkhäuser. Es fertigt die notwendigen Teile dafür in eigener Produktion. Mit dem Mut zur Individualität und zum Systembau etablierte sich das Familienunternehmen als einer der erfolgreichsten Mittelständler Deutschlands.
07/2021
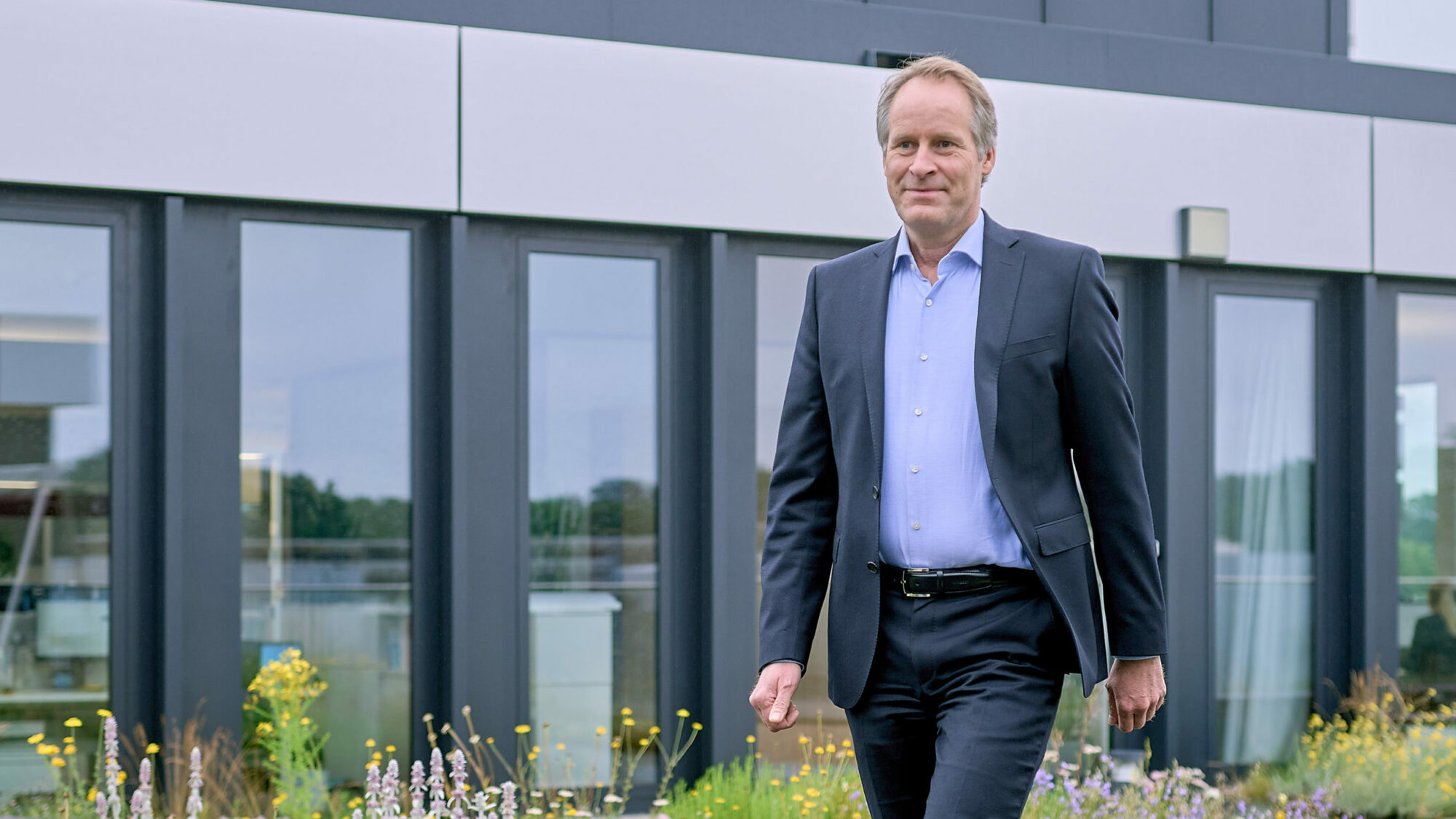
„Wir haben schon immer Dinge anders gemacht als andere“, sagt Jörg-Uwe Goldbeck (53), geschäftsführender Gesellschafter des Bau- und Dienstleistungsunternehmens Goldbeck in Bielefeld. Seit 2007 steht er zusammen mit seinem Bruder Jan-Hendrik (44) an der Spitze des Traditionshauses. Gegründet wurde es 1969 von ihrem Vater Ortwin Goldbeck, heute 83 Jahre alt. Mittlerweile beschäftigt die Firmengruppe mehr als 8.000 Mitarbeitende. Es ist das größte familiengeführte Bauunternehmen Deutschlands. Der Aufstieg des Traditionshauses zu einem der erfolgreichsten Mittelständler der Republik basiert auf unternehmerischem Mut und Innovationen.
