Project “P”:
A Blank Slate
at Audi
Audi has completely reorganized its production work. One of the largest restructuring projects in Germany’s automotive industry was completed within a single year — and is already paying off.
09/2020
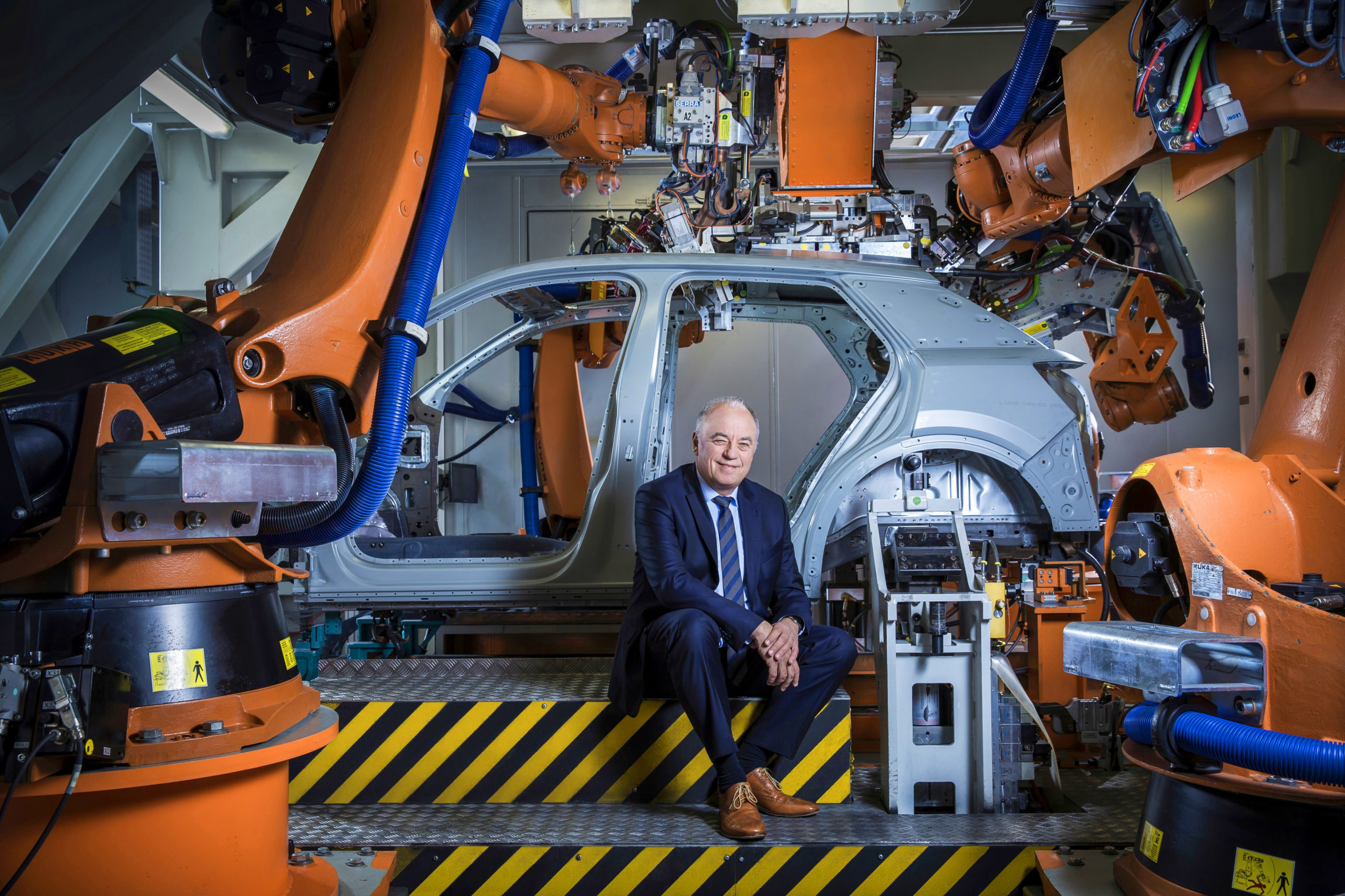
December 2, 2019, is a momentous day for the production and logistics division at Audi. It marks the start of a new era for the production. The heart of every car maker is its production department, and Audi has just given it a new organizational form. This might sound like a minor administrative reform. But that would be like equating the shift from combustion engines to electric drives with a simple model facelift. This first Monday in December 2019 marked “the largest transformation project in Audi’s history,” says Peter Kössler, the company’s board member in charge of production. “We pulverized our complete organization,” he adds. One could also say the company conducted one of the largest internal reorganizational projects ever seen in German automotive industry.
