Building Should
Be Fun
Since 1960, prefabricated house manufacturer WeberHaus has successfully relied on traditional craftsmanship. Today, it combines this proven quality with smart robotics to produce sustainable, prefabricated timber-construction houses. The family-run company is defying the difficult conditions on the house construction market with new service offerings.
04/2025
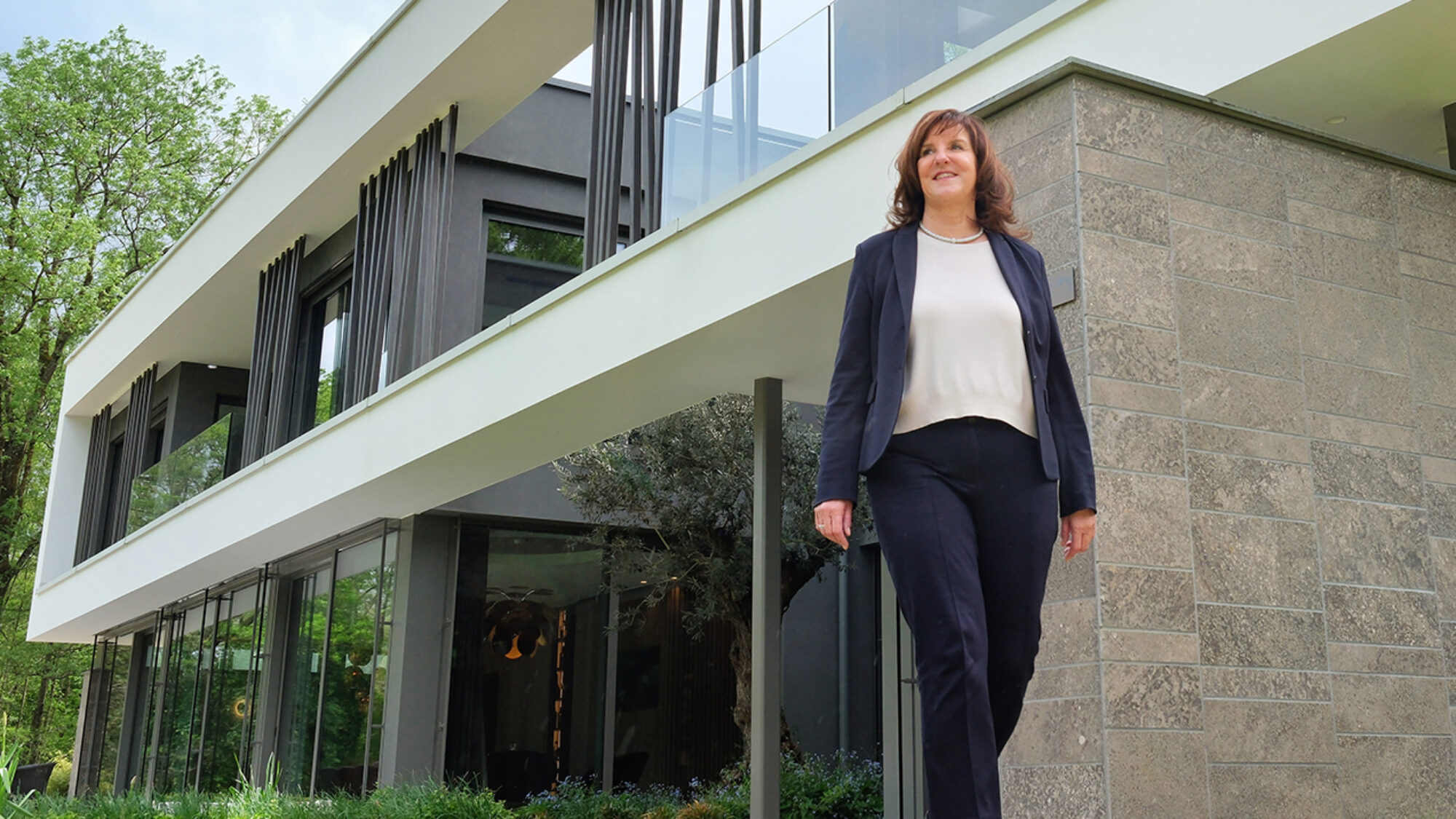
At a country inn, the friendly waiter serves local delicacy Badische Käsespätzle with braised red onions. A really satisfying dish for 14.50 euros. We are in the border region between France and Germany. The city of Strasbourg, the seat of the European Parliament, is not far away. The Rhine river separates the two European neighbors from each other. Tullastrasse winds through the small village of Rheinau-Linx. The speed limit is 30 kilometers per hour. Follow the next curve, then turn right into Erlenpark with its extensive lawns and lovingly designed beds of perennials.
All of a sudden, you’ll find yourself in the middle of World of Living, an impressive open-air exhibition showcasing state-of-the-art homes – for young families, multi-generational living projects or dream villas. The villas are also popular with wealthy English people, especially when erected as country houses in beautiful communities on the outskirts of London. The basic framework of the wall and ceiling elements consists of a wooden stud wall made of spruce. These segments, which even include built-in windows and windowsills, are manufactured in factory halls before being shipped to Britain and other destinations. It’s a good 900 kilometers to Britain and the journey includes crossing the English Channel, the strait between Calais and Dover. The turnkey house will then be built within a few weeks.
