"Not to push,
but to pull!"
Dramatic transformation: The workforce is expected to use its expertise to dismantle its workplace and sell the resulting materials as reusables or dispose of them as waste. Nikolaus Valerius, Chief Technology Officer of RWE Nuclear GmbH and Member of the Executive Board, Nuclear at RWE Power AG, is turning this into a formula for success.
05/2022
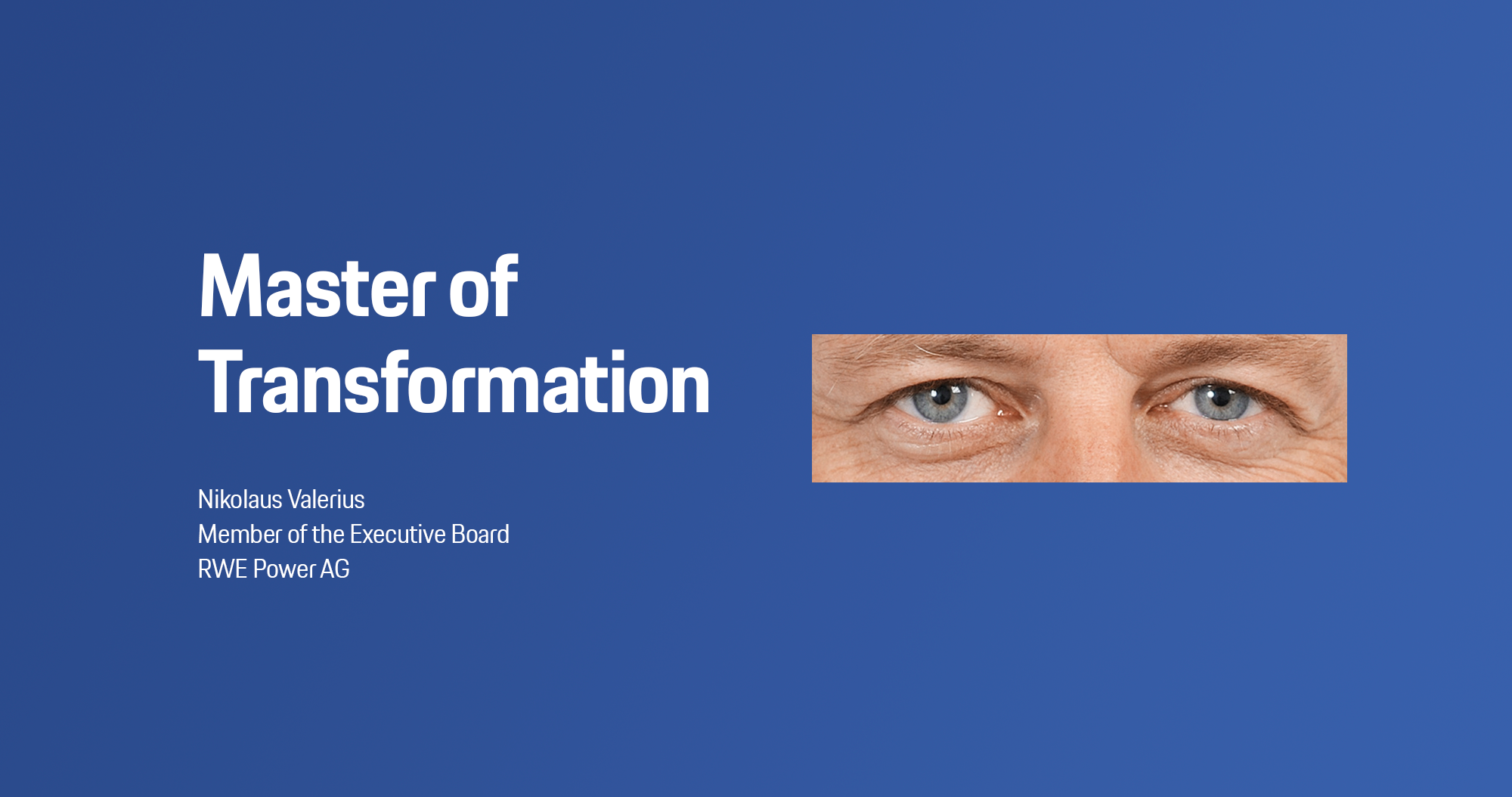
What was the goal of the transformation at RWE Nuclear?
