The Launch of Smarter Construction
The construction industry cannot keep up with the demand for housing. This is largely because construction sites are not efficient enough. New technologies and business models could succeed in cutting this Gordian knot.
09/2020
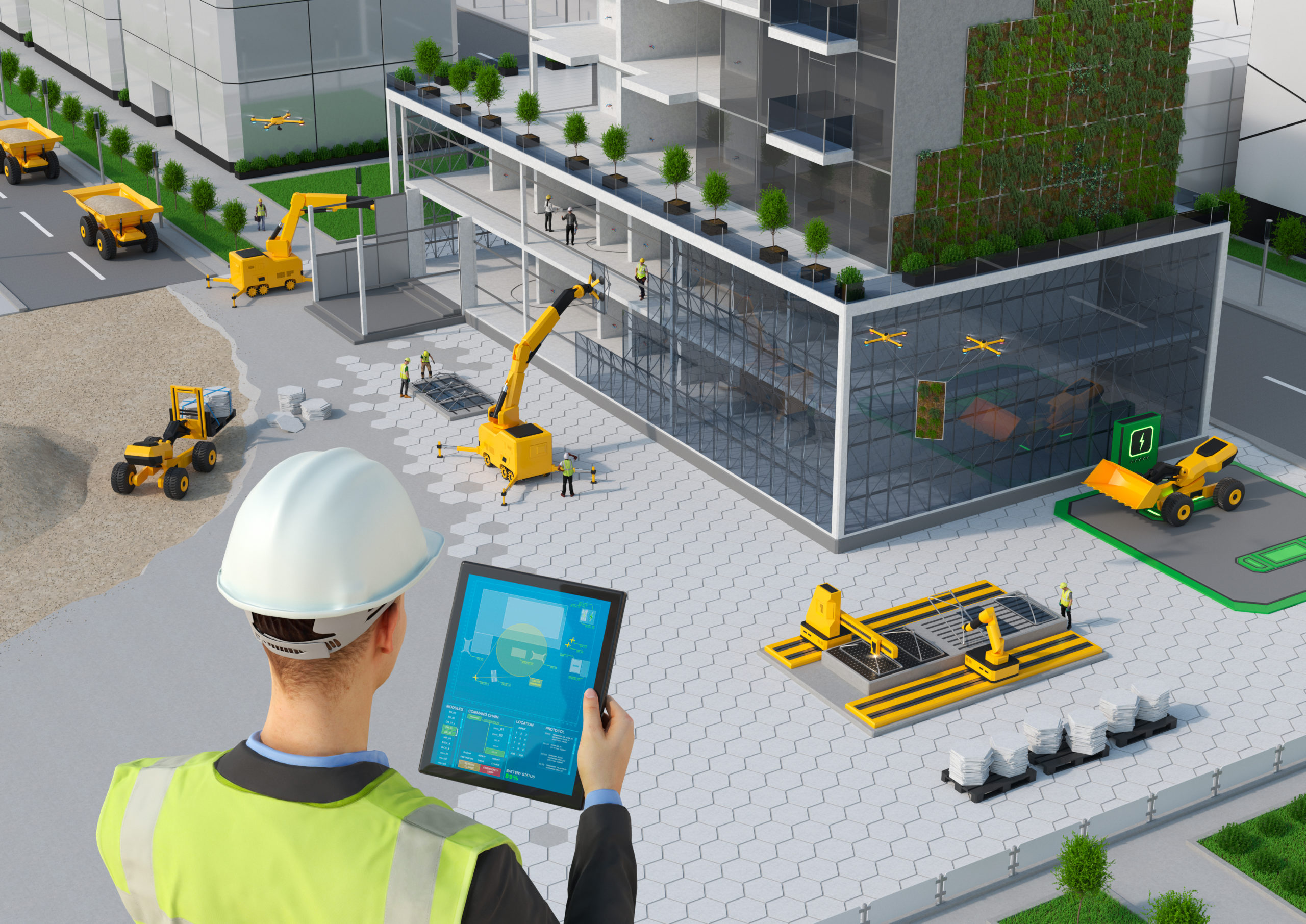
There’s no doubt that the shortage of housing in major cities will increase all the more over the next decades. The UN estimates that by 2050, seven billion of the world’s ten billion people will be living in cities. New metropolitan centers of unprecedented size will arise. There are currently more than thirty megacities of more than ten million inhabitants. Living space is becoming ever more scarce. According to an analysis by the World Economic Forum, around 1.6 billion more homes will be needed in the next thirty years alone. Moreover, people in many urban centers are at a turning point. They no longer want urban planning to focus on cars, but instead want greener and more sustainable policies. At the same time, buildings are facing ever greater demands—they are supposed to be smarter, more energy-efficient, and offer universal access. All these considerations are directly linked to the following question: What should construction be like in the future?