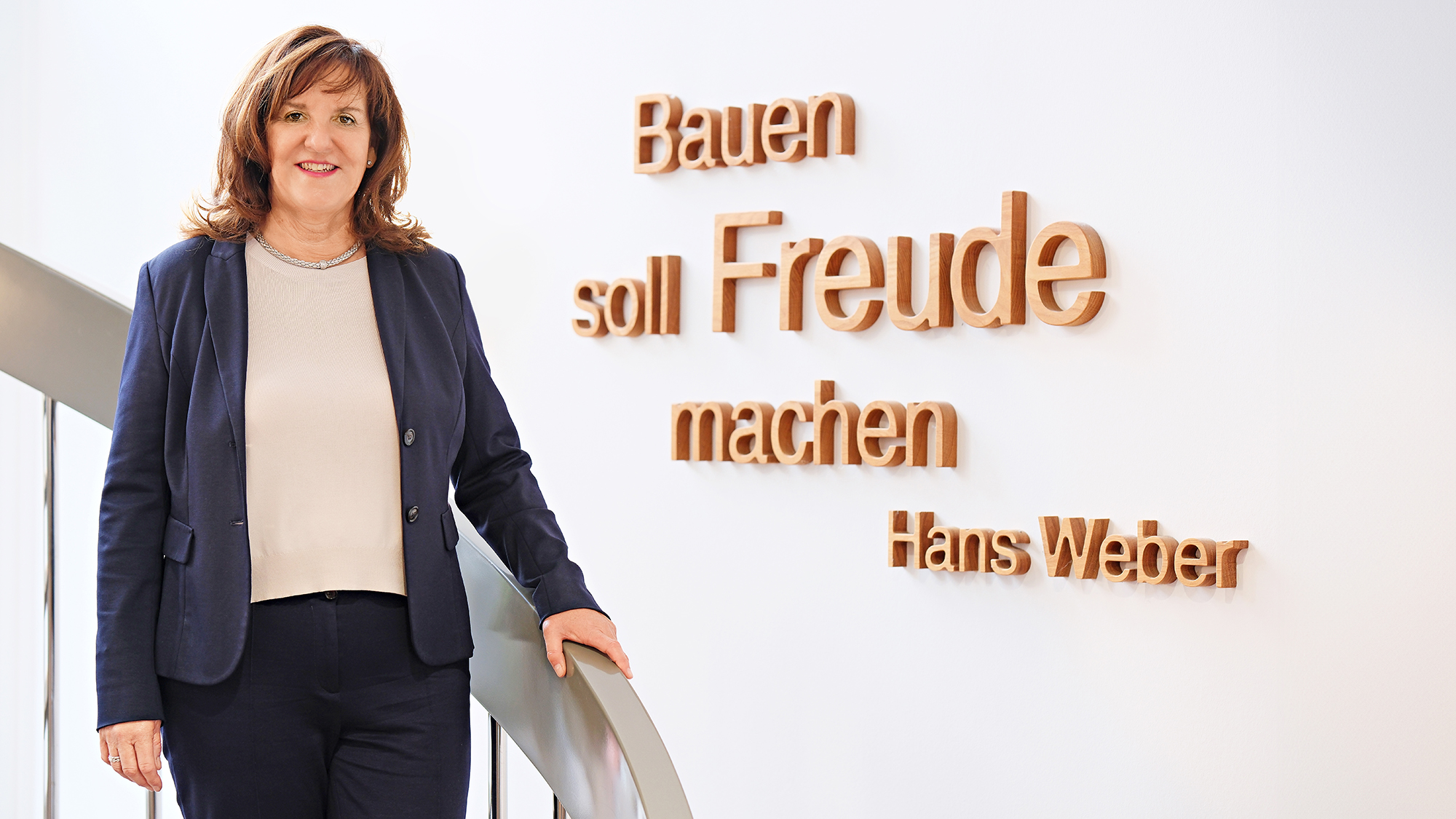
Rheinau-Linx is the headquarters of the family-run company WeberHaus. It is one of the largest manufacturers of prefabricated houses in Europe (sales in 2023: 322.3 million euros; 1360 employees). Heidi Weber-Mühleck, the second-generation owner, meets us on the spiral staircase in the administration building. Her words of welcome include her motto: “Building should be fun.” For customers, for employees and, of course, for WeberHaus itself. These formative words from her father are also memorialized in three-dimensional letters on the wall of the foyer. The letters are of course made of wood. Her father, Hans Weber (born in 1936), is a trained carpenter and founded the current company in Rheinau-Linx back in 1960, immediately after his master craftsman examination.
The entrepreneur passed on his love for wood and his dedication to the family business to his daughter. One year before Heidi Weber-Mühleck’s birth in 1964, her parents Hans and Christa Weber built their own WeberHaus. For the Webers, the house became not only a family home, but also an extended office space on their own factory grounds. The spirit of the family business is also carried on by the current managing partner: Not only did she grow up on the factory premises, she has also lived in the company’s prefabricated houses her whole life, apart from during her apprenticeship. In 2000, she built her own WeberHaus. “Once you are used to the special atmosphere you get from these houses, you never want to be without it,” says the owner of the family business.

Great climate
A pleasant climate in all living spaces is one of the unique selling points that sets apart the wooden houses of the WeberHaus brand. At regular intervals, the prefabricated construction company has the room air quality checked for harmful substances by the three independent institutes TÜV Rheinland, Sentinel Holding Institut, and Dr. Blei. The high air quality is confirmed time and again by tests showing that the pollution level is far below the legal threshold. The air quality is promoted by the special wall structure that forms the heart of every Weber house. In order to build houses in a healthy way, the choice of materials used and the processing is crucial.