To change from an energy provider into a company that dismantles power stations. Dismantling our plants so nothing is left but green fields yields materials that can be fed back into a conventional use cycle. You can do that with around 95 percent of a plant’s materials. Around 2 percent are packaged in the requisite ways and handed over to the German government for intermediate and then final storage. Of special note here is that we’re doing two things at once, because while we’re dismantling we also have to keep producing power, like in Lingen until the end of 2022 or in Gundremmingen where we did so until 2021.
What are the main changes for the employees?
For large parts of the workforce everything has changed—except their employment contracts. We launched this transformation systematically in 2018. We began by bringing around 15 employees on board, from Lower Saxony to Bavaria. Then we started the “Wir in Nuclear” (“we in nuclear”) program with the aim of taking everyone along on the transformation journey. Right from the start, we also and especially worked on our corporate culture. Additional steps included instituting new processes, a new control system, and a new structure to handle the dismantling work. We immediately set up a team whose job it is to sell the materials we get from the dismantling process, like concrete, synthetics, and metals.
How did your company's employees react to the upcoming changes? Did different levels of the hierarchy respond differently? And did everyone feel they were included?
While top managers joined in very quickly, a number of mid-level managers needed a closer look at our ideas. Some of our colleagues were not exactly overjoyed at the changes, and were concerned they would suffer losses on an individual level. On the other hand, many employees like technical and trade specialists shifted relatively quickly to the idea of becoming a dismantling company. A conceptual approach proved to be helpful. Leadership personnel has to explain the solid logic behind the change in precise detail. The more the workforce can understand and assimilate that, the faster the transformation can proceed. In our case, understanding was followed by enthusiasm. And the desire to be part of it.
RWE Nuclear: Dismantling as a Business Model
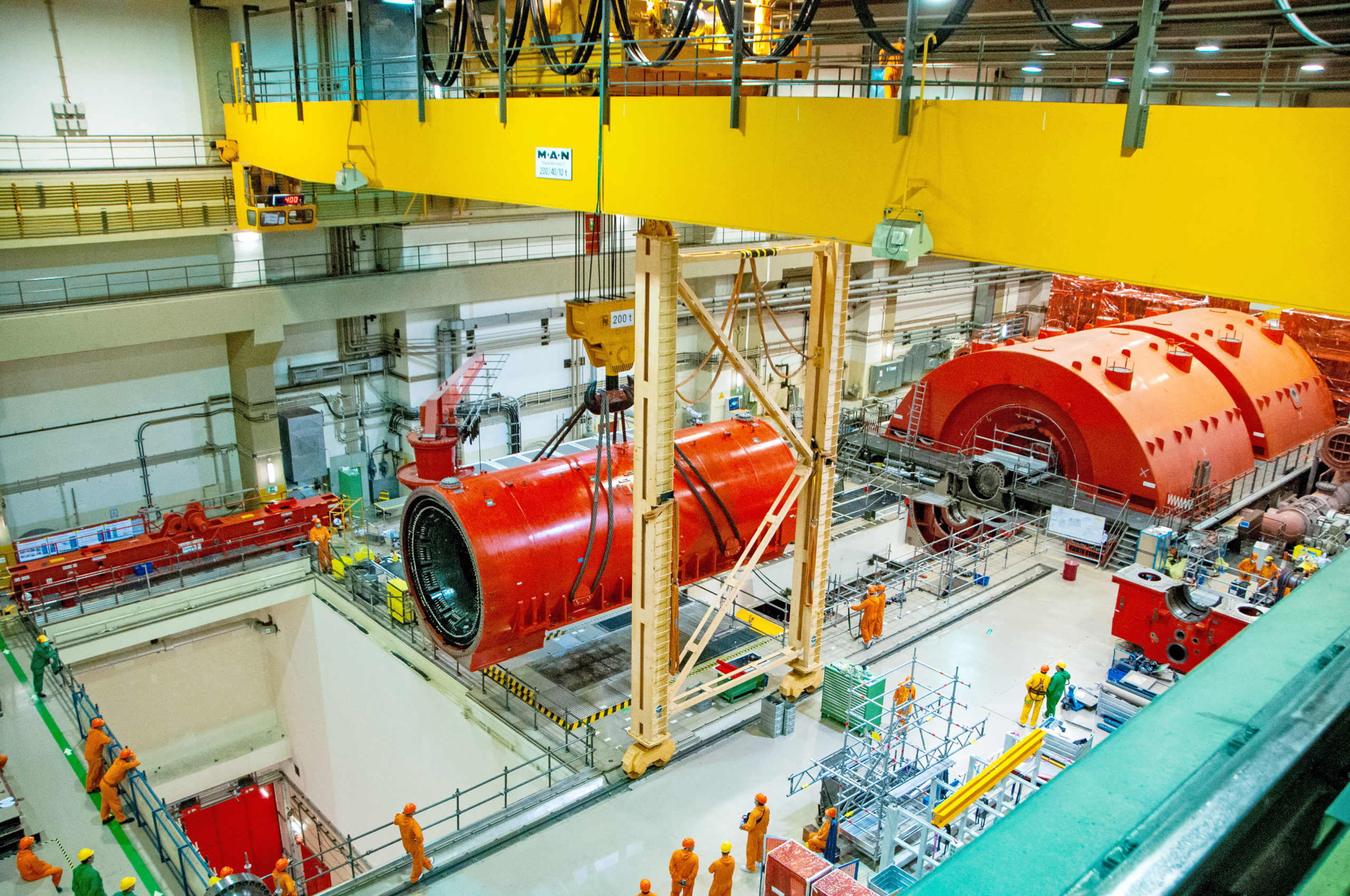