Construction sites of the future will produce hardly any exhaust gases or noise pollution. They will be much safer and more orderly. Above all, they will be faster and more efficient. Electrified excavators controlled remotely by camera will be connected with construction machinery featuring sophisticated sensor systems that let them proactively notify manufacturers of any technical problems. Drones will fly overhead to register progress at the site. And driverless trucks will deliver entire prefabricated building modules just in time, which will be assembled in short order by robots. A large part of the work will be done in factory halls before the ground is broken. Skilled workers at the site will assume largely coordinating functions or work “hand in hand” with the robots. And virtual dashboards will always be available to let them monitor and guide construction progress in real time.
Most buildings are made on a craftsmanship basis.
Lego construction principle
Much of this is still a long way off. “Little has changed at construction sites for decades, and the teams often lose track of the overall picture,” says Uwe Brühl, vice president of digital building solutions at the Sto Group, a leader on the international market for innovative construction materials based in the Black Forest town of Stühlingen. “Construction machines are becoming more efficient and new processes are taking root, but most buildings are still made on a craftsmanship basis.” The ability to adhere to schedules depends on weather conditions and frequently also on chance, and construction defects have a negative effect on the company image. Although price-adjusted productivity per working hour has increased by an average of 44 percent relative to work volume from 1991 to 2018, the construction industry has essentially stagnated, with a 4 percent increase during the same period of time. In Brühl’s opinion, the history and traditions of the trades are acting like a brake on progress. “For a simple single-family house, you need different professionals to do the excavation, shell construction, tiling, sanitary facilities, windows, and roof, so you end up with thirty or forty specialists, each with their own plans and views. This results in new lineups for every project, and these conditions often make it impossible to have efficient processes.
Yet another problem lies in the shortage of skilled workers, both now and in the future. This situation is evident across the industry. Large-scale construction projects in industrial countries are no longer possible without the help of migrant workers. But these workers tend to concentrate only in the boom markets of certain regions. In addition, highly qualified young professionals such as engineers and architects are switching to other industries after a few years. And construction costs have been rising the world over. These factors are prompting investors to search for alternative solutions. Replacing a purely project-oriented attitude with a mass production approach featuring higher levels of standardization and modularization could achieve the sought-after level of productivity at construction sites. The advantage of this method lies in the ability to put buildings together like Lego blocks. An astonished world witnessed how the principle works in early 2020 in the Chinese city of Wuhan at the start of the coronavirus epidemic. Two completely equipped hospitals were set up there by modular means in only ten and twelve days, respectively. Yet the industrial production of homes is an issue that has divided experts since the beginning of the twentieth century. Its critics fear a “McDonaldization” of architecture.
We’re moving construction sites into factories
“Modern technology has taken modular construction to new heights. We can produce buildings in more individualized ways and on considerably higher levels than ever before. We can reduce complexity by a factor of ten, and overcome some of the traditional divisions of labor among the trades and replace them with strong value-adding partnerships,” says Brühl. In the USA and Canada, the Sto Group and its network of partners have been making modular interior walls and façade components since 2013, which are furnished with insulating materials, plaster, paint, brickwork, natural stone, or stucco elements and then delivered for assembly. What does this mean for total construction times? “It shortens the construction time for something like a hotel project from one and half years to six months,” says Brühl.