New matrix for new challenges
“Expertise-oriented matrix organization” is the key to the future of “P,” Audi’s production division. This new organizational form is designed to enable the car maker to meet upcoming challenges considerably more efficiently and cost-effectively, because the automotive industry needs to master the greatest transformation in its history. The industry’s very foundations have been shaken by innovative technological trends and a fundamental shift in how society views mobility. Digitalization, driverless cars, alternative powertrains, intelligent assistance systems, big data—car designers today need more know-how than NASA engineers did to build their first lunar rocket. The wheel of innovation is spinning ever faster, and anyone who cannot keep up will quickly fall off. This calls for innovative business models and products. And that in turn requires production facilities to accommodate ever shorter intervals in technological developments as well as changing expectations on the part of customers. Within the space of just one year, Audi therefore took its production department from the initial idea to the actual launch of what it calls an expertise-oriented matrix organization.
In effect, that means a completely new model for collaboration. New responsibilities. New communication channels. New interfaces to other parts of the company, and the elimination of one complete level in the hierarchy. And—an essential ingredient—comprehensive concentration on different types of expertise. As a result, tasks can be consolidated and standardized more effectively. Time and cost-intensive redundancies are to be avoided. And not least of all, the production process should not be overloaded. The greatest aim of the transformation project is to relieve the plants of unnecessary burdens so they can focus on their core task of making cars. A new strategic planning organizational unit now serves to coordinate the company’s divisions. It sets the main guidelines and targets for all activities related to Audi’s production plants as well as to central divisions from logistics to the pressing plant network.
Photos of fax machines
To grasp the significance of this restructuring project, one needs to look back at the past. The fall of 2018 will suffice for a start. That was when the first major meeting for the upcoming transformation took place with production board member Peter Kössler, all the division managers, and experts from Porsche Consulting and Audi Consulting. At the meeting, Kössler showed some photos from his early days at Audi. The native of Ingolstadt, joined the world of four rings in the mid-1980s as a trainee. The photos included old rotary-dial phones, bulky computers with small storage capacities, and fax machines. “This is what Audi looked like when I started working here more than thirty years ago,” he said. The machines have since been replaced by ever more modern systems. But the organizational structure, which is the backbone of successful car production, had hardly been changed over the preceding thirty years.