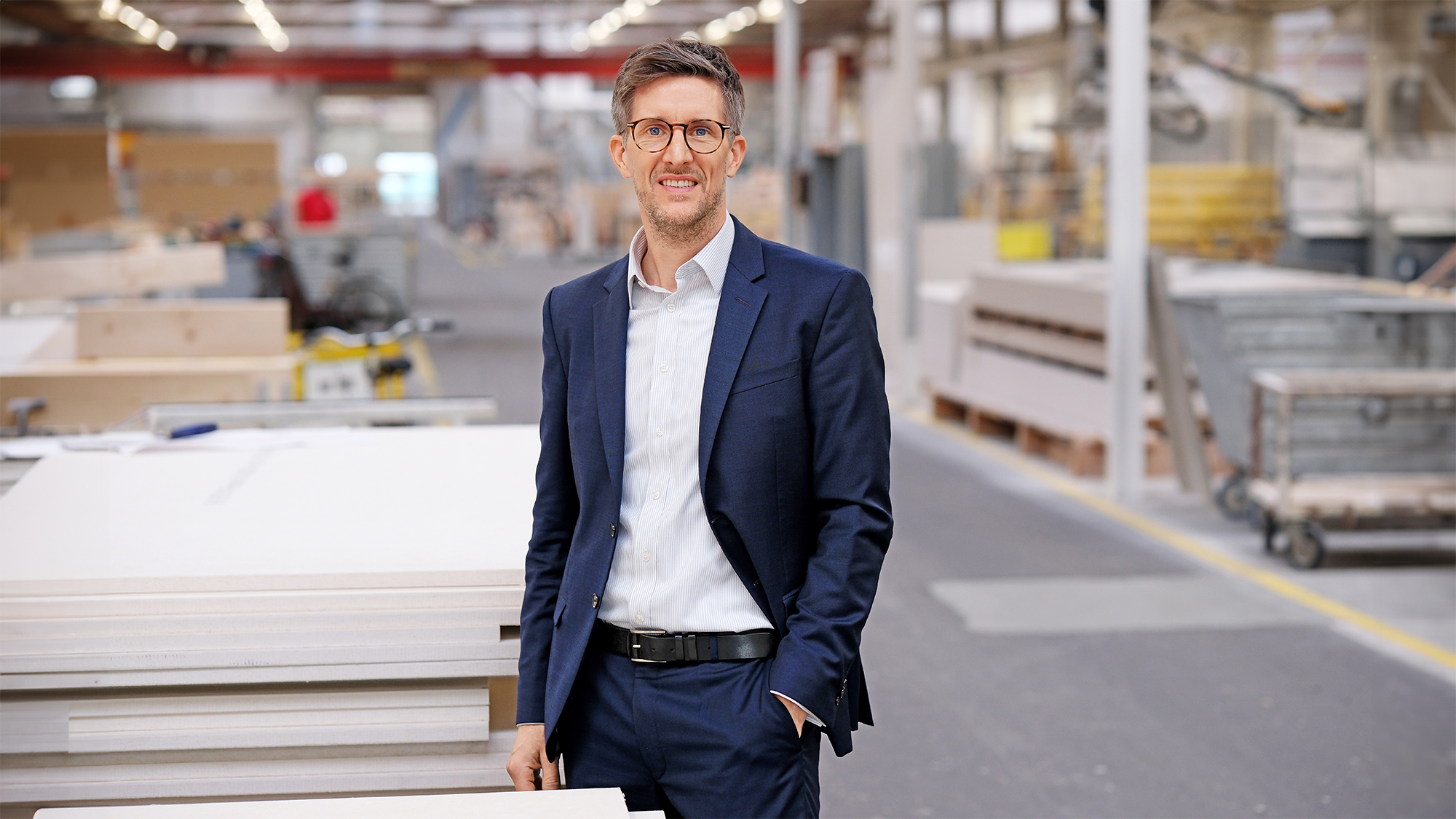
For example, polystyrene is used by many manufacturers as an insulation material. But not by WeberHaus: “We use mineral wool insulation made of recycled glass and certified with the Blue Angel environmental seal, as well as wood-fiber insulation panels. This means that WeberHaus is years ahead of the legal requirements,” explains Dr. Manuel Schönwitz, Technical Director at the Wenden-Hünsborn plant. The wood fiber panels are manufactured from untreated wood chips. Like all the wood used, they are sourced from local forestry. The wooden panels in the walls also bear the Blue Angel test seal. At the same time, the innovative, ecological building shell boasts excellent energy values and outstanding insulation properties in terms of heat, cold, sound, and fire protection.
Sustainable materials lifecycle
Founder Hans Weber has had a strong influence on the company’s sustainable positioning since its beginnings. Not only in the ecological planning of the houses, but also in terms of sustainable production methods. “Since the 1970s, we have been using our wood waste to fully heat the Rheinau-Linx and Wenden-Hünsborn sites in a climate-neutral way,” says Heidi Weber-Mühleck, “from the factory halls to the office buildings, right through to our World of Living discovery center and showhouse exhibition.” What’s more, the same energy is used to supply hot water to the park and to cool it in summer. The by-products generated during the production phases – such as sawdust, planing chips, and other residual wood – are collected and processed in a wood-chip incineration plant. Schönwitz adds: “By comparison, the resulting useful heat could supply around 450 households per year.” Of the other waste generated by production, such as pallets or excess mineral wool, 92 percent is sorted by type in the production area and returned to the manufacturers for reuse. In addition, large-scale photovoltaic systems have been installed on the production buildings. This generates environmentally friendly electricity and reduces energy costs both in Rheinau-Linx and in the second plant at Wenden-Hünsborn in the Sauerland region of Germany.