How did you view your own role in the transformation, and what part did you play in conveying it?
If conviction and enthusiasm are what you’re after, you have to start with yourself. And that includes understanding the situation, formulating the goal, and charting a new course—from the perspective of both the company and the employees. That’s not something you do alone. It’s just as crucial to bring direct leadership on board as it is to take a program or project approach to reach employees from all corners and levels of the hierarchy. You want a coalition of constructive critics and dedicated backers! So that’s the way we organized the work, and we created forums for discussion and input. When I took on this job in 2017, I was helped by having begun my career in the nuclear energy sector and spending the first three years learning the craft, so to speak. Knowledge of the industry also made it easier to analyze, to persuade people, and to communicate in credible ways. I listened, explained, and tried to motivate. If you need complicated arguments to explain a new process or structure, it means you haven’t grasped it fully yourself yet. Or conversely: if it’s clear, it gets simple. And then everyone understands it! My aim and my role are to have leaders convince and motivate employees. Not to push them in a certain direction but rather to pull them and bring them to where they are themselves. Leadership means leading the way.
What else is important for a transformation to be successful? Did you change existing guidelines, indicators, and incentive systems?
We work with clear language and goals, whether it’s a short-, medium-, or long-term context. In 2021, we wanted to dismantle and recycle around 3,600 tons of material, and we managed an impressive 4,500. In 2022 we’re aiming for 6,000 tons. We show the employees our progress on a weekly basis. And our performance incentives don’t exclude anyone. After two years it’s abundantly clear that we’re serious, and didn’t just go “leaping onto a bandwagon.” That’s another reason the employees are pulling together. But nothing is perfect, of course. Not everyone feels accommodated all the time, not everything runs smoothly without exception, and we don’t always meet all our goals. There are “gaps to target,” in other words. But we’re spotting these discrepancies faster and working to solve them.