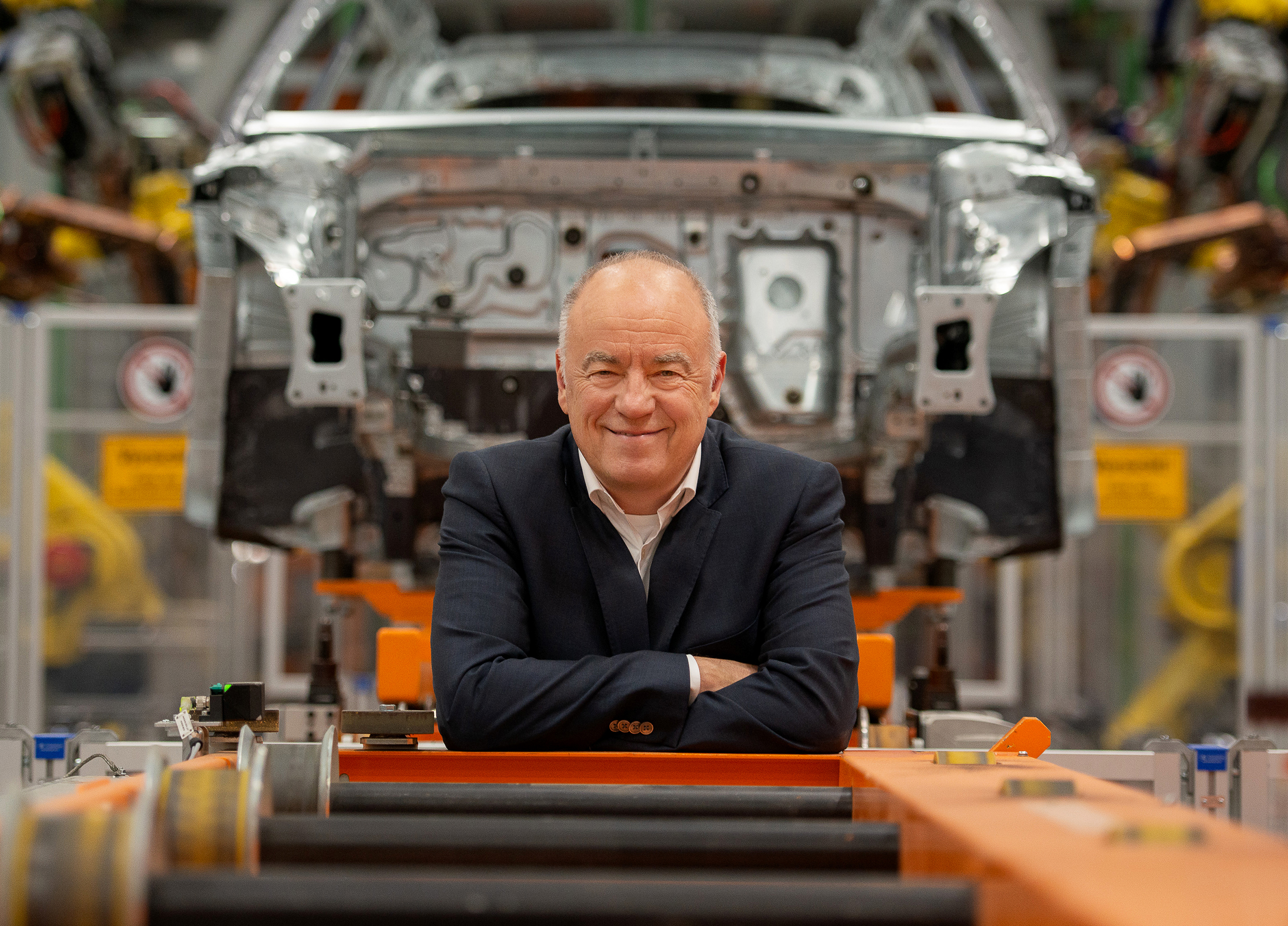
“For decades, production at Audi focused on functions,” explains Boris Kainz, an associate partner at Porsche Consulting who participated in Audi’s reorganizational project. That was not a problem when it was only a matter of the two sites in Ingolstadt and Neckarsulm. Distances were short and coordination was simple. But the principle is no longer viable in today’s globalized world with the company’s five plants plus joint ventures in China, as well as shorter product cycles and greater product and model diversity. Audi’s production resembled a federal system in which each plant and central office formed its own unit with its own targets, standards, problems, and means of finding solutions. “It was tough, time-intensive, and occasionally impossible to achieve the central coordination and control needed to focus on brand optimization overall,” says Kainz. The message behind Kössler’s retrospective photo show was clear. Something had to change. And that “something” meant actually everything.