Inspired by the shipbuilding and automotive industries
According to Mikael Hedberg, CEO of the Finnish Admares start-up, construction sites should essentially become assembly sites as soon as their foundations and basements are completed. “We’re moving construction sites into factories, because automated production of modularized building complexes is the only way to significantly improve the quality and reduce the costs in the real estate sector,” he says. He expects this approach to cost up to 30 percent less than conventional construction methods. It would shift 80 to 95 percent of the value-adding processes from construction sites to industrial production facilities, and bring enormous changes to the traditional building sector.
Admares: Digitalizing the Construction Industry
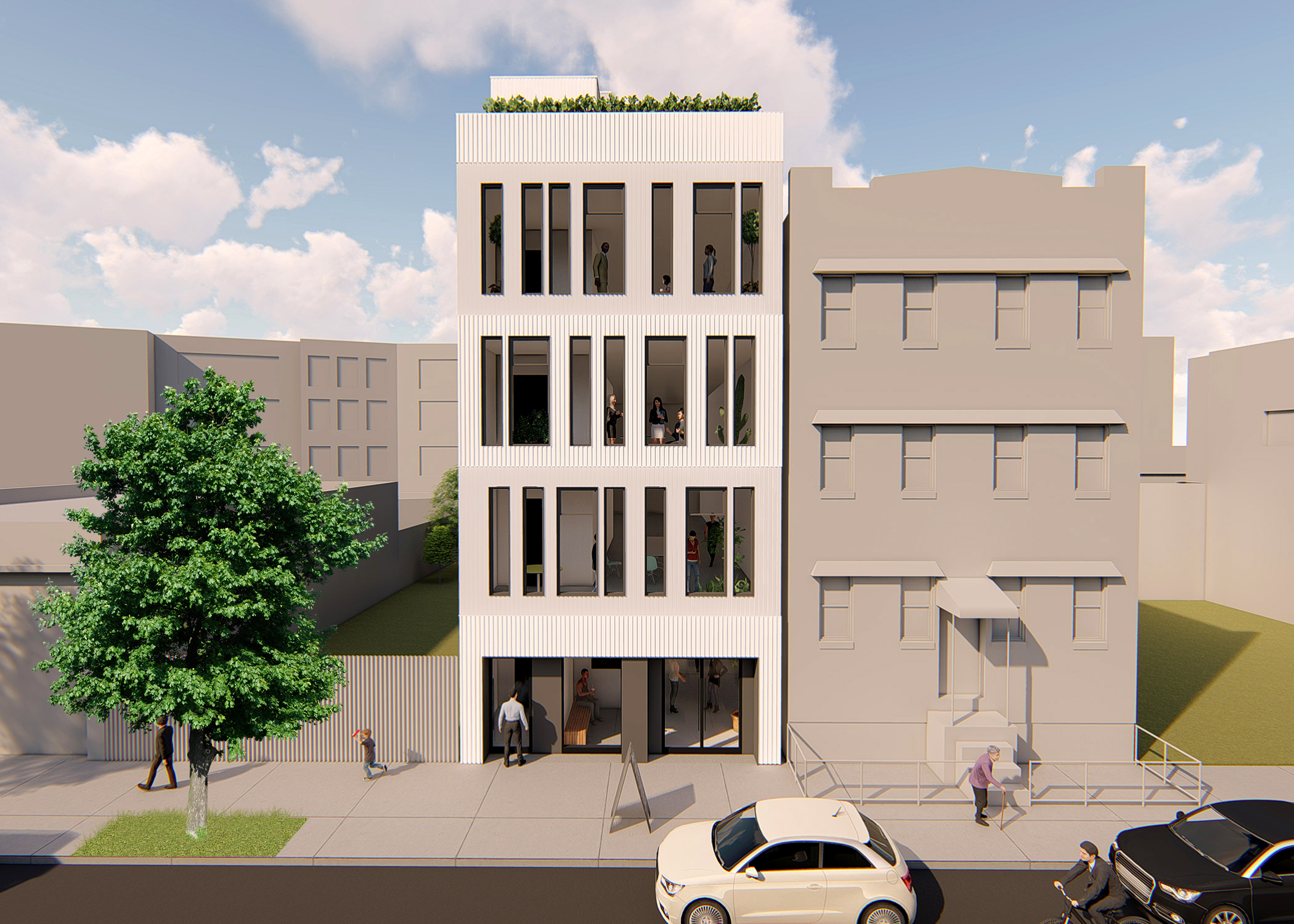
Hedberg sees numerous advantages to that. “There will be less noise, traffic, and dirt for nearby residents,” he notes. “And we’ll reduce construction waste by 60 to 70 percent.” There are positive effects for construction workers and tradespeople as well. Employees without specialized knowledge can be trained quickly. And they can work in factory halls that are protected from wind and weather, and where large numbers of components are made under industrial conditions in accordance with a logical system developed by architects and engineers. By 2022 at the latest, Hedberg wants to start up the world’s first factory that will produce entire ready-to-use hotels, residential buildings, and hospitals. All sections of the buildings will be produced in the factory, along with key products such as fixed furniture, windows, doors, and bathroom modules. All pre-fabricated sections will then be joined on the main assembly line before being transported to the construction site. At the site itself only the final minor steps will be carried out, such as connecting the building’s room modules and core elements. That comprises only 2 to 10 percent at most of the entire construction process.