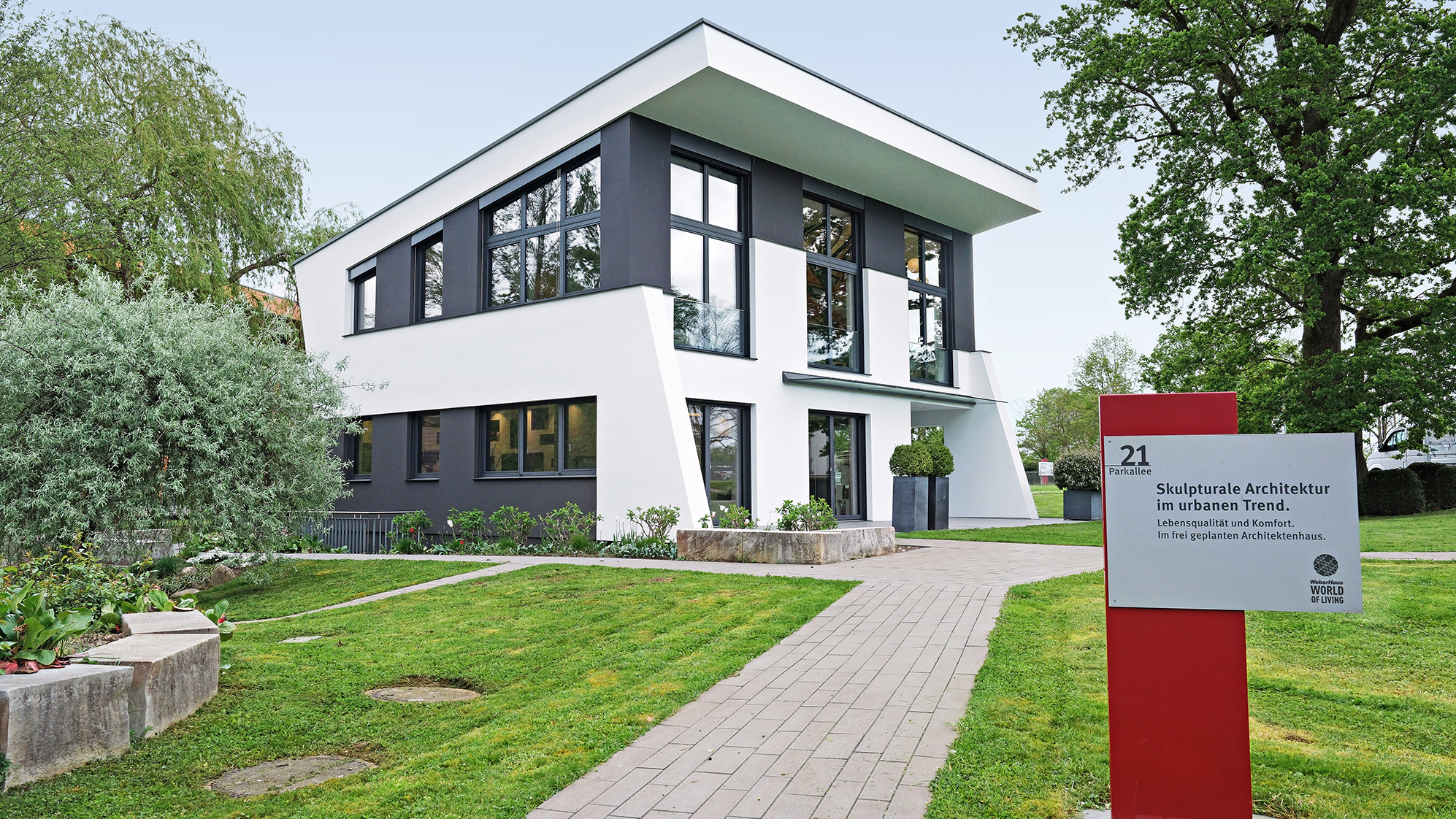
New market, new opportunities
In addition to its strong focus on the most sustainable and energy-efficient planning and production of its houses, WeberHaus is increasingly looking at the development of new customer segments. Land shortages and increased property costs, construction costs, and interest make it challenging for people interested in house building to fulfill their dream of owning one for themselves. The prefabricated construction company, which grew and developed in a world of classic single and duplex home construction, is responding to the difficult conditions on the house construction market with new offerings. “We are seeing a strong trend toward smaller houses,” explains Weber-Mühleck.
“With the new Option house type, we are targeting new customer groups, such as single people or couples without children, but also older generations who want to downsize,” says the company owner. The Option house is offered as a single-story, step-free bungalow with a floor area of 55 square meters and as a two-story version with up to 90 square meters. For customers, this means a lower price and a more modest space requirement that can be accommodated on smaller properties, as well as on already existing larger existing properties. Dr. Manuel Schönwitz: “Our motto when planning Option was: ‘as small as possible but as large as necessary.’ We are consciously differentiating ourselves from the Tiny House segment. Our goal is to balance cost effectiveness with high quality and feel-good factor for our customers.”