“Think big – things will shrink on their own”
What the company then accomplished in just a little more than a year is impressive. Audi formed a “change team” with managers from all the divisions along with “heavy-project” managers Dr. Siegfried Schmidtner and Michael Breme. Porsche Consulting did something similar. As the head of “P,” Kössler set the course with the maxim “Think big—will shrink on their own.” In other words, the team was unencumbered by prohibitions and urged to think beyond departmental lines. Whether and how ideas would then be implemented was to be decided later on. In addition, the team established its own transparent communication strategy to ensure that everyone was always up to date. All those involved—employees, the works council, management, and board—were to be kept up to date at all times. More than one hundred Audi managers were directly involved in the transformation, and the restructuring project affected over 50,000 production employees.
Another of the project’s maxims was that the structure should reflect the processes. More than one thousand individual processes were identified and each one of them was assessed for possible overlaps and whether decentralized processes could be consolidated at a central source. One key scene in this major year-long transformational project illustrates the general tenor. In mid-March of 2019, or around four months into the project, the experts from Porsche Consulting arranged a workshop at a conference center outside Ingolstadt. The seminar room’s views of the surrounding meadows and woodlands were soon obscured. The walls, windows, and even the floor were quickly covered with 1,100 strips of white paper, each listing a specific production process at Audi. And then the struggle began. Each work step and each subprocess described on each slip of paper was examined. Twenty-five members of Audi’s change team walked around the room with “bunches of strips of paper,” recalls Kainz. “The strips were ripped up, crumpled, combined, sorted, and reposted. Everyone rolled up their sleeves and joined in. There’s a reason why we worked with paper, pencils, and tape—it gives you a completely different and very physical experience.” And the result was impressive. The number of main processes was cut in half, and the subprocesses were reduced by a third.
Clear responsibilities – experts for every challenge
One example of the benefits of streamlining Audi’s production can be seen today in the logistics activities. Previously each of the five plants had a logistics manager who concentrated primarily on the well-being and problems of that plant’s production department and reported solely to the plant’s manager. In the event of disruptions like shortages in the supply chain, that meant the strongest plant or the logistics manager with the best network had the edge. Other plants, which might also have been waiting for window lifters, for example, were left in the cold. That has now changed. The logistics managers at the five plants now report to the central logistics department. It works together with the sites to distribute components such as window lifters with the aim of finding the best solution for the brand overall.
The approach to launching new models has also been changed, with individual sites no longer expected to handle everything alone. For example, in 2017 the site in Brussels, which had thus far produced only one model—the A1—was charged with launching Audi’s first electric car—the e-tron—with its especially sophisticated technology. “That was an enormous challenge for a site that had previously only launched a new model every seven years,” observes Kössler. It became clear that the company should not require sites of that type to run such projects alone. “The plant had to break new ground and do a lot of improvising,” he adds. With the new expertise-oriented matrix organization, sites are no longer left to their own devices. A launch team with representatives of the relevant central departments and experts specializing in precisely these jobs was formed to coordinate production launches and guide the projects successfully for both Audi and the individual plants.
First big stress test: Covid-19
The first stress test for the new organization came quickly and with a vengeance. However, it was a stroke of luck for the project team that the new production organization was up and running when the effects of the Covid-19 pandemic set in. As Kössler observes, “From the perspective of the current situation and looking back at the past months of supply-chain shortages, furloughed employees, and suspensions in production, it’s absolutely clear to me that without the new organization, we could never have handled it in this form, particularly those difficult weeks in spring. We managed all the plants, especially in terms of logistics, from a single source and applied a coherent strategy to the new challenges that kept arising every day.”
And that is how the new aspects of “P” established themselves very quickly. But the most unusual part of the enormous transformation is that someone who had visited an Audi plant in the fall of 2018 and did so again today would not notice any difference. The largest transformation in the history of Audi has left hardly any visible traces on the shop floor—although it has changed almost everything.
