The MedTech Factory of the Future
Siemens Healthineers is setting new standards in medical technology at a cutting-edge plant where a digital twin provides very high transparency for the greatest efficiency.
09/2024
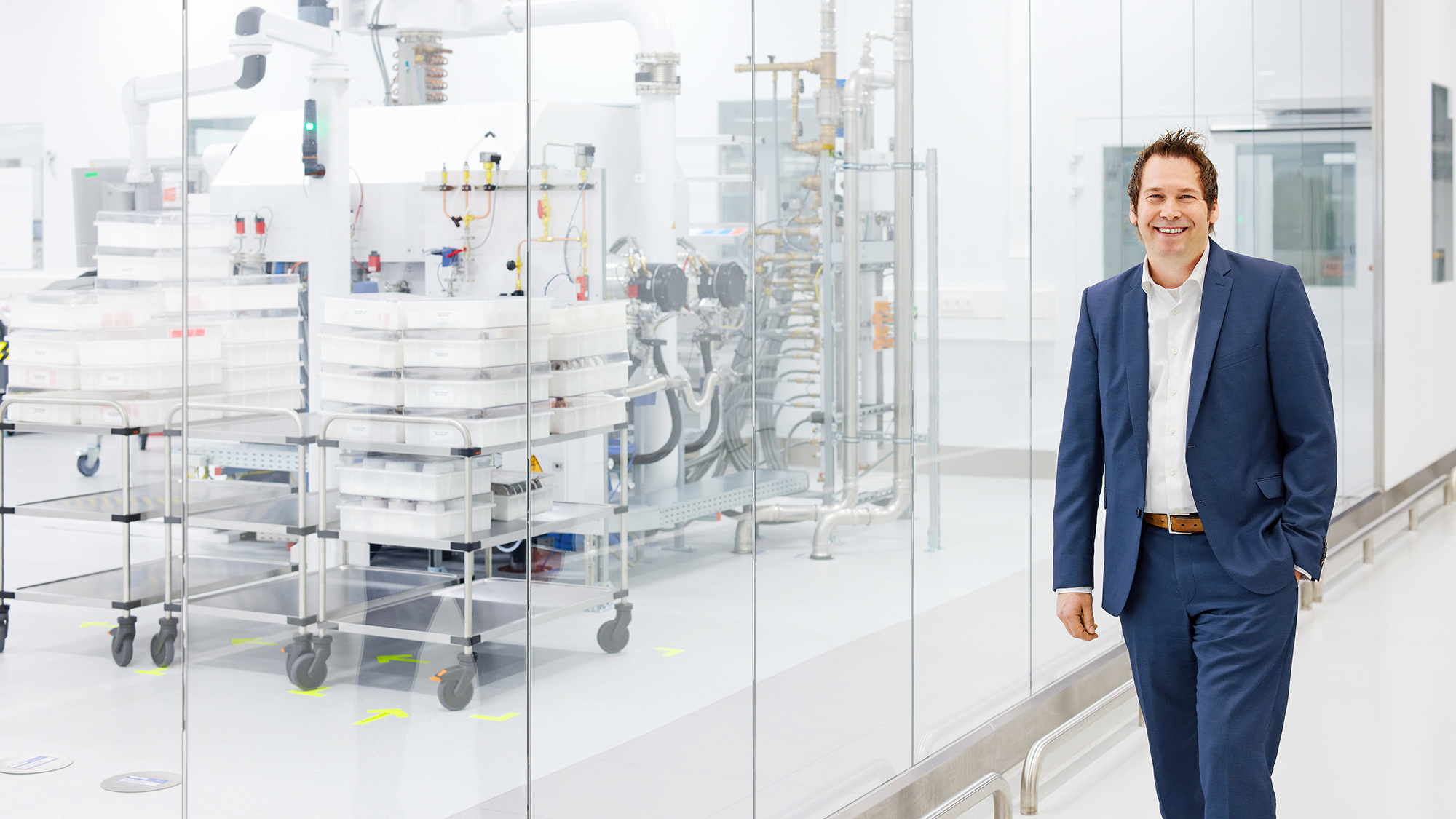
Any one of us could find ourselves in this situation at the emergency room (ER) of a major hospital: an ambulance arrives and the paramedics bring a patient through the doors on a yellow-wheeled stretcher. A woman in her mid-40s, she had abruptly lost sensation in her right arm and leg. A doctor quickly appears and speaks with the patient under the bright lights of the ER. Her initial diagnosis: “Reduced blood supply to the brain.” Treatment needs to begin right away.