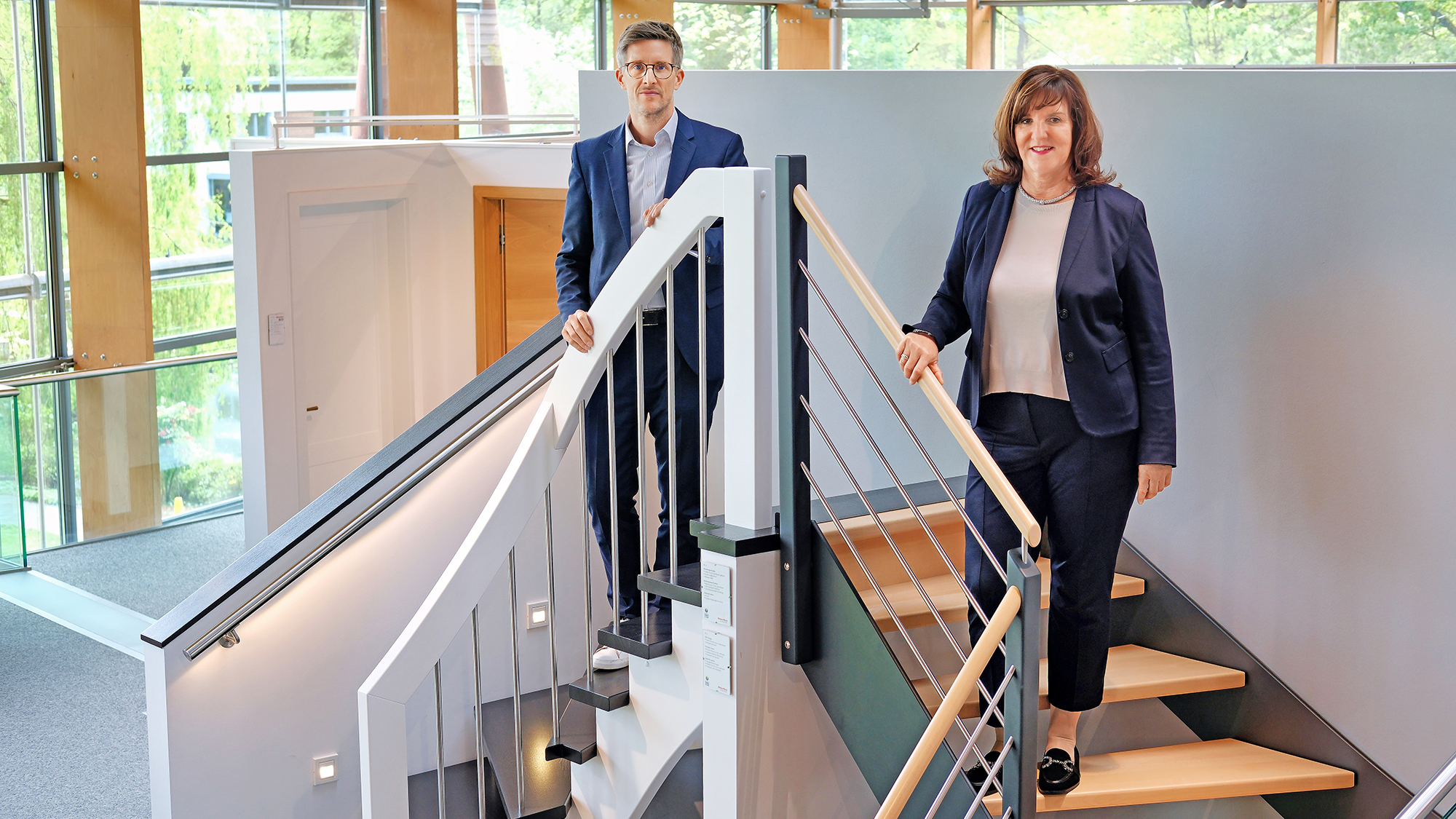
In order to be able to respond more effectively to future customers’ more limited budgets, WeberHaus wants to make the technical equipment options of its houses even more flexible. This could be made possible using a clever technical trick: integrating various sensor systems directly into the house at the production plant. These sensor systems would remain deactivated for the time being and the customer would not be charged. This includes sensors for measuring temperature and humidity, as well as sensors on lockable components. It could also include sensors that enable advanced smart home functionalities. “Similarly to the automotive sector, where digital functionalities can be activated in the vehicle as required, customers would be able to activate technical functions in their home at a future date after their home has been constructed,” says Manuel Schönwitz. “They could do so either by paying a one-off amount or in the form of a subscription model.”