Modern shipbuilding processes gave Hedberg his inspiration. Cabins are prefabricated and lifted onto luxury liners by cranes, deck by deck, until all the sections are then joined into a whole. Another example is the automotive industry. “When customers order a Porsche sports car, they can choose one of a large number of possible configurations,” he says. “You won’t get identical 911s rolling from the production line. Our customers should also be able to use a configuration system to design their buildings individually, and see the price and timetable for any given variant.”
BIM: Top-value twin
Digitalization is revolutionizing planning processes in the construction sector for both the trades and industry. “There will be fundamental changes to our planning and design work in the future, and we’ll benefit from other sectors’ digital technologies in the process,” says Brühl. As the Sto Group’s vice president of digital building solutions, this expert is dealing directly with the transformation himself. As he notes, “Most construction sites still base their planning on 2D-supported documents.” A more modern approach is to have a “digital twin” of each building project, generated by a process known as BIM (building information modeling). The core of BIM is a three-dimensional digital model that contains all the construction details and documents all the processes throughout the building’s life cycle, including everything from progress at the construction site to subsequent modernization. With interfaces to all the skilled trades and stakeholders involved, work can take a more concerted form. BIM platforms will also soon be offering docking options for construction machinery and their data. Systems of these types open up enormous opportunities. As just one example, German companies could guide construction sites in China without being physically present.
Building Information Modeling—The Digital Twin
White Paper: Top-Value Twin
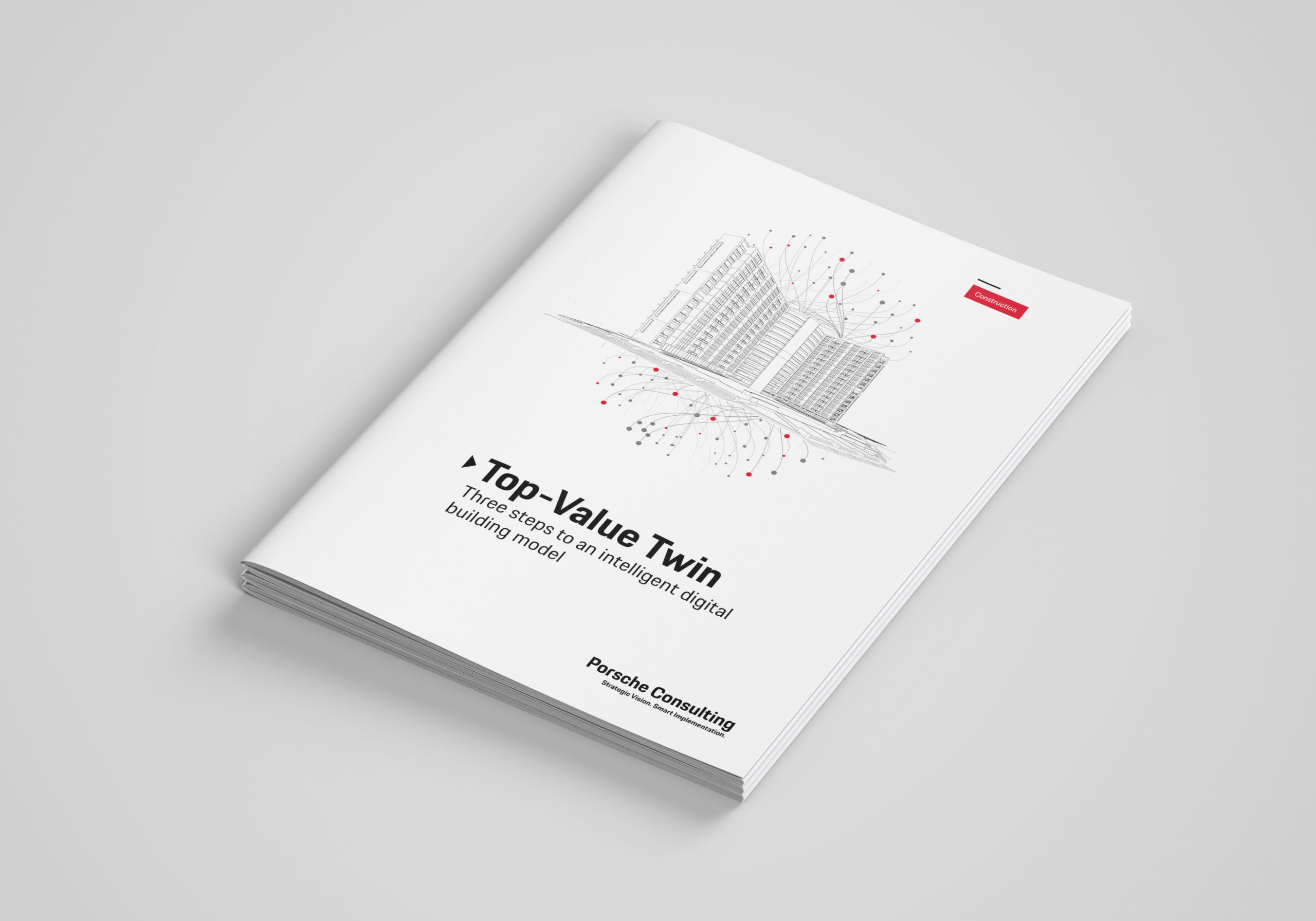
Excavators without excessive noise