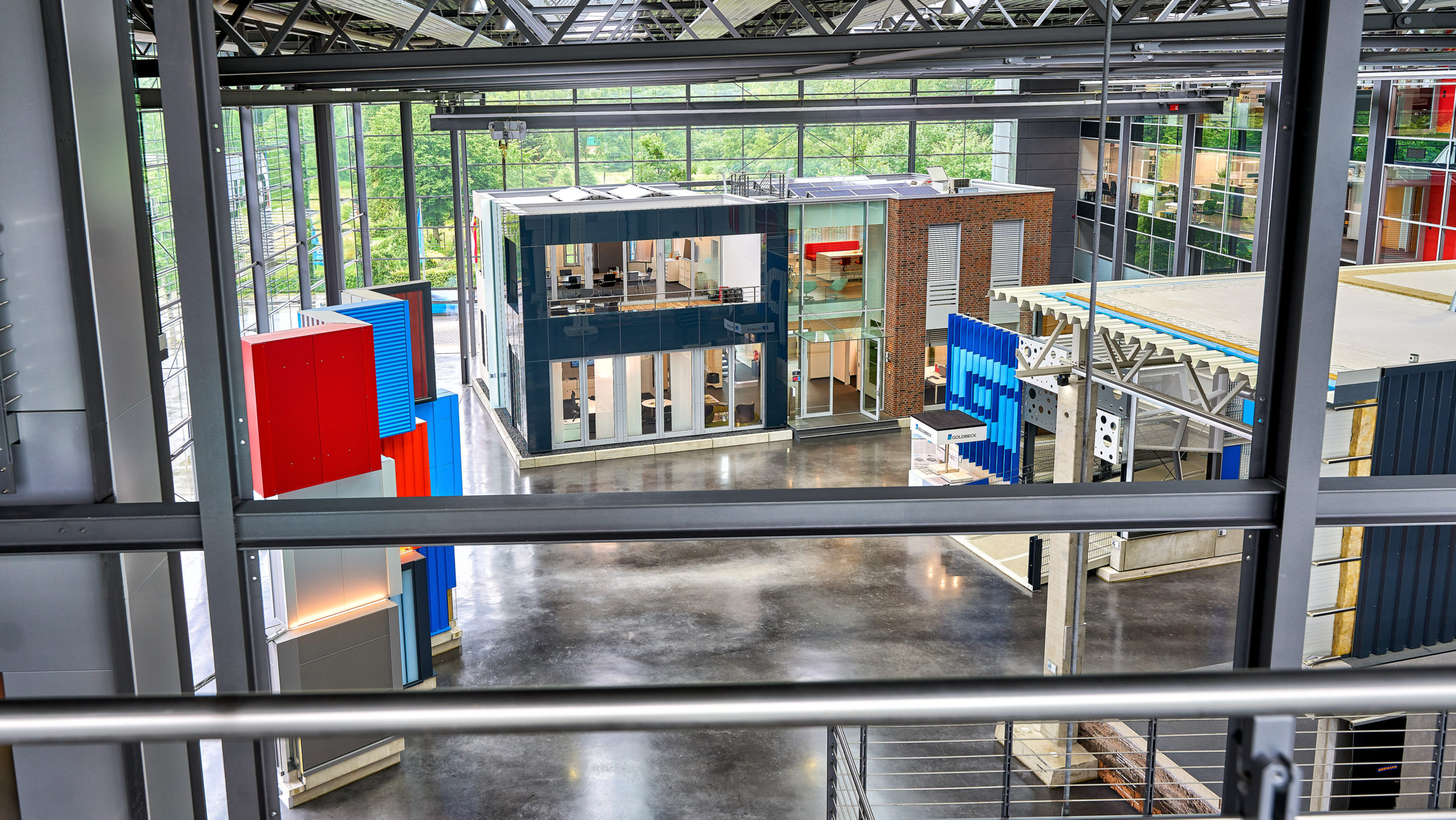
Wir bauen nichts, was wir nicht geplant haben, und wir planen nichts, was wir nicht selbst bauen.