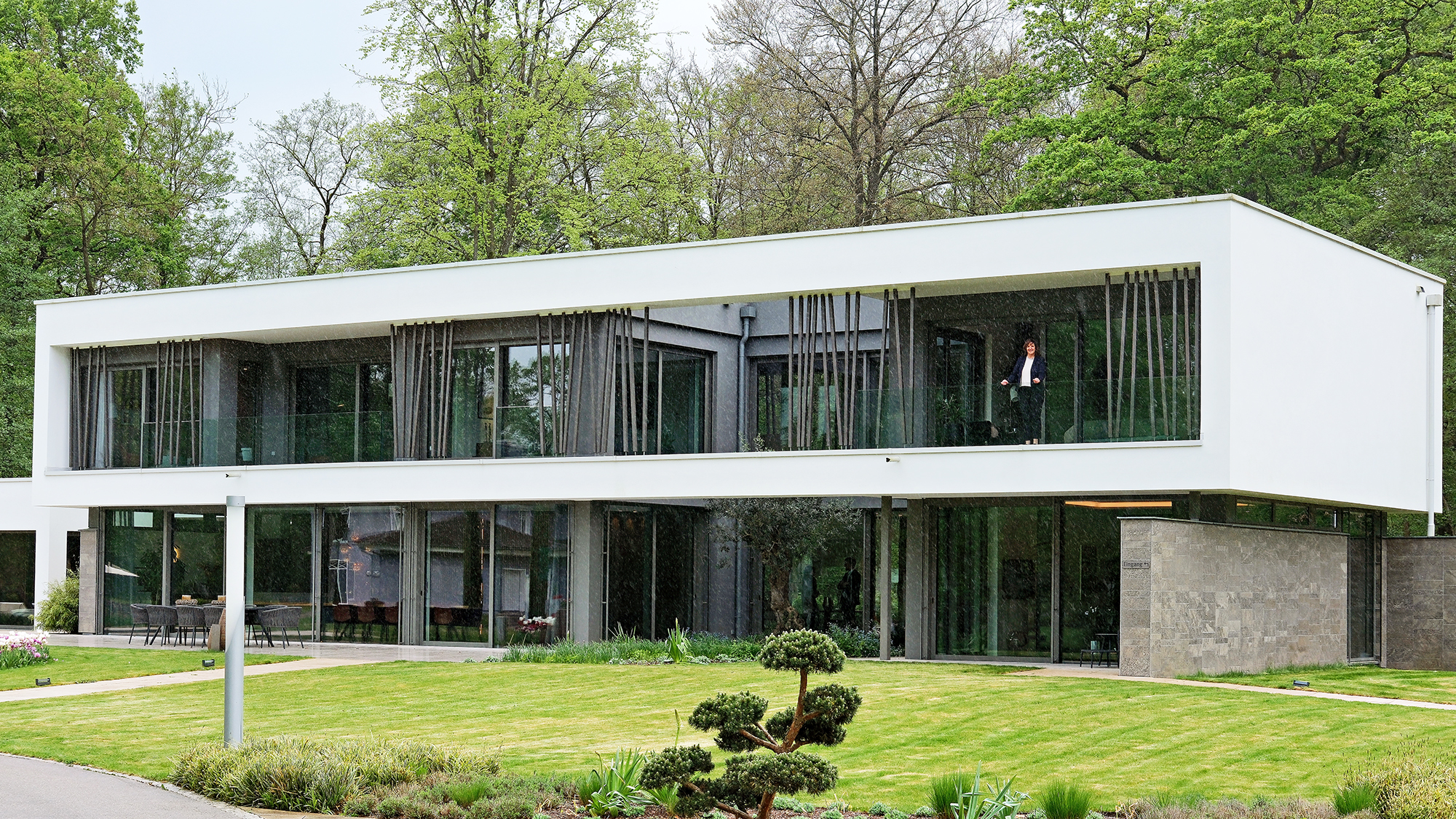
Another pillar: commercial property construction and renovation
In view of the high density of residential development in Germany, the prefabricated house manufacturer is also focusing more on commercial construction. This includes, for example, the planning and construction of apartment buildings, but also company premises, employee apartments, hotels, and properties in the health sector. With a view to maintaining Weber houses that have already been built, the renovation and reconstruction segment is also becoming an increasingly important pillar of the business for WeberHaus. “With now more than 40,000 houses built, there is enormous potential for us here,” stresses the company owner. This includes, for example, offerings such as building extensions or the installation of photovoltaic systems, battery storage units, and air-conditioning systems. It also includes renovations of bathrooms and refurbishment of heating systems and electrical wiring.
“We have always had a service department serving these areas. But of course not to the extent that we want to implement it now – or are already in the process of doing.” Refurbishment and conversion measures have so far been implemented only on specific customer request. In the future, the prefabricated house manufacturer would like to push this segment more strongly and actively draw the attention of existing customers to the range of services offered. This does mean that the company now has to establish new structures in sales and in the partner network. For this purpose, the company has purchased new businesses, including providers of roofing, heating, sanitary, and electrical installation services.
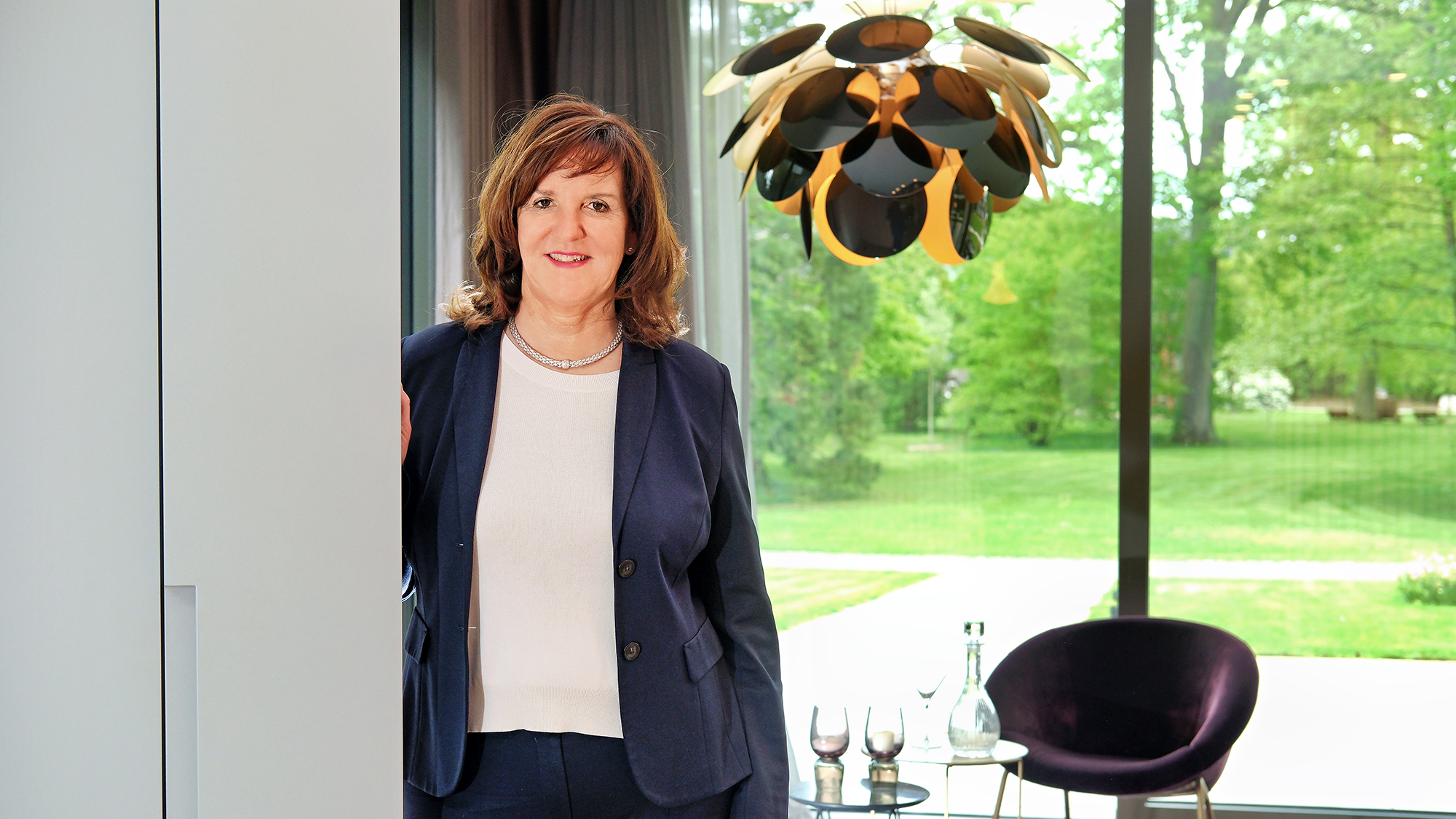
Talent in the company’s own ranks