An anesthesiologist administers a sedative and the patient loses consciousness. The doctor inserts a wire-like catheter into a blood vessel in the groin and maneuvers it up into the affected part of the brain. A large screen shows her the instrument’s position and the pattern of the blood vessels. She discovers that a thrombus, or blood clot, is blocking an artery in the brain. Using the catheter, she succeeds in suctioning it away and thereby freeing the vessel. An hour later the patient can feel her right side again. A very fortunate outcome—for she could soon have suffered a stroke with serious consequences. Thanks to the precise diagnosis and prompt appropriate treatment, she will leave the hospital in a few days in good health.
Navigation system for doctors
Scenes like this now transpire thousands of times a year at hospitals in Germany that have the right equipment. The country is not alone in this respect. “Similar measures are taken in Japan and Nepal, in South Africa and the United States—new image-supported processes have dramatically improved the prospects for stroke patients,” says Horst Schmidt, Head of Power & Vacuum at Siemens Healthineers, a leading company in medical technology.
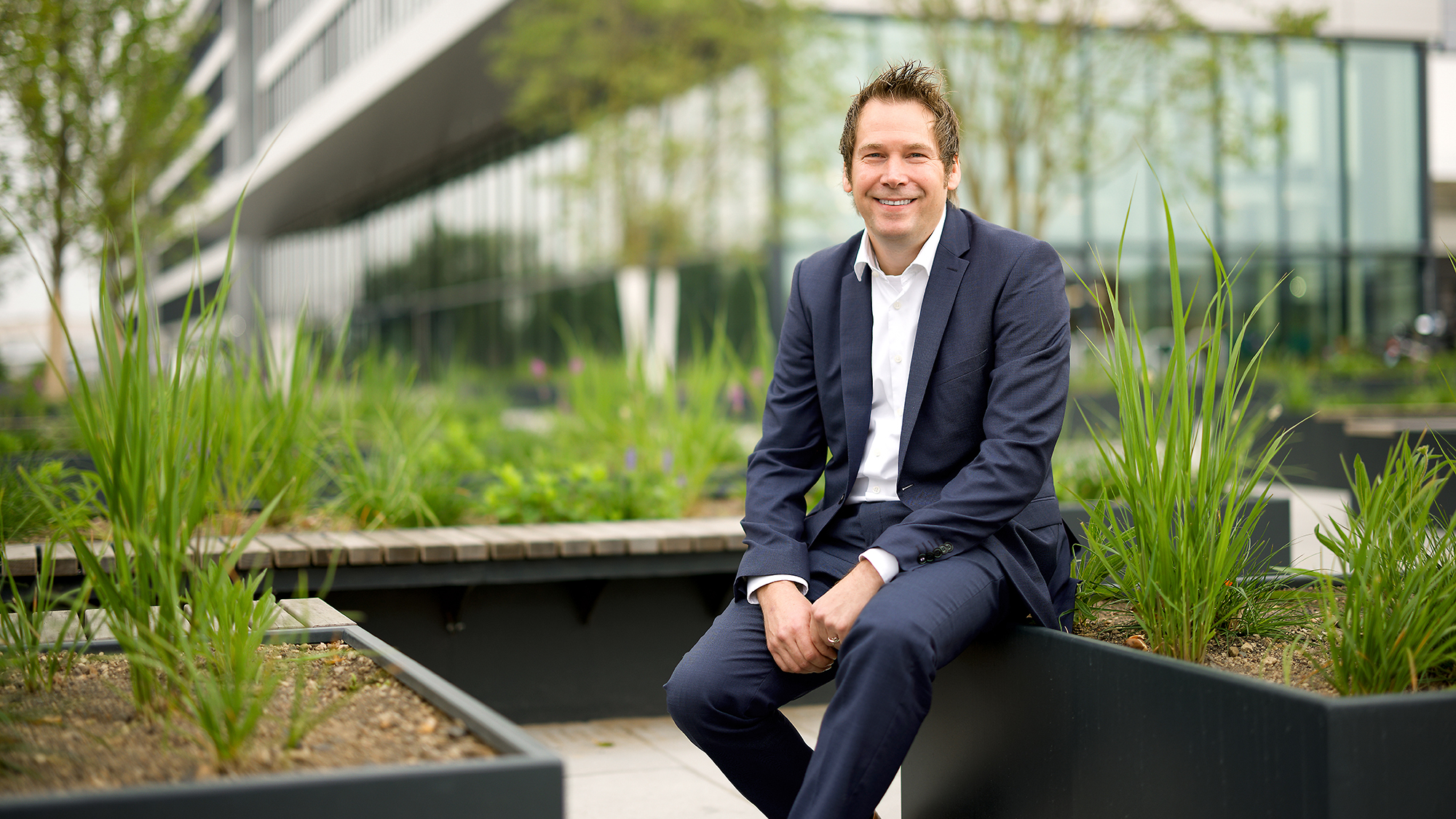
“Time is brain” is a formula also heard at neurological departments in hospitals. Endovascular stroke treatments require not only skill on the part of medical practitioners, but also the ability to see exactly where their instruments are in patients’ bodies. This can be achieved by taking multiple images in quick succession and compiling them into a type of video. Siemens Healthineers produces this imaging equipment. “Our devices are essentially navigation systems for doctors,” says Schmidt. And he and his team are responsible for manufacturing the core component of these systems.
