Thomas Schmall:
“Success Factor
Raw Materials”
Lithium, cobalt, and nickel are three substances that make electromobility possible — and that also create dependencies. Porsche Consulting Magazine asked Thomas Schmall, the member of the Group Board of Management responsible for Technology, how Volkswagen seeks to ensure supply and sustainability over the long term.
05/2024
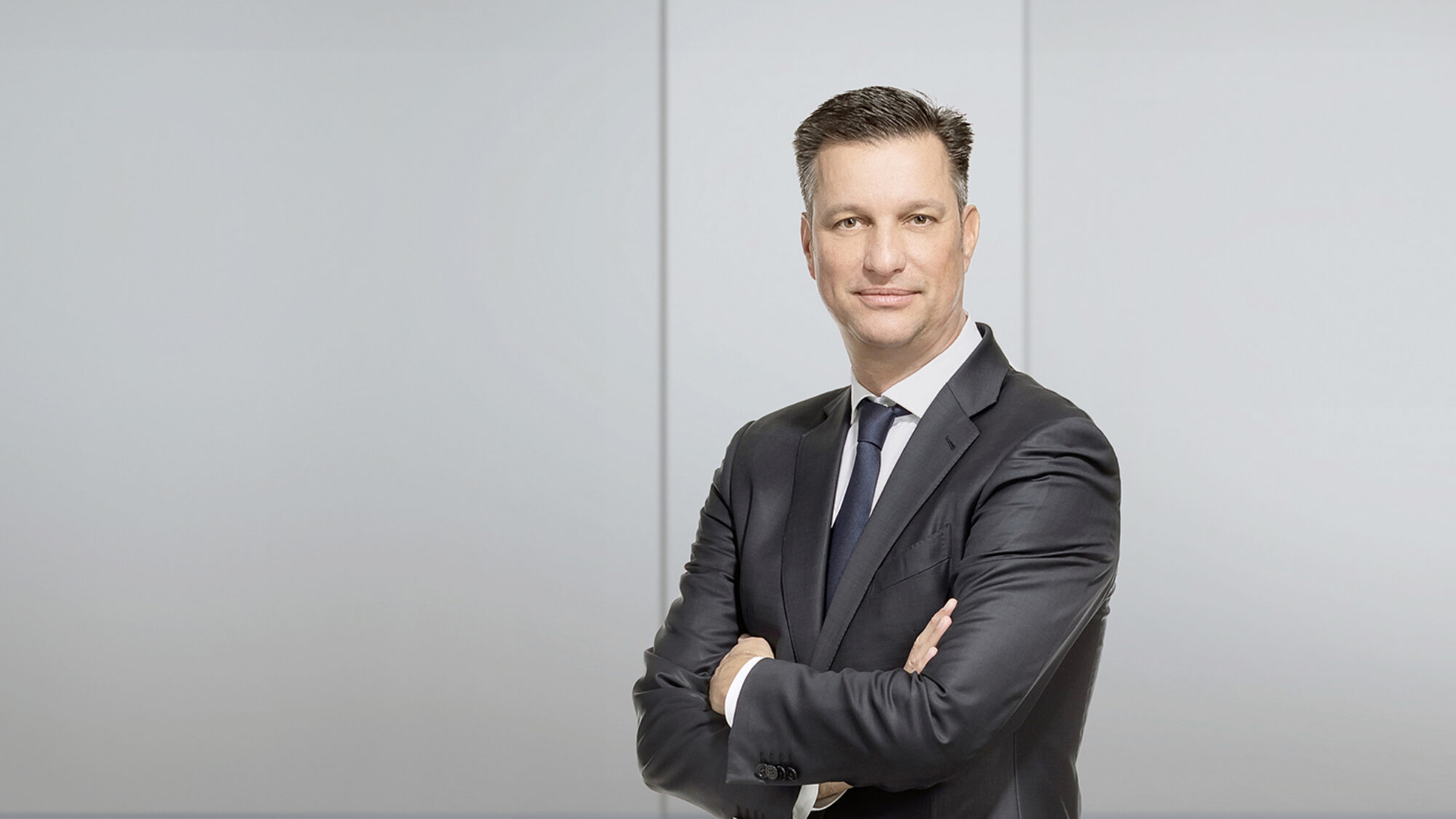
Mr. Schmall, let’s talk about raw materials. Why is this topic becoming so important in connection with electromobility?