In addition to the acquisition of external skills, WeberHaus places great importance on training its own people. This has long been a great strength of WeberHaus. The training of in-house specialists, especially in the skilled trades sector, has been very much supported since the beginning by company founder Hans Weber. For many decades, young artisans have been trained in the company’s own carpentry workshop. In total, WeberHaus provides training in twelve different professions, including painters, electronics engineers, computer scientists, industrial managers, and architectural draftsmen. This is a big win for the prefabricated construction company – especially in times of a shortage of skilled workers. “The satisfaction of our employees is a matter close to our hearts – they are the most valuable asset that a company can have,” stresses Heidi Weber-Mühleck.
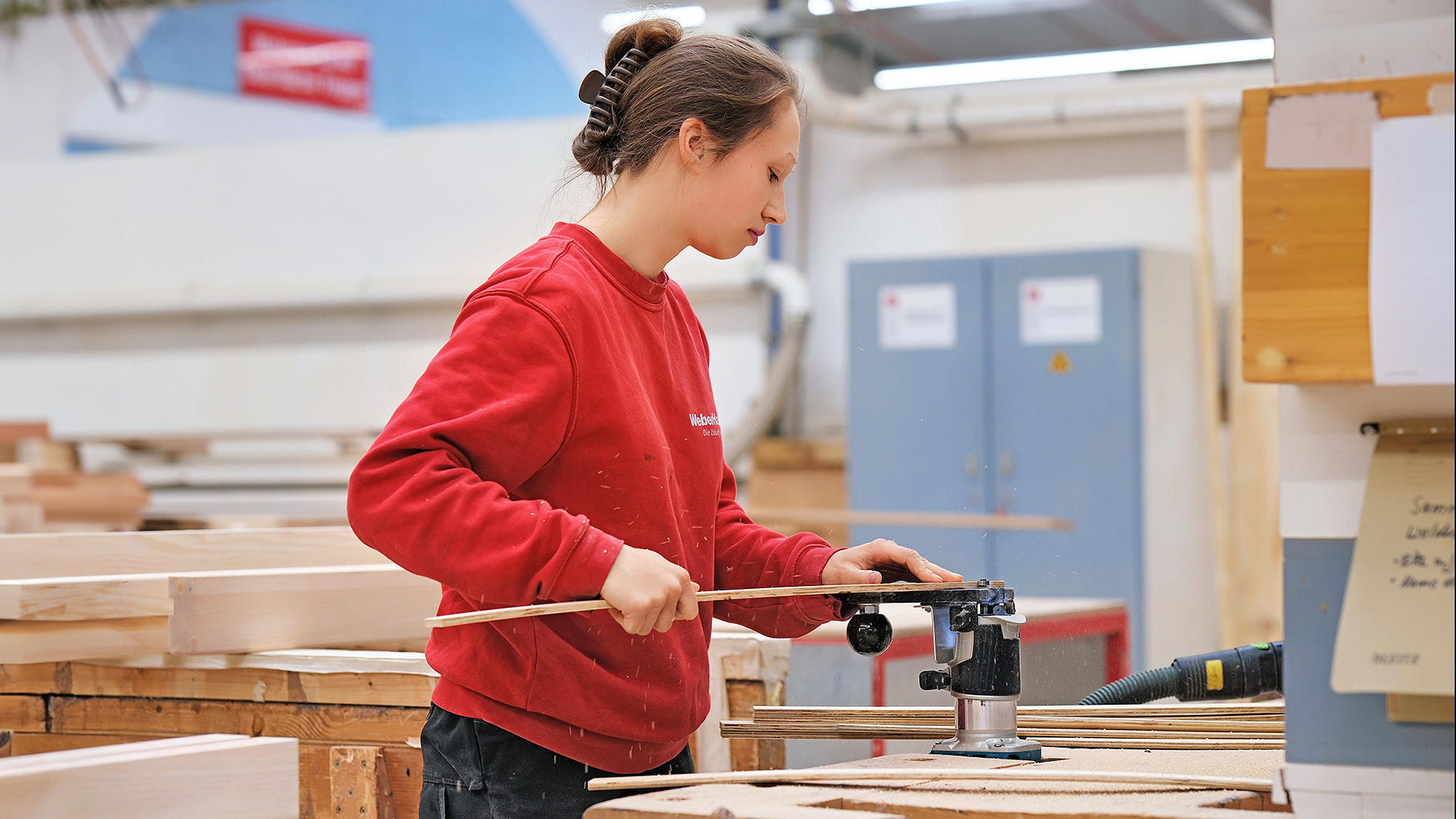
The prefabricated house manufacturer is currently setting up its own academy to offer advanced training to its employees. Last but not least, the familial, down-to-earth environment in the family-run business contributes to the fact that many of the employees have been loyal to the company for several decades: “Many of our employees have been with the company for 30 to 45 years, some of them in the third generation,” says Weber-Mühleck. “The first apprentice that my father hired stayed with the company until he retired.” Speaking of the company founder, Hans Weber is still part of the family of executive shareholders. He is an early riser and likes to take walks through the beds of perennials at the company headquarters shortly after sunrise. A tour of his successful life’s work before the first house buyers of the day arrive at the park for viewings.