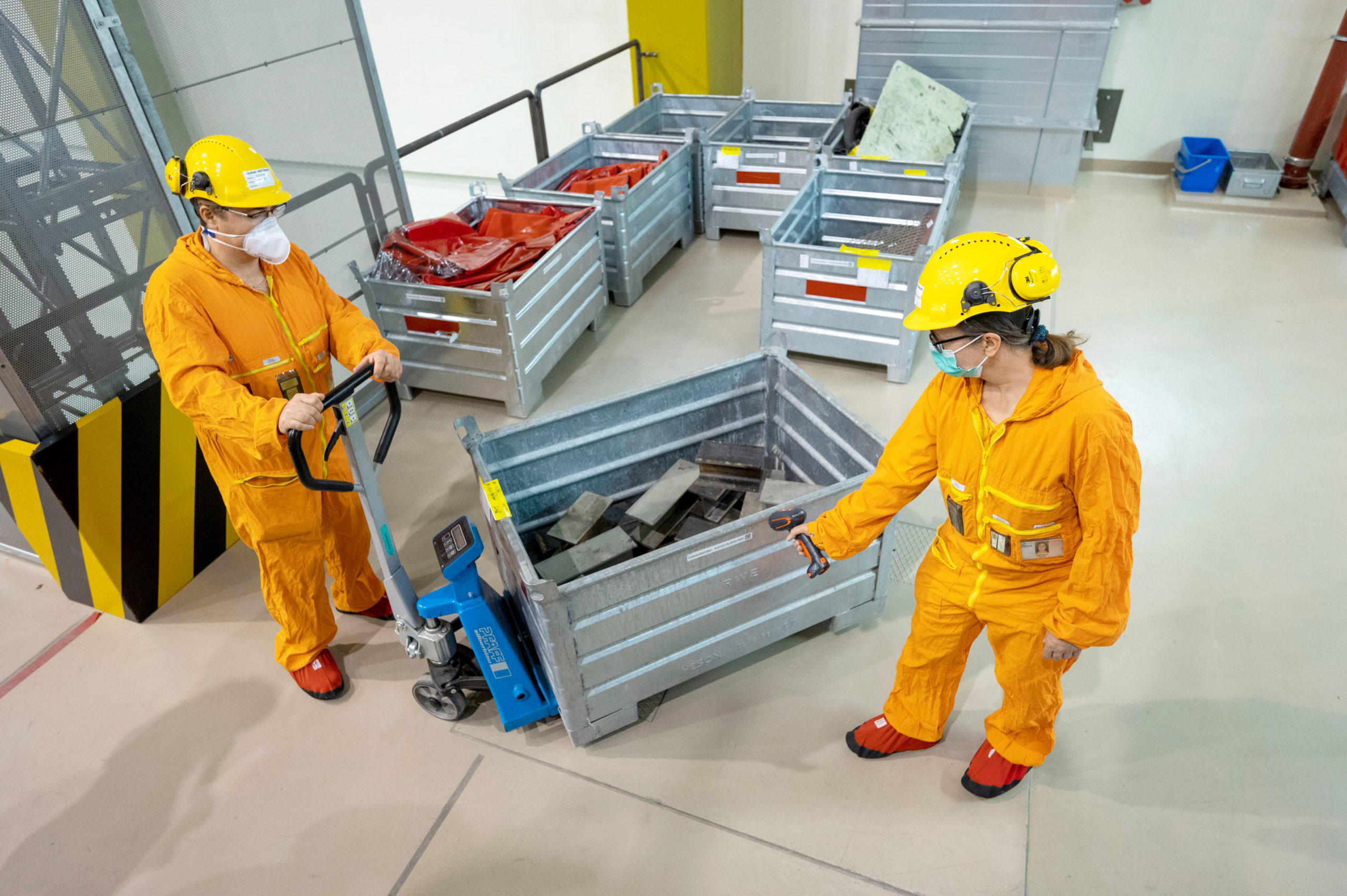
Has the change meant having to alter traditional forms of collaboration?
Yes, totally. Here’s one example: there used to be the headquarters—the main office. It handled a lot of the management, rules, and directives. This office was far removed from the workers at the power stations. Now we’re better organized. Our individual plants are always the centers of our operations, and the organization in Essen is set up to provide the sites with expertise and support to reach our shared goals. Cross-site groups of experts are in charge of specific issues and make decisions that we carry out everywhere. Yet each group is also responsible for a specific portfolio. That’s very valuable, because for key questions we need the full range of power and know-how from all our people.
A transformation means that employees need new types of knowledge. How did you develop these skills?
One important factor is the cross-site transfer of ideas and expertise we just mentioned. Colleagues from the Gundremmingen site observed the dismantling processes at the Mülheim-Kärlich, Biblis, and Lingen stations. Instead of focusing only on one’s own site—as was previously the case—we’ve replaced this typical silo thinking with a “we process.” All the employees are now pursuing one and the same goal. Our own specially instituted dismantling academy is a good tool for imparting knowledge, as are online-based training programs. We also get all manner of useful knowledge from the market, like from suppliers. The dismantling simulator that we developed ourselves is also helpful in training and qualifying people for new tasks. Every employee studies our integrated dismantling process for two days in the course of a simulation. That also encourages people to come up with new ideas and innovations.