First of all, e-mobility is and will remain the key to greater climate protection in traffic and transportation. Electric drives will be powering most of the vehicles on our roads in the future. We as a company have made a very clear commitment to electrification and are pursuing this strategy worldwide. But the shift to electric cars means changing the entire value chain. The technological and commercial heart of each vehicle is now the battery. And when you look at batteries, you quickly see that raw materials are by far their largest cost item. A crucial factor on the road to affordable electric cars for everyone therefore consists of competitive costs for battery materials like lithium and nickel.
But these raw materials are said to be in short supply. Not a good situation, right?
A stable supply of raw materials has in fact become a major competitive factor. Not only for Volkswagen but for the entire industry. The shortages have less to do with global deposits than with the available capacities for mining and further processing them. Over the past years we’ve seen very volatile raw material prices, a veritable roller coaster. In order to shield ourselves from this over the long term, we’re taking a very strategic approach to raw material procurement.
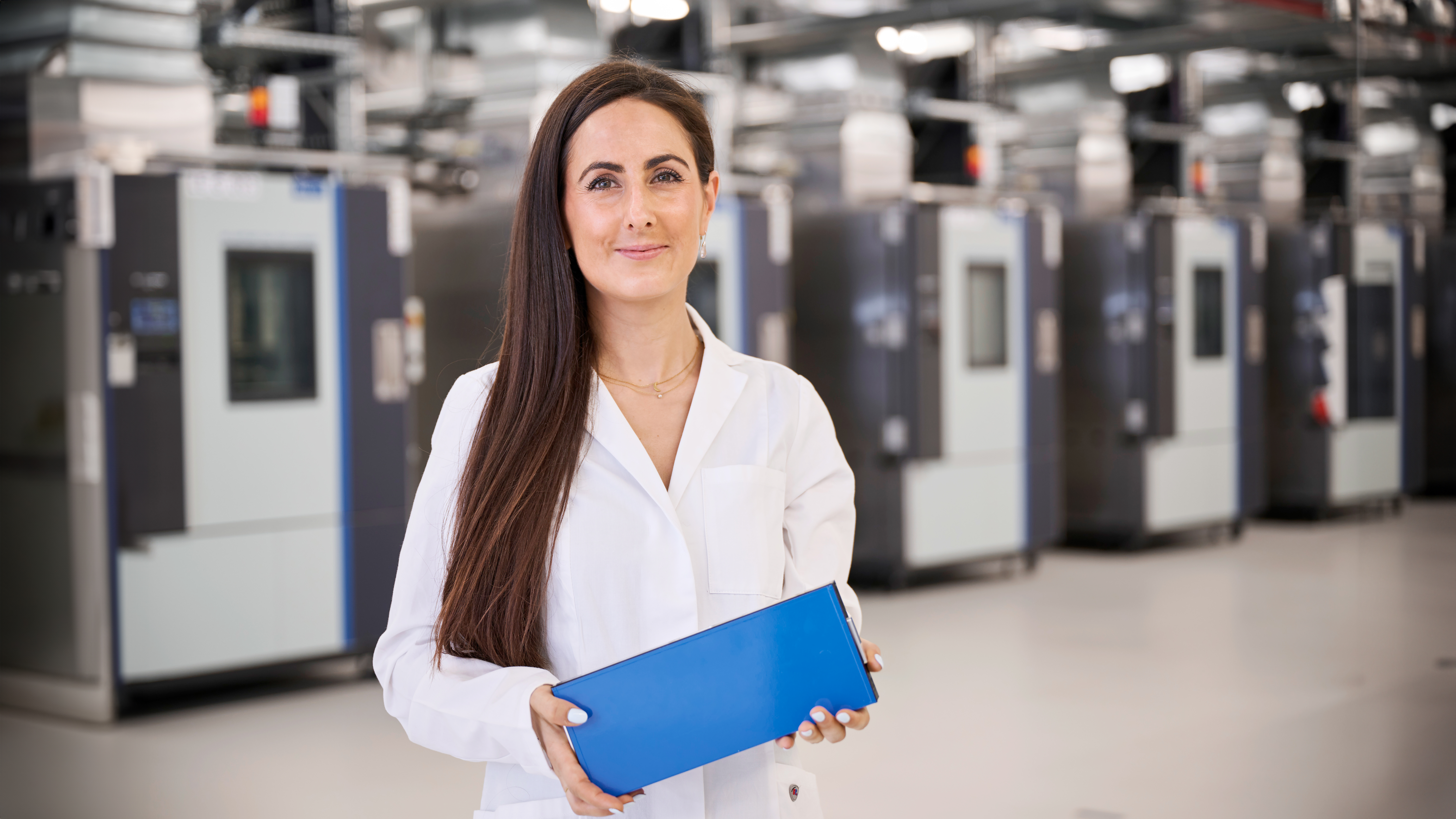
What does that strategy look like?