When things finally get moving at construction sites, excavators, wheel loaders, bulldozers, cranes, dump trucks, and other specialized construction machines get to work. Many manufacturers envision a future business sector consisting of cleaner, quieter, and more efficient machinery. All the leading makers have already presented initial prototypes. “Electric mobility and alternative powertrains are an increasingly significant field not only for cars and vans,” says Patrick Scherr, senior vice president of Schaeffler’s Offroad Europe business unit. “The makers of construction vehicles and machinery are advancing electrification of their own products. They’re installing electric drives especially in smaller construction machines and lower performance categories. Hybrid drives are also increasingly of interest. There’s a high demand for systems that support simple activities and also offer a secondary power source when high performance levels are needed, such as for excavators or medium-sized wheel loaders.” Schaeffler offers friction-optimized and robust roller-bearing solutions for challenging operational conditions.
Dr. Rüdiger Kaub emphasizes the role of government actors and regulations in promoting zero-emissions construction machinery. As chairman of the management board of Bauer Maschinen, he visits construction sites on a daily basis. Clients interested in the specialized excavation machines from this Bavaria-based leader on the world market read like a who’s who of construction corporations. “Calls for construction project proposals from our neighbors in the Netherlands, for example, or in Singapore, require the machinery to leave a minimal CO2 footprint and produce very little noise,” says Kaub. After all, in many places these machines run essentially around the clock. And electrification is not always possible. “Heavy-duty excavators with around 1,000 horsepower run on diesel engines, and that’s not going to change all that quickly,” says Professor Sebastian Bauer, managing director for R&D at Bauer Maschinen. “There could in fact be electrical solutions for medium-sized excavation machinery, but they would need special wiring and facilities or all the lights would go out at the construction sites.” A downsizing trend is also evident. “For decades our fleet was getting bigger, heavier, and more powerful, but there will be greater calls in the future for more compact, lightweight, and transportable machines more suitable for the tighter space in urban contexts. We can probably lower noise levels by a substantial amount with developments in mechanical engineering,” explains Kaub. The company is also studying the use of fuel cells and hydrogen drives.