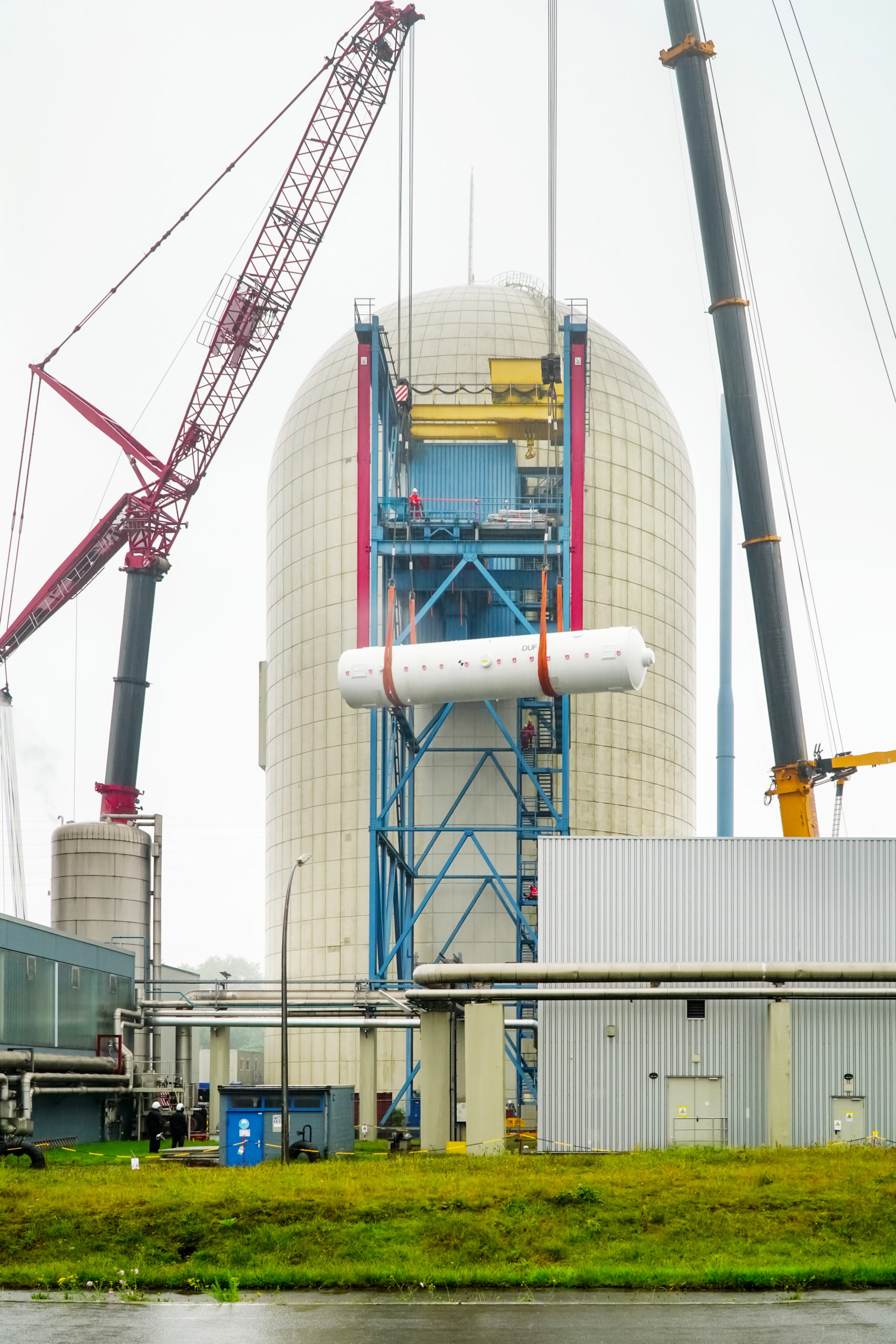
What was an especially key factor in the success of this transformation?