“The organization has been rejuvenated in many areas”
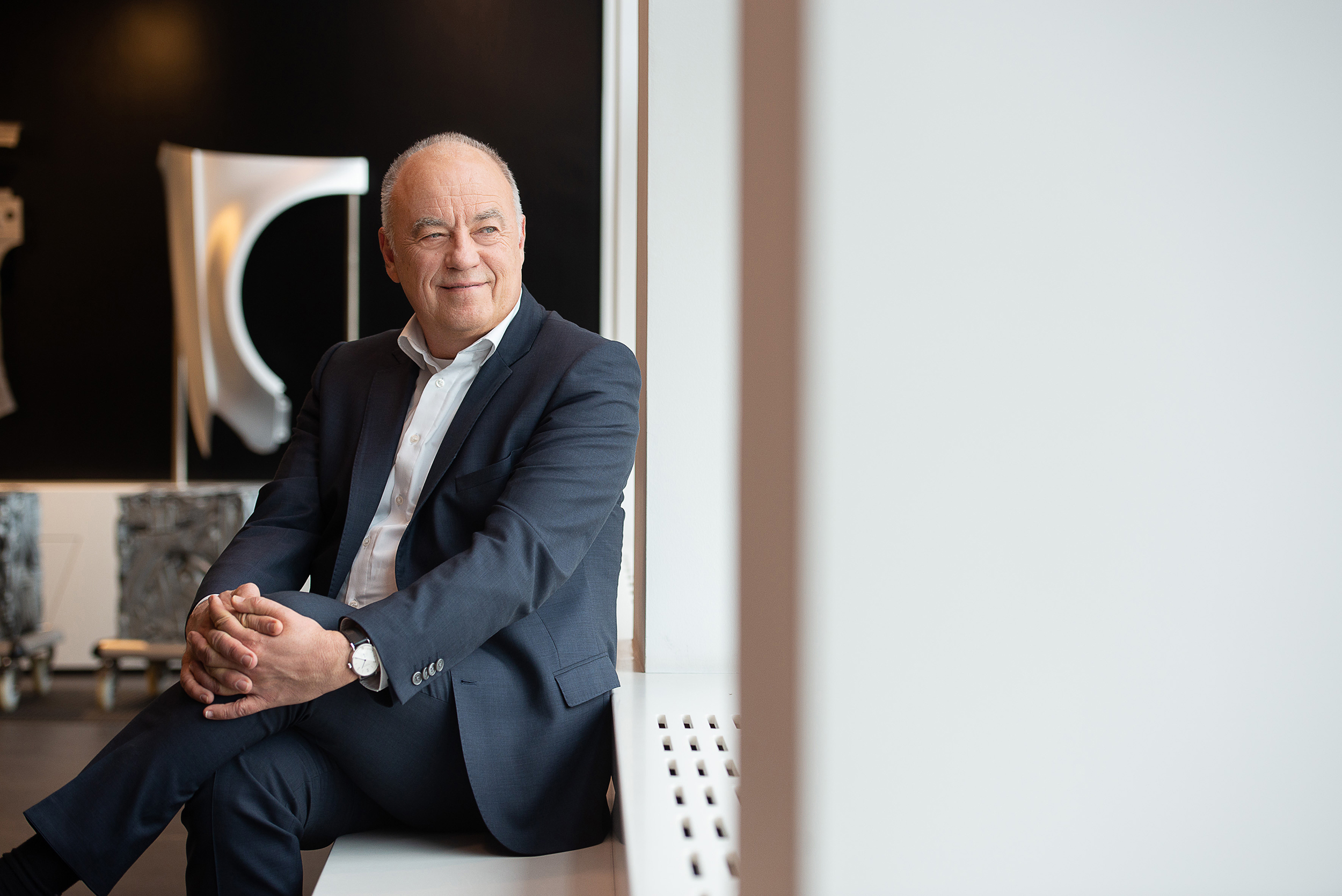