Operation
Powerhouse
Volkswagen is redefining the car, counting on electric drive systems. Thomas Schmall, member of the Volkswagen AG Board of Management responsible for Technology and CEO of Volkswagen Group Components, is leading the battery, charging infrastructure, and vehicle component activities and thereby mastering major parts of this challenge of the century — the strategic transformation of the world's largest car manufacturer.
04/2022
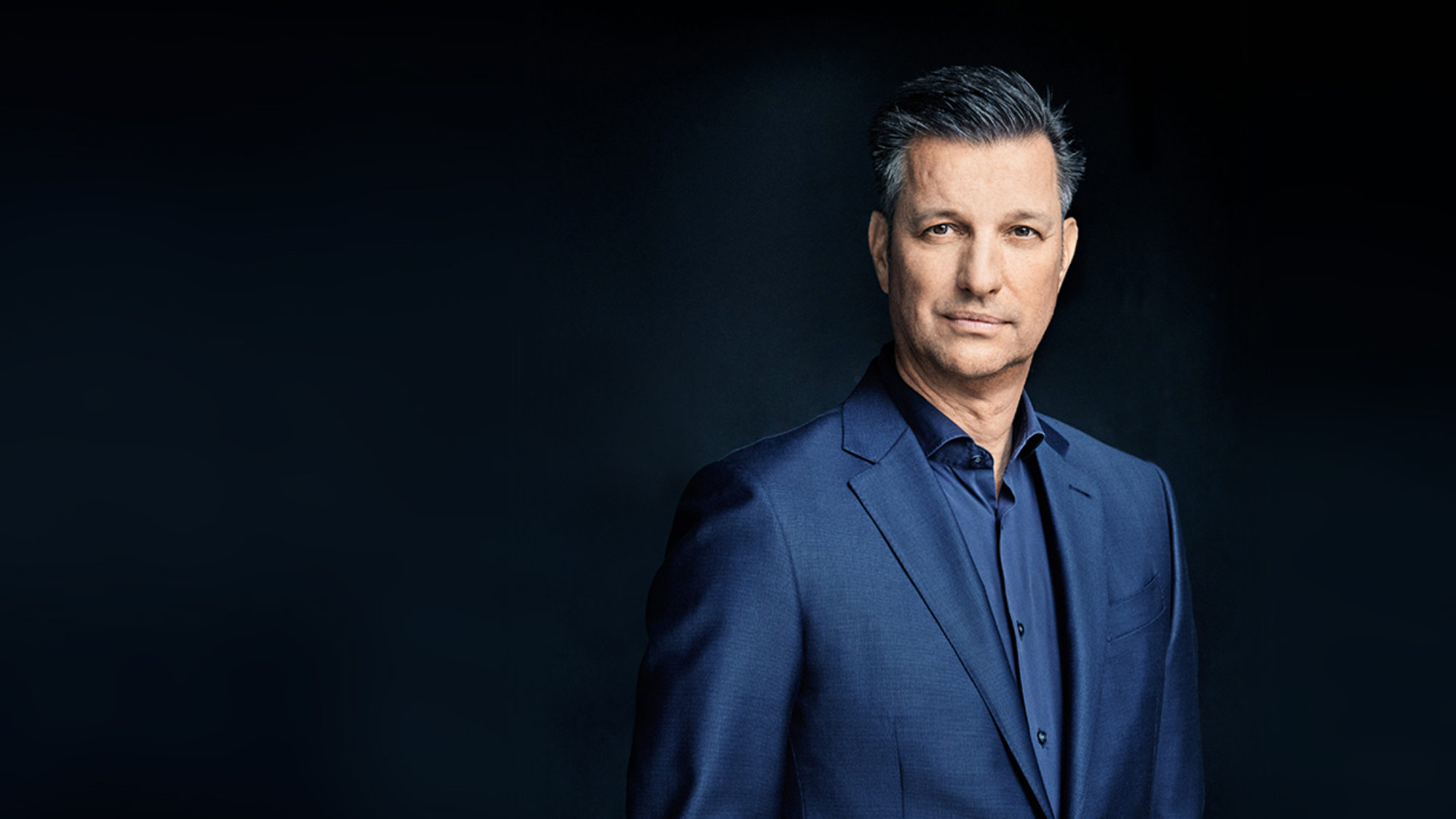
Despite all its retro charm, Wolfsburg’s “alte Gießerei” (“old foundry”) constitutes the control center of a new world. Its light-filled industrial halls with a non-hierarchical open-space design house the management of the Volkswagen AG Technology division and of “Components,” as employees still call the independent Volkswagen Group Components unit. With 75,000 employees at 45 locations worldwide, Components is a core part of the Volkswagen Group, which has a long-standing and nearly unparalleled connection with Germany.