Die Positionierung der inhabergeführten Baufirma klingt nüchtern: Generalunternehmer im gewerblichen und kommunalen Hochbau. Darüber hinaus gebäudenahe Serviceleistungen. Der Clou ist die Arbeitsweise, denn Goldbeck stellt schlüsselfertige Hallen, Büros und Parkhäuser in Systembauweise her. Gebäude begreifen die Ostwestfalen als Produkt. Sie entwickeln und fertigen wesentliche Teile selbst, errichten die Bauwerke und übernehmen auf Wunsch auch Betreuung und Betrieb. Der Kunde bekommt alles aus einer Hand. Jörg-Uwe Goldbeck: „Wir bauen nichts, was wir nicht geplant haben, und wir planen nichts, was wir nicht selbst bauen.“
Besser, schneller, günstiger
Der Systemgedanke des Industrieunternehmens im Bausektor geht auf die Automobilindustrie zurück. Diese gilt als Vorreiter der Produktion verschiedener Modelle auf einer Plattform. „Zu Beginn wurden wir für unseren Weg von vielen Wettbewerbern belächelt“, erinnert sich Jörg-Uwe Goldbeck. Das änderte sich schnell, denn der Erfolg gab der mutigen Familie recht. „Systematik hat unsere Arbeit besser, schneller und günstiger gemacht“, resümiert der Firmenchef. 80 bis 90 Prozent der auf einer Goldbeck-Baustelle verwendeten Teile werden in eigenen Werken vorproduziert – selbst sieben Tonnen schwere Decken und 18 Meter hohe Betonsäulen. Goldbeck hat insgesamt zehn eigene Werke. Darunter Betonfabriken, in denen Wände und Decken hergestellt werden, sowie Aluminium- und Stahlbauwerke, aus denen Tragwerke, Fenster und Türen kommen. Europaweit ist das Unternehmen an über 70 Standorten mit Dependancen vertreten.
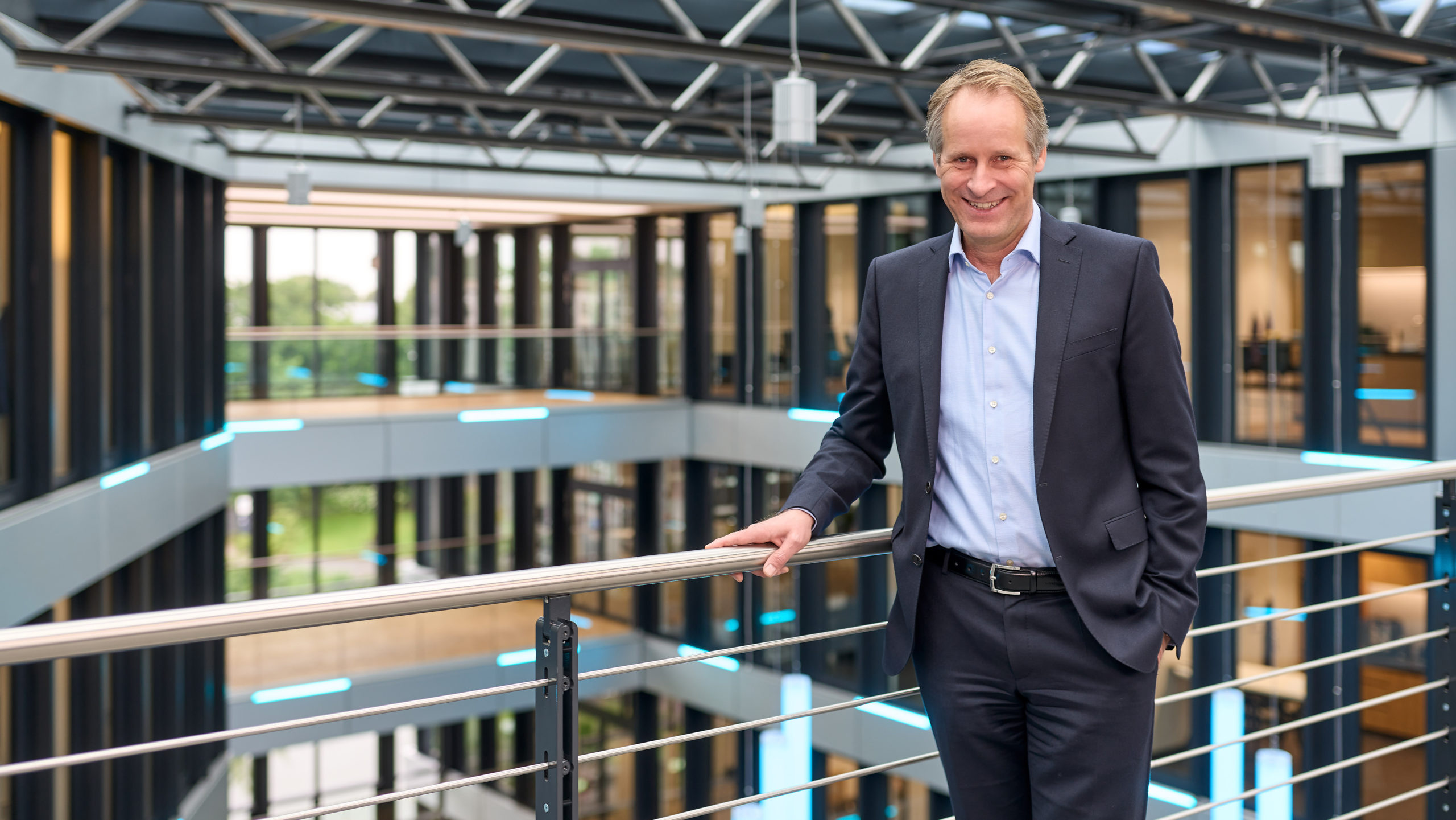