The Construction Boom in Numbers
- The global volume of construction work is estimated at $9 trillion, and is expected to reach $15 trillion by 2025.
- The highest volumes are seen in China, India, and the USA.
- Construction activity increased by 15 percent in the EU from 2014 to 2019.
- Germany is the largest European construction market, with a nominal volume of €430 billion in 2019.
- The world’s 100 largest construction companies had a combined overall revenue in 2019 of more than $1.463 trillion.
- Chinese corporations account for 44 percent of revenue in the top 100, and six Chinese companies are in the top ten.
All construction experts agree that in order to increase productivity, construction machines need higher levels of automation and the ability to communicate with each other. That will make these expensive machines more efficient, and allow them to be used around the clock. “Numerous assistance systems are supporting drivers today, which means the machines are already partially automated,” says Kaub. “These digital assistants make it possible for less experienced workers to operate the machines too.” That could be one answer to the shortage of skilled construction workers. Many parts of the world now use driverless dump trucks to make rounds and transport raw materials on set routes, for example at mines in Australia and South America.
We provide tested technology for driverless construction machines.
Tested key technologies
Automated functions not only improve safety levels at construction sites. They also reduce driver fatigue and help comparatively inexperienced users be more productive. Schaeffler Paravan, a subsidiary of Schaeffler, has developed a suitable baseline technology for this purpose, namely, its Space Drive drive-by-wire digital control system, which assumes all the driving and steering processes without mechanical connections. It processes electronic signals within nanoseconds and transmits them via actuators to the axles. Electronic signals control acceleration, braking, and steering. Traditional steering wheels, pedals, and steering columns are no longer needed to transmit commands mechanically to the wheels. The advantage here is that construction vehicles can be operated via tablets, apps, or remote control systems while the operators stand off to the side or in completely different locations. “Schaeffler’s Space Drive system has been used successfully for many years now, both on the roads and in vehicles like mining trucks,” says Scherr. “It’s a proven technology that we’re providing to run construction machinery autonomously.”