Our transformation isn’t finished; the real dismantling work is only beginning. Together with the employees we’ve laid a robust foundation for it. And the transformation doesn’t stop with our own team. Suppliers, auditors, public authorities—they’re all integrated into a process we’re ultimately driving and coordinating. It has run smoothly thus far because we’ve communicated a coherent idea clearly and made strategic leadership a core part of our corporate culture. Leadership personnel has to organize the work such that employees can do what they’re good at. Then you’ll also get good results.
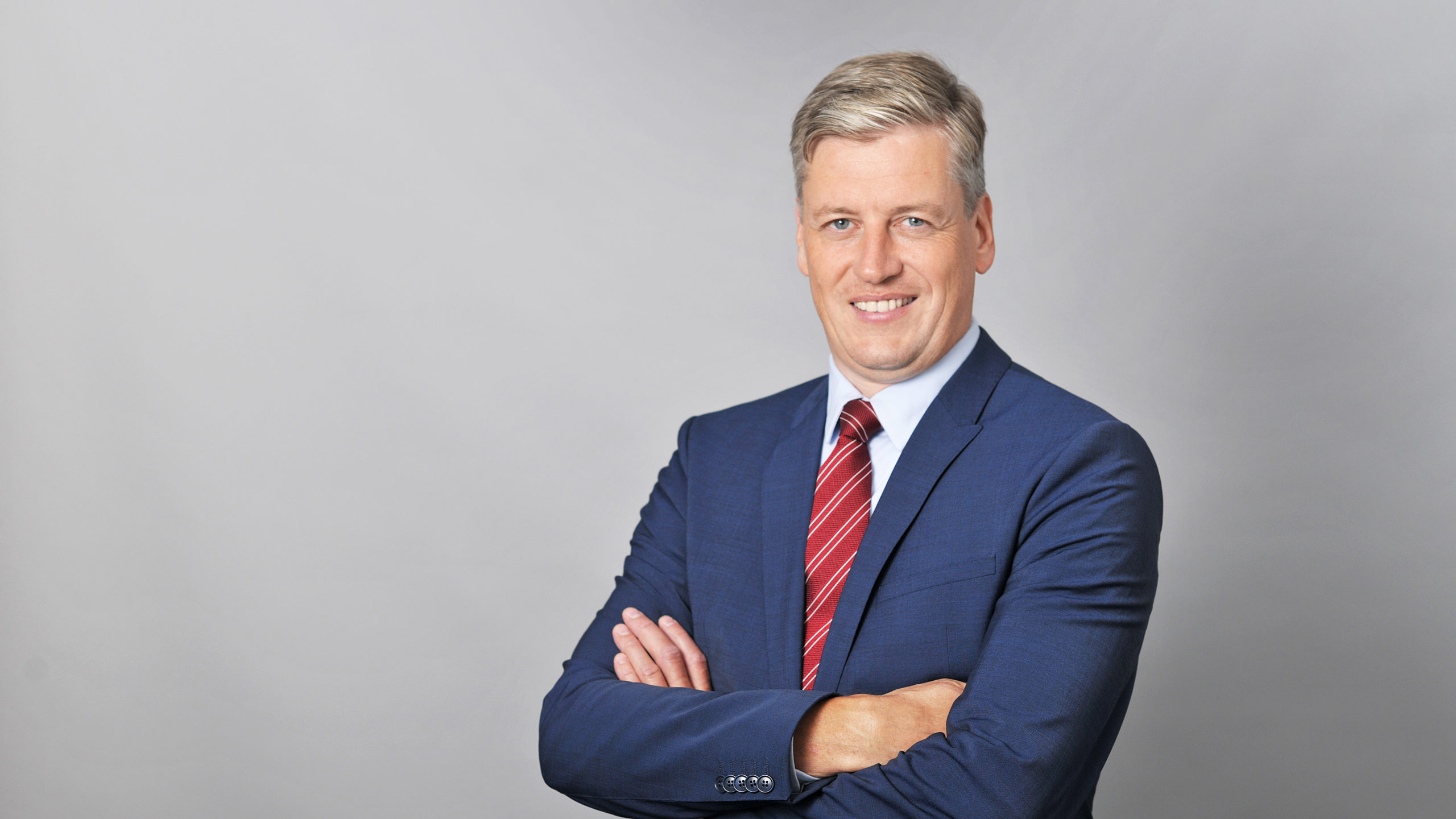