PowerCo’s strategy is based on an integrated value chain. That means taking all the relevant areas, from raw material procurement and processing to cell production and recycling, into its own hands — both independently and with partners.
Right now we get all our battery cells from external suppliers, who also procure the raw materials. That will change in 2025 when PowerCo begins running its first gigafactory in Salzgitter and powers up its own cell production. Gigafactories in Valencia and in St. Thomas in Canada will follow. At the same time, we’ll be taking greater control of our raw material production and processing.
What does that mean in concrete terms?
Here’s one example: we founded the IONWAY company with our Belgian partner Umicore to produce cathode and preliminary materials. That’s basically the step between mines and cell factories. We’re working together to build Europe’s largest cathode production plant in the Polish town of Nysa.
Above and beyond that, recycling and second-life applications are also important, such as using old e-car batteries in energy storage systems. We need that in order to cover our long-term raw material needs on our own. It’s good for the environment, and it’s also its own business division with considerable potential to make our prices even more competitive.
Will Volkswagen also be running mines in the future?
We’re looking at that very closely right now. We certainly want direct access to the relevant raw materials. To do that, we’re concentrating on long-term supply contracts with raw material producers and on financial instruments to secure prices, but can also imagine investing directly in mines. That makes it easier to calculate not only access to key materials but also costs. The current status is that PowerCo has already covered a large part of its relevant battery material needs up to 2030. The goal is a robust, sustainable, and competitive supply of raw materials, enabling us to ensure our transformation to electromobility and take the next step toward worldwide leadership in e-mobility solutions.
China plays a dominant role in the battery sector and also controls a large part of the raw material business. Is it even possible to become independent under these circumstances?
It’s not a matter of independence but rather of a reasonable balance. We’ll continue to use external suppliers in the future, including from Asia and China. But with PowerCo we’re establishing our own strong alternative for the core field of battery technology.
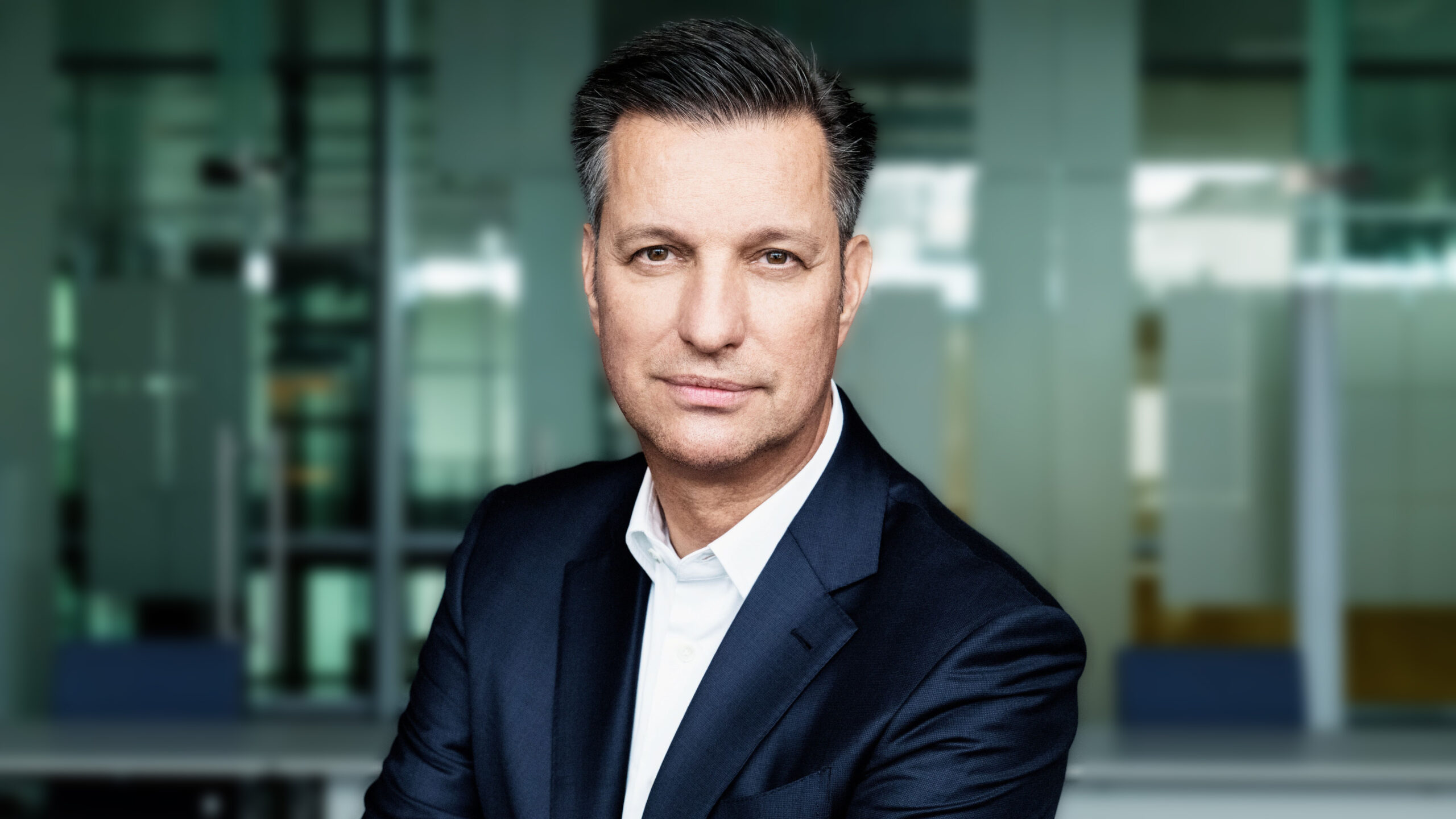
Lithium, cobalt, and nickel are critical raw materials that are sometimes extracted under very contentious conditions. How will you prevent possible violations of human rights or environmental standards in your supply chains?
We take our responsibility for sustainability, the environment, and human rights very seriously — not only on paper. Volkswagen already requires its suppliers to commit to high sustainability and safety standards. And we monitor compliance on site. By 2040, more than 95 percent of the Group’s suppliers should be able to demonstrate a positive sustainability assessment and certified environmental management. We’re also making ourselves very transparent as a company: for four years now we’ve been publishing a Responsible Raw Materials Report on our own initiative. It covers 18 raw materials we’ve identified as critical to the supply chain, including battery materials such as lithium and cobalt. As far as I know, we’re the first in our industry to do so.