“It will be another fifteen or twenty years before we see fully automated driverless machines at typical construction sites,” estimates Bauer. “When we reach that stage, the drivers will take on different jobs such as supervising and coordinating the autonomous machines from control rooms, and being ready to intervene and make corrections at any time.” As chairman of the board of the Research Association for Construction Building and Material Machines (FVB) and president of the Otto von Guericke Federation of Industrial Research Associations (AiF), his research takes place at the interfaces between people and machines. “Independent control as a semi-autonomous step will relieve drivers’ workloads over the next ten to fifteen years and help achieve greater levels of safety and performance,” he says, adding that “this will be accomplished with technology in the form of AI, 5G, GPS, camera systems, radar, and software.”
Study: The Future of Construction Machinery
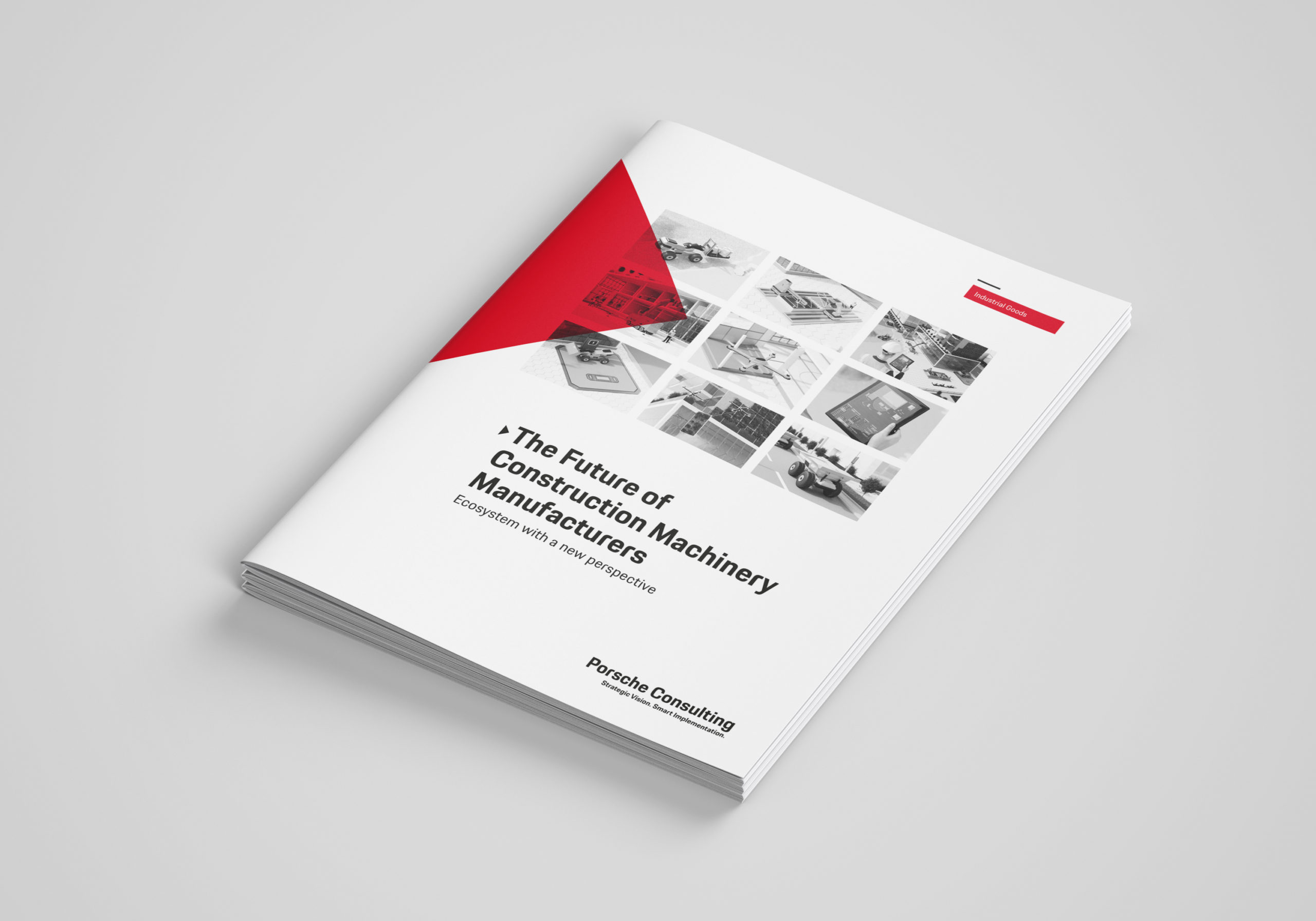
Data as a new business field
Predictive maintenance will play a key role in autonomous and connected machinery at future construction sites in areas like safety, productivity, and machine availability. While some sensors on modern dredgers, wheel loaders, and excavators scan the surroundings, other sensors will monitor inner components of the machines such as bearings and valves and detect even the slightest deviations from normal operations. They will register engine speeds and noise levels as well as the temperature of oils and other operating materials. The combination and analysis of these data will yield information about the state of construction machines. That in turn will provide early information on when certain components will wear out and should therefore be replaced in order to prevent repair costs or unexpected outages. For predictive—as opposed to preventive—maintenance, the intervals are not specified in advance. Instead, they are determined on the basis of sensor data. Schaeffler’s Optime already offers an economical, wireless, plug-and-play way to monitor stationary assemblies. Its sensors monitor vibrations at measurement sites and fully automatically provide operators with analyses and recommendations for action. Based on this experience and with digital services in general, Schaeffler is superbly equipped to meet the challenges in the construction machinery sector.
The engineers at Bauer can currently switch into around one thousand pieces of machinery regardless of where they are being used. The machines regularly send data packages wirelessly to company headquarters. “We use big-data applications to help our customers evaluate and continuously optimize our products with updates and finely tuned maintenance, which means we can increase quality and functionality and lengthen product service lives,” says Kaub. In the future it should be possible to switch into the cabins in real time to support drivers. High levels of data are changing the business models for companies like Bauer. They are becoming ever more important sources of revenue and laying the groundwork for new data-based services. Bauer is also giving older machines a second chance by enhancing them as far as possible with software and new hardware. This lends new meaning to an old construction site motto: What doesn’t fit will be made to fit.