Coffee connects
Schmidt’s office is in Siemens Healthineers’ newly erected High-Energy Photonics (HEP) Center of Siemens Healthineers in Forchheim, a southern German town near Nuremberg with a population of 34,000. Located right next to the Main-Danube Canal, this new production site replaces two older plants that had reached their capacity limits. The HEP Center will now be manufacturing the core parts for many of the Siemens Healthineers imaging systems. Companies that expect high performance from their employees need to offer good working atmospheres: attractive conditions, a positive team spirit, high motivation. This new building houses production and administrative facilities in close proximity. Each floor has a casual coffee bar, where factory and office staff can mingle. Everyday contact also fosters short paths and prompt solutions in interdisciplinary collaboration. However, that’s just one small—albeit important—reason why the HEP Center is a lighthouse project not only for the medical technology industry, but also for future production environments in general.
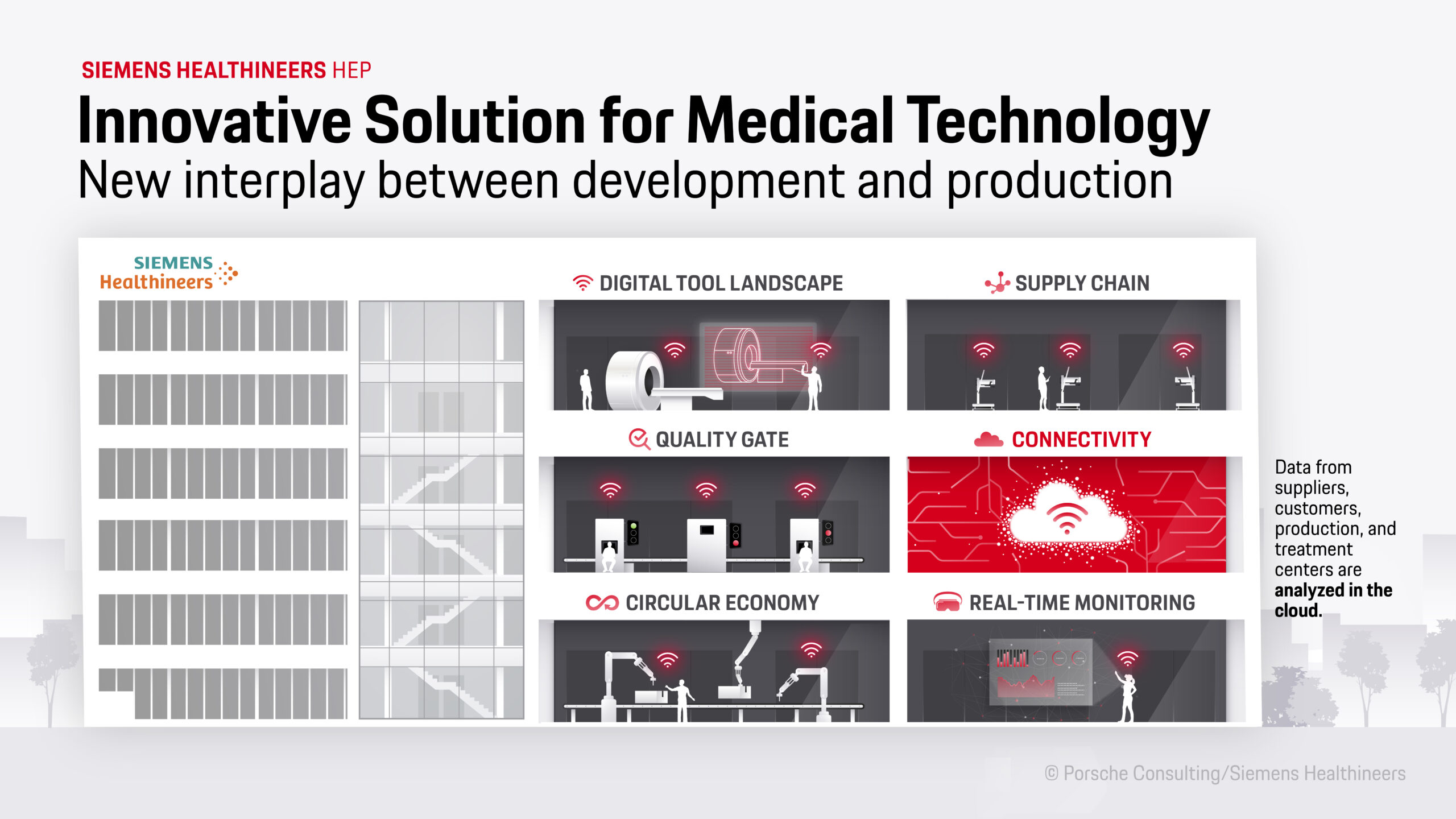
In this transparent factory everything is digitally connected, from the production facilities and equipment to the logistics processes—including the building’s digital twin. The HEP Center’s digital transformation aims to raise performance levels, minimize risks, and ensure that knowledge is transparent. Examples include:
- Digital shop floor and visualization: Tools such as digital shop-floor applications (DSA) and manufacturing execution systems (MES) are being used to visualize key performance indicators (KPIs) and improve decision-making processes.
- Digitalizing data: The HEP Center concentrates on transforming, generating, processing, and connecting digital data to add more value to production and business processes.
- Automation: New hardware is automating at least one manual step in each process.
New production facilities naturally need to focus on efficiency, automation, and digitalization these days. The entire HEP Center is digitalized and connected, and every part of it is digitally mapped. Yet no jobs have been cut. “The Center was built to promote growth by raising output,” explains Schmidt. He mentions two more key aims: quality and precision. The X-ray tube assemblies made at the HEP Center are installed in X-ray, mammography, CT, and interventional radiography systems of Siemens Healthineers enabling catheter and other applications for neurological and cardiovascular care. “It’s a high-end field,” he notes. “Our customers are doctors from around the world who want the best possible care for their patients, and are also increasingly interested in mobile units. They’re constantly seeking even better quality and higher resolutions to be even quicker and more accurate in their diagnoses and actions.”
Robots take the night shift
A key part of this trajectory consists of automating and digitalizing production. In 2019, Siemens Healthineers worked with a team from the Porsche Consulting management consultancy to develop its vision of a smart factory. “Back at the beginning we were looking down quite a long road,” says Dr. Jens Fürst, Principal Key Expert Digitalization & Automation. “But we’ve covered it amazingly fast.” The new complex, with an investment of around 350 million euros, was completed in less than five years—a remarkable period of time for a project of that complexity consisting of three broad production floors and six narrower adjacent office floors for a total surface area equivalent to eight soccer fields.
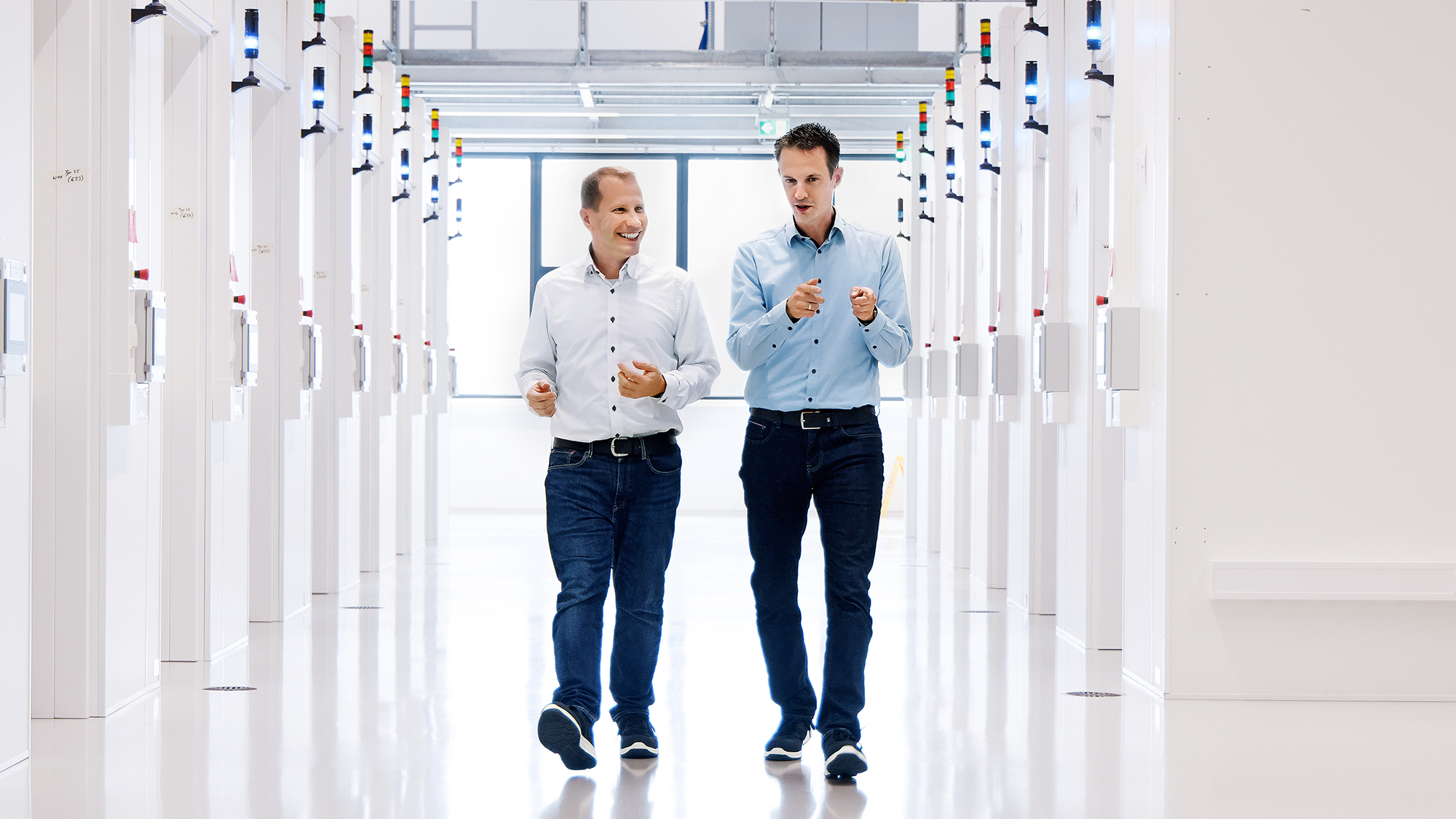
Dr. Fürst likes to take guests onto the interior ‘balcony’, a narrow gallery on the third floor of the production hall with an impressive panoramic view of the assembly lines. The birds-eye perspective affords a good overview of the production steps for the X-ray tubes as well as the generators. Put very simply, the X-ray tubes are first made in a clinical clean room. At night they undergo high-voltage ‘conditioning’ to achieve even higher levels of cleanliness by automated robots. When employees arrive for the early shift the next day, they test the tubes’ functionality and precision manually in insulated cabins. Only then are the tubes released for installation in their end devices at other plants.
Jointly developed digitalization strategy
Dr. Fürst works closely together with Dr. Markus Kaupper. “Five years ago, I was excited about the technical and digitalization prospects, but couldn’t really judge what would be possible from today’s perspective,” says the latter in recalling the initial stages of the new plant. Today, Dr. Kaupper is the HEP Center’s Head of Digitalization.
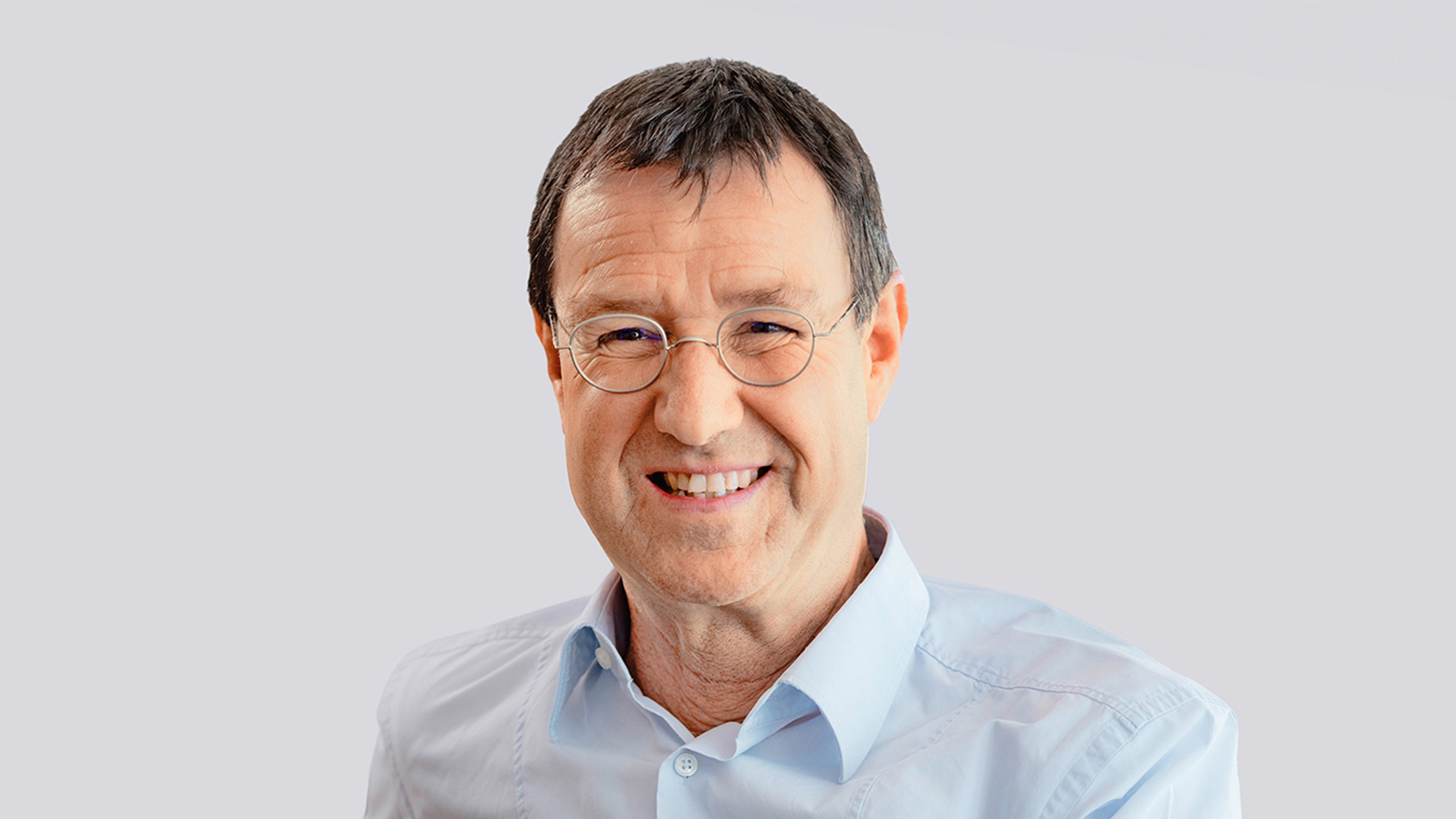
Nearly every part of the factory along with every process and every component that goes through it is digitally mapped. The dimensions, physical properties, and performance data are all known, forming a digital twin of the factory. “The HEP Center is our first completely digitalized factory and a crucial part of our smart factory network,” says Dr. Peter Schardt, Chief Technology Officer at Siemens Healthineers. “A reliable and connected production environment is of crucial importance in the medical sector,” he adds.
Service ‘senses’ when it’s needed
If a product doesn’t pass its final quality control with flying colors, the experts start by searching for possible causes in the digital twin. They might ascertain, for example, that the gripper surfaces at a certain spot are not an ideal match for the product, which can lead to inaccuracies. They also test new production lines virtually to eliminate any problems before they go into operation. “They’ll usually then run quite smoothly when we put them into actual practice,” says Dr. Kaupper. This represents an enormous boost in efficiency, especially for small production lines like most of those at the Center.
Because the digital twin is constantly fed with real data that are supported by artificial intelligence, Siemens Healthineers is also in a position to make increasingly precise predictions. Component wear is one example. As part of the Siemens Healthineers TubeGuard program, some physicians allow the company access to their systems’ sensors while in operation. The data can be used to predict when the X-ray tube will fail with a high level of accuracy. “A service technician is already there with a replacement before the customer notifies us,” says Schmidt. This represents yet another boost in efficiency, not only for Siemens Healthineers but also for the hospitals and healthcare personnel who can then plan exactly for the comparatively brief downtimes needed for service.
Desire for own programs
Work at the HEP Center has also brought fundamental changes for the staff. “You can’t impose these levels of automation and digitalization overnight,” says Verena Gollisch, Transformation Manager at the Center. “A lot of the previous tasks are no longer needed, and many people had to adopt a new approach to their work. Some view it as an opportunity, others can be daunted by it. We’ve always found it important to get our personnel on board early on, have them help shape the changes, get their feedback, and make the Center’s new opportunities evident to everyone.”
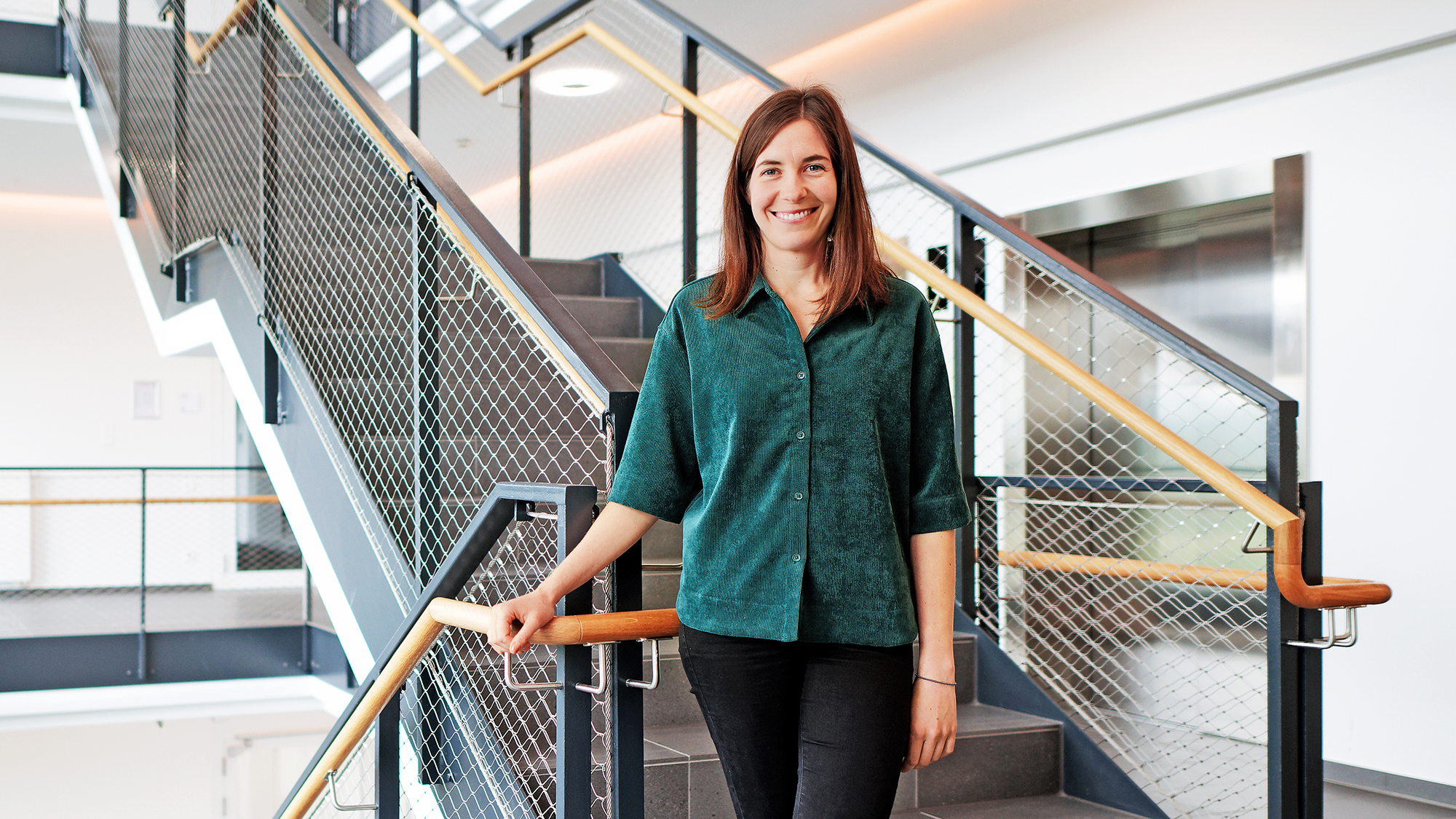
Countless events encouraged employees to help get the HEP Center up and running. These included hackathons where the employees could write programs to improve processes, and protected spaces where they could try out new activities. The factory is now nearly completely up and running, and Dr. Kaupper emphasizes that the employees have handled the adjustment well. “We’ve discovered many new talents among our team members,” he remarks. “There’s a logistics specialist, for example, who enjoys programming in her spare time and developed an app that lets cell phones function as scanners.”
People remain indispensable
Many workplaces now have large screens that show employees what they should be doing with which tools in the next steps of their work. While this could be viewed as micromanaging, it can also be welcomed as assistance or as a direct form of quality control that the computer assumes for the worker. “Fortunately, our employees have adopted the view that the computers aren’t eliminating, but rather expediting, their work,” says Gollisch. And that is in fact the case at the vast majority of work stations. The people and their machines and programs complement each other, because each can contribute their respective strengths. But the people remain in charge. And are irreplaceable in many areas anyway. Siemens Healthineers employs glass blowers, for example, to produce its X-ray tubes. This classic skilled trade is indispensable for the high-end products made at the HEP Center.
That might be yet another lesson to be learned from this lighthouse project: one should focus on automation and digitalization—yet rely on one’s employees at the same time. Only when everyone and everything work together can it really be considered to be a factory of the future.
From Vision to Reality
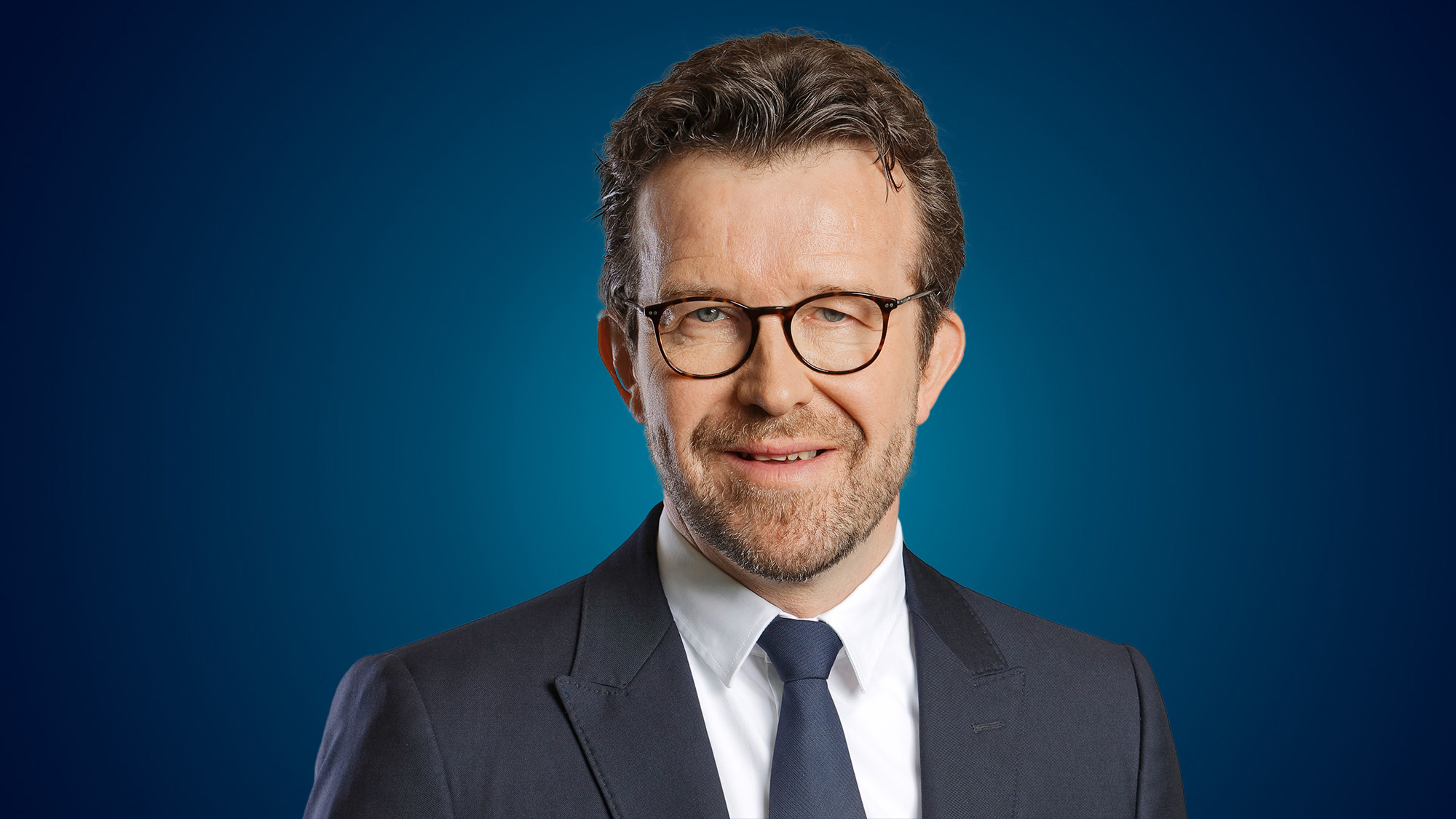