Trotz der modularen Bauweise ist jedes Gebäude individuell, hat andere Geschosshöhen, eine andere Fassade. Von den rund 500 Projekten, die Goldbeck pro Jahr stemmt, sind etwa 50 Prozent Logistikhallen, die übrige Hälfte entfällt auf Büros, Parkhäuser und andere Gebäude. In diesem Segment ist das Bauunternehmen unumstrittener Marktführer: Jedes zweite Parkhaus in Deutschland ist „developed and made by Goldbeck“. Ein besonderer Coup war der Großauftrag für den Bau der „Gigafactory“ von Tesla in Grünheide bei Berlin. Den erhielt Goldbeck im Juni 2020, elf Monate später, im Mai 2021, konnte das Werk an den Elektroautohersteller aus Kalifornien übergeben werden – termingerecht und zu den vereinbarten Kosten. Ein Leuchtturmprojekt. „Möglich war das nur durch die industrielle Vorfertigung der Bauelemente in unseren Werken“, erläutert Goldbeck.
Was Bauleute im Silicon Valley lernen
Ein weiteres Erfolgsrezept des Unternehmens: Innovationen. Dafür schauen die Firmeninhaber über den Tellerrand hinaus. Was machen Betriebe in anderen Branchen besser? Was kann neu dazugelernt und für das eigene Geschäft adaptiert werden? Ein Beispiel: Ein kleines Forschungs- und Entwicklungsteam kundschaftet seit zwei Jahren im kalifornischen Silicon Valley Kooperationsmöglichkeiten mit Start-ups aus, die Digitalisierung und Bauen verbinden. Das Unternehmen pflegt zudem einen engen Kontakt mit der Stanford University, an der es einen Lehrstuhl mit dem Forschungsschwerpunkt digitalisiertes Bauen gibt. „Unsere Vision ist, auf intelligente Weise mit neuen Technologien zu bauen“, sagt Jörg-Uwe Goldbeck. Stichwort: Produktion der Zukunft. Schon heute spielen beispielsweise Roboter auf den Goldbeck-Baustellen eine Rolle. Sie werden aktuell testweise für Bohr- und Malerarbeiten eingesetzt, ein „hundartiger“ Roboter scannt und dokumentiert den Baufortschritt.