WeberHaus: Craftsmanship meets modern technology
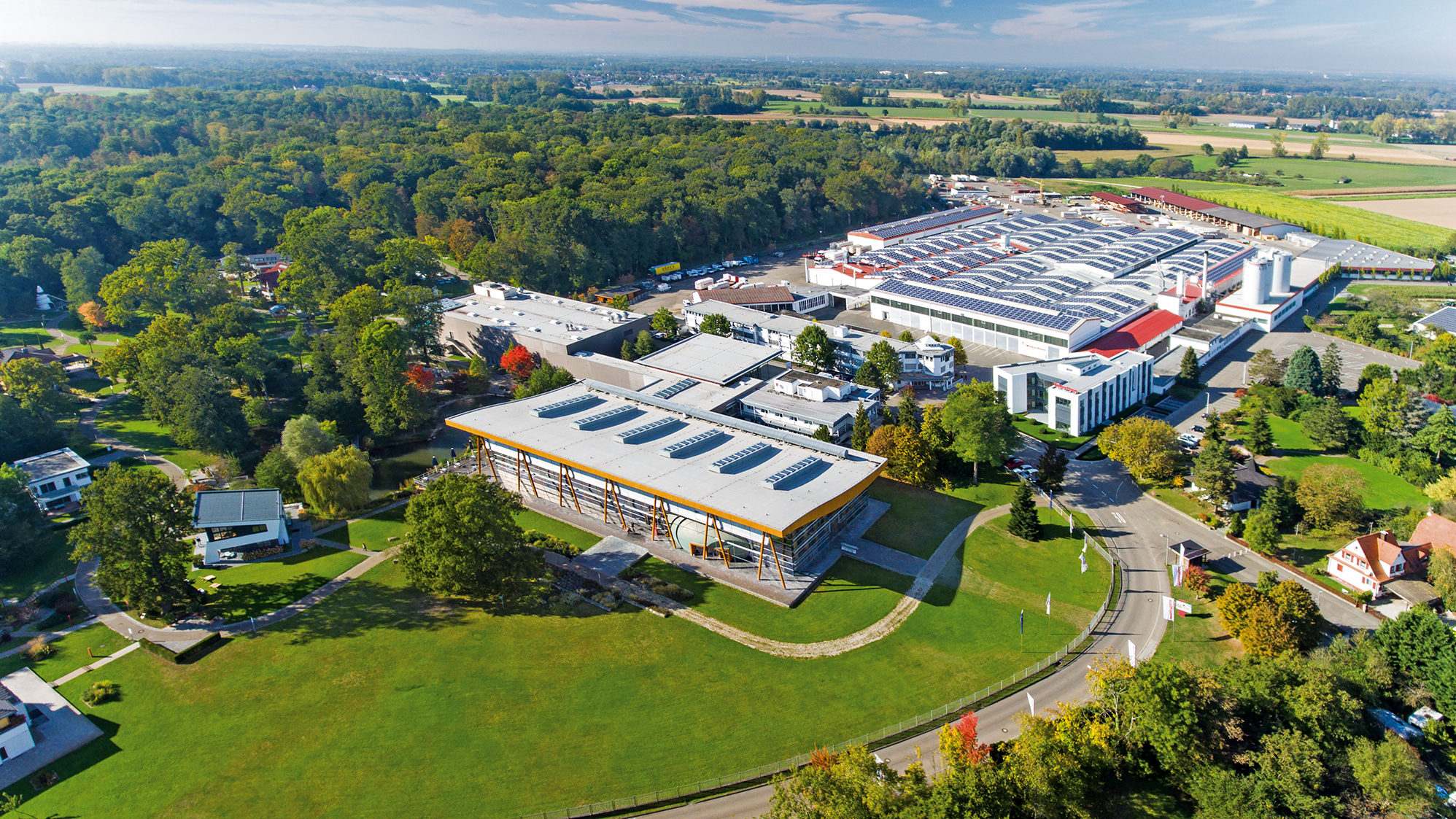