Since its realignment in 2015, Components has pursued a veritably ground-breaking course, starting from a production unit for classic vehicle components like transmissions, engines, and raw castings and now turning into the nucleus of transformation in the era of electromobility. The new Group Technology division, to which Components belongs, now also develops and manufactures battery systems and drivetrains for electric vehicles. It moreover shapes crucial future-oriented topics such as charging infrastructures. Above all, however, Components is responsible for the important new battery business field, focusing on all steps along the entire value chain—from processing raw materials to developing and producing a unified cell format, managing the six planned European giga-factories, and generating business models for recycling used batteries. To consolidate all these battery-related activities, Volkswagen recently founded a European public company (Société Européenne).
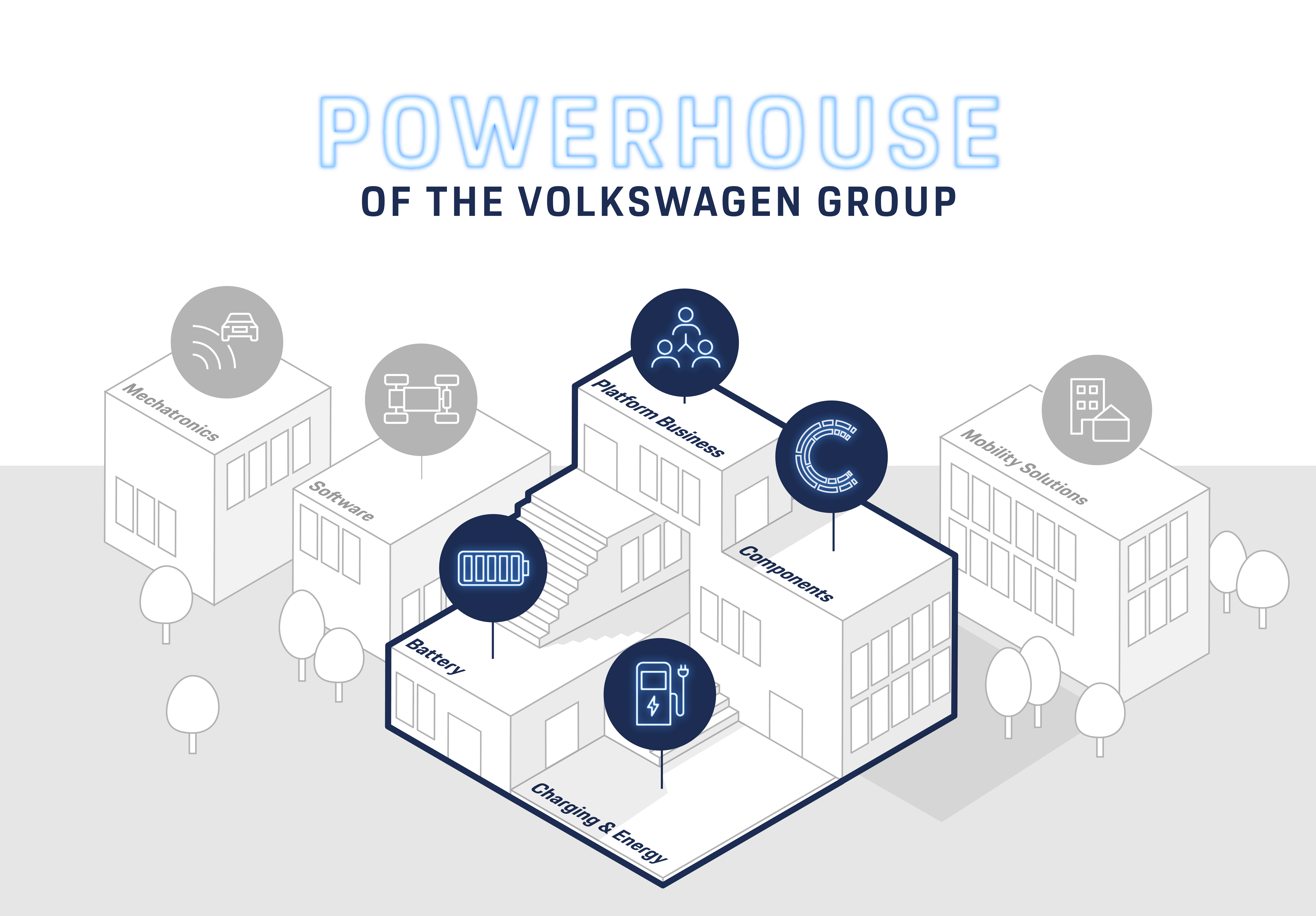
In this inspiring ambiance of the “old foundry” Thomas Schmall has his office. Born in 1964, this member of the Board of Management responsible for Technology is guiding what may be the largest restructuring project in Germany´s economic history. “We’d rather take on new topics actively than waiting passively to see how long we might survive with the old ones,” is his maxim. For Volkswagen, electric mobility is the future of the automotive industry: a journey down a road with no chance to turn around—a journey that must not fail. Market forecasts are bright, with global mobility sales expected to double by 2030.
Transforming the Components unit requires radical changes that Thomas Schmall has to cope with: new expertise and fields of business need to be established. International plants have to be gradually adapted and networked in efficient ways. Entire workforces need to be realigned and retrained to be ready for an electrified world.
The suppliers have to undergo an analogous transformation. There'll be an interchange between internal and external suppliers.