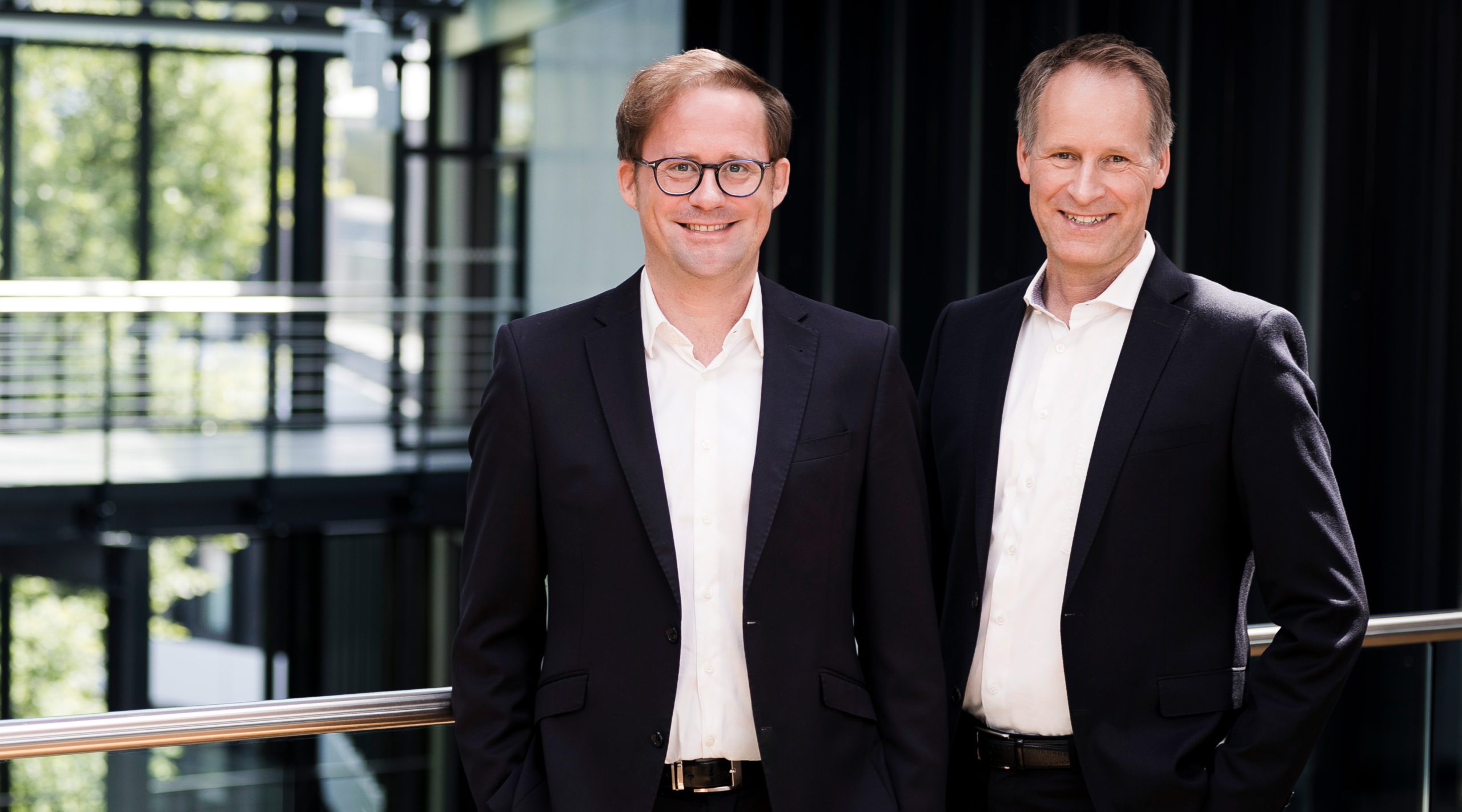
Und noch etwas zeichnet das erfolgreiche Bauunternehmen aus: Das Duo an der Spitze funktioniert. Jan-Hendrik Goldbeck ist vornehmlich für Technologie, Digitalisierung und die Internationalisierung des Unternehmens zuständig, Jörg-Uwe Goldbeck kümmert sich unter anderem um Finanzen, Personal und Produktion. „Wir ergänzen uns sehr gut“, konstatiert er. Wichtig ist den Brüdern, im Team mit klugen und engagierten Mitstreitern zu arbeiten. „Die unterschiedlichen Fähigkeiten und Kompetenzen unserer Mitarbeitenden im Unternehmen optimal zu nutzen, ist uns extrem wichtig”, betont Jörg-Uwe Goldbeck. Sie sollen Problemlöser, Erfinder, Wegweiser und Ausbilder sein, engagiert und zuverlässig. Denn auch heute noch gilt die Maxime des Unternehmensgründers Ortwin Goldbeck: „Wir schreiben Strategien mit Bleistift und Werte mit Füller.“ Auf diese Werte wird auch beim Recruiting geschaut. Goldbeck: „Wir achten darauf, eine große Bandbreite an Talenten zu haben und Menschen, die sich für das Unternehmen einsetzen wollen.“ Führungspersonen entwickelt das Bauunternehmen mit dem blauen Firmenlogo vorwiegend intern. Schlüsselpositionen im Produktionsbereich besetzt Goldbeck dagegen bewusst mit externen Managern – zum Beispiel aus der Automobilindustrie: „Um auch künftig erfolgreich zu sein, dürfen wir nicht nur in den eigenen Reihen schauen, sondern brauchen unvoreingenommene Spitzenkräfte, die frische Ideen einbringen.“
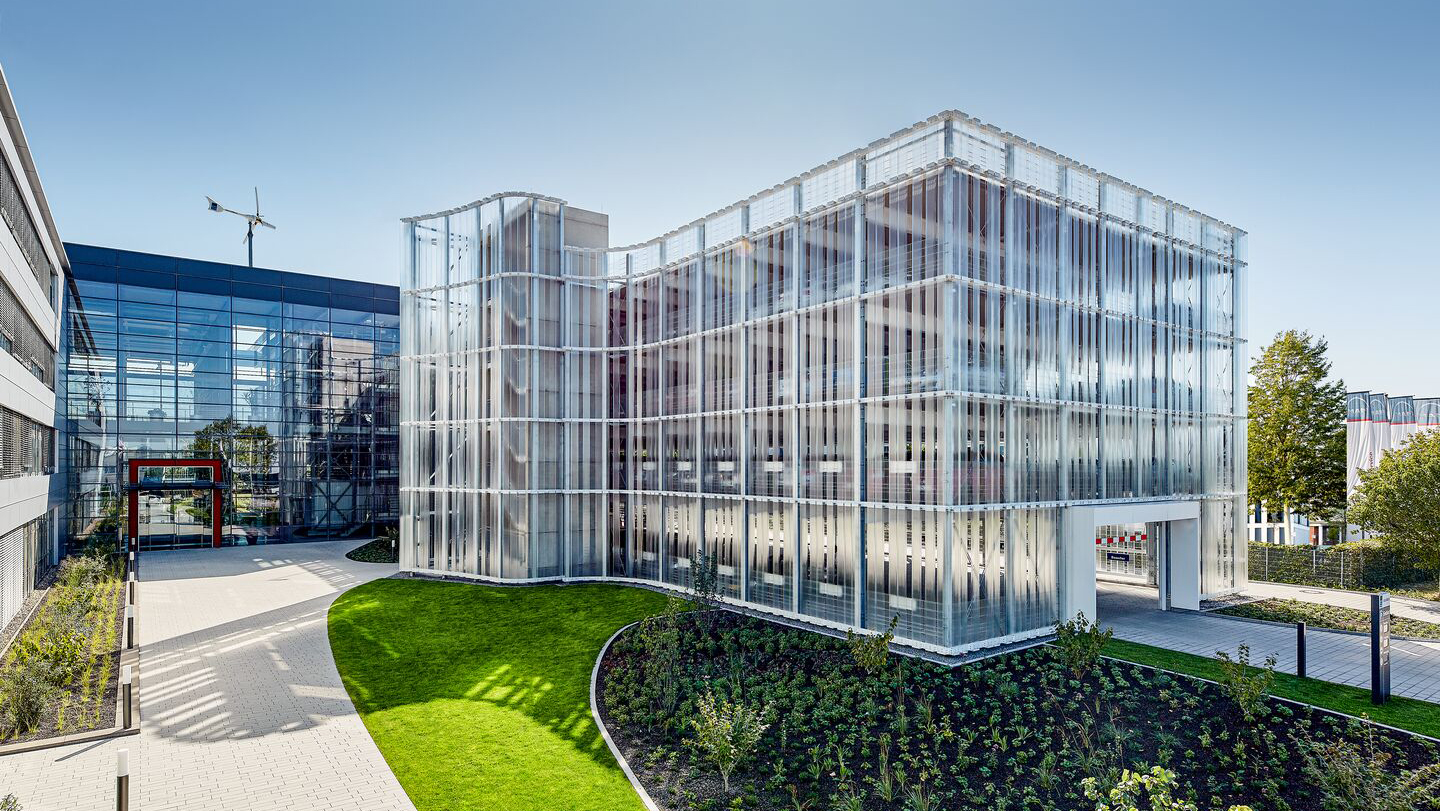
Stahl versus Carbon
Das gilt auch für das Thema Nachhaltigkeit. Das spielt bei den Bielefeldern, die 2019 von der Intes-Akademie zum „Familienunternehmen des Jahres“ gekürt wurden, seit jeher eine wichtige Rolle. Beispiel: Stahl versus Carbon. Es geht um Korrosionsfreiheit, Leistungsfähigkeit und Gewichtsreduzierung – ein Thema sowohl in der Flugzeug- und Automobilindustrie als auch im Baugewerbe. Die industriell hergestellten Fasern aus Kohlenstoff-Elementen sind gut 20 Prozent leichter und 40-fach fester als Stahl und halten extremen Belastungen stand. „Beim Einsatz von Carbon im Gebäudebau benötigen wir kleinere Fundamente und weniger Beton. Wegen seiner Korrosionsfreiheit ist Carbonbeton zudem langlebiger und wartungsarm“, betont Jörg-Uwe Goldbeck.
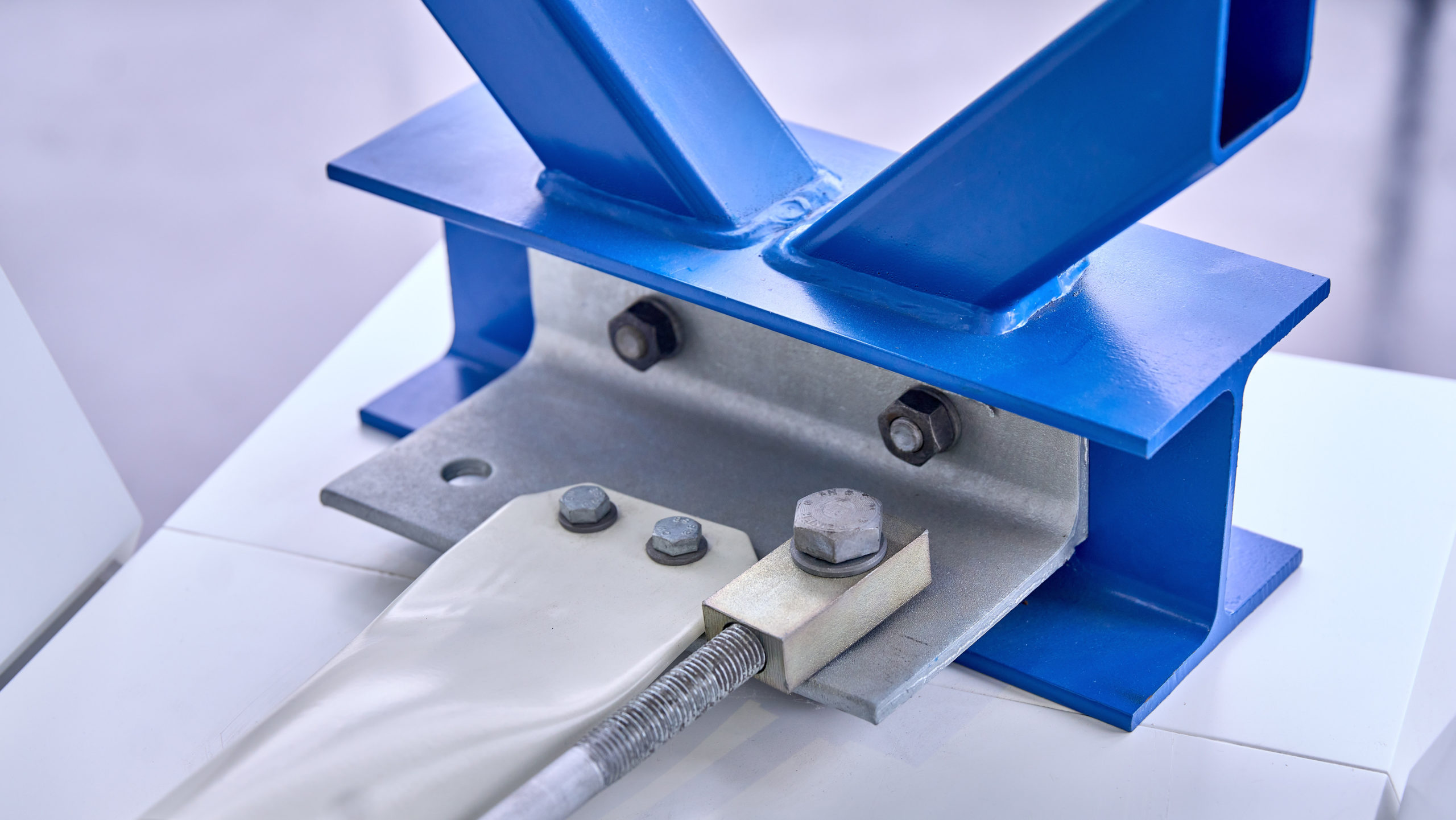
Die Haltbarkeit der Bausubstanz, Nachhaltigkeit und langfristige Flexibilität durch eine Bauweise, die den Rückbau erleichtert, werden immer wieder hinterfragt. „Wir haben vom ersten Entwurf an den gesamten ersten Lebenszyklus eines Gebäudes von durchschnittlich 30 bis 40 Jahren im Auge.“ So verwendet Goldbeck beim Bau, wo immer möglich, mechanische Verbindungen, die eine spätere Demontage und das sortenreine Recycling erleichtern. Denn aus Nachhaltigkeitsgründen und im Sinne des lebenszyklusübergreifenden Ansatzes denkt man bei Goldbeck schon vor Baubeginn auch über den Abriss eines Gebäudes nach.

Ein Zukunftsfeld für Goldbeck sind öffentliche Bauvorhaben. Bei der Realisierung von Schulen und Verwaltungsgebäuden hat sich das Unternehmen schon einen Namen gemacht. Dagegen gehört der Wohnungsbau erst seit 2017 zum Portfolio, hier gibt es erste Referenzprojekte. „Wir wollen Erfahrungen sammeln und möglichst viele Erkenntnisse aus anderen Bereichen einbringen“, betont Jörg-Uwe Goldbeck. Das Unternehmen soll wachsen – vor allem in Deutschland und den europäischen Nachbarländern. „Mit sehr guten Leistungen ist man überall willkommen.“

Produktion der Zukunft
„Es ging um die Beantwortung folgender Frage: Welche Technologien versetzen uns in die Lage, in unseren Werken künftig die Bauteile herzustellen, die notwendig sind, um unseren Vorsprung auszubauen und auch in Zukunft die Nummer eins in unserer Branche zu sein?“, sagt Dr. Härtel. Die Rolle, die Porsche Consulting zukam: Sparringspartner und Technologie-Scout. Zunächst wurden 27 Technologiesuchfelder definiert – von der Anlieferung über die Produktion bis zur Intralogistik und Auslieferung –, die für eine Produktion der Zukunft relevant sind. Dann wurden rund 200 Technologien unter die Lupe genommen. Dr. Manuel Schönwitz, Projektleiter bei Porsche Consulting: „Dafür haben wir in diversen Datenbanken intensiv recherchiert und so manch Neues aufgespürt.“ Ausgewählt wurden schließlich 33 Technologien, die kurzfristig genutzt werden sollen. Sie liegen im Werkzeugkasten der Bielefelder, wenn es darum geht, bestehende Fabriken modular zu erneuern oder neue Werke zu bauen. Diese Technologien haben einen hohen Reifegrad und können bereits eingesetzt werden. „Die Praxistauglichkeit, Robustheit, aber auch Zukunftsfähigkeit waren bei der Auswahl das A und O“, so Dr. Härtel.
Im zweiten Teil des Projekts wurde ein Modell-Layout für die künftigen Beton- und Stahlbauwerke entworfen. „Schließlich geht es nicht nur um die Vision modular aufgebauter Fabriken, sondern auch um die Machbarkeit der Umsetzung“, sagt Dr. Wulf Härtel. Im Juni wurde das Projekt abgeschlossen. Was jetzt noch lediglich auf Papier zu sehen ist, könnte schon bald Realität sein: Goldbeck-Beton- und Stahlbauwerke, die aufgrund ihres modularen Aufbaus und innovativer Technologien flexibel auf sich ändernde Ansprüche reagieren können.