No contracts without sustainability?
That’s what we’re after. We want to make a positive contribution to transforming the raw material sector and to minimizing the consequences of extraction as much as possible. With direct access to mines and their operators, PowerCo will give us more opportunities to do so. But I have to warn against unrealistic expectations. Decarbonizing the economy and society will always impact nature in some way — the processes are currently highly dependent on raw materials such as lithium, cobalt, and nickel. The materials we extract today are the key to protecting the climate in the future. Recycling as part of a raw-material loop can also considerably reduce the impact over the foreseeable future.
The road we’re taking to get there, with its clear commitment to sustainability, is both necessary and very challenging. However, it will pay off with systematic decarbonization, the prospect of lower environmental consequences throughout the entire value chain, higher volumes, and greater control over costs. That will mean lower-priced cars with adequate profit margins, which will enable us to achieve our goal of making sustainable mobility available to everyone.
Carmakers often talk about supply chain complexity, which can make it very difficult to trace materials back to specific mining sites. That will change once you gain access to these materials or even operate mines yourself, right?
That’s correct. Integrating the entire battery supply chain does in fact offer new opportunities. In the future we’ll know much more precisely where the raw materials for our e-cars come from. For example, mine operator agreements can require them to work with IRMA standards, which are the best and highest standards for responsible mining. We can also ensure compliance considerably better, for instance with new possibilities arising for dialogue on site with local communities. That’s part of the responsibility we’re taking.
How realistic is the vision of green sustainable batteries?
Sustainability at any price is just as unhelpful as ruthlessly low costs. Our goal is to combine the two requirements and set the industry standard for sustainable and competitive battery cells. PowerCo is planning to reduce battery costs by up to 50 percent with its unified cells. At the same time, we’re working on a series of technologies and measures to substantially lower our resource requirements over the coming years and decades. That includes minimizing carbon emissions from raw material extraction, and also using batteries that don’t contain any cobalt or nickel. Our cell factories will be operating on carbon-neutral power. We’re also banking very strongly on a circular economy that immediately recycles production surpluses and reuses the raw materials from batteries at the end of their service lives. In Salzgitter we’re running our own recycling plant to further maximize our quotas here. All these steps will also benefit our customers. For PowerCo I can say we’re not yet where we want to be, but we stand behind our vision and are working hard to achieve it.