Not everyone will be involved in the Group’s redefinition project; however, most people will. “Fifty percent of our employees will already be working on electric mobility by 2025,” says Schmall. Many existing skills will still be needed in the future. After all, a facility manager for engine production is not far removed from an expert who oversees highly automated battery cell production.
Strategic Transformation
We will need to change how we think about cars. By 2030, the world of mobility will have undergone fundamental change. Zero-emission electric drives and fully connected autonomous vehicles will dominate the ways we get around. It is no coincidence that the Volkswagen Group’s strategy is called “New Auto—Mobility for Generations to Come.” If this strategy succeeds, the world’s largest car maker will have evolved from a vehicle manufacturer to a leading global software-driven mobility provider. Schmall’s sphere of influence is playing an important role in this transformative process. “Readiness for change and improvements to the performance of our Components unit were, and still are, key elements of our leap into electric mobility,” he observes. “Our own production already covers around 40 percent of the value creation for current e-models. In the future that will also include battery cells which are the most important part of an electric car.”
In this new world, new industrial standards have to be set. “No car manufacturer will be able to afford developing vast numbers of different drive systems and components,” says Schmall. An overarching platform is the promising concept here. Its key role becomes visible when it comes to the mass production of electric cars which has only been possible in connection with the new Modular electric drive matrix (MEB). By 2030, the Group wants to be producing around 26 million e-cars, most of them based on the MEB. High-volume brands like Volkswagen, Škoda, Seat, and Cupra are making extensive use of the toolkit. Incidentally, Ford will also be a client of MEB—it wants to use the toolkit for all-electric models in the future as well.
A platform approach reduces a lot of complexity and streamlines enormous processes.
The next step is to establish a uniform Group-wide ecosystem. As of 2026, the existing e-car platforms—not only the MEB but also the PPE platform for Audi and Porsche’s high-end segment—will be replaced by the Scalable Systems Platform (SSP). The SSP will enable development and production of all the Group’s brand models, in extremely efficient ways, because each brand will be able to make use of elements like electric modules.
Rethinking cars as a whole
There’s no getting around the fact that batteries are the key component of the e-mobility strategy, as well as the largest cost factor at around 40 percent of manufacturing outlay. The market is still dominated by Asian providers, but Volkswagen wants to change that. “Our goal is to lead the way in cell technology,” states Schmall.
To achieve this ambitious goal, the team in Wolfsburg is taking cell development and production into its own hands. And it conceptualizes the car models in a completely new way. Batteries will no longer be developed to fit the cars; instead, and right from the start, the cars will be designed around the batteries. The more uniform the battery format, the more cost-efficient the production. Volkswagen is therefore working on a unified cell that can be installed in 80 percent of its vehicles.
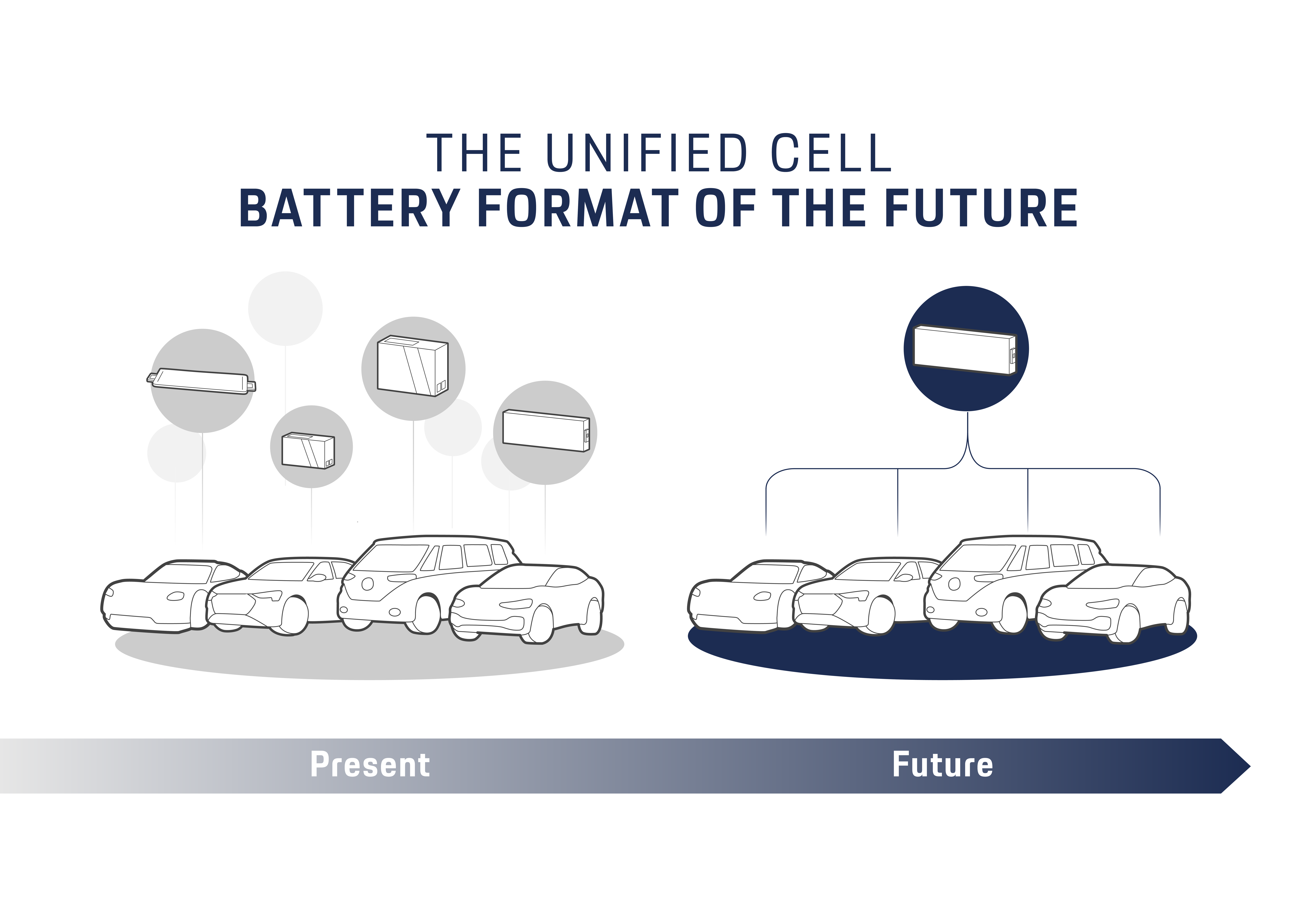
The intelligence behind battery design lies in the chemistry, explains Schmall. Test labs are currently working extra hours as they analyze constituents down to the atomic level. The Group is expected to start its own unified cell production in 2025. “Then we’ll be on equal footing with the competition. And our unified cell will be state-of-the-art.”
The next step in technology will be solid-state batteries, which feature lower weights, greater ranges, and shorter charging times. “They represent a real quantum leap over how we currently conceive of batteries,” says Schmall. “The first car maker to bring solid-state batteries to series production will enjoy a crucial competitive advantage. We’re expecting our first pilot plants in 2025 or 2026.” Volkswagen is collaborating closely with the US-based company QuantumScape.
Wolfsburg is showing a high degree of openness to external expertise in general. Sweden-based Northvolt AB is another of its partners, as is Gotion, a Chinese battery cell expert. Three additional strategic partnerships were recently launched with Umicore, 24M Technologies, and Vulcan Energy Resources to advance the industrialization of relevant technologies and large-scale series production of sustainable and innovative batteries. That was followed by a collaboration agreement with Bosch to industrialize battery cell production processes. “We’re well advised to bring technology partners on board and collaborate with them in shaping the transformation process,” says Schmall. By 2030, Volkswagen wants to build with its partners six new gigafactories for cell production in Europe alone, with an annual production capacity of 240 gigawatt hours. That should be enough to furnish batteries for up to four million passenger cars.
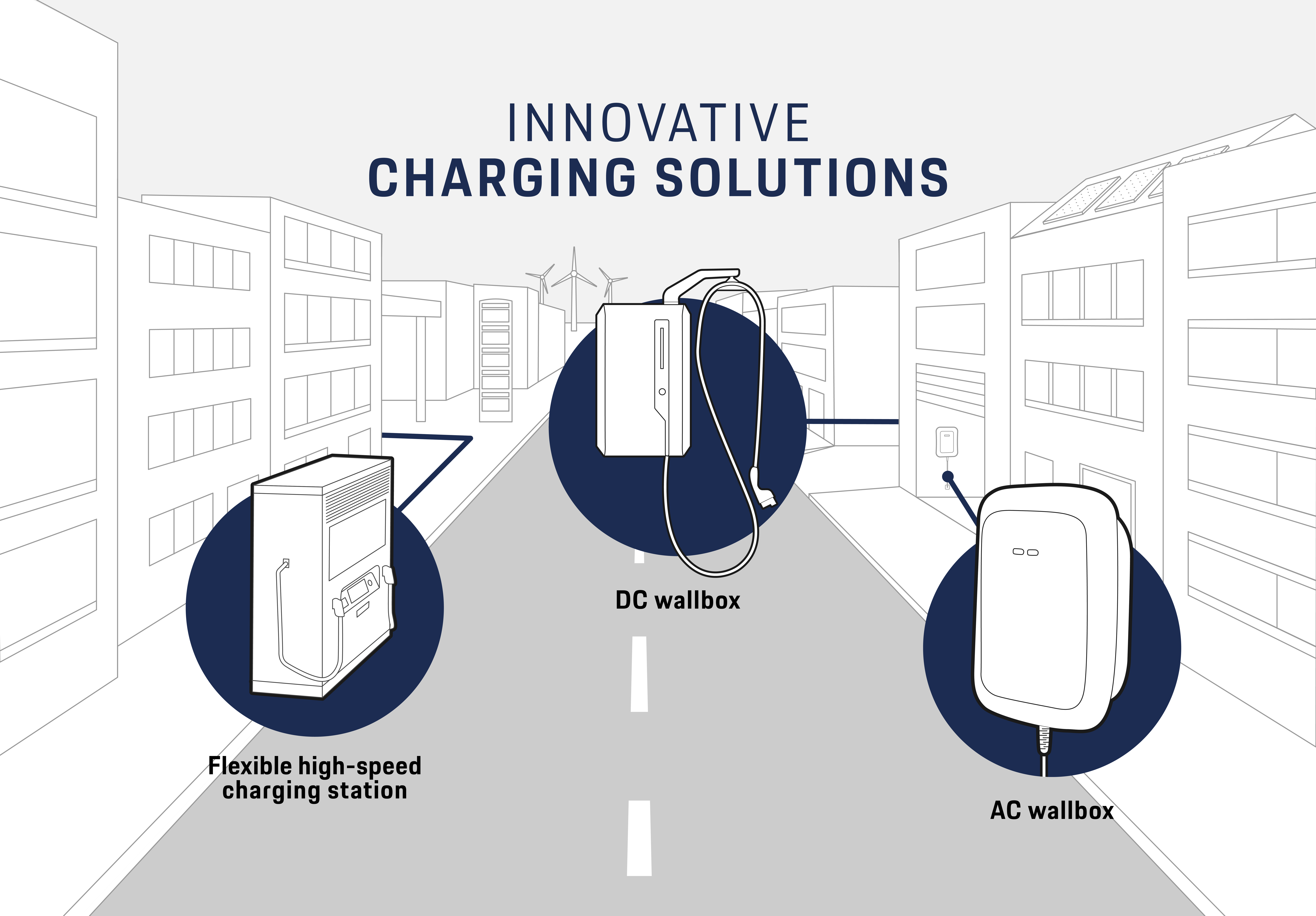
The aim of this vision—although Schmall is too prudent for rash pronouncements—is nothing less than to overtake Tesla. The US-based manufacturer is still leading the world in e-car sales and is considered a driving force for future automotive developments. Schmall wants to change that. “We have a clear plan, and we’re following it closely. We have the capabilities, the scope, and the expertise.”
From purely car maker to "new business factory"
The transformation to electric mobility is also opening up completely new fields of business. E-cars will no longer just carry passengers and goods, but also serve as mobile power storage units. They will be able to draw power from a solar facility, for example, and feed it back into the local grid after sundown. This will operate in parallel and without any limitations to mobility, because the high-voltage batteries in modern electric cars will be that powerful. Viewed over the long term, e-cars could even serve as mobile power banks for the entire grid. Experts see new opportunities here too, and suddenly find themselves negotiating collaborative ventures with interested energy providers.
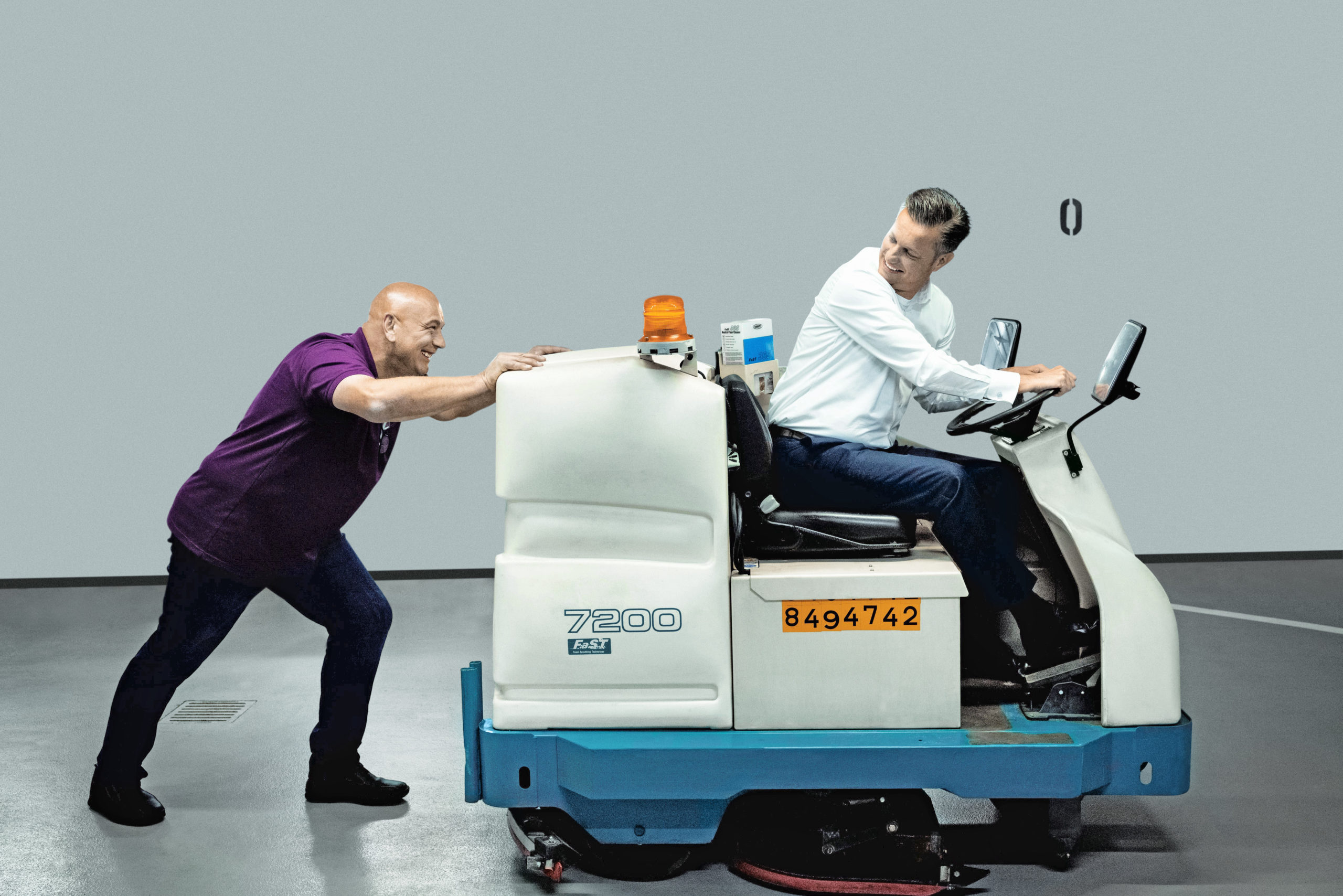
But new worlds can only be mastered if everyone in the Group pulls together. It remains a cultural challenge to sustainably anchor the new mentality and a stable culture of “We can do this together” right across the diverse workforce. As Schmall puts it, “Transformation will only succeed if we have strong leaders and can clearly communicate our aims and how to reach them. We have to set an example in this process and make sure our teams are on board. That’s what will carry us together throughout this entire